Business Flows for Supply Planning
You use the Supply Planning work area, a modern planning cloud solution, to run business flows to transform demand to supply.
You can perform the following in the Supply Planning work area:
-
Process data collection, inventory planning, and supply planning.
-
Automate the entire sequence of planning processes or run a subset of the processes.
-
Analyze and adjust your data at any stage.
The following figure illustrates the sequence of a supply planning business flow, starting from data collection, inventory planning, supply planning, and ending with execution and archival.
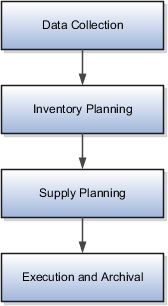
Data Collection
Data collection is the first step of the planning business flow. You can collect data from various Oracle Fusion Cloud Supply Chain & Manufacturing (SCM) applications and use the data in planning applications.
You can collect data that are primarily of three types:
-
Master data: Primarily sourced from Oracle Fusion Cloud Supply Chain & Manufacturing (SCM).
-
Demand data: Two potential sources of demand data are sales orders that flow from Oracle Fusion Cloud Order Management and the shipment history from Oracle Fusion Cloud Inventory Management.
-
Supply data: The supply data are collected from three sources:
-
Oracle Fusion Cloud Inventory Management
-
Oracle Fusion Cloud Manufacturing
-
Oracle Fusion Cloud Purchasing
-
Apart from collecting data from an Oracle Fusion source system, you can also collect data from an external source system. Use the predefined collection templates (XLSM files) to collect data from an external source system.
Inventory Planning
You can use inventory planning capability to calculate the statistical safety stock based on the volatility of demand and stocking targets. It addresses diverse supply and demand patterns with multiple algorithms based on mean absolute deviation in units (MAD), mean absolute percentage error (MAPE), and arrival rate. You can set the target service levels at any dimension of the hierarchy, which enables you to segment your stocking policies by customer, channel, product family, warehouse, or other factors. You can also set the inventory manually by using mass updates when appropriate. For example, you can set the inventory manually when you launch a new product.
Supply Planning
Using supply planning, you can calculate resource and material requirements based on customer and safety stock requirements, lead times, calendars, availability, and other parameters.
You can generate unconstrained supply plans, meaning that you ignore limited resource or supplier capacity, which provides the following advantages:
-
Balances supply and demand and recommends new supplies as needed.
-
Recommends when to reschedule or cancel a supply.
-
Identifies material shortages, resource overloads, and supplier capacity overloads.
-
Identifies when supplies don't have sufficient lead time (lead time compression).
-
Plans your entire supply chain, including contract manufacturers.
Supply plans can model outsourced manufacturing and delivery scenarios, including drop ship and back-to-back orders. It also supports hub and spoke planning configurations, such as using an MPS plan as a demand schedule to an MRP plan.
Plan Execution
You can share the order recommendations and save the plan to drive execution.
By default, the supply planning processes are integrated with other Oracle Fusion Cloud SCM applications. During the plan execution, the integration helps in the following:
-
Automatically releases planned orders and reschedules of existing supplies.
-
Manually releases groups of orders when necessary.
-
Manages changes and cancellations.
-
Manage back-to-back and drop ship orders.
Planners can set up automatic release rules or release orders manually.