Work Centers
A work center consists of people and machines.
A work center is a specific production facility on the shop floor where the routing operations occur. For each work center, you define:
Number, description, and associated business unit.
Queue and move times.
Operator, machine, and hours-per-day capacity.
Rates for setup, labor, machine, and overhead.
A work center enables you to:
Set up a dispatch group for departments that perform similar operations.
Specify if an operation is a reporting point for material, or labor, or both.
Define crew size per work center.
Specify the work center efficiency for JD Edwards EnterpriseOne Product Costing.
Define work center labor, machine, and setup rates.
You should arrange the work centers so that work in process moves efficiently from one area to the next.
This process flow illustrates equipment grouped by operation; this structured flow layout provides a direct path and ensures efficient workflow:
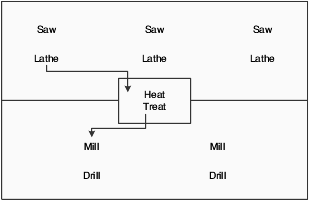
After you have defined the item's bill of material and where each operation occurs on the factory floor (work center), you must define the sequence of operations that is necessary to manufacture the item (routing instructions).
Routing instructions are critical for shop floor control, capacity requirements planning, product costing, and measuring production efficiency.
For each item, you define routing instructions that include:
Production process.
Equipment.
Operator skill level.
Inspection criteria.
Operations.
Sequence.
Applicable work centers.
Standard values for setup, machine, and labor times.
You can define an alternate routing instruction operation to be performed, for example, using drill B if drill A is not operational. An alternate routing instruction operation is information for shop floor personnel. The system ignores it during product costing and backscheduling.
For activities that occur outside the plant, you define outside operations. Outside operations are characterized by their own line types and stocking types. They require a supplier and a purchase order.
For multiplant environments, set up identical or different routing instructions for an item by plant. Use the effective from and thru dates to enter and date routing instruction changes as they occur.
You have the option of setting up a master routing to create one routing instruction for parts that use the same manufacturing steps. You must define an Item Cross Reference for the Item to be used as a master routing. Create a record in the Item Cross Reference application (P4104) with a cross reference type MR. By creating a master routing, you can eliminate duplicate routing instructions. For example, during the manufacture of furniture, the frame and fabric might change, but the routing instructions are the same. To set up a master routing, you must activate the Master Routing option in the Manufacturing Constants program (P3009) for the branch/plant where the item will be manufactured.
Use batch routing instructions for products that are commonly made in batch quantities. Batch routing instructions are useful in industries, such as pharmaceuticals, foods, or petroleum, where products are manufactured in fixed quantities or batches. You can create different batch routing instructions for the same item by branch, type, batch quantity produced, or a combination of these items.