Understanding Parts List Requirements
This diagram illustrates a parts list that includes items B, E, F, and G:
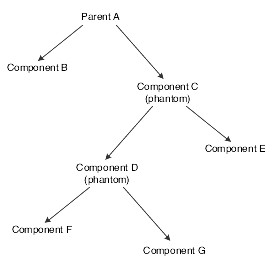
For variable quantity items, the system calculates component quantities according to the order quantity on the work order.
When the inventory available is insufficient to cover the parts list requirements for the work order, the system highlights the Order Quantity field on the parts list for the item that is in short supply. If you set the Substitutions processing option on the Parts List tab for R31410, the system will automatically include the substitute item if there is insufficient inventory for the original item.
The lead time offset indicates the number of days that a part is needed before or after the start date of a manufacturing work order. The system adds the lead time offset days for the part to the start date of the work order to determine the actual date on which the part is required. To indicate how many days after the work order start date that the part is required, enter a positive number on the Enter Bill of Material Information form (W3002A). To indicate that a part is needed prior to the work order start date, enter the days as a negative number. Examples of items that require negative lead time offset days are items that need processing or inspection before they can be used in an assembly. If the requested date for a component is later than the order completion date, the system enters the order completion date for the item.
When you define a shrink factor for the item on the Additional System Info form of the Item Branch program (P41026), the system compensates for the loss by increasing the component requirements for parent items by the percentage or quantity. The system displays the increased order quantity in the Order + Shrink field on the work order header. You use scrap or yield to inflate the component quantity. The system includes shrink adjustments, if applicable, when it calculates parts list quantities and routing instructions for the order.