Defining Location Accounting
One option for structuring accounting rules is with the location accounting approach. Location accounting enables you to define different ChartField combinations for each storage area within an inventory business unit. For example, you can assign a raw material account to one storage area and a finished goods account to another storage area. Any material residing in the raw material storage area debits or credits the raw material inventory account when material moves in or out of that storage area. Any material residing in the finished goods storage area debits or credits the finished goods inventory account.
When using the location accounting option in a manufacturing environment, assign ChartFields to both storage areas and production areas. By assigning ChartFields to storage and production areas, you can segregate raw material, in process material, and finished goods inventory for accounting purposes.
Note: For location accounting, you perform many of the same steps used to define the basic accounting structure. Please read the preceding section, " Defining the Accounting Structure" before setting up location accounting.
To define the location accounting structure:
Select the Location Accounting Required check box on the Inventory Options page.
This page is defined by SetID. Any inventory business unit using this SetID for the record group IN_01 (business unit attributes) uses location accounting.
Define cost profiles to use storage area control.
Use the Storage Area Accounting page to establish ChartField combinations for each storage area within the inventory business unit.
(Manufacturing environment only) Use the Production Area Accounts page to define the ChartField combinations for each production area.
Use the Accounting Rules page to define ChartField combinations that are not included in the Storage Area Accounting page.
The system uses both pages to create the complete accounting entries.
After establishing the accounting structure, the Transaction Costing process costs transactions and the Accounting Line Creation process creates accounting entries. Both processes are initiated from the Cost Accounting Creation process page.
Page Name |
Definition Name |
Usage |
---|---|---|
BUS_UNIT_OPT_IN |
Select the Location Accounting Required check box to turn on location accounting. |
|
SET_CNTRL_TABLE1 |
Verify that the inventory business unit uses the SetID from the Inventory Options page. Check the record group IN_01. |
|
Profiles Page |
CM_PROFILE_DEFN |
Use cost profiles to determine how the system costs items in the business unit's cost book. When using location accounting, select the Storage Area Control for Costs check box. |
STORAGE_ACCT_INV |
Define the ChartField combinations for each storage area. The system debits and credits these ChartFields when material is moved in and out of the storage area. |
|
SF_PRAREA_ACCT |
Define the ChartField combinations for each production area. The system debits and credits these ChartFields when material is received into or issued from the production ID or schedule. This page applies to a manufacturing environment only. |
|
CM_ACCTG_DIST |
Create the debit and credit lines for the accounting entries based on the business unit, transaction group, distribution type, item or item group, and cost element. The system uses this page in combination with the Storage Area Accounting page. |
Use the Inventory Options page (BUS_UNIT_OPT_IN) to select the Location Accounting Required check box to turn on location accounting.
Navigation:
To use storage location accounting, select the Location Accounting Required check box on the Inventory Options page. This page enables you to set up storage location structures and attributes (such as stocking units and dimensions) at the TableSet level. You can share these attributes with one or more inventory business units. Use the Set Control - Record Group page to attach these inventory options to an inventory business unit by setting the record group IN_01 to the same SetID that you used to define the Inventory Options page.
It is highly recommended that if you are using location accounting, you should use the storage area control option located on the Cost Profile page (Set Up Financials/Supply Chain, Product Related, Cost Accounting, Cost Profiles, Profiles). Select the Storage Area Control for Costs check box to apply the FIFO or LIFO depletion method (defined in the cost profile) at the storage-area level. The system uses FIFO or LIFO as the cost based on the receipts to the specific storage area from which the item was depleted. In PeopleSoft Cost Management, you assign cost profiles to items to determine how to cost inventory transactions.
Storage area control can be used even with storage area accounting off. This enables you to stratify the granularity of FIFO and LIFO layers. For example, suppose that there is a FIFO cost flow method on the cost profile. Three receipts are putaway in an inventory business unit (receipts 1, 2, and 3). Each has a separate receipt cost. Receipt 1 is placed in the storage area Zone A. Receipts 2 and 3 are placed in Zone B. Then, items are issued from Zone B. Without storage area control, the deplete cost would be from receipt 1 in a FIFO environment, but with storage area control, the deplete cost comes from receipt 2, because it is the first within Zone B.
To define accounting by storage area, use the Storage Area Accounting component (STORAGE_ACCTS). Use the Storage Area Accounting Rules component interface (STORAGE_ACCTS_CI) to load data into the tables for this component.
Use the Storage Area Accounting page (STORAGE_ACCT_INV) to define the ChartField combinations for each storage area.
The system debits and credits these ChartFields when material is moved in and out of the storage area.
Navigation:
This example illustrates the fields and controls on the Storage Area Accounting page (partial page). You can find definitions for the fields and controls later on this page.
