Vendor-Managed Inventory Components
Vendor-managed inventory (VMI) provides visibility into the entire replenishment process. VMI enables the supplier or the enterprise user to own inventory planning and replenishment creation activities.
Based on the process and actions performed, VMI tasks are performed in the following product work areas:
-
Oracle Fusion Cloud Supply Chain Collaboration
-
Oracle Fusion Cloud Procurement
-
Oracle Fusion Cloud Inventory Management
-
Oracle Fusion Cloud Financials
VMI When Supplier Owns Inventory Planning and Replenishment
This figure provides an overview of VMI when a supplier owns inventory planning and replenishment:
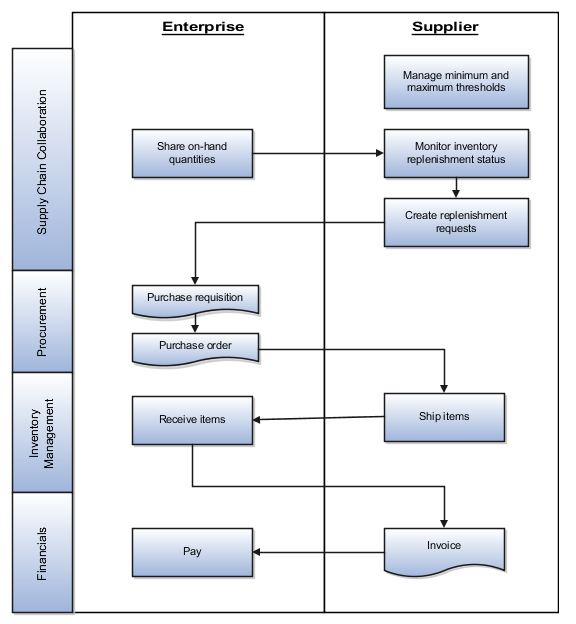
Work Areas |
VMI Process |
Actions |
---|---|---|
Supplier Portal |
Supplier updates the item's minimum and maximum quantities |
Suppliers provide minimum and maximum thresholds |
Inventory Management |
Enterprise maintains on-hand quantities in Inventory Management |
Share on-hand quantities with suppliers and VMI analysts |
Supplier Portal |
Calculate replenishment status using on-hand quantities and minimum and maximum thresholds |
Suppliers create replenishment requests |
Supply Chain Collaboration |
Replenishment request is transformed into an externally managed purchase requisition using the Purchase Request web service |
NA |
Procurement |
Based on a blanket purchase agreement, a purchase order is generated from the requisition, either automatically or manually |
Create and approve the purchase order If the requisition is not automatically converted into a purchase order. You can search for requisitions requiring manual processing, using the Process Requisitions and View Requisition Lines tasks. Enterprise users can find the number of the generated purchase requisition using the Manage Replenishment Requests page in the Supply Chain Collaboration work area. |
Supplier Portal |
Purchase order awaits shipment |
Supplier creates an advanced shipment notice (ASN) Supplier ships the product |
Inventory Management |
Enterprise receives the shipment and delivers the items |
Create a receipt notice |
Supplier Portal |
Supplier creates an invoice or enterprise can generate the invoice on behalf of the supplier |
Supplier creates an invoice |
Financials |
Enterprise pays supplier |
Enterprise creates a payment notice |
Supplier Inventory Planning Owner Flow
The VMI process flow when a supplier owns inventory planning and replenishment includes the following steps:
-
Depending on who the min-max quantity source is for an item, the enterprise user or the supplier sets the minimum and maximum quantities for the item. If enterprise and VMI relationship scope is organization, min-max quantities are set on the item record. If enterprise and VMI relationship scope is subinventory, min-max quantities are set at the item subinventory. If supplier, min-max quantities are set on the Manage Inventory page in the Supplier Portal work area or using the Vendor-Managed Inventory Items REST service.
-
The supplier monitors the replenishment status of items and decides which items need replenishment. If the on-hand quantity is less than the minimum quantity, the supplier creates a replenishment request.
-
The supplier submits replenishment request, which is then transformed into an externally managed purchase requisition by Supply Chain Collaboration using the Purchase Request web service.
-
Based on a blanket purchase agreement, a purchase order is generated from the requisition either automatically or manually by the buyer. The purchase order is then approved and ready for the supplier to fulfill. For more information on purchase agreements and purchase orders, see the Oracle Procurement Cloud Using Procurement guide.
-
The supplier inventory manager is now able to fulfill the purchase order. They can view the open purchase order quantity in the Purchase Order Quantity column on the Manage Inventory page. They can also navigate to the open purchase orders using the Manage Orders page.
-
The supplier inventory manager is now able to ship the product. The supplier optionally creates an advanced shipment notice (ASN) using Create ASN on the Manage Inventory page. Once an ASN is created the quantity shipped now appears as In-Transit Quantity on the Manage Inventory page.
-
The inventory management user receives and delivers the item to its deliver-to location. The supplier inventory manager can view the items awaiting to be delivered using the Received Quantity column on the Manage Inventory page. Once an item has been delivered it will be included in the on-hand quantity.
