Understanding Engineering Change Management
To maintain and increase market share, manufacturers often must respond quickly with engineering changes to their products. Engineering changes might be necessary to respond to market demand, governmental requirements, safety issues, service requirements, or for other functional or competitive reasons. Changes can involve adding a new part, changing an existing part, replacing an old part with a new part, or removing an existing item. Use Engineering Change Management to create, plan, review, approve, and implement engineering change orders and engineering change requests for any of these types of changes.
Product or process changes can affect many areas within the company, including:
Customer service
Tooling
Standards
Suppliers
Master production schedule
Product cost
Service parts
Inventory
Plant layout
Engineering change orders (ECOs) are numbered documents that you use to track product changes within Engineering Change Management. After you have tested and approved an ECO, you can implement it and modify the standard product or process.
Engineering change requests (ECRs) are numbered documents that you use to track requested product changes within Engineering Change Management. After you have tested and approved an ECR, you can convert it to an ECO and implement it using the ECO processes.
The procedures for ECOs and ECRs are the same, except that you must use order type EN when you set up, review, or approve ECOs; and you must use order type EG when you set up, review, or approve ECRs.
This process flow illustrates the engineering change order process:
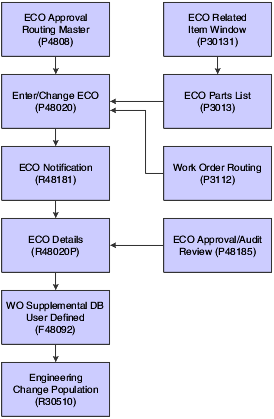