Pegging in PeopleSoft Maintenance Management
A work order in PeopleSoft Maintenance Management can be pegged as demand to an interunit transfers (supply-side) in PeopleSoft Inventory and requisitions or purchase orders from PeopleSoft Purchasing. Work orders can only use soft pegs. Pegged supply received and putaway in an inventory business unit can be reserved or allocated to the work order. If you are working with a non-inventory item ID or description-only item, then the method for pegging a work order differs from an order using an inventory ID.
A peg for a work order can by created using the:
(inventory items only) Pegging Workbench.
The workbench displays work order tasks with inventory items to be pegged to. In addition, you can peg a requisition or purchase order to a work order task that you created on the workbench using the Add Work Order Material link.
(inventory items only) Work Order-Schedules page in PeopleSoft Maintenance Management.
Add/Update Requisitions component in PeopleSoft Purchasing.
Add/Update POs component in PeopleSoft Purchasing.
Add/Update Express POs component in PeopleSoft Purchasing.
Create Requisitions component in PeopleSoft eProcurement.
You can access peg chains and create new peg chains by accessing the Pegging Workbench or view peg chains by accessing the Pegging Inquiry page from the Work Order - Schedules page in PeopleSoft Maintenance Management.
Note: The link to the Pegging Workbench is only visible if the User Security page gives access to the user ID.
This process flow diagram illustrates pegging a work order with an inventory item ID to an incoming interunit transfers. The sequence of events in the process flow is explained below the diagram:
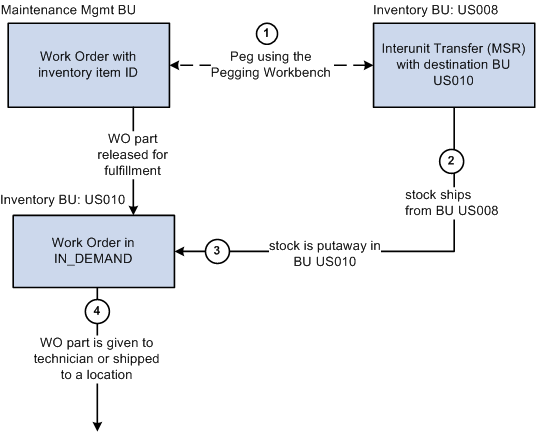
The sequence of events in the process flow when pegging a work order with an inventory item ID to an incoming interunit transfers is:
Peg is created using the Pegging Workbench. When a work order part is pegged, it is placed in the IN_DEMAND table for fulfillment, if it is not already there. The interunit transfer's destination business unit must match the work order's inventory business unit.
The supply-side interunit transfer is shipped from the sending business unit.
The supply-side interunit transfer is putaway in the destination business unit. During putaway, the stock can be soft-reserved or allocated. In the IN_PEGGING table, if the pegged quantity (QTY_PEGGED field) is equal to the putaway pegged quantity (QTY_COMPLETE field) then the peg status in this table is updated to complete. If either the demand or supply order has no more open peg quantity, then the peg status on the order itself is also updated to complete.
If the notification framework has been defined for the Message Dashboard, then a notification is sent to the owner of the peg when the stock completes putaway in the Inventory business unit.
The work order is fulfilled in PeopleSoft Inventory using the picking or issue features for work orders in the Fulfill Work Orders menu. The work order part is given to a technician or delivered to a location.
This process flow diagram illustrates pegging a work order with an inventory item ID to a requisition or purchase order. The sequence of events in the process flow is explained below the diagram:
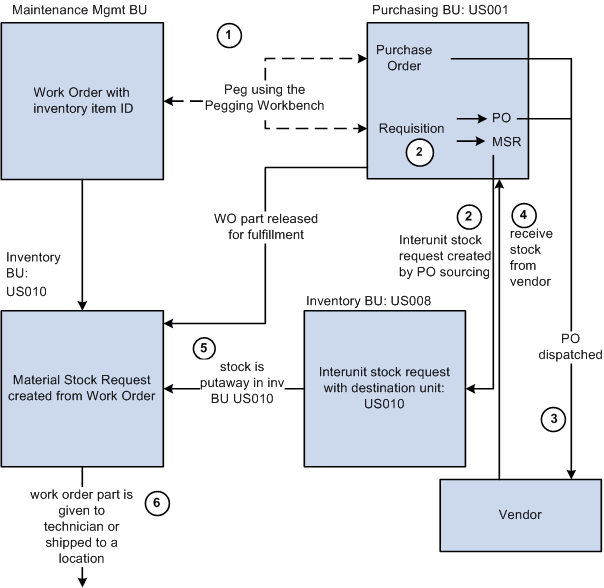
The sequence of events in the process flow when pegging a work order with an inventory item ID to a requisition or purchase order is:
Peg is created using the Pegging Workbench. When a work order part is pegged, it is placed in the IN_DEMAND table for fulfillment, if it is not already there. A work order is pegged to a requisition or purchase order.
The requisition goes through the PO sourcing module and is sourced to an interunit stock request or a purchase order or both. The interunit stock request is created in the sending inventory business unit.
The purchase order is dispatched to the supplier.
The supplier ships the stock and it is received into the Purchasing business unit. If the notification framework has been defined for the Message Dashboard, then a notification is sent to the owner of the peg when stock is received into the Purchasing business unit.
