How Configure-to-Order Works
Here's an example of how Supply Chain Orchestration fulfills a configured item in a make flow.
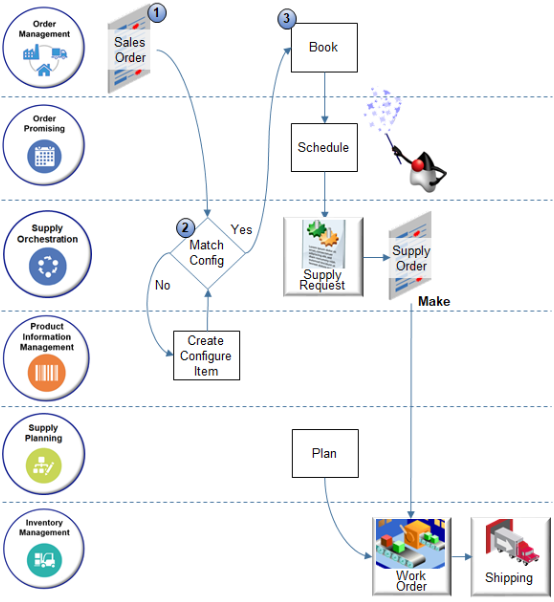
Note
-
Your user creates a sales order in the Order Management work area, searches the catalog line for the zCZ_AT6751010- Vision Slimline 5001 item, clicks Configure and Add, uses the Configure dialog to set configure options, clicks Finish, then submits the order.
-
Order Management sends a request to Supply Chain Orchestration. The request includes details about the configured item, including options that the user chooses.
If its an assemble-to-order request, or a pick-to-order request with at least one assemble-to-order component, then Supply Chain Orchestration examines the request to determine whether it already processed the configured item during a prior request.
If Supply Chain Orchestration
Description
Hasn't already processed the configured item during a prior request.
Supply Chain Orchestration sends a request to Product Information Management to create a new one, and Product Information Management creates it.
Product Information Management stores the configuration in a single record with a unique name. Order Management stores the record identifier in the Configuration Item attribute on the order line.
For example:
-
Assume the user adds the Vision Slimline 5001 to an order line. It includes configure options for the screen and CPU. The user sets the screen to 10" and CPU to 2.5GHz. Supply Chain Orchestration searches it records and finds that no other order line has ever requested this configuration, so it sends a request to create it.
-
Some time later, the user adds another Slimline and sets the screen to 10" and CPU to 2.5GHz. Supply Orchestration finds the exact same configuration and uses it.
-
Some time later, the user adds another order line that contains the Slimline, but this time sets the screen to 8" and CPU to 2.5GHz. Supply Chain Orchestration doesn't find the exact same configuration, so it sends a request to create it.
Supply Chain Orchestration sends a request to create a new configuration even if only one option is different from configurations it already created.
This feature works the same across users, order lines, and orders.
Already processed the configured item with the same configure options in a previous request.
Supply Chain Orchestration sends the Configuration Item attribute to Order Management.
Here's how Product Information Management stores the zCZ_AT6751010.
Note
-
A search for zCZ_AT6751010 returns the model and each instance of the model.
-
zCZ_AT6751010 is the configuration model you create. Product Information Management doesn't update it.
-
Supply Chain Orchestration sent a request to Product Information Management to create the other two instances when your user ordered them in Order Management.
-
zCZ_AT6751010*1088 is a unique instance of zCZ_AT6751010. It contains specific values that your user chooses, such as a 10" screen and 2.5GHz CPU.
-
zCZ_AT6751010*1089 is another unique instance of zCZ_AT6751010. It contains an 8" screen and 2.5GHz CPU.
Product Information Management stores the item as a nonconfigured item with no structure. It doesn't store the structure of the configured item instance. It does this to avoid storing duplicate structural elements in tables. Supply Chain Orchestration stores the choices your user makes for each configure option and the structure in the match repository that Supply Chain Orchestration uses. If you enable transaction attributes on your item, then Supply Chain Orchestration also stores them in the match repository.
-
-
-
The flow continues. It uses the same steps that a make flow uses for an item that isn't configured. For details, see How Supply Chain Orchestration Works.
Points to Consider
-
Configure-to-order primarily supports the make flow and the buy flow. It also supports the transfer flow and drop ship flow. For example, if your customer returns a configured item, then its available for transfer or ship from stock.
-
Supply Chain Orchestration sends a request to Product Information Management to create the configured item for assemble-to-order when the user clicks Submit in the Order Management work area.
-
The configure-to-order flow creates the configured item in Product Information Management on demand, when you need it. If the configuration already exists, then the flow reuses it instead of creating a new record.
Inventory creates the physical item just-in-time, only when you need it, then ships it. Inventory doesn't stock the item before you need it. Inventory creates another instance of the physical item for each shipment.
-
Configure-to-order also supports drop ship where you source and ship from a supplier. Supply Chain Orchestration doesn't manage supply for drop ship, but it does manage creating the configured item in a drop ship flow.
-
To support the make flow, configure-to-order uses the work definition to create a work order at runtime. The model can be valid in Product Information Management but the flow can still fail in manufacturing. For example, if the work order in manufacturing fails to assign even one option or option class to an operation step, then the work definition isn't valid, Promising won't provide a recommendation, and the flow will fail.
-
Use the View Configured Item Structure page or a web service to get details about each configure option. For details, see View Structures of Configured Items.
-
You can't disable matching because it makes sure your flow is efficient.
-
You can add a transactional item attribute for configuration matching that implements specificity in your configuration. You can add it to an item class at any level of your model.
-
The Match Configuration attribute on the Specifications tab on the Edit Item page in Product Information Management applies to Oracle E-Business Suite. It has no effect on Oracle Cloud applications.
-
At runtime, you can't cancel a configure option in a pick-to-order item or kit when the shipment is out of proportion. Assume configured item A includes configure option B and configure option C. 1 unit of item A includes 1 unit of option B, and 1 unit of option C, so the proportion is 1-1-1 (1 unit of A equals 1 unit of B and 1 unit of C). Assume you order 10 units of item A, so the ordered proportion is now 10-10-10. Assume you ship 8 units of B and 2 units of C. The proportion in the shipment is 10-8-2, and its out of proportion. If the shipment is out of proportion, then you can't cancel the remaining quantity that hasn't shipped.
-
Child Components
Configure-to-order supports each item or assemble-to-order model as a child component in a pick-to-order model. The back-to-back flow can stock each component separately, in different locations.
-
It isn't necessary to source all child components in a pick-to-order model from the same business-to-business flow.
-
You can ship some children in a typical Order Management shipment as long as you ship them together with the business-to-business items.
-
If you use the same date, then you can ship all children in a business-to-business flow or none in the business-to-business flow.
-
You can drop ship all children from the same supplier.