Pegging in PeopleSoft Order Management
A sales order in PeopleSoft Order Management can be pegged as demand to the following supply order type; interunit transfers (supply-side) in PeopleSoft Inventory, production IDs from PeopleSoft Manufacturing, and requisitions or purchase orders from PeopleSoft Purchasing. Sales orders can use soft-pegs or hard-pegs. A peg for a sales order can by created using:
The Alternate Sources of Supply page in PeopleSoft Order Management.
The Alternate Sources of Supply page enables you to create pegs, cancel pegs, change peg quantities, and view existing pegs. When needed, this page provides a link to the Pegging Workbench.
The direct ship feature by selecting the Direct Ship from Supplier check box on the Order Entry Form in PeopleSoft Order Management. This check box is located in the Order Line Entry group box under the Ship Options 1 tab.
The Requisition Loader (PO_REQLOAD) process or the Production Request (CPPIPRDN) process for a configured item on a sales order.
You can create new pegs and change existing peg chains for sales orders by using the Alternate Sources of Supply page in PeopleSoft Order Management. If the sales order schedule is pegged and has more than one demand line in the unfulfilled state, then the Alternate Sources of Supply page displays the Change Quantity link to take you to the Pegging Workbench.
Note: The link to the Pegging Workbench is only visible if the User Security page gives access to the user ID.
You can view peg chains for sales orders using the Sales Order Supply Source Detail page in PeopleSoft Order Management.
This process flow diagram illustrates pegging a sales order to a production ID. The sequence of events in the process flow is explained below the diagram:
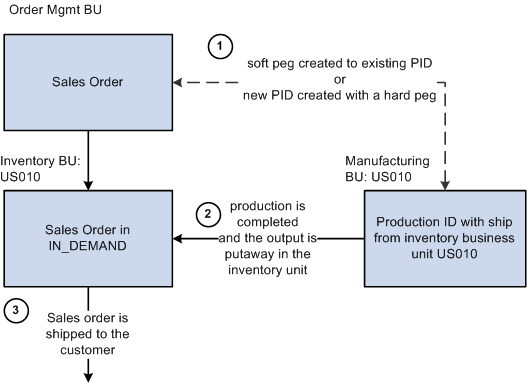
In this example, the PeopleSoft Manufacturing business unit of the production ID matches the Ship From Inventory business unit on the sales order; therefore, there is no interunit transfer.
Note: You can only peg to the primary output of a production ID.
The sequence of events in the process flow to peg a sales order to a production ID is:
Peg a sales order by using the Alternate Sources of Supply page in PeopleSoft Order Management to:
Create a soft peg between the sales order and an existing production ID.
Create a new production ID to fulfill the sales order. This is a hard peg between the sales order and production ID. The production ID is created when the sales order is saved. The Alternate Sources of Supply page uses the lead time fields located on the Define Business Unit Item - Manufacturing: General page to determine if the item can be manufactured in time to meet the scheduled shipment date. If the item can be manufactured in time, then a new production ID can be used as an alternate source.
When the sales order is saved it is inserted into the IN_DEMAND table in PeopleSoft Inventory.
The production is completed and the output placed in the inventory business unit. During putaway, the stock is soft-reserved or optionally allocated to the sales order. The peg status is changed to complete in the IN_PEGGING record and in the supply and demand transactions if either:
The production order is closed.
All the pegged quantity has been received and putaway (QTY_COMPLETE=QTY_PEGGED).
If the notification framework has been defined for the Message Dashboard, then a notification is sent to the owner of the peg when the stock completes putaway in the Inventory business unit.
The sales order is fulfilled in PeopleSoft Inventory and shipped to the customer.
