Understanding Configured Item Transfer Orders
A transfer order ships inventory between branch/plants within the company. When you enter a transfer order, the system creates supporting purchase orders and sales orders that are used to maintain accurate inventory.
You can transfer configured items between branches using a Transfer Order Entry version of Sales Order Entry (P4210) to create transfer orders for configured items.
When you enter an order for a configured item directly through Transfer Order Entry, everything on the order is transferred. Thus, the complete parent configured item is transferred.
In the transfer order scenario, Branch A has requirements for a configured item that is in Branch B. This configured item consists of the parent and all components. Transfer order entry is used to configure the item on a purchase order. A corresponding sales order for the configured item is sent to Branch B. The configured item is shipped from Branch B to Branch A, where it is received and stocked in inventory.
This diagram illustrates the transfer order process:
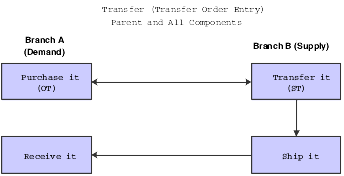
In some instances, Branch B might have to build the configured item before it can be shipped to Branch A.
This diagram illustrates the step of generating work orders to manufacture the configured item before it is shipped to Branch A:
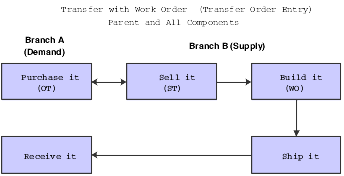
The system also supports transfer orders for components of the parent configured item. The component of the parent configured item could be a standard manufactured component, subassembly, or configured subassembly. Although the setup requirements vary, the functionality is the same.