Analyzing Production Variances for Standard Cost Items
When you close a production ID or production quantity for accounting, PeopleSoft Manufacturing calculates variances. The variances capture the differences between the cost of what is built and the frozen standard cost of the item. The process breaks down the variances by reason, such as: configuration, usage, component yield, lot size, routing process, rework, teardown, outside processing, and output mix. These variances are summarized up to the production ID and cost element level and are used for accounting and analysis purposes.
Once closed for accounting, PeopleSoft Manufacturing calculates these production variances:
Variance Type |
Accounts For |
Calculation |
Transaction Group |
---|---|---|---|
01- Configuration |
See Understanding the Configuration Variance section below this table. |
Summarized for all components, calculated by cost element: [(ISSUE_QTY + YIELD_QTY) * component's this level and lower level costs] - component usage variance - component yield variance - (production ID completion qty * prodcost LL cost) - component total production scrap cost - mix variances- operation yield. |
261 – Material Variances |
02 - Usage |
Cost that is associated with the difference between the component's current scheduled quantity and the actual issue quantity. The current scheduled quantity is based on the number of components that should have been used for the completed assemblies. The actual issue quantity is the number of good components that are consumed for the completed assemblies or kitted to the production ID. Usage variance is not calculated for floor stock or expensed items. |
[ISSUE_QTY - (CURR_SCHED_QTY * YIELD/100)] * each element of the component's costs summarized by this level and lower level. The component's current scheduled quantity is adjusted to take into account assemblies that are scrapped before where the component is required. Additionally, the current scheduled quantity is adjusted again when the full production quantity is not completed but production is closed. |
261 – Material Variances |
03 - Component yield |
Cost associated with the difference between the expected and the actual component yield loss of a component in production. Component yield variance is not calculated for floor stock or expensed items. |
[(YIELD_QTY - (Current Schedule Qty * 1 - YIELD/100)] * component cost by cost element summarized by this level and lower level. The component's current scheduled quantity is adjusted to take into account assemblies that are scrapped before the component is required. Additionally, the current scheduled quantity is adjusted again when the full production quantity is not completed but production is closed. In this manner, the current schedule quantity is based on the quantity completed multiplied by the quantity per for the component. |
261 – Material Variances |
04 - Labor (and Machine) Lot size |
Difference in per-unit setup, fixed run, and postproduction conversion costs when the system completes assemblies (with a quantity that differs from the average order quantity [AOQ]) at an operation. Lot size variances could occur if you have split a production ID and the parent and child production ID quantity are each less than the assembly item's AOQ. |
For labor and machine lot size variance: Calculated by operation: (AOQ - assembly quantity issued to the operation) * (setup, fixed run, or postproduction operation time expressed in hours * corresponding labor or machine rate/AOQ). |
262 – Conversion Variances |
05 - Routing process |
Financial impact of changes in an item's routing for a production ID or production run. This includes adding, deleting, or skipping operations and changing work centers or tasks. Note: The Routing Process variance is not displayed on the Production Variance Drilldown page. |
Summarized by cost element: Earned labor, machine, and overhead costs from SF_EARNCONCOST - lot size variance - this-level-only assembly scrap - this-level-only assembly completions. |
262 – Conversion Variances |
08 - Material Lot Size |
A material lot size variance accounts for the difference between the production quantity and the AOQ for those components whose production quantity is per order. Lot size variances could occur if you have split a production ID and the parent and child production ID quantity are each less than the assembly item's AOQ. |
(AOQ - assembly quantity issued to the operation) * component's this-level plus lower-level costs. |
261 – Material Variances |
09 - Rework (Material) Expense |
Total charges that are incurred for the rework production ID are compared to the standard cost of the reworked assembly. The difference is the rework expense. |
Standard cost of the reworked assembly - total charges that are incurred for the rework. |
263 – Rework Expense |
10 - Rework Labor Expense |
263 – Rework Expense |
||
11 - Outside Processing Variance PPV |
The difference between the standard outside processing costs of the operation and the supplier's price as stated on the purchase order that is used to manage the subcontracted operation. |
