How Backward Scheduling and Order Dates Are Calculated
Backward scheduling is the process by which lead time is applied to supply orders. When the planning mode is unconstrained, backward scheduling is performed by the planning process.
When you run a supply plan, the planning process reports constraint violations as capacity overloads and lead time exceptions so that you're alerted to supply problems. The supply for your sales order becomes due on the end demand date.
Settings That Affect Backward Scheduling and Order Dates
When supply is just in time for a demand, the supply completion date is the demand date. The supply is then scheduled backward to arrive at the start dates for each operation that must be completed and due dates for supply of lower-level components that make up the final supply.
During backward scheduling of dates, if the plan start date is crossed, then all earlier dates are bucketed to the plan start date. This process is referred to as compression.
Backward scheduling affects order due dates in the following ways for different types of items:
-
For make items, compression begins at preprocessing lead time. The first operation and each successive operation are then compressed to zero duration until there is sufficient lead time for the remaining operations to complete using the resource duration.
-
For transfer and buy items, the preprocessing lead time is compressed first. The processing lead time is then compressed and if insufficient lead time remains, postprocessing lead time is compressed.
Note: The processing time for a buy item is independent of item quantity.
You can set organization and customer receiving and shipping schedules and carrier transit schedules in the Manage Transportation Schedules section in Logistics. The only valid dates that planning calculations use for backward scheduling are the working days on the manufacturing and shipping calendars. Calendar defaulting rules are used by planning to determine order dates calculations. The defaulting rules are:
-
Valid Supplier Capacity Calendar: Either the Supplier Site Capacity Calendar is used or a fully open calendar of 7 days, 24 hours. If the Supplier Site Capacity Calendar in the Approved Supplier List is blank, then the Supplier Site Calendar from the Supply Network Model is used.
-
Valid Supplier Shipping Calendar: The Carrier, or Supplier, or Supplier Site Calendar, the Supplier, or Supplier Site Shipping Calendar, the Carrier, or Supplier Calendar, the Supplier Shipping Calendar, or a fully open calendar of 7 days, 24 hours is used.
-
Valid Organization Receiving Calendar: Either the Carrier or Organization Calendar is used, or the Organization Receiving Calendar, or the Organization Manufacturing Calendar.
How Backward Scheduling Is Calculated
Backward scheduling is calculated based on the following:
-
Planned Make Order: If your order is for a make item, the component due date is the start date for the operation that requires it and supply is scheduled backward. The work definition provides the information about the component and resource requirements for such an order. The new order due date becomes the date of the end demand.
Note: A make planned order exists only as a planned order in supply chain planning, and isn't part of manufacturing yet. -
Work Order: If your order is for an item that already exists as a work order, the component and resource requirements are collected from the work order. The planning process can shift the work order to a new set of dates without making alterations to the relationship of dates in the work order. The component due dates for that end item are collected from manufacturing.
For example, take the following scenario:
-
A is an end item with two components B and C that have different start dates.
-
C is a make item with two components D and E that also have different start dates.
Components D and E are in the lower level of the work definition for item C and they're needed for the assembly of the make planned order C. Similarly, components B and C are in the lower level of the work definition for item A and they're needed for the assembly of the work order A.
The following figure illustrates the relationship between components A, B, C, D, and E that are used to make an end item.
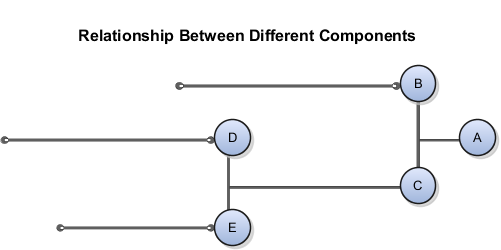
The planned make order rescheduled dates are determined by total quantity of demands and order modifiers. Total make order lead time (days) = fixed lead time + quantity multiplied by variable lead time.
The work order rescheduled dates are determined by component requirement start dates and end dates. If the end date is moved by 3 days, the start date is also moved by 3 days.