Setting Up Pegging
Pegging is set up at the Business-unit level, Item level, User level, Material storage location level, and Notification framework.
Page Name |
Definition Name |
Usage |
---|---|---|
IN_PEG_SETUP |
Define pegging attributes for the PeopleSoft Inventory business unit. |
|
IN_PEG_IT_SETUP |
Define pegging attributes for the item and business-unit combination. This page only needs to be used if the item varies from the business-unit level setup. |
|
IN_PEG_USER_SEC |
Based on the User ID, select the type of supply and demand that the user can work with. |
|
Default Putaway Locations Page |
DEFAULT_LOC_INV |
Define a default material storage location to place pegged supply quantities when received into the inventory business unit. This pegging location is defined for the inventory business unit and item ID combination. You can establish material storage locations for both owned and non-owned stock putaways. The system uses this location if no material storage location is specified on the putaway transaction. |
Default Pegging Putaway Location Details Page |
DFLT_PEG_LOC_INV |
Define a default material storage location to place pegged supply quantities when received into the inventory business unit. This pegging location is defined for the inventory business unit level. Both an owned and non-owned material storage location can be defined for a business unit. The system uses this location if no material storage location is specified on the Default Putaway Locations page. |
Setup Fulfillment - Shipping Page |
OF_SETUP6_INV |
At the business-unit level, define the default pegging location as the picking material storage location for pegged orders. |
Setup Item Fulfillment - Shipping Options Page |
OF_SETUP_IT2_INV |
At the item level, define the default pegging location as the picking material storage location for pegged orders. |
To set up pegging attributes at the inventory business-unit level, use the Setup Pegging by Business Unit (IN_PEG_SETUP_GBL) component.
Use the Pegging Setup page (IN_PEG_SETUP) to define pegging attributes for the PeopleSoft Inventory business unit.
Navigation:
This example illustrates the fields and controls on the Pegging Setup page. You can find definitions for the fields and controls later on this page.
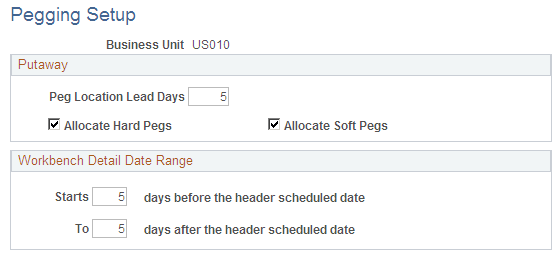
Field or Control |
Description |
---|---|
Unit |
Enter the Inventory business unit. |
Peg Location Lead Days |
Enter the number of lead days for pegged items in this inventory business unit. When the putaway processes receive pegged supply quantities, the peg location lead days are used to determine where to place the stock. The system adds the peg location lead days to today's date and compares the result to the scheduled ship date of the outgoing pegged demand order. If the order is within the lead days window, then the pegged supply quantity is received (putaway) into the pegged material storage location specified. If the order is not within the lead days window, the pegged supply quantity is received into the standard material storage location determined by the putaway processes. |
Allocate Hard Pegs |
Select to allocate any hard-pegged receipts to the outgoing demand line at the time of putaway. A hard allocation reserves stock at a specific material storage location within the inventory business unit to satisfy an outgoing order line. Deselect this check box to reserve any hard-pegged receipts to the outgoing demand line at the time of putaway. A soft reservation reserves stock at the inventory business unit level to satisfy an outgoing order line. The specific material storage location for picking and shipping the stock is not reserved. |
Allocate Soft Pegs |
Select to allocate any soft-pegged receipts to the outgoing demand line at the time of putaway. A hard allocation reserves stock at a specific material storage location within the inventory business unit to satisfy an outgoing order line Deselect this check box to reserve any soft-pegged receipts to the outgoing demand line at the time of putaway. A soft reservation reserves stock at the inventory business unit level to satisfy an outgoing order line. The specific material storage location for picking and shipping the stock is not reserved. |
Workbench Detail Date Range
Enter values to determine the time window displayed on the Pegging Workbench; this is used to limit the number of rows returned in the workbench search. These values only apply to unpegged supply or demand transactions.
