Using Alternate Sourcing and Pegging
This topic provides an overview for alternate sourcing and pegging.
Page Name |
Definition Name |
Usage |
---|---|---|
Order Entry Form Page |
ORDENT_FORM_LINE |
Enter header and line information and perform advanced sourcing. |
ORDENT_SSRC_UPDT |
Use to view supply source options and to choose the optimum sources for this order line or schedule. You can choose one or more sources of supply from this page. This page is available only if you are using the Manual or Automatic Availability Option on the Order Entry Features page for the PeopleSoft Order Management Business Unit. |
|
Product Availability Page |
ORDENT_PRODAVAIL |
Use to access product availability from other databases. This is informational only. |
Alternate Sources of Supply Advanced Search Page |
ORDENT_SSRCH_PG |
Use to search by additional criteria. |
ORDENT_SSRC_DTL |
Use to view existing pegs and pegs for new purchase orders, production orders, requisitions, and interunit transfers. |
Alternate sourcing and pegging are closely related and enable CSRs to expand the tools they can use to meet customers demands and provide superior customer service. Alternate sourcing and pegging rely on security to control how the CSR can use the features.
See .Understanding Alternate Sources of Supply
See Understanding Feature Function Security
Alternate Sources of Supply
You can choose alternate sources of supply for the order line or schedule if you select the advance sourcing option (advanced or manual) at the Order Management Business Unit. On the Alternate Source of Supply page during order entry, you can change the ship from business unit or look at alternate sources and enter different quantities for each of the sources. Inventory on-hand availability sources as well as sourcing options from new requisitions, new purchases orders, and new interunit MSRs are defined in the Alternate Sources arbitration plan and rules and retrieved by the sourcing engine. Additionally, existing supply sources (existing requisitions, purchase orders, interunit transfers, and production orders) are retrieved by the sourcing engine. These existing sources of supply do not require you to set up alternate sources of supply arbitration plans and rules. However, you must have the authority defined for your user ID setup in Inventory pegging security.
The CSR enters the quantity they want from each supply source. If the CSR chooses existing incoming supply to source the order line or schedule, the supply is soft pegged to the sales order at save time of the order. If the CSR chooses to source the order line or schedule from a new requisition, purchase order, or interunit transfer, the supply document is created and hard pegged to the order schedule when the order is saved and additional information may be required from the CSR. For new requisitions, the requisition will be pegged to the sales order when the PO_REQLOAD (Purchasing Requisition Loader) process creates the requisition.
The existing incoming supply sources are filtered through the new Inventory pegging security definition for the user ID of the current user and appear after the alternate sourcing arbitration plan/rules sourcing options in the grid. Once a supply source option is selected, the source type and disposition are stored on the line or schedule. Sourcing is done at the order line level if only one schedule exists; otherwise, it is performed at the schedule level. For each source that is selected for the order line, a new order schedule is created. If sourcing is being done on an order schedule and multiple sources are selected, the original schedule is updated and additional schedules are created.
If the CSR wants to change the supply source, the system verifies that the change is allowed. For example, the PO may already be dispatched. If the change is allowed and the supply is hard-pegged to the order schedule, Order Management will automatically update the supply document with cancellations or quantity changes. If the change to the supply document is not allowed or the supply is soft-pegged to the order, the change is still allowed on the order schedule, but only a notification is sent to the supply document owner.
The full range of Alternate sources of supply functionality can be done online. In batch, alternate sourcing is performed only for distribution network and Inventory Business Unit on hand quantity sources. The additional source options for new purchase orders, new production orders, requisitions, and interunit MSRs are not available with batch processing. If the Order Management availability option is set to Automatic (advanced sourcing), the order completion process must be performed before the advanced sourcing lookup.
Pegging
Through alternate sourcing, the CSR can choose to select on-hand available quantity from inventory business units outside the standard distribution network. Selecting quantity on-hand and direct-shipping from the warehouse is equivalent to assigning the Inventory Business Unit as the ship-from business unit on the order schedule. The item ships from that warehouse directly to the customer. Alternatively, the CSR can peg or tag lines during sales order entry to existing incoming supply or new supply to ensure that items are reserved to the order as soon as they become available in the warehouse.
