Understanding Daily Planning and Sequencing
To help you meet firm demand (which is represented by unfulfilled sales orders within a given time frame), the Daily Planning and Sequencing program (PF34S002) enables you to create daily production plans and then sequence the planned quantity on the line.
You create a production plan based on sales orders for which the recommended start dates are within the planning date range that you define. By setting processing options, you can also include past-due sales orders that have not been planned, as well as past due plans. When you create a plan from a sales order, the system populates the sales order and customer information fields on the plan record—for example, the sales order number and quantity, and the customer name and number—from the sales order record. You cannot edit these fields on the Define Daily Plan form. However, you can access the DFM Demand Entry program (PF30L801) and the DFM Customer Master program (PF30L301) by using the links in the Sales Order Number field and the Customer Number field. As you create the plan, the system compares the daily rate to the demand at capacity to determine whether the plan is valid.
This diagram provides an overview of the daily plan process:
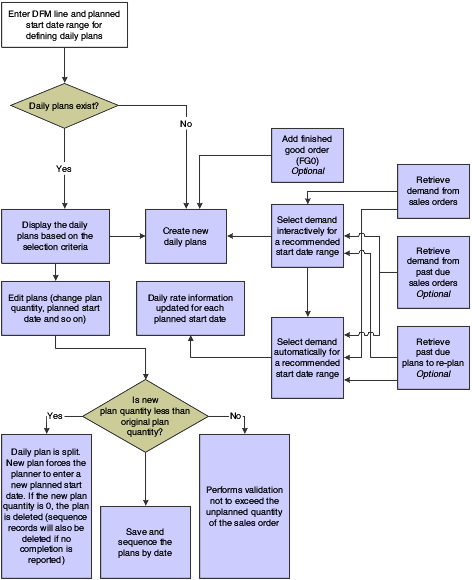
After creating a valid plan, you can sequence the planned quantity for the production line using the Daily Sequencing program (PF34S001). The system provides several methods for dividing the planned quantity for sequencing purposes—for example, dividing the planned quantity by maximum or minimum order quantity that you specified for the item. You can perform sequencing multiple times and make manual changes to create an optimal production sequence. If you change the planned quantity, you have to generate new sequence records. Generating a sequence populates the Sequenced Quantity field in the grid on the Define Daily Plan form and serves as an indicator that sequencing has already been performed at least once. You can also review the result of sequencing online in the View Daily Sequence program (PF34S005).
This diagram shows the data flow for sequencing:
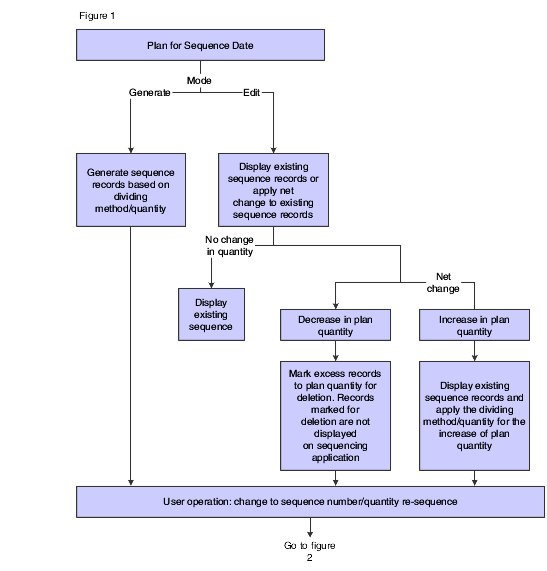
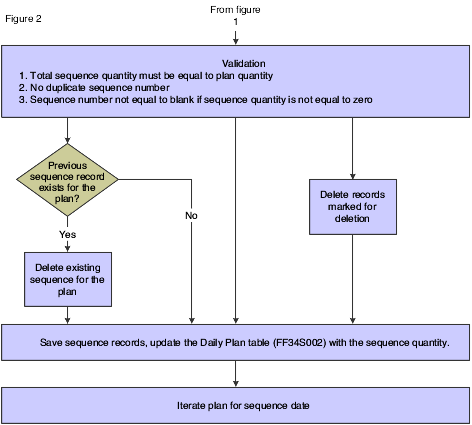
When you complete a quantity against a plan using the Item Completions program (PF31011), the completions process populates the Completed Quantity field and the Scrapped Quantity field (if scrap exists). You can close a plan manually if you are not using JD Edwards EnterpriseOne Shop Floor Management to perform item completions.
You delete a plan by selecting it on the grid and clicking the Remove button. You can delete multiple plans at a time. Deleting a plan also deletes the corresponding sequence records. You can delete a plan only if no quantity has been reported against the plan.
Changing the planned quantity splits the plan. For example, if the planned quantity is 100 and you change it to 35, the system creates a new plan for a planned quantity of 65. If the new plan that was created from the original plan has the same planned start date, the system issues an error message, forcing the planner to enter a different planned start date. This does not apply to a finished good order.
If you modify the planned start date of a plan and if sequence records exist for the original planned start date, these sequence records are deleted. You have to generate a sequence for the new date. However, if the planned quantity and the sequenced quantity do not match for a planned start date, the system issues a warning.