Understanding Kanban Processing
Kanbans can be used as part of a one-phase or two-phase process. The one-phase process assumes that the completion or receipt of quantity to the supplying location and transfer to the consuming location are performed in one step. With a one-phase kanban, the status of the kanban progresses as follows:
Check In to Check Out.
Check Out to Check In.
This diagram illustrates the one-phase kanban process:
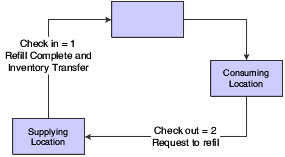
The two-phase approach assumes that the completion and transfer to the consuming location are reported separately. You complete or receive the quantity to the supplying location by using the Complete status, which is status 3. After the quantity has been physically received at the supplying location, you initiate an inventory transfer from the supplying location to the consuming location by checking in the kanban. The kanban status changes to Checked In (1). Using this method is helpful when you are working with items that require inspections or tests before they are moved to the consuming location. With a multiphase kanban, the status of the kanban progresses as follows:
Check In to Check Out.
Check Out to Complete.
Complete to Check In.
When you check in a kanban quantity from the supplier, the system can initiate a receipt transaction if you select the Receipts option in the kanban master.
This diagram illustrates the two-phase kanban process:
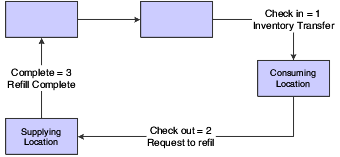
You can process kanbans for:
Inventoried items
Manufactured items (subassemblies)
Externally supplied items (supplier)
Interbranch items
When you check out an inventory kanban (source type 2), the system changes the kanban status. The supplying location replenishes the kanban quantity. You then check in the kanban, which results in an inventory transfer. Inventory kanbans only perform software transactions during the check-in process. All other statuses for this kanban type are informational only.
When you check out a work center kanban (source type 1), the program:
For discrete manufactured items, the software creates a new work order.
For rate scheduled items, which have an order policy code of 5 in the item branch record, the software looks for an existing open rate.
If no rate exists for the item and line combination that is specified in the kanban master record, then the software creates a new rate for the kanban quantity.
You should be aware that the software assumes that rate quantities that are generated from kanbans are due the same day that they are initiated. Therefore, no standard spreading of the subsequent rate quantity occurs in the Line Scheduling Workbench. You can set a processing option for the Enter/Change Rate Schedule program (P3109) so that the system automatically attaches the parts list and routing instructions when a new rate is created or changed.
When you check in a work center kanban, you complete the work order or rate, issue materials, enter hours and quantities, and transfer the parent item to the consuming location.
When you check out a kanban that a work center or production line supplies, and the item is a phantom, no transactions other than inventory transfers occur. When you have no work orders or rates to process; the producing line replenishes the item, and the system completes the kanban and checks it in. This results in a transaction for inventory transfer, from the supplying location to the consuming location.
An externally supplied kanban creates an open purchase order for the kanban item. This purchase order can be an existing one, or, optionally, one that is created during the check-out process. In addition, when you check out the kanban, the system might also initiate an electronic data interchange (EDI) transaction. When you check in kanbans from an external supplier, the system optionally creates a receipt for the purchase order. You can also use kanbans to release quantities from open blanket purchase orders.
A kanban that is supplied from a branch/plant requires you to create a transfer sales order when you check out the kanban. When you check in the kanban that is supplied by another branch/plant, the system creates a transfer purchase order and receipt.
For JD Edwards EnterpriseOne Demand Flow® Manufacturing, a raw in-process (RIP) (source type 0) kanban supports material movement within the RIP without requiring valid locations. The DFM dual card kanban (source type 6) triggers kanban replenishment from a machine cell. For a dual card kanban, the number of cards must be checked out from the consuming location for the replenishment to be triggered. A one-phase DFM kanban check-in triggers lean completions and an inventory transfer. A two-phase DFM kanban complete status triggers lean completions and check-in triggers an inventory transfer.