The CSR can peg to:
Existing interunit transfers
Existing production orders
Existing purchase orders
Existing requisitions
Inventory Business Unit, direct receipt (new interunit transfer)
Distribution network, direct receipt (new interunit transfer)
New production order
New purchase order
New requisition
In addition, from the alternate sources of supply page, the CSR can choose supply sources of:
Distribution network
Inventory Business Unit
Note: These quantity-on-hand supply sources are not pegged when the disposition of the items is direct ship-to the customer. The ship-from business unit on the order schedule is changed to the source Inventory Business Unit selected and the demand for these sources is reserved based on the inventory business unit definition for the item. If the disposition of the supply is direct receipt, a new interunit transfer MSR is created when the order is saved.
After the CSR selects the type of supply, he determines whether it should be a direct ship (ships directly to the customer) or direct receipt (ships to the warehouse and then to the customer). There can be multiple sourcing options displayed and selected. Each selected supply source will be broken into separate schedules once the options are accepted by the CSR.
Note: The disposition of the items (direct ship or direct receipt) cannot be changed for existing supply.
There are two types of pegs:
A soft peg links an outgoing order to the quantity included in an incoming supply. For example, a sales order for 10 units is soft pegged to an incoming purchase order with 2,000 units. When a soft peg is changed or canceled, the peg is changed but the incoming supply (in this case the purchase order) is not changed. A notification is sent to the buyer informing them that a change in the demand pegged to the PO has taken place. Soft pegs are useful when items are in short supply and you want to peg higher priority customer orders to specific supply.
A hard peg is created when a sales order (demand) creates a purchase order, requisition, or interunit transfer (supply) to fulfill it. Hard pegs are only created from the sales order when adding a Direct Ship or Direct Receipt. All other orders would be considered soft pegs and will result in notifications only upon changes. When a hard peg is changed or canceled, not only is the peg changed, but also the incoming supply is changed. For example, a sales order for 10 units is hard pegged to an incoming purchase order with 10 units. If the sales order is changed to four units, then the purchase order is changed to 4 units. Hard pegs are useful for make-to-order items or special products.
Here are examples of hard pegs:
A new Direct Ship purchase order (formerly a drop ship purchase order)
A new Direct Receipt purchase order or a Direct Receipt interunit transfer that is created from a sales order
A new Direct Ship requisition (formerly a drop ship requisition)
A new Direct Receipt requisition that is created from a sales order
A new Direct Ship production order that is created from a sales order when the Inventory business unit is same as the Manufacturing business unit.
Note: All other orders would be considered soft pegs.
The CSR can make changes to the pegs from the sales order alternate sources of supply page by changing the quantity requested or selecting new sources of supply. However, if the changes are not possible from the sales order, the CSR can use the Pegging Workbench to make additional changes. The CSR could also perform the pegging from the workbench instead of from the Alternate Sources of Supply page.
Note: Creating the pegs from the pegging workbench will only create soft pegs.
Pegging can occur as long as the sales order demand is not past the Unfulfilled state in PeopleSoft Inventory. However, the CSR cannot peg product kits, configured kits, ATP or VMI items. If the demand is already soft-reserved, it cannot be pegged. Choosing to peg an existing schedule that is already soft-reserved will cancel the reserved demand and create new pegged demand for the schedule. A peg cannot be modified from the sales order if more than one unfulfilled demand line exists for the schedule (a backorder has been created). You must use the pegging workbench (a link is provided from the sales order alternate sources page) to modify the pegs.
To peg to existing supply documents, the CSR must have the appropriate security defined. The Inventory pegging user security has to be set up enabling the user ID to peg supply documents to sales order demand.
You can set up notifications to notify the CSR if changes are made to any documents that are pegged. Similarly, notifications can be sent to the supply owner if changes are made to the sale order. The system has preestablished notifications set up using the Message Dashboard. You can use the existing notifications or add notifications.
