Defining Fulfillment Options for Specific Business Unit and Item Combinations
To define fulfillment parameters at the business unit and item combination level, use the Setup Item Fulfillment (ORD_FULF_IT_SETUP) component.
To set up reservation and backorder rules, use the Reservation/Backorder Rules (IN_FL_RULE_CMP) component.
After you establish general order processing rules and defaults at the business unit level using the Setup Fulfillment component, you can adjust key parameters for specific business unit and item combinations using the Setup Item Fulfillment component.
Page Name |
Definition Name |
Usage |
---|---|---|
OF_SETUP_IT_INV |
Override business unit fulfillment options for a specific item. |
|
OF_SETUP_IT2_INV |
Override the business unit fulfillment shipping options for a specific item. |
|
OF_SETUP_IT3_INV |
Override the business unit level defaults for the reservation and backorder rules with item-specific defaults. |
Use the Setup Item Fulfillment page (OF_SETUP_IT_INV) to override business unit fulfillment options for a specific item.
Navigation:
This example illustrates the fields and controls on the Setup Item Fulfillment page. You can find definitions for the fields and controls later on this page.
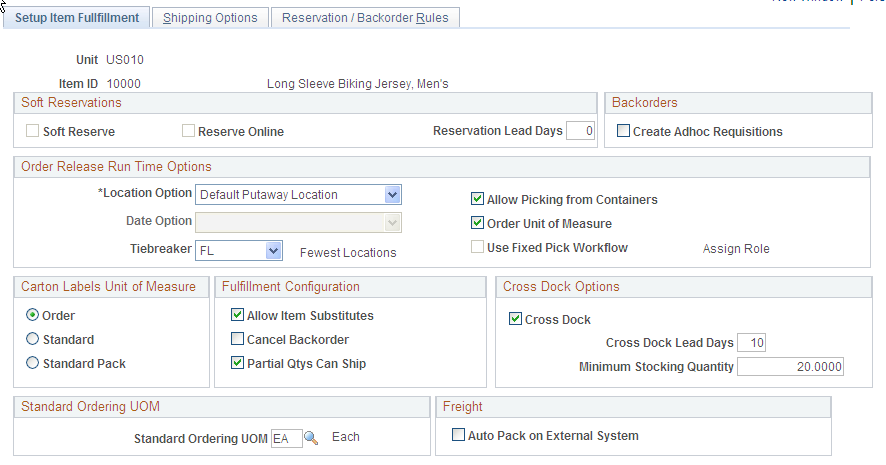
Note: Only items with a status of Active or Discontinue are valid options, and only these items appear in the Valid Values prompt table.
Soft Reservations
Specify parameters that govern how the Reserve Materials process handles soft-reserved order processing at the business unit/item level. The default settings come from the Setup Fulfillment- Reservation page.
Field or Control |
Description |
---|---|
Soft Reserve |
Select to enable the Reserve Materials process to soft reserve this item within this business unit. Clear this check box to prevent soft reservations for this specific business unit/item combination. A soft reserve moves item quantity from the business unit's quantity available to the business unit's quantity reserved so that future orders cannot consume the stock. If you do not enable soft reservations, stock is allocated to orders only at the time of order release (when the line is moved to the released state). Note: You cannot change this option at either the business unit level (on the Setup Fulfillment- Reservation page) or the business unit/item level (this page) if there are any reserved quantities processing in the system. This includes any demand that has been lot allocated or processed by the Reserve Materials process but that has not yet been shipped and depleted. |
Reserve Online |
Select to require order lines with this business unit/item combination to be soft-reserved manually using the Shortage Workbench. Performing soft reservations online enables you to manage situations of short supply by controlling how the available quantity of an item is distributed among order lines. This option applies only to soft-reserved items (you can only modify it if the Soft Reserve option is selected). The Reserve Materials process does not include items marked for online soft reservations. If you modify the Reserve Online option for business unit-item level defaulting purposes, be aware that the system ignores this setting for non-soft-reserved items. For example, you might disable soft reservations at the business unit level but select it for specific business unit/item combinations. To perform online reservations for most of those items, select as the default the Reserve Online check box at the business unit level. |
Reservation Lead Days |
Indicate the number of days required to pick, pack, and ship this specific item in the business unit. If no entry is made here, the system uses the reservation lead days in the Setup Fulfillment component. The Reserve Materials process reserves the quantity for soft-reserved order lines that have a scheduled ship date between the current date and the date defined by the current date plus the number of reservation lead days. Note: If the business unit requires closure calendar validation and processing for shipping activities as defined on the Closure Calendar page, and the calculated scheduled ship date falls on a defined closure date, the system adds one day for every number of closed days to the number of reservation lead days to compare against the scheduled ship date. Therefore, the number of lead days includes only open business days. To enable the closure calendar, you must select the Use Closure Calendar check box on the Setup Fulfillment- Reservation page. |
