How You Purchase Project-Specific Inventory
Project-Driven Supply Chain is an end-to-end, integrated solution across Oracle Fusion Cloud Supply Chain and Project Management applications. This solution supports the business process to purchase project-specific material to satisfy project demand.
Project-specific purchase orders ensure that the cost of the purchase is charged to the project and the material is received into project inventory. With this feature, you can automate the purchase of project-specific materials for multiple projects and carry forward project attributes through the entire procure-to-pay cycle.
Here's the high-level process flow to purchase project-specific inventory:
-
The process starts with the creation and approval of a requisition in Self-Service Procurement or with the release of a buy planned order from Supply Planning.
-
After the requisition is approved, a project commitment is created.
-
Next, the purchase order is created from the requisition and the project commitment is moved to the purchase order.
-
This is followed by the receipt and put away of the end product into project-specific inventory that can be verified by checking on hand inventory for that project.
-
After receipt and put away, the project commitment is relieved.
-
Cost accounting distributions are created in costing and the project details are reviewed for the accounting distributions.
-
The costs are final accounted and imported into Project Portfolio Management where they're further managed.
-
And finally, the project invoices are generated to bill the customer based on the percentage of completion or milestones achieved on the project.
This illustration explains the high-level process flow to purchase project-specific inventory.
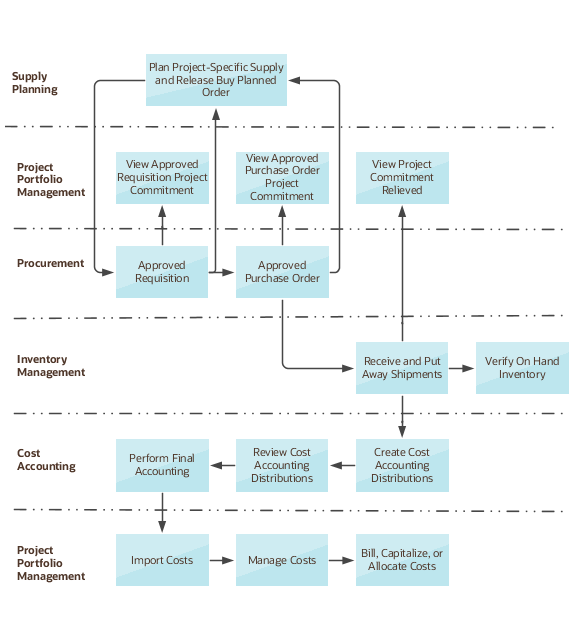