If an order goes on hold when pegging to a PO, then the Pass to Purchasing flags will determine whether the PO is created or whether a requisition is created. The PO is created if the Pass to Purchasing flag for the hold is set to Yes. If the Pass to Purchasing flag is set to No, a requisition will be created using requisition loader. When the order hold is removed, the requisition loader should be run which will create a requisition and peg the order to it. When the requisition becomes a PO, the order will be then pegged to the PO.
Use the Claimback/Supply Source tab in the line grid area of the Order Entry Form page (ORDENT_FORM_LINE) or Shipment Schedules page
Navigation:
Note: The Find Alternate Supply Sources button appears if advanced sourcing is used for the PeopleSoft Order Management Business Unit. The Manual or Automatic Availability Option must be selected on the Order Entry Features page for the business unit.
Field or Control |
Description |
---|---|
Source Type |
The value is provided by default from the highest priority sourcing option returned from the supply source engine if the availability option on the Order Management Business Unit is Automatic. Otherwise, it is set based on the alternate source of supply you choose. |
Disposition |
The value is provided by default from the highest priority sourcing option returned from the supply source engine if the availability option on the Order Management Business Unit is Automatic. Otherwise, it is set based on the alternate source of supply you choose. If you change the sourcing option on the Alternate Sources of Supply page, it will update the value. Note: If multiple schedules are available for the line, the source type becomes the original default (Distribution Network or Inventory Business Unit) and the Disposition is Direct Ship. If the product is marked as Direct Ship from Supplier, then the Source Type is New Requisition and the Disposition is Direct Ship. |
|
Click the Find Alternate Sources button to perform additional sourcing on the Alternate Sources of Supply page. |
Supply Source Data |
Click the link to access the Supply Source Detail page. |
Claimback ID |
The claimback defaults and can be changed. |
Use the Alternate Sources of Supply page (ORDENT_SSRC_UPDT) to use to view supply source options and to choose the optimum sources for this order line or schedule.
You can choose one or more sources of supply from this page. This page is available only if you are using the Manual or Automatic Availability Option on the Order Entry Features page for the PeopleSoft Order Management Business Unit.
Navigation:
Click the Find Alternate Supply Sources link from the Line or Claimback/Supply Source tab in the line grid area on the Order Entry Form page.
Click the Find Alternate Supply Sources link from the Line or Claimback/Supply Source tab in the line grid area on the Shipment Schedules page.
This example illustrates the fields and controls on the Alternate Sources of Supply page (1 of 2). You can find definitions for the fields and controls later on this page.

This example illustrates the fields and controls on the Alternate Sources of Supply page (2 of 2). You can find definitions for the fields and controls later on this page.
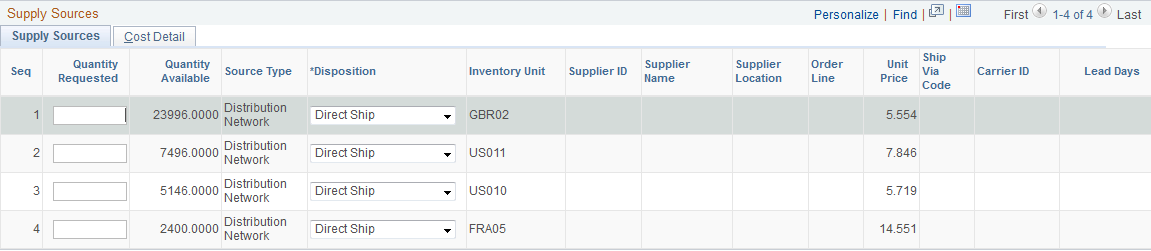
These restrictions exist for using advanced sourcing, depending on the item and product attributes:
Product kits can only be sourced from Inventory Business Units or Inventory Business Units from a Distribution Network with a Direct Ship Disposition. You can perform advanced sourcing, but the availability of the kit components will not be validated until the order is saved. The system will return Inventory Business Units with zero availability because sourcing is performed at the product kit product ID level. Only Inventory Business Units that stock the component items will be returned.