Field or Control |
Description |
---|---|
Starts |
Enter the number of days prior to the demand line's scheduled shipment date or prior to the supply line's receipt date that should be displayed. The system subtracts the Start days from the demand or supply date and selects any supply/demand to be received/shipped within this window. |
To |
Enter the number of days past the demand line's scheduled shipment date or past the supply line's receipt date that should be displayed. The system adds the To days to the demand or supply date and selects any supply/demand to be received/shipped within this window. |
To set up pegging attributes at the item level, use the Pegging Attributes by Item (IN_PEG_IT_SETUP_GBL) component.
Use the Pegging Item Setup page (IN_PEG_IT_SETUP) to define pegging attributes for the item and business-unit combination.
This page only needs to be used if the item varies from the business-unit level setup.
Navigation:
This example illustrates the fields and controls on the Pegging Item Setup page.

Define pegging attributes for a particular item ID to override the same attributes at the business-unit level.
For field definitions, see the Defining Pegging Attributes for the Inventory Business Unit section above.
See Pegging Setup Page.
To set up user security for pegging, use the Pegging User Security (IN_PEG_USER_SEC_GBL) component.
Use the User Security page (IN_PEG_USER_SEC) to based on the User ID, select the type of supply and demand that the user can work with.
Navigation:
This example illustrates the fields and controls on the User Security page. You can find definitions for the fields and controls later on this page.

This page enables you to set up pegging security by user. The user must be defined within the User Security page in order to peg demand or supply.
For each component where pegging is enabled, the system checks the user ID security setup. If the relevant order type is selected, then the system displays the link within that component. For example, if the user is in the Order Entry Form in PeopleSoft Order Management, the link Peg to Demand is available only if the Sales Orders check box has been selected for the user on the User Security page. In addition, once the link is taken, the Pegging Workbench filters the supply or demand based on the check boxes selected on the User Security page. For example, if a user can peg to all supply order types but production, then only purchase orders, requisitions, and interunit transfers would be available to peg to in the Pegging Workbench.
Demand Order Type
Select the demand side for pegging.
Field or Control |
Description |
---|---|
Sales Orders |
Select to enable this user ID to peg sales orders from PeopleSoft Order Management. |
Stock Requests |
Select to enable this user ID to peg stock requests in PeopleSoft Inventory. |
Work Orders |
Select to enable this user ID to peg work orders from PeopleSoft Maintenance Management. |
Transfer Demand |
Select to enable this user ID to peg the outgoing interunit stock requests. Interunit stock requests in PeopleSoft Inventory are used to transfer stock from one inventory business unit to another. |
Supply Order Type
Select the supply side for pegging.
Field or Control |
Description |
---|---|
Purchase Orders |
Select to enable this user ID to peg to purchase orders in PeopleSoft Purchasing. |
Requisitions |
Select to enable this user ID to peg to requisitions in PeopleSoft Purchasing. |
Production |
Select to enable this user ID to peg to production IDs in PeopleSoft Manufacturing. |
Transfer Supply |
Select to enable this user ID to peg to interunit stock requests as incoming supply. Interunit stock requests in PeopleSoft Inventory are used to transfer stock from one inventory business unit to another. |
Peg QTY Putaway/Sourced
System administrators determine which users can use the Pegging Workbench to correct input errors or reverse a peg completion. Use caution and limit the number of users who have this ability. For more information about correcting peg quantities, see the "Changing Peg Chains" section of this topic.
Field or Control |
Description |
---|---|
Allow Change |
Select this check box to enable the user to change the Peg Qty Putaway/Sourced field on the Pegging Workbench. |
Deny Below Order Complete |
Select this check box to prevent the user from reducing the quantity in the Peg Putaway/Source field below the quantity that has already been completed on the supply transaction or demand transaction. This check box is only available if you have selected the Allow Change check box. This feature prevents the user from creating open pegged quantity that is linked to completed quantity, for example, opening peg quantity that is linked to quantity that has already been putaway. |
See Changing Peg Chains.
When pegged supply arrives at the Inventory business unit for putaway, the system must decide where to place the stock. A separate material storage location can be defined to prevent pegged supply from combining with incoming supply available to fulfill other orders. You can establish default pegging locations for the putaway of both owned and non-owned stock.
Note: When choosing a default pegging location, the system prevents you from selecting a materials storage location that is defined as non-open, non-nettable, WIP, or cross-docked.