This process flow diagram illustrates pegging a sales order to a production ID in PeopleSoft Manufacturing when the ship from inventory business unit is different between the sales order and the production ID. In other words, the stock is shipped to the customer from a different warehouse or distribution center than the manufacturing finished goods warehouse. The sequence of events in the process flow is explained below the diagram:

The sequence of events in the process flow to peg a sales order to a production ID when the ship from inventory business units are different between the demand and supply transactions is:
Use the Alternate Sources of Supply page in PeopleSoft Order Management to create and peg to a new production ID. When the sales order is saved, the PeopleSoft system:
Inserts the sales order into the IN_DEMAND table in PeopleSoft Inventory.
Creates a new production ID. The Alternate Sources of Supply page uses the lead time fields located on the Define Business Unit Item - Manufacturing: General page to determine if the item can be manufactured in time to meet the scheduled shipment date. If the item can be manufactured in time, then a new production ID can be used as an alternate source.
Creates an interunit transfer (material stock request) to move the finished stock from the production IDs ship from inventory business unit to the sales order's ship from inventory business unit. This stock request is placed in the IN_DEMAND table in PeopleSoft Inventory.
Creates two pegs. One peg between the production ID and the interunit transfer and another peg between the interunit transfer and the sales order. These pegs are stored in IN_PEGGING and its related tables.
The production is completed and the output placed in the inventory business unit with the same name as the manufacturing business unit; this is the production IDs ship from inventory business unit. During putaway, the stock is reserved or allocated to the outgoing interunit transfer. The status of the first peg is changed to complete if either:
The production order is closed.
All the pegged quantity has been received and putaway (QTY_COMPLETE=QTY_PEGGED).
The interunit transfer is used to ship the stock from the sending business unit to the destination business unit. When the stock is putaway in the sales order's ship from inventory business unit, the stock is reserved or allocated to the outgoing sales order. The status of the second peg is changed to complete in the IN_PEGGING record.
The sales order is fulfilled and shipped to the customer.
Note: If the notification framework has been defined for the Message Dashboard, then a notification is sent to the owner of the peg when the stock completes putaway in the inventory business unit.
This process flow diagram illustrates pegging a sales order to an interunit transfer (supply). The sequence of events in the process flow is explained below the diagram:

The sequence of events in the process flow to peg a sales order to an interunit transfer is:
Peg a sales order by using the Alternate Sources of Supply page to:
Create a soft peg between the sales order and an existing interunit transfer.
Create a new interunit transfer to fulfill the sales order. This is a hard peg between the sales order and interunit transfer. The interunit transfer (MSR) is created when the sales order is saved.
When the sales order is saved it is inserted into the IN_DEMAND table in PeopleSoft Inventory.
The supply-side interunit transfer is shipped from the sending business unit.
The supply-side interunit transfer is putaway in the destination business unit. During putaway, the stock is soft-reserved or optionally allocated to the outgoing sales order based on your setting in the pegging setup pages. In the IN_PEGGING table, if the pegged quantity (QTY_PEGGED field) is equal to the putaway pegged quantity (QTY_COMPLETE field) then the peg status in this table is updated to complete. If either the demand or supply order has no more open peg quantity, then the peg status on the order itself is also updated to complete.
If the notification framework has been defined for the Message Dashboard, then a notification is sent to the owner of the peg when the stock completes putaway in the inventory business unit.
The sales order is fulfilled and shipped to the customer.
This process flow diagram illustrates pegging a sales order to a requisition or purchase order. The sequence of events in the process flow is explained below the diagram:

The sequence of events in the process flow when pegging a sales order to a requisition or purchase order is:
Peg a sales order by using the Alternate Sources of Supply page to:
Create a soft peg between the sales order and an existing requisition or purchase order.
Create a new requisition or purchase order to fulfill the sales order. This is a hard peg. The purchase order is created when the sales order is saved. The requisition is created by the Requisition Loader process.
When the sales order is saved it is inserted into the IN_DEMAND table in PeopleSoft Inventory.
If a requisition was created, it goes through the sourcing processes in PeopleSoft Purchasing and is sourced to an interunit stock request or a purchase order or both. The interunit stock request is created in the sending inventory business unit.
If a purchase order was created, it is dispatched to the vendor.
