Understanding Operation Entry
Operations are individual activities that together define the blend process. Operations include the activities of receiving bulk material into the system, crushing the bulk material and subjecting it to a variety of treatments, such as moving it into vessels with specific characteristics that are intended to affect the product, and stirring the liquid. You can also mix in additives that change the characteristics of the product, for example by raising the sugar content. As part of the process, you can perform quality tests to monitor the state of the product. At the end of the process, you package the product for sale purposes, for example you bottle the wine that you have produced.
Configured operations can be classified into seven major categories, as the following table illustrates:
Operation Category |
Examples |
---|---|
Receiving operations |
Receive wine, receive transferred wine, receive full tank, receive full barrel, receive to tank, decant. |
Move operations |
Tank to tank, barrel fill, barrel to barrel, top barrel from tank, top barrel from barrel, barrel empty, crush, drain press, filter/centrifuge. |
Add operations |
Tank addition, barrel addition. |
In-place operations |
Tank in place, barrel in place, portable tank relocation, barrel relocation, barrel self topping, empty tank in place, empty virtual barrel tanks (VBT) in place. |
Administrative operations |
Adjust lot attributes, adjust inventory, VBT maintenance, error correction, declared loss, override composition material type. |
QA operations |
Quality assurance. See Managing Quality. |
Removal operations |
Ship and transfer bulk material, ship full tank, ship full barrel, bottling, transfer empty tank, transfer empty VBT. |
When you elaborate operations, you must add tanks or VBTs containing one or more barrels to the operation. For additive, in-place, administrative, and QA operations, you need only source vessels (From vessels) because you do not move the bulk material. Receiving, move, and removal operations require From and To vessels as the source and destination vessels of the operation. Vessels include not only tanks and VBTs, but also weigh tags, bills of lading, and bottling vessels.
The bulk material in a vessel is represented by the blend lot. Lots are the mechanism that the system uses to track changes to the bulk material. Operations change the attributes of the blend lot and effectively create new lots. For example, turning grapes into juice changes the material type of the bulk material. Moving bulk material into a barrel may result in style changes as a result of the impact of the barrel style. Mixing additives into the bulk material changes the QA result the next time you perform a test. Thus each operation has a Before and an After lot in relation to each vessel.
If an operation uses more than one vessel, for example in move operation, both the From and the To vessels have their own Before and After lots. If you move a quantity from one vessel to another, the After lot of the From vessel shows a decreased quantity, whereas the After lot of the To vessel shows the increase. The following diagram illustrates the relationship of vessels and lots in move operations:
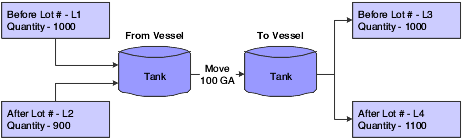
The system enables you to move bulk material from one vessel to many, but also from many vessels to one. In addition, you can perform many-to-many movements.