If the pegged order (outgoing demand) is scheduled to ship within the pegging lead days window, then the pegged supply quantity is received (putaway) into the default pegging location specified. If the pegged order is not within the pegging lead days window, the pegged supply quantity is received into the standard material storage location determined by the putaway processes.
When pegged supply is received into PeopleSoft Inventory, the putaway processes:
Places the stock in the material storage location specified on the putaway transaction.
If no location is specified on the putaway transaction, then the system looks to the Default Putaway Locations page to determine if a default pegging location has been specified for the inventory business unit and item ID combination.
If no location is specified on the Default Putaway Locations page, then the system looks to the Default Pegging Putaway Location Details page to determine if a default pegging location has been specified for the inventory business unit.
For demand lines with a pegged quantity that was reserved during the Complete Putaway process, the Order Release process can now allocate stock from a specific material storage location. If you choose to create an allocation, the Order Release process attempts to find stock to allocate to a pegged quantity in:
The default pegging location defined on the Default Putaway Locations page for the inventory business unit and item ID combination.
If no location is specified on the Default Putaway Locations page or no stock is available in the location, then the system looks to the Default Pegging Putaway Location Details page to determine if a default pegging location has been specified for the inventory business unit.
If there is no default pegging location or no stock available in the location, then the system uses the picking method specified on the Order Release process page.
Keep in mind that pegged quantities that were allocated during the Complete Putaway process will keep that allocation when released for picking.
Both soft and hard pegs can send Message Dashboard notifications to interested parties when:
Pegged supply is received into the purchasing business unit.
Pegged supply completes putaway into the inventory business unit.
The pegged orders are changed or canceled.
This is a critical step to monitoring your peg chains in your environment. To use Message Dashboard notifications, you must set up the system-level registry and the business-unit level registry for pegging notifications.
The Message Dashboard is a central place to view all information related to messages, warnings and errors that occur from batch or online processes. A user receives notification of a message through an email, a worklist, or XML format. The notification method contains a link to the message dashboard, so that the user can quickly view the message detail, and take action. The message dashboard provides potential actions, which make the decision making process easier for the user, or may redirect the user to other components within the system.
For pegging notifications using the Message Registry, the following process names do not use the user role or user ID defined in the BU-Level Notifications page or the System-Level Notifications page. Instead, these process names use the owner of the transaction, as follows:
Process Name |
User Notified |
---|---|
OM_PEGGING |
The customer service representative (CSR) located on the sales order. |
WM_PEGGING |
The lead person located on the work order. |
PO_PEGGING |
The buyer located on the purchase order. |
REQ_PEGGING |
The requester located on the requisition. If no requester is listed, then the system uses the user ID or user role listed on the BU-Level Notifications page or the System-Level Notifications page. |
IN_PEGGING and PRDN_PEGGING process names use the user ID or user role defined on the BU-Level Notifications page or the System-Level Notifications page.
For all of the above pegging notifications:
An online pegging notification sends an email and a worklist entry.
A batch pegging notification sends a batch email and no worklist entry.
Pegging Notifications in PeopleSoft Manufacturing
The pegging notifications for production IDs in PeopleSoft Manufacturing have an additional setting on the MFG Business Unit Options page. The Compl and Close Peg Qty Change group box controls how often notifications are sent to a production ID. This group box controls how often pegging notifications are sent to a user or group of users when changes are made on a production ID. PeopleSoft Manufacturing has a number of common circumstances that could cause excessive pegging notifications to be generated. For example, normal scrap activity during the completions process could result in quantity reduction notifications. Completing serial controlled items would generate a receipt notification for every serialized item. The close process generates close notifications for every order closed. PeopleSoft Manufacturing offers three options for controlling the number of pegging notifications generated during the completions and close processes:
Notify at Compl and Close: Enables all normal pegging notifications including order quantity changes and closing of production.
Notify at Close: Enables normal notifications in the production close process and prevents order quantity change notifications during completions.
No Notify at Compl or Close: Suppresses close notifications during the close process and suppresses quantity change notifications during completions.
Pegging Notification Process Flow
The following diagram illustrates the process flow for notifications from online pegging processes. The online process creates a message, which is automatically sent to the Message Dashboard. If notifications are enabled in the message at the business-unit level registry or the system-level registry, then the system notifies the appropriate person using an email or a worklist entry where a link is provided to take the individual to the message detail page of the Message Dashboard:

See the product documentation for PeopleSoft Events and Notifications Framework