The supplier ships the stock and it is received into the purchasing business unit. If the notification framework has been defined for the Message Dashboard, then a notification is sent to the owner of the peg when stock is received into the purchasing business unit.
The stock from the supplier or the sending inventory business unit (or both) is putaway in the destination inventory business unit. During putaway, the stock is soft-reserved or optionally allocated to the outgoing sales order based on your setting in the pegging setup pages. In the IN_PEGGING table, if the pegged quantity (QTY_PEGGED field) is equal to the putaway pegged quantity (QTY_COMPLETE field) then the peg status in this table is updated to complete. If either the demand or supply order has no more open peg quantity, then the peg status on the order itself is also updated to complete.
If the notification framework has been defined for the Message Dashboard, then a notification is sent to the owner of the peg when the stock completes putaway in the inventory business unit.
The sales order is fulfilled and shipped to the customer.
This process flow diagram illustrates hard pegging a direct ship from supplier sales order to a requisition or purchase order. The sequence of events in the process flow is explained below the diagram:

The sequence of events in the process flow for a direct ship from supplier sales order is:
Use the Alternate Sources of Supply page to create a new requisition or purchase order to fulfill the sales order. This is a hard peg. The purchase order is created when the sales order is saved. The requisition is created by the Requisition Loader process.
If a requisition was created, it goes through the sourcing processes in PeopleSoft Purchasing and is sourced to a purchase order.
The purchase order is dispatched to the supplier.
The supplier ships the stock directly to the customer.
This process flow diagram illustrates pegging a sales order with a configured product to a requisition in PeopleSoft Purchasing. The sequence of events in the process flow is explained below the diagram:

The sequence of events in the process flow for a configured product sourced from PeopleSoft Purchasing is:
A sales order with a configured product is created and saved. The demand line contains a configuration code generated by your PeopleSoft Product Configurator setup. This configuration code uniquely identifies the exact configuration for this product. The configured item is also lot-controlled. When the sales order is saved, it is inserted into the IN_DEMAND table in PeopleSoft Inventory.
The Requisition Loader process in PeopleSoft Purchasing, creates a requisition to fulfill the sales order. This requisition contains the configuration code. The Requisition Loader process also creates a soft peg between the sales order and the requisition. This soft peg is stored in IN_PEGGING and its related tables.
The requisition goes through the sourcing processes in PeopleSoft Purchasing and is sourced to a purchase order.
The purchase order is dispatched to the supplier.
The supplier ships the stock and it is received into the purchasing business unit. If the notification framework has been defined for the Message Dashboard, then a notification is sent to the owner of the peg when stock is received into the purchasing business unit.
The stock from the supplier is putaway in the inventory business unit. During putaway, the stock is lot-allocated to the outgoing sales order. Lot allocation reserves the incoming stock to the sales order at the business unit, item, lot, and storage location levels. In the IN_PEGGING table, if the pegged quantity (QTY_PEGGED field) is equal to the putaway pegged quantity (QTY_COMPLETE field) then the peg status in this table is updated to complete. If either the demand or supply order has no more open peg quantity, then the peg status on the order itself is also updated to complete.
If the notification framework has been defined for the Message Dashboard, then a notification is sent to the owner of the peg when the stock completes putaway in the inventory business unit.
The sales order is fulfilled and shipped to the customer.
