How You Plan Project-Specific Supply
Let's understand the high-level process flow of project-specific supply planning. You can find more details about these processes in different topics of this chapter.
-
You start your project-specific supply planning with the collection of these entities:
-
Project and task attribute values and their relationships from Project Portfolio Management
-
Supplies and demands with project and task values from Oracle Inventory Management, Oracle Order Management, Oracle Purchasing, and Oracle Manufacturing
-
Forecast and safety stock that are specific to project and task
-
Organization attribute with project references
-
Item attributes, such as Hard Pegging Level and Allow Use of Common Supplies, required for project-specific supply planning
-
-
You then create project groups and assign projects to the groups. Creating project groups enables the planning process to net supplies within a project group across multiple projects and their tasks.
-
The next step is to create attribute-based netting rules. The planning process uses the netting rule to net and share supplies at the project group, project, and task levels.
-
You create a plan and associate the netting rule to the plan. You then run the plan from the Supply Planning or the Demand and Supply Planning work area.
-
You review your plan output for project-specific supplies and demands and release planned orders with project and task attributes to Manufacturing, Purchasing, or Inventory.
Here's an illustration that explains the high-level process flow of project-specific supply planning:
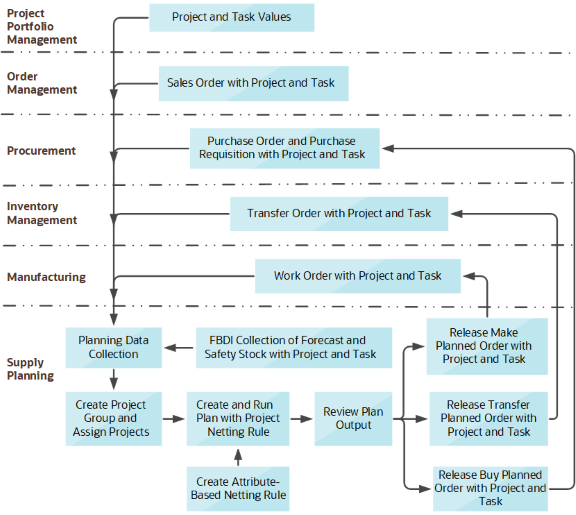