Understanding Standard Parts Lists and Work Order Instructions
You can set up standard parts lists and standard work order instructions for work orders. You use a standard parts list when the maintenance task for which the work order applies is routine and repetitive, and when you have advance knowledge of the parts requirements.
For example, suppose that you overhaul the hydraulic assembly of a particular piece of equipment every 250 hours. Because the overhaul procedure requires the same repair kit, you would set up a standard parts list that includes all of the parts that are necessary to overhaul the hydraulic assembly.
Work order instructions specify the sequence of operations that is required to complete a work order, as well as the work centers that are responsible for each operation. You use standard work order instructions when the maintenance task for which the work order applies is routine and repetitive, and when you have advance knowledge of the labor requirements. To use standard work order instructions, you must set up work center information and information about the sequence of operations.
You can set up as many standard parts lists and standard work order instructions as you need. In addition, you can use a standard parts list or a version of standard work order instructions on as many work orders as you need. Typically, you assign standard parts lists and standard work order instructions to model work orders, but you can also use information from standard parts lists and standard work order instructions to create parts lists and routing instructions that you can attach to corrective work orders.
You use work centers to define each production facility on the shop floor where routing instruction operations occur. After you set up the work centers, you can enter costing and accounting information so that you can generate reports and journal entries.
This diagram illustrates how the system uses information from a standard parts list and standard work order instructions to generate a parts list and labor routing instructions for a work order that is assigned to a specific maintenance task:
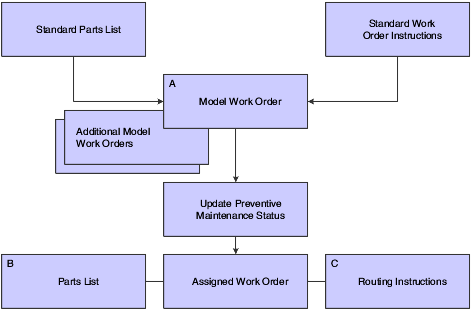