Configured items can be sourced using alternate sourcing. No advanced sourcing options, however, can be used for configured product kits.
Non-inventory items can be sourced using Direct Ship requisitions or purchase orders.
Non soft-reserved items and configured item cannot be sourced from a requisition, purchase order, interunit transfer, or production order. If it is defined on the sources of supply formula, it will be skipped.
If an item is marked as a RFQ item (request for quote) on the Purchasing Controls page of the Purchasing Item Attributes component, you will not be able to create a new purchase order.
The PeopleSoft Order Management Business Unit, order, line and schedule, and the Product ID and associated Item ID display from the order.
Each line of the order line or schedule is sourced individually. If you use multiple sourcing options, a schedule is created for each of the sourcing options.
For new order lines or schedules, the sourcing options retrieved from the sourcing engine appear first. They appear in the order defined on the sourcing arbitration plan. If the user is authorized to peg to existing supply documents (requisition, purchase orders, interunit transfers, or production orders), these existing supply sources appear following the sourcing engine supply options.
For existing order lines or schedules, the existing supply source pegs appear first with the quantities that are pegged to the supply. Then, the sourcing options retrieved from the sourcing engine appear in the order defined on the sourcing arbitration plan. If the user is authorized to peg to existing supply documents (requisition, purchase orders, interunit transfers, or production orders), these existing supply sources appear following the sourcing engine supply options.
Field or Control |
Description |
---|---|
Cross-CPU Product Availability |
Click the link to access the Product Availability page. |
Ship From |
Initially appears from the schedule. You can change the value, but you need to select the Search Sources button to display new results in the grid at the bottom of the page. This is the ship-from business unit from where the items will ship to the customer. |
Alternate Source Type |
Use to narrow down the types of sources displayed for the line or schedule. Only the source type that is selected will be returned to the supply sources grid or use the All Sources option to search for all the valid sources based on the options set up from the arbitration plan associated with the Shipping and Returns page on the PeopleSoft Order Management Business Unit. |
Display Row for each Supplier |
If you select this option, all of the suppliers will display for new purchase orders and requisitions. If this option is not selected, you can select the supplier from the available options. |
Include Zero Availability |
Select if you want the system to include inventory business units with quantity available of zero in the results. |
Search Sources |
Click the button to display your selection in the Supply Sources grid at the bottom of the page. |
Advanced Search |
Use to refine your search even further. For example, you could search for Direct Receipt Disposition types. |
Quantity Ordered and Quantity Scheduled |
Displays the total quantity ordered for the line and the quantity scheduled for the current schedule. |
Quantity Pegged |
Displays the supply pegged to the schedule. The pegged quantity will also be displayed in the first lines in the grid if you are viewing the page after the initial schedule has been pegged. |
Quantity Reserved |
Displays the amount that has already been reserved to the schedule for the ship-from BU. |
Calculate Quantity |
Click to calculate the remaining quantity to be sourced. |
Remaining Quantity |
Displays the amount that is left to source. |
Accept |
When you have made your selections and are satisfied with the sourcing, click the button to source the schedule from the alternate sourcing chosen in the grid and return to the sales order. The results are validated, and you will be prompted for required fields. A separate schedule is created for each sourcing option you choose.
|
Cancel |
Click to return to the order line or schedule without accepting the sourcing options. |
Note: If you want the requisition or purchase order shipped to your warehouse, you can use the alternate sources page to select the direct receipt disposition for the items. Note that the item must be defined as a stocked item to receive the items into the destination warehouse. If the business unit item definition does not exist on the destination warehouse, then the system will create one for you based on the item template defined in the Inventory business unit transfer item copy definition.
Note: When you create a direct receipt purchase order from alternate sources of supply, the location address of the Inventory business unit is defined as an override address on the purchase order line to ensure that the items are shipped to the exact location of the warehouse.
Choosing Alternate Sources on the Supply Sources Tab
The results of the sources appear in the grid.