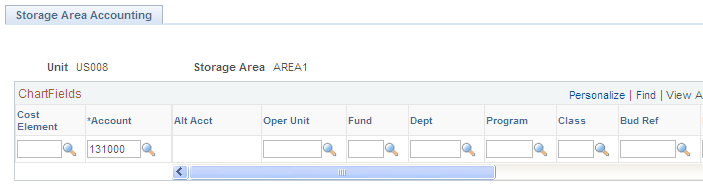
If you are using location accounting, enter the ChartField combinations for each storage area using the Storage Area Accounting page. Use these ChartField combinations to create the debit entry when materials are received in the storage area and to create the credit entry when materials are issued from the storage area. The other side of the entry comes from the matching Accounting Rules page.
This page remains available to edit, thus, giving you the ability to alter the ChartField combinations over time.
Working with Cost Elements
An item can have one or more cost elements defined in its product structure. The Transaction Costing process calculates and stores the costs by cost element. During the Accounting Line Creation process, the system attempts to match up the item's transaction costs by cost element to any rows using the same cost element on the Storage Area Accounting page. If this is not found, then the system uses a row with a blank cost element. Therefore, you add flexibility to the system by adding different combinations of cost elements using different rows on the same page. Rows with a blank cost element can be used for any unspecified cost elements. If you can use the same ChartFields, regardless of the cost element, leave the Cost Element field blank.
Use the Production Area Accounts page (SF_PRAREA_ACCT) to define the ChartField combinations for each production area.
The system debits and credits these ChartFields when material is received into or issued from the production ID or schedule. This page applies to a manufacturing environment only.
Navigation:
If you are using location accounting in a manufacturing environment, use this page to define the ChartField combinations for the production areas to track in-process inventory. As material is received or issued from a production ID or production schedule, the system uses the ChartField combinations of the production area to create debit or credit entries. When you create accounting entries, the system debits the ChartFields specified here for any material consumption, earned labor, applied overhead, or favorable variances. The system also credits the ChartFields for any assembly completions to stock or to another production area, assembly scrap, or unfavorable variances. The other side of the entry comes from the matching Accounting Rules page.
This page remains available to edit, thus, giving you the ability to alter the ChartField combinations over time.
Select the production type for which the ChartFields are defined. You can define a set of accounts for Production, Rework, and Teardown production types.
Working with Cost Elements
In the Accounting Line Creation process, the system attempts to match up the item's transaction costs by cost element to any rows using the same cost element on the Production Area Accounts page. If this is not found, then the system uses a row with a blank cost element. If you can use the same ChartFields, regardless of the cost element, leave the Cost Element field blank.
Use the Accounting Rules page (CM_ACCTG_DIST) to create the debit and credit lines for the accounting entries based on the business unit, transaction group, distribution type, item or item group, and cost element.
The system uses this page in combination with the Storage Area Accounting page.
Navigation:
The Storage Area Accounting page and Production Area Accounts page defines one side of the accounting entry when material is putaway, issued, or adjusted within a storage or production area. The other side of the accounting entry comes from the corresponding Accounting Rules page based on the business Unit, Transaction Group, Item ID or Item Group, and Distribution Type fields. If the transaction is not directly related to a storage or production area, then they system derives both sides of the transaction from the appropriate Accounting Rules page.
If you are using location accounting, the system derives ChartField combinations that it uses to create accounting entries from these pages:
Transaction Group |
Description |
DR |
CR |
---|---|---|---|
010 |
Receipt to Inspection |
Storage Area Accounting |
Accounting Rules |
012 |
Return to Vendor |
Accounting Rules |
Storage Area Accounting |
013 |
Return to Vendor From Inspection |
Accounting Rules |
Storage Area Accounting |
020 |
Putaway |
Storage Area Accounting |
Accounting Rules |
021 |
Receipts from Production |
Storage Area Accounting |
Production Area Accounts |
024 |
Customer Returns |
Storage Area Accounting |
Accounting Rules |
030 |
Usages & Shipments |
Accounting Rules |
Storage Area Accounting |
032 |