-
The supplier inventory manager may create an invoice, or an invoice will be automatically generated by the enterprise on behalf of the supplier. The supplier inventory manager can view the invoices associated to a specific replenishment item by using Review Item Transactions on the Manage Inventory page.
-
The enterprise processes the invoice and generates a payment. The supplier inventory manager can view the payments associated with a specific replenishment item using Review Item Transactions on the Manage Inventory page.
VMI When Enterprise Owns Inventory Planning and Replenishment
This figure provides an overview of VMI when the enterprise owns inventory planning and replenishment:
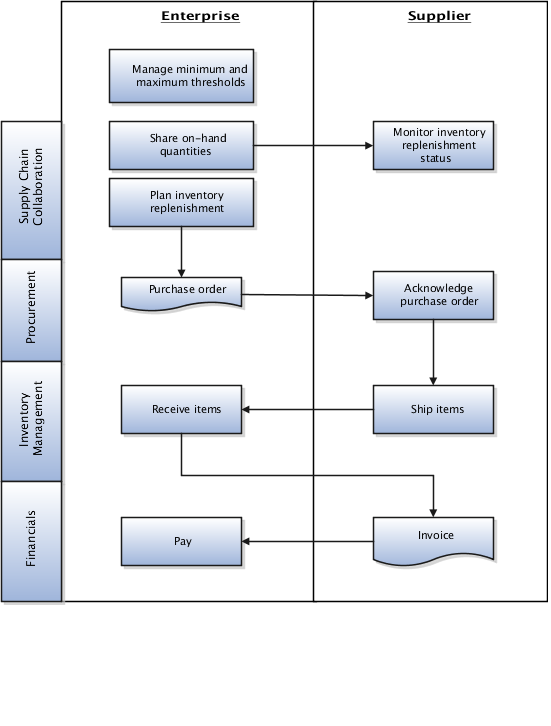
The following table describes the product work areas, VMI processes, and the corresponding actions.
Work Areas |
VMI Process |
Actions |
---|---|---|
Item Record Item Subinventory Record |
Enterprise maintains minimum and maximum thresholds on the item or item subinventory record. Min-max quantities can be manually updated or calculated using the Calculate Min-Max Planning Policy Parameters scheduled process. To learn more see the Using Inventory Management guide. |
Share minimum and maximum thresholds with suppliers and VMI analysts |
Inventory Management |
Enterprise maintains on-hand quantities in Inventory Management |
Share on-hand quantities with suppliers and VMI analysts |
Supplier Portal |
Calculate replenishment status using on-hand quantities and minimum and maximum thresholds. |
Suppliers monitor replenishment status |
Inventory Management |
Enterprise performs inventory replenishment. |
Enterprise runs min-max planning report or manually creates purchase orders. For more information, see the Using Inventory Management guide |
Supplier Portal |
Purchase order awaits shipment |
Supplier creates an advanced shipment notice (ASN) Supplier ships a product |
Inventory Management |
Enterprise receives shipment and delivers items. |
Create a receipt notice |
Supplier Portal |
Supplier creates invoice or enterprise can generate the invoice on behalf of the supplier. |
Supplier creates an invoice |
Financials |
Enterprise pays supplier |
Enterprise creates a payment notice |
Enterprise Inventory Planning Owner Flow
The VMI process flow when the enterprise owns inventory planning and replenishment includes the following steps:
-
The enterprise user sets the minimum and maximum quantities. If the VMI relationship scope is organization, min-max quantities are set on the item record. If the VMI relationship scope is subinventory, min-max quantities are set on the item subinventory.
-
The enterprise user can also automatically calculate min-max quantities using the Calculate Min-Max Planning Policy Parameters scheduled process. The enterprise user monitors the replenishment status of the item and decides which item needs replenishment. To replenish items, the enterprise user creates purchase orders manually or generates purchase orders automatically by running the min-max planning report. For more information about min-max planning report, see the Using Inventory Management guide
-
Optionally, the generated purchase order can require supplier acknowledgment. The supplier is allowed to make changes to the suggested replenishment at that time. The supplier can view the requiring acknowledgment quantity in the Pending Acknowledgment column on the Manage Inventory page. They can also navigate to the purchase orders using the Manage Orders page.
-
Once acknowledged, the supplier inventory manager is now able to fulfill the purchase order. They can view the open purchase order quantity listed in the Purchase Order Quantity column on the Manage Inventory page. They can also navigate to the open purchase orders using the Manage Orders page.
-
The supplier inventory manager is now able to ship the product. The supplier can optionally create an advanced shipment notice (ASN) using Create ASN on the Manage Inventory page. Once the ASN is created, the quantity shipped now appears as In-Transit Quantity on the Manage Inventory page.
-
The inventory management user receives and delivers the item to its deliver-to location. The supplier inventory manager can view the items awaiting to be delivered using the Received Quantity column on the Manage Inventory page. Once an item is delivered it will be included in the on-hand quantity.
-
The supplier inventory manager may create an invoice, or an invoice will be automatically generated by the enterprise on behalf of the supplier. The supplier inventory manager can view the invoices associated to a specific replenishment item using Review Item Transactions on the Manage Inventory page.
-
The enterprise processes the invoice and generates a payment. The supplier inventory manager can view the payments associated to a specific replenishment item using Review Item Transactions on the Manage Inventory page.