(PRICE_PO from the production ID's purchase order - outside processing cost from the production ID's operation list) * quantity that is completed at the subcontract operation. |
264 – Outside Processing PPV |
12 - Mix |
The difference between the actual outputs and the expected outputs. |
Calculated and totaled by cost element. Applied to all outputs (co-product, by product, waste, and recycle). OUTPUT_LIST.SCHED QTY - OUTPUT_LIST.COMP QTY) * (prodcost TL cost + prodcost LL cost) |
261 – Material Variances |
13 - Teardown Material Expense |
Total charges that are incurred for the teardown production ID are compared to the standard cost of the assembly that is to be torn down. This variance includes any components that are lost in the teardown process. |
(Standard cost of the assembly to tear down + standard cost of any additional components) - (standard cost of component outputs or assembly scrap) |
265 – Teardown Variance |
14 - Teardown Conversion Expense |
Total charges that are incurred for the teardown production ID are compared to the standard cost of the assembly that is to be torn down. This always includes the This Level Labor costs of the assembly that is torn down. It could also include additional labor and overhead costs if a teardown operation list is used. |
(Standard cost of the assembly to tear down + any labor and overhead added) - (standard cost of component outputs or assembly scrap) |
265 – Teardown Variance |
15 – (Operation) Yield |
Difference between actual scrap and expected scrap at the operation when there is operation yield on the operation list. The difference in scrap quantity is costed at the cumulative cost for the operation at which it is incurred. |
Calculated by cost element: {(actual scrap – [operation start quantity * (1– (operation yield/100))]} * cumulative operation cost |
262 – Conversion Variances |
Note: Variances can be incurred depending on the item's unit of measure rounding and precision. If you have a unit of measure for an item that has a precision of 0 to the right of the decimal, the item can be issued only in whole units. If the item is a component on a BOM and has a component yield factor, the system schedules the component on a production ID or schedules only in whole units. However, the cost of the assembly item using the component is calculated by using the fractional quantity. This could result in small variances, because the sum of the scheduled component costs is greater than the cost of the total completed number of assemblies using the component.
Understanding the Configuration Variance
The configuration variance consists of variance amounts caused by:
Difference between the cost of the production ID or production quantity's bill of material (BOM) and the cost of the bill that is used to determine the current production costs.
Changes to AOQ.
Quantity differences due to rounding to the appropriate unit of measure.
Any remaining variance amounts not already included in another production variance.
If the Enable Variance Drilldown check box was selected at the business unit level, then any configuration variance is stored in the Configuration Variance Detail record (SF_CFGVAR_DET) by the Close Production process. The configuration variance amounts are documented in this record with a message set and message number to identify the reason for the amount, including:
Message Set |
Message Number |
Message Text |
Description |
---|---|---|---|
15401 |
252 |
Component Std Cost or Qty-Per changed |
The standard cost or quantity per amount has been changed on the bill used for production. |
15401 |
253 |
Component cost not in ASSY Frozen Std |
A component cost in production does not match the frozen standard cost of the BOM. |
15401 |
254 |
Added to component list, not in the frozen std |
The cost of a component that was added to production but was not included in the BOM. |
15401 |
255 |
Component Deleted |
A component was deleted from production but was part of the BOM. |
15401 |
261 |
Misc Config Variance by Cost Element |
Miscellaneous variances that could be due to rounding, changes in quantity per order, and other reasons. |
Reviewing Production Variances Reports for Standard Cost Items
PeopleSoft Manufacturing provides the online Production Variance Drilldown component (Production Control, Close and Analyze Production, Production Variance Drilldown) to view the calculations of each production variance. The production variance calculation details are retrieved from the Production Variance Detail record (SF_VARS_DETAIL) and the Configuration Variance Detail record (SF_CFGVAR_DET ) that are populated during the Close Production process (SFS1100) for production IDs and schedules with the status of Closed for Accounting.
In addition, after the Cost Accounting Creation process has been run, the Posted Variance Drilldown page (Cost Accounting, Inventory and Mfg Accounting, Analyze Production Costs, Posted Variance Drilldown) can be used to view the accounting lines related to the production variances. Links on both the Production Variance Drilldown page and the Posted Variance Drilldown page enable you to drill down into more detailed information or drill up into summary information.
