Understanding Types of Picking Documents
Warehouse personnel can print documents to assist them with retrieving inventory from the warehouse to fill a customer's order, shipment, or load. Additionally, you can print lists to pick items for multiple sales orders. A control pick slip, or a pick list, enables warehouse personnel to fill multiple sales orders efficiently.
This table lists and describes the documents that you can print for warehouse personnel to use in retrieving inventory:
Document |
Description |
---|---|
Pick Slips (R42520) |
A pick slip is a document that contains information about the items to be shipped, such as quantity and location, for a single sales order. Use pick slips:
If you hard-commit inventory when you print pick slips, a pick slip can include several locations from which you can pick items. It lists the specific lot and location of an item. If not enough availability exists to pick from a single lot location, the system splits the line and creates a separate line for each lot and location. The system assigns the pick slip number by order number or by requested date and prints the total number of items for that order. |
Control Pick List (R42522) |
A control pick list has information about the items to be shipped for multiple sales orders. The control pick list groups the items by item number and sequences them by quantity and location. Control pick lists enable warehouse personnel to fill multiple sales orders efficiently, reducing the amount of time that is spent locating necessary quantities. The system assigns the pick slip number by location and prints the total number of items for that location. If you use taxed prices and access the Control Pick List report, the system recalculates the extended price, taxed extended price and extended tax amount if a sales order line is split. See Tax Price |
Packaged Pick Slip (R42521) |
A packaged pick slip enables warehouse personnel to pick inventory to fill a certain shipment or load. The system assigns the pick slip number by shipment or load number and prints the total number of items for the shipment. If you use taxed prices and access the Packaged Pick Slip report, the system recalculates the extended price, taxed extended price, and extended tax amount if a sales order line is split. See Tax Price |
If you print a control pick slip before you print a pick slip, you can later print a pick slip for each sales order on the control pick list. The warehouse personnel can use these pick slips to determine the items and quantities to pack for each of the sales orders that they are shipping. The pick slips help warehouse personnel work efficiently because they can pack multiple orders from one area. The system assigns a number to each pick slip that you can later use to confirm a shipment.
When you have kits on sales orders, the system prints kit parent and component items sequentially on a pick slip. The value in the Kit ID field in the F4211 table enables the system to determine kits and their corresponding components.
If you use the JD Edwards EnterpriseOne Demand Scheduling system from Oracle, the report displays the Scheduled Pick Time (PDTT) information on the report in a column labeled Date/Time. This report also displays charge references for detached adjustments and flat rates.
You can assign a priority code to customers in the customer billing information to have the system fill customer orders and generate pick lists according to the priority of the customer. This helps to ensure that you have sufficient inventory for certain customers.
This diagram illustrates how the system uses control pick slips and pick slips to fill orders:
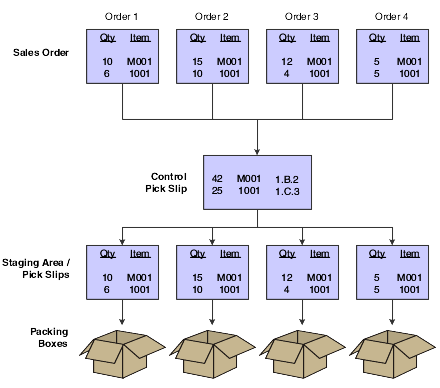
You can reprint pick slips if the printing process is interrupted or if you need additional copies. The system reprints the pick slip without advancing the status codes for that order.
You must set the processing options to identify the type of pick slip to print.