This process flow diagram illustrates pegging a sales order with a configured product to a production ID in PeopleSoft Manufacturing when the ship from inventory business unit is the same on the sales order and the production ID. In other words, the stock is shipped to the customer from the manufacturing finished goods warehouse. The sequence of events in the process flow is explained below the diagram:
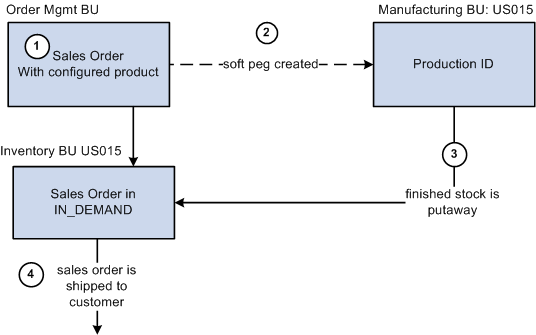
The sequence of events in the process flow for a sales order with a configured product to a production ID when the ship from inventory business unit is the same on both transactions is:
A sales order with a configured product is created and saved. The demand line contains a configuration code generated by your PeopleSoft Product Configurator setup. This configuration code uniquely identifies the exact configuration for this product. The configured item is also lot-controlled. When the sales order is saved, it is inserted into the IN_DEMAND table in PeopleSoft Inventory.
The Production Request process in PeopleSoft Product Configurator, creates a production ID to fulfill the sales order. This production ID in PeopleSoft Manufacturing contains the configuration code. The Production Request process also creates a soft peg between the sales order and the production ID. This soft peg is stored in IN_PEGGING and its related tables.
The production is completed and the output placed in the inventory business unit. During putaway, the stock is lot-allocated to the outgoing sales order. Lot allocation reserves the incoming stock to the sales order at the business-unit, item, lot, and storage location levels. The peg status is changed to complete in the IN_PEGGING record and in the supply and demand transactions if either:
The production order is closed.
All the pegged quantity has been received and putaway (QTY_COMPLETE=QTY_PEGGED).
If the notification framework has been defined for the Message Dashboard, then a notification is sent to the owner of the peg when the stock completes putaway in the inventory business unit.
The sales order is fulfilled and shipped to the customer.
This process flow diagram illustrates pegging a sales order with a configured product to a production ID in PeopleSoft Manufacturing when the ship from inventory business unit is different between the sales order and the production ID. In other words, the stock is shipped to the customer from a different warehouse or distribution center than the manufacturing finished goods warehouse. The sequence of events in the process flow is explained below the diagram:

The sequence of events in the process flow for a sales order with a configured product to a production ID when the ship from inventory business units are different between the demand and supply transactions is:
A sales order with a configured product is created and saved. The demand line contains a configuration code generated by your PeopleSoft Product Configurator setup. This configuration code uniquely identifies the exact configuration for this product. The configured item is also lot-controlled. When the sales order is saved, it is inserted into the IN_DEMAND table in PeopleSoft Inventory for the ship from inventory business unit on the sales order.
The Production Request process in PeopleSoft Product Configurator:
Creates a production ID to fulfill the sales order. This production ID in PeopleSoft Manufacturing contains the configuration code.
Creates an interunit transfer (material stock request) to move the finished stock from the production IDs ship from inventory business unit to the sales order's ship from inventory business unit. This stock request is placed in the IN_DEMAND table in PeopleSoft Inventory.
Creates two soft pegs. One peg between the production ID and the interunit transfer and another peg between the interunit transfer and the sales order. These soft pegs are stored in IN_PEGGING and its related tables.
The production is completed and the output placed in the inventory business unit with the same name as the manufacturing business unit; this is the production IDs ship from inventory business unit. During putaway, the stock is lot-allocated to the outgoing interunit transfer. Lot allocation reserves the incoming stock to the interunit transfer at the business-unit, item, lot, and storage location levels. The peg status is changed to complete if either:
The production order is closed.
All the pegged quantity has been received and putaway (QTY_COMPLETE=QTY_PEGGED).
If the notification framework has been defined for the Message Dashboard, then a notification is sent to the owner of the peg when the stock completes putaway in the inventory business unit.
The interunit transfer is used to ship the stock from the sending business unit to the destination business unit. When the stock is putaway in the sales order's ship from inventory business unit, the stock is lot-allocated to the outgoing sales order. Lot allocation reserves the incoming stock to the sales order at the business-unit, item, lot, and storage location levels. The peg status is changed to complete in the IN_PEGGING record.
The sales order is fulfilled and shipped to the customer.