Example of Cost Rollup
This example illustrates how the unit cost of a make item is calculated by the Roll up Costs process after the standard costs, resource rates, and overhead rates are defined in the cost scenario.
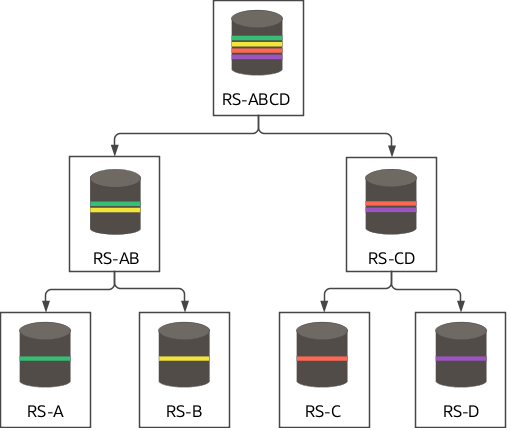
Scenario
Your organization is manufacturing an item RS-ABCD that has a structure as shown in the image here. To make this item, you first need to make RS-AB and RS-CD. RS-AB is made using the materials RS-A and RS-B. RS-CD is made using the materials RS-C and RS-D. Apart from these materials, you also require various other resources to manufacture this item.
For this item, you create these work definitions.
Item |
Work Definition Name |
Version |
Start Date |
---|---|---|---|
RS-AB |
Main |
1 |
9/1/2020 |
RS-CD |
Main |
1 |
9/1/2020 |
RS-ABCD |
Main |
1 |
9/1/2020 |
Let's assume that the batch size of the work definition output is 1 each (primary UOM of these items).
Standard Costs, Resource Rates, and Overhead Rates
Now, to calculate the unit cost of RS-ABCD, you start by creating a cost scenario. You must make sure that the effective start date of the cost scenario is same as or later than the work definition start date. So, set the effective start date as 9/1/2020.
Next, you must define the standard costs for the materials used, the rates for the various resources used when manufacturing the item, and the overheads incurred. Define the standard costs, resource rates, and overhead rates for this cost scenario as listed in these tables.
Standard Costs
Item |
Cost Element |
Cost Element Type |
Expense Pool |
Unit Cost |
---|---|---|---|---|
RS-A |
||||
CML Material |
Material |
1.00 |
||
CML Overhead |
Overhead |
CML Exp Pool |
0.50 |
|
1.50 |
||||
RS-B |
OSPMatElement |
Material |
2.00 |
|
RS-C |
0554-MatElement |
Material |
3.00 |
|
RS-D |
P2P-Material-CE |
Material |
4.00 |
Resource Rates
Resource |
Cost Element |
Cost Element Type |
Expense Pool |
Unit Cost |
---|---|---|---|---|
Machine Operator |
Direct Labor |
Resource |
MFG_Resources_EP |
1.00 |
Fabrication Engineer |
||||
0554-ResElement |
Resource |
P2P_Res_Pool |
1.50 |
|
ZCST-Electrical |
Overhead |
P2P_Exp_Pool |
0.50 |
|
2.00 |
||||
Electrician |
Direct Labor |
Resource |
3.00 |
|
Inspector |
RS-Resource |
Resource |
4.00 |
|
Welding Torch |
Direct Equipment |
Resource |
5.00 |
Overhead Rates
Overhead Rate Type |
Item Category |
Item |
Cost Element |
Expense Pool |
Absorption Type |
Rate |
---|---|---|---|---|---|---|
Plant Overhead |
RS-ABCD |
Manufacturing Overheads |
MFG_Resources_EP |
Percentage of Material Cost |
1% |
Analysis
After you define the cost scenario and the corresponding standard costs, resource rates, overhead rates, run the Roll up Costs process for the cost scenario.