PeopleSoft Cost Management provides two reports for analyzing variances:
Field or Control |
Description |
---|---|
Potential Production Variance Report |
Lists potential variances that exist in production before closing the production IDs and schedules for accounting. You can generate the report when you are in a production status that is in process, pending complete, complete, or closed for labor. Review this report periodically so that you can act to correct potential production problems. In addition, the system can send the report to the appropriate individuals through workflow to notify them of the potential variances. When this report is run, no accounting close occurs, and no variances are posted. This process only calculates and reports the variances based on the current snapshot of production. |
Production Variance Report |
Lists production variances that exist after you close production IDs and schedules for accounting. Reports all PeopleSoft Manufacturing variances except efficiency and utilization. |
Page Name |
Definition Name |
Usage |
---|---|---|
CE_PRD_VAR_INQ |
View accounting lines related to production variances calculated in PeopleSoft Manufacturing. Links on this page enable you to drill down into more detailed information or drill up into summary information. |
Use the Posted Variance Drilldown page (CE_PRD_VAR_INQ) to review accounting lines posted for production variances produced for a production ID or schedule in PeopleSoft Manufacturing.
Navigation:
This example illustrates the fields and controls on the Posted Variance Drilldown page. You can find definitions for the fields and controls later on this page.
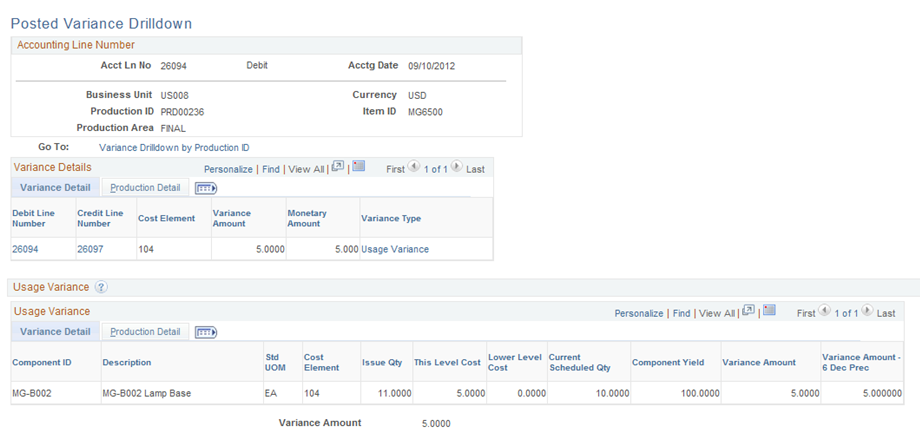
The Posted Variance Drilldown page displays only one accounting line number at a time.
Note: In order to view accounting line data using the Posted Variance Drilldown page, the production ID or schedule must be in the status of Closed for Accounting and you must first run the Close Production process to populate the Production Variance Detail record (SF_VARS_DETAIL) and the Configuration Variance Detail record (SF_CFGVAR_DET ) and then run the Cost Accounting Creation process to generate accounting entries.
The Account Line Number group box displays information about the accounting line reviewed on this page.
Click the Variance Drilldown by Production ID link to access the Production Variance Drilldown page where you can review the calculation details of the production variances produced for a production ID or schedule. The Production Variance Drilldown page displays only one production ID or schedule at a time.
Variance Details
The Variance Details group box displays the accounting entry details, amounts, and different variance types. The Production Detail tab displays information about the accounting entry.
Field or Control |
Description |
---|---|
|
Click the Download icon to move the data in the displayed tab to a Microsoft Excel spreadsheet. |
Debit Line Number and Credit Line Number |
Displays the accounting line number. Click this link to access the Production Variances- Transaction Details page to view additional transaction details related to the production variance. |
Variance Type Group Box
For the production variance that created this accounting line, you can display a group box for the specific variance. The title of the group box is the variance type name. All required information used to calculate the variance is included in the Variance Detail tab. The fields displayed are different based on the variance type. The Production Detail tab displays information about the production ID or schedule.
Field or Control |
Description |
---|---|
|
Click the Embedded Help icon to display information about the production variance and how it is calculated. |
|
Click the Download icon to move the data in the displayed tab to a Microsoft Excel spreadsheet. |