Field or Control |
Description |
---|---|
Seq (sequence) |
The results appear in this order:
|
Quantity Requested |
Enter an amount to be sourced. You can select multiple source options by entering quantity in different fields. Each quantity sourced becomes its own schedule. |
Quantity Available |
Displays the amount that is available for each Inventory business unit. |
Source Type |
Displays the source possibilities. The rows of the grid appear based on the sort option selected on the arbitration plan for alternate sources of supply. If pegs exist, then they appear first. They are followed by the sourcing engine sources of supply and then the existing supply documents if the user has the authority to peg to existing supply. |
Disposition |
For new sourcing, you can select the shipping option; otherwise, the field is unavailable for entry. Values are: Direct Receipt: Ship from the supplier or warehouse to a warehouse. Direct Ship: Ship from the supplier or warehouse to a customer. |
Inventory Unit |
The Inventory business unit appears for Inventory business unit and Network source types. |
Supplier ID |
If you set up alternate sources of supply rules, the supplier ID appears based on your sourcing formula. Otherwise, all of the valid suppliers for the item are available for you to choose from the prompt on the supplier ID field. The Supplier Name fields appears. For new requisitions and purchase orders, you can select from the valid list of suppliers. |
Supplier Location |
For existing sources, the field is display-only. For new sources, you can use the search button to select from a list of valid locations for the selected supplier. |
Order Line |
Displays line information for the purchase order. |
Unit Price |
Displays the purchase price of the item for source types of requisition or purchase order. This is the unit cost for Inventory business unit or Network source types. For purchase orders, the Unit Price is the cost that is used to calculate the margin. |
Get Price |
For new purchase orders where the Supplier ID was selected, click the button to retrieve the price that will be defaulted to the new purchase order. The price will be updated in the Unit Price field. |
Field or Control |
Description |
---|---|
Ship Via Code |
Optionally select for Distribution Network and Inventory business unit source types where the disposition is direct receipt and you are creating an interunit transfer. |
Carrier ID |
Displays the ID of the freight carrier. Note: You can edit the ID only when the disposition is direct receipt. |
Lead Days |
If the Ship Via Code appears, then the interunit transportation lead times will be included for Distribution Network and Inventory business unit source types. The supplier lead time appears for new supply for purchase orders or requisitions. For existing pegs or existing supply not yet pegged, the lead time is calculated using the dates on the schedule. The production portion of the Lead Days displayed is based on the schedule quantity. If the user changes the new production quantity, the Lead Days will be recalculated based on the new quantity. If the lead days is blank, the lead days are less then zero. |
Note: If you want to create an interunit transfer (MSR), select either Inventory Business Unit or Distribution Network in the Source Type field and Direct Receipt in the Disposition field.
If you want to create supply shipped directly from the supplier to your customer (drop ship), select either New Requisition or New Purchase Order in the Source Type field and Direct Ship in the Disposition field.
Changing Supply Information
Sourcing options for order schedules that were already pegged can be changed on the alternate sources of supply page. Schedules with existing pegs appear at the top of the supply sources grid with the peg quantity supplied by default to the requested quantity field in the grid. You can change the quantity to change the peg. If the supply is hard-pegged, the supply document will be automatically updated. If the supply is soft-pegged, a notification is sent to the buyer or the warehouse manager depending on the supply type.
Hard-pegged requisitions are updated through the Requisition Loader process.
Hard-pegged purchase orders are updated when you save the sales order if the update is allowed. You define when the purchase order update is allowed on the Order Management business unit. Update is allowed up to the purchase order due date or up to the time the purchase order is dispatched to the supplier.
Hard-pegged interunit transfers are updated if the demand change configuration for the source inventory business unit allows changes to be made from Order Management, depending on the state of the demand in fulfillment.
Changes for soft-pegged supply only results in a notification to the buyer or the warehouse manager, depending on the supply type. Changes for hard-pegged production orders will only be made if the status is Entered, Firmed or Released. When changes are made to a sales order with a direct receipt production order, the changes are only applied to the interunit transfer since the interunit transfer is hard-pegged to the sales order. Changes are not made to the soft-pegged production order. However, if a schedule change results in the interunit transfer being cancelled, the production order will also be cancelled if the order output quantity is equal to the interunit transfer quantity and the production order status is Entered, Firmed or Released.