Rolled Up Costs
Let's start with identifying the costs for the items RS-AB and RS-CD. To fabricate RS-AB, you need couple of machine operators and fabrication engineers. The item cost calculation for RS-AB is as shown here.
Number |
Operation Sequence |
Item |
Item Description |
Unit Cost |
Quantity |
Extended Cost |
---|---|---|---|---|---|---|
Main (#V1) |
RS-AB |
RS-AB |
9.50 |
1 |
9.50 |
|
10 |
Fabrication |
9.50 |
||||
RS-A |
RS-A |
1.50 |
1 |
1.50 |
||
RS-B |
RS-B |
2.00 |
1 |
2.00 |
||
Machine Operator |
1.00 |
2 |
2.00 |
|||
Fabrication Engineer |
2.00 |
2 |
4.00 |
To make RS-CD, you need an electrician and the work must be inspected by an inspector. This is the item cost calculation for RS-CD.
Number |
Operation Sequence |
Item |
Item Description |
Unit Cost |
Quantity |
Extended Cost |
---|---|---|---|---|---|---|
Main (#V1) |
RS-CD |
RS-CD |
14.00 |
1 |
14.00 |
|
10 |
Electrical |
10.00 |
||||
RS-C |
RS-C |
3.00 |
1 |
3.00 |
||
RS-D |
RS-D |
4.00 |
1 |
4.00 |
||
Electrician |
3.00 |
1 |
3.00 |
|||
20 |
Inspection |
4.00 |
||||
Inspector |
4.00 |
1 |
4.00 |
RS-ABCD is made by using RS-AC and RS-CD. You need welding torches and the work must be inspected by an inspector. This is the item cost calculation for RS-ABCD.
Number |
Operation Sequence |
Item |
Item Description |
Unit Cost |
Quantity |
Extended Cost |
---|---|---|---|---|---|---|
Main (#V1) |
RS-ABCD |
RS-ABCD |
37.60 |
1 |
37.60 |
|
10 |
Frame Assembly |
33.50 |
||||
RS-AB |
RS-AB |
9.50 |
1 |
9.50 |
||
RS-CD |
RS-CD |
14.00 |
1 |
14.00 |
||
Electrician |
5.00 |
2 |
10.00 |
|||
20 |
Inspection |
4.00 |
||||
Inspector |
4.00 |
1 |
4.00 |
|||
Plant Overhead |
0.10 |
Cost details of the materials, resources, and overheads for the item RS-ABCD are summarized here.
Cost Element |
Cost Element Type |
Expense Pool |
Cost Level |
Unit Cost |
---|---|---|---|---|
ZCST-Electrical |
Overhead |
Lower Level |
1.00 |
|
ZCST-Electrical |
Overhead |
This Level |
0.00 |
|
CML Material |
Material |
Lower Level |
1.00 |
|
CML Overhead |
Overhead |
Lower Level |
0.50 |
|
CML Overhead |
Overhead |
This Level |
0.00 |
|
OSPMatElement |
Material |
Lower Level |
2.00 |
|
OSPMatElement |
Material |
This Level |
0.00 |
|
RS-Resource |
Resource |
Lower Level |
4.00 |
|
RS-Resource |
Resource |
This Level |
4.00 |
|
P2P-Material-CE |
Material |
Lower Level |
4.00 |
|
P2P-Material-CE |
Material |
This Level |
0.00 |
|
0554-MatElement |
Material |
Lower Level |
3.00 |
|
0554-MatElement |
Material |
This Level |
0.00 |
|
0554-ResElement |
Resource |
Lower Level |
3.00 |
|
0554-ResElement |
Resource |
This Level |
0.00 |
|
Direct Labor |
Resource |
Lower Level |
5.00 |
|
Direct Labor |
Resource |
This Level |
0.00 |
|
Direct Equipment |
Resource |
This Level |
10.00 |
|
Manufacturing Overheads |
Overhead |
MFG_Resources_EP |
This Level |
0.10 |
37.60 |