The stock from the supplier or the sending inventory business unit is putaway in the destination inventory business unit. During putaway, the stock can be soft-reserved or allocated. In the IN_PEGGING table, if the pegged quantity (QTY_PEGGED field) is equal to the putaway pegged quantity (QTY_COMPLETE field) then the peg status in this table is updated to complete. If either the demand or supply order has no more open peg quantity, then the peg status on the order itself is also updated to complete.
If the notification framework has been defined for the Message Dashboard, then a notification is sent to the owner of the peg when the stock completes putaway in the Inventory business unit.
The work order part is fulfilled in PeopleSoft Inventory using the picking or issue features for work orders in the Fulfill Work Orders menu. The work order part is given to a technician or delivered to a location.
When using a non-inventory item ID or a description-only item on a work order line, you cannot peg to a materials stock request (interunit transfer, supply-side) or a production ID. You can peg to a requisition or purchase order. You can create the peg from the PeopleSoft Maintenance Management side or the PeopleSoft Purchasing side. The Pegging Workbench cannot be used to peg a non-inventory item ID or a description-only item. The Pegging Inquiry component can be used to view peg chains to non-inventory item ID or a description-only items.
This process flow diagram illustrates pegging, from PeopleSoft Maintenance Management, a work order that is using a non-inventory item ID or a description-only item. The sequence of events in the process flow is explained below the diagram:
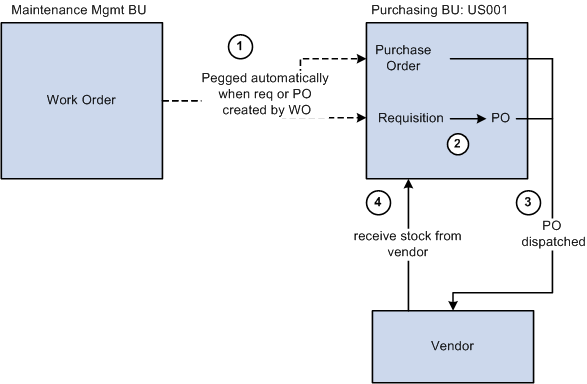
The sequence of events in the process flow is:
Using the Work Order - Schedules page, select the Purchase/On-Hand link, add a non-inventory item or description-only item, and then:
Click the Load Requisition button to place the work order line in a staging table where the Requisition Loader process will retrieve it and create a requisition in PeopleSoft Purchasing.
Click the Load Purchase Order button to place the work order line in a staging table where the Create Purchase Order process will retrieve it and create a purchase order in PeopleSoft Purchasing.
Use the sourcing module in PeopleSoft Purchasing to build a purchase order from the requisition. The requisition cannot be placed on a material stock request since there is no inventory item ID.
The purchase order is dispatched to the supplier.
If receiving is required, then the parts are received into the purchasing business unit. If receiving is not required, then the peg status is updated to complete when the purchase order is closed.
This process flow diagram illustrates pegging, from PeopleSoft Purchasing, a work order that using a non-inventory item ID or a description-only item. The sequence of events in the process flow is explained below the diagram:
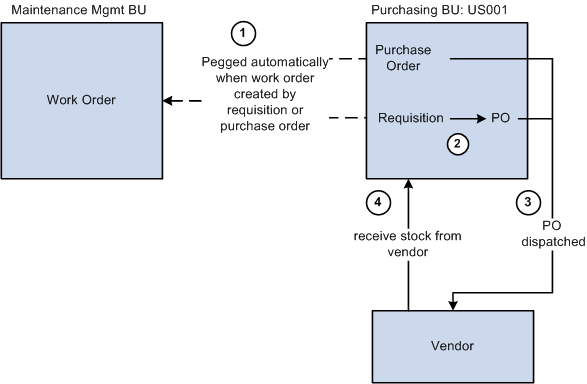
The sequence of events in the process flow when pegging from PeopleSoft Purchasing to a work order is:
Create a requisition or purchase order line:
In the Add/Update Requisitions component in PeopleSoft Purchasing, add a non-inventory item ID or a description-only item, select the Schedule button, select the Maintenance WO tab. Enter the Maintenance WO business unit, work order, task number, resource type, and resource line number. The work order ID and task must already exist in PeopleSoft Maintenance Management, however the resource line number can be added here if needed. If the item does not exist on the work order and you want to add it, then leave the resource line number at zero. When the requisition is saved, a peg is automatically created between the requisition line and the work order.
In the Add/Update Purchase Order component in PeopleSoft Purchasing, add a non-inventory item ID or a description-only item, select the Schedule button, select the Maintenance WO tab. Enter the Maintenance WO business unit, work order, task number, resource type, and resource line number. The work order ID and task must already exist in PeopleSoft Maintenance Management, however the resource line number can be added here if needed. If the item does not exist on the work order and you want to add it, then leave the resource line number at zero. When the purchase order is saved, a peg is automatically created between the purchase order line and the work order.
For a requisition, use the sourcing module in PeopleSoft Purchasing to source the requisition into a purchase order. The requisition cannot be placed on a material stock request since there is no inventory item ID.
The purchase order is dispatched to the supplier.
If receiving is required, then the parts are received into the purchasing business unit. If receiving is not required, then the peg status is updated to complete when the purchase order is closed.