Note: If the purchase order has already been created for the requisition, changes made on the sales order will take effect immediately on the purchase order via the alternate sourcing order change functionality. Only the purchase order will be updated with the changes.
View Cost Information on the Cost Detail Tab
The fields display additional pricing and cost information.
Field or Control |
Description |
---|---|
Total Unit Cost |
The unit cost of the item multiplied by the markup percent and the transportation cost. |
Unit Cost |
The unit cost of the item or the transfer price. |
Transfer Price |
The cost to transfer the item out of the PeopleSoft Inventory Business Unit from either the Inventory Business Unit item or Inventory Business Unit level. |
Transportation Cost |
The transit cost between two PeopleSoft Inventory business units, the Inventory Business Unit item level or Inventory Business Unit level. |
Price Markup % |
Percent of price markup defined at either the PeopleSoft Inventory Business Units item level or Inventory Business Unit level. If defined, this price markup is applied to the unit cost. |
Use the Supply Source Detail page (ORDENT_SSRC_DTL) to use to view existing pegs and pegs for new purchase orders, production orders, requisitions, and interunit transfers.
Navigation:
Click the Supply Source Data link on the Claimbacks/Supply Source tab in the line grid area of the Order Entry Form page.
Click the Supply Source Data link on the Claimbacks/Supply Source tab in the line grid area of the Shipment Schedules page.
Current Pegs
Existing purchase order, requisitions, interunit transfer and production order pegs for the entire order appear at the top of the page. Each peg shows the information and the quantity pegged, the order type, the link to view the document for the peg, and a button to take you to view or update the supply document.
New Pegged Supply for Purchase Orders, Requisitions, Interunit Transfers and Production Orders
Below the existing pegs grid, the new supply source detail information is presented to the CSR where it can be changed prior to saving the sales order and creating the new supply documents such as new requisition, purchase order, interunit transfer or production order. New requisition lines and new purchase order lines are consolidated by Supplier ID and location. New interunit transfer lines are consolidated by source inventory business unit.
Once the new supply document is created, the supply detail information is no longer available, and the CSR uses the "Edit Document" button in the top of the grid to view or update the actual supply document that was generated and pegged to the sales order schedule.
For new requisitions, the quantity cannot be changed. The purchase quantity for the requisition is set by the Requisition Loader and is always set to the order schedule quantity. A hard-peg is created when the process creates the requisition. If you increase the requisition quantity in PeopleSoft Purchasing after it has been created, the hard-peg to the sales order is changed to a soft-peg.
For new purchase orders, the purchase quantity can be changed. If you increase the purchase quantity so that it is greater than the sales order schedule quantity, the order quantity is pegged to the PO and a hard peg is created. The hard peg is not removed until the purchase order is received at the warehouse, at which time the order quantity is reserved and possibly allocated. The remaining quantity received is put away to stock as available quantity on hand.
For new direct ship production orders, the production quantity can be changed. If you increase the production order quantity to be greater than the sales order schedule quantity, the order quantity is pegged to the production order and a hard peg is created. The hard peg is not removed until the production order is completed. The order quantity is reserved and possibly allocated at this time. The remaining quantity produced is put away to stock as available quantity on hand.
For new direct receipt production orders, the production quantity can be changed. This will cause the interunit transfer necessary to receive the goods to increase by the same amount. The order quantity is pegged to the interunit transfer and a hard peg is created. A soft peg will be created between the production order and the interunit transfer. In addition, the carrier and ship type can be changed for the interunit transfer. The hard peg is not removed until the interunit transfer is received and put away. The order quantity is reserved and possibly allocated at this time. The remaining quantity received is put away to stock as available quantity on hand.
Note: After you perform initial sourcing, you can change the status of the line or schedule to Pending and save the order so that you can update the sourcing information at a later time. When you update the order, you can access the Supply Sources Detail page and make changes. You cannot perform sourcing for a line or schedule that is in Pending status, the status must be set to Open initially.