Non Stock Shipment |
Accounting Rules |
Accounting Rules |
037 |
VMI Interunit shipment |
Accounting Rules |
Storage Area Accounting |
038 |
VMI Consumption |
Accounting Rules |
Storage Area Accounting |
040 |
Physical Count Adjustments |
Accounting Rules |
Storage Area Accounting |
041 |
Cycle Count Adjustment |
Accounting Rules |
Storage Area Accounting |
050 |
User Adjustments |
Accounting Rules |
Storage Area Accounting |
051 |
Inventory Scrap |
Accounting Rules |
Storage Area Accounting |
052 |
Shipping Adjustment |
Accounting Rules |
Storage Area Accounting |
053 |
Floor Stock Issues/Ret |
Accounting Rules |
Storage Area Accounting |
054 |
Inventory Scrap for RTV |
Accounting Rules |
Storage Area Accounting |
060 |
Bin-to-Bin Transfers |
Storage Area Accounting |
Storage Area Accounting |
200 |
Inventory Revalue |
Accounting Rules |
Storage Area Accounting |
201 |
Inventory Reval - Inspection |
Accounting Rules |
Storage Area Accounting |
205 |
Value Adjustment |
Accounting Rules |
Storage Area Accounting |
206 |
Value Adjust/ActCost Items |
Accounting Rules |
Storage Area Accounting |
210 |
WIP Revalue (Comps, Assys) |
Accounting Rules |
Production Area Accounts |
211 |
WIP Revalue (Conv Costs) |
Accounting Rules |
Production Area Accounts |
212 |
WIP Revaluation (Scrap) |
Accounting Rules |
Production Area Accounts |
220 |
Component Kit |
Production Area Accounts |
Storage Area Accounting |
221 |
Route to Production Kit |
Production Area Accounts |
Production Area Accounts |
222 |
Waste Completion |
Production Area Accounts |
Accounting Rules |
223 |
Component/Output Transfers |
Production Area Accounts |
Production Area Accounts |
230 |
Component Consumption |
Production Area Accounts |
Storage Area Accounting |
231 |
WM Usage (Maintenance Management Usage) |
Accounting Rules |
Storage Area Accounting |
240 |
Earned Labor |
Production Area Accounts |
Accounting Rules |
250 |
Assembly Scrap |
Accounting Rules |
Production Area Accounts |
261 |
Material Variances |
Accounting Rules |
Production Area Accounts |
262 |
Conversion Variances |
Accounting Rules |
Production Area Accounts |
263 |
Rework Expense |
Accounting Rules |
Production Area Accounts |
264 |
Outside Processing PPV |
Accounting Rules |
Accounting Rules |
265 |
Teardown Variance |
Accounting Rules |
Production Area Accounts |
400 |
Std Cost Variance Receipts |
Accounting Rules |
Accounting Rules |
401 |
Wt Avg Updates from AP |
Storage Area Accounting |
Accounting Rules |
402 |
Std Cost Exchange Rate Var |
Accounting Rules |
Accounting Rules |
403 |
Wt Avg Cost Updates - ERV |
Storage Area Accounting |
Accounting Rules |
405 |
Wt Avg Update Writeoffs |
Accounting Rules |
Accounting Rules |
407 |
Subcontract Standard Cost PPV2* |
Accounting Rules |
Accounting Rules |
408 |
Subcontract Standard Cost PPV2 ERV* |
Accounting Rules |
Accounting Rules |
415 |
RTV Variances |
Accounting Rules |
Accounting Rules |
461 |
Voucher Variance Writeoffs |
Accounting Rules |
Accounting Rules |
500 |
Miscellaneous Charges |
Accounting Rules |
Accounting Rules |
501 |
Freight Charges |
Accounting Rules |
Accounting Rules |
601 |
Wt Avg Upd Production Var |
Storage Area Accounting |
Accounting Rules |
605 |
Wt Avg Upd Prod Writeoffs |
Accounting Rules |
Accounting Rules |
606 |
Avg Rev Compl Write-off* |
Accounting Rules |
Accounting Rules |
622 |
Actual Waste Cost |
Production Area Accounts |
Accounting Rules |
630 |
Overhead |
Production Area Accounts |
Accounting Rules |
640 |
Actual Labor Costs |
Production Area Accounts |
Accounting Rules |
645 |
Actual Machine Costs |
Production Area Accounts |
Accounting Rules |
651 |
Production Cost Writeoff |
Production Area Accounts |
Accounting Rules |
661 |
Actual Cost Variances |
Production Area Accounts |
Accounting Rules |
664 |
Subcontracted Cost |
Accounting Rules |
Accounting Rules |
If the transaction involves interunit or intercompany transfers, then part of the accounting entries are derived from pages defined for the interunit model explained in the "Managing Interunit Transfer Pricing and Additional Costs" topic. The interunit and intercompany transaction groups include:
022 - IBU Transfer Receipts.
025 - InterCompany Receipts.
031 - InterBU Transfer Shipments.
035 - InterCompany Transfers.
042 - IBU Transfer Adjustments.
300 - Gain/Loss on Transfer Price.
301 - InterCompany Cost of Goods.
If the transactions involve Shipment On Behalf Of or InterUnit Expensed Issues, see the sections in this topic related to these subjects. These transaction groups are:
034 - Ship on Behalf of Other BU.
036 - InterUnit Expensed Issue.
026 - Expensed Issue Return.
302 - ShipOnBehalf Gain/Loss.