Backorders
Field or Control |
Description |
---|---|
Create Adhoc Requisitions |
Select to enable the Reserve Materials process to create an ad hoc replenishment request when insufficient stock is available to fulfill the demand for this business unit/item combination. Ad hoc replenishment requests can also be created by the fulfillment engine transaction requests and the Shipping/Issues component when short shipping stock. PeopleSoft Purchasing or a third-party purchasing application processes the ad hoc replenishment request. Keep in mind, partially-filled or zero-filled orders are handled by the reservation and backorder rules, and (if no rules are established) the Cancel Backorder check box. Consider your rules setup when choosing this option. |
Order Release Run Time Options
Enter the default values for order release run time options for the business unit/item combination if different from the business unit level settings. The default values come from the Setup Fulfillment- Order Release page. For descriptions to these fields see the Defining Order Release Options section of this topic.
Carton Labels Unit of Measure
Select the unit of measure to be used for this item when generating carton labels. Select only if the UOM is different from the business unit level setting on the Setup Fulfillment-Pick Plan Label page.
Fulfillment Configuration
The default values come from the Setup Fulfillment page. The Cancel Backorder and Partial Qtys Can Ship values established here are used purely as defaults for new orders created using the Create/Update Stock Request component, the Create Par Replenishment Requests process, and the purchase order sourcing processes. You can override any of these defaults on the order line. For descriptions to these fields see the Defining Basic Fulfillment Defaults section of this topic.
Cross Dock Options
Field or Control |
Description |
---|---|
Cross Dock |
Select to enable cross docking for this item in the business unit. The default value comes from the Setup Fulfillment page. |
Cross Dock Lead Days |
Identify the number of days to use when calculating open demand quantity for this cross docked item in the business unit. The default value comes from the Setup Fulfillment page. If the Use Closure Calendar check box is selected on the Setup Fulfillment- Reservation page, the system takes closure dates into consideration when calculating open demand. For example, if the closure calendar specifies Saturday and Sunday as closed days, then these days are not counted as lead days when calculating open demand. |
Minimum Stocking Quantity |
Enter the minimum quantity of the item that should be stocked in the cross docking location of this business unit. This quantity should be expressed in the stocking UOM for this item. When you receive and put away stock, the system ensures that the minimum stocking quantity is maintained in the cross docking location by adding additional stock if necessary. If enough stock is available, the system stocks either open demand or minimum stock quantity, whichever is greater. |
Standard Ordering UOM
Enter an unit of measure to be used as the default ordering UOM when creating a materials stock request for this item in this business unit. This default UOM is used by the:
Create/Update Stock Request component.
Express Issue page.
Create Par Replenishment Requests process.
You can enter both ordering and shipping UOMs as defined on the Units of Measure page (Items, Define Items and Attributes, Units of Measure). In order for the UOM value on this page to default:
To the Create/Update Stock Request component or the Create Par Replenishment Requests process, the UOM must be defined as an ordering UOM on the Units of Measure page.
To the Express Issue page, the UOM must be defined as a shipping UOM on the Units of Measure page.
A default UOM can populate the new MSR using the following default hierarchy:
The UOM entered in this field, the Standard Ordering UOM field on the Setup Item Fulfillment page. If this UOM is blank or invalid, then the system uses:
The UOM defined as the Default Req UOM on the item's Units of Measure page. This UOM must be defined as a shipping UOM for the Express Issue page and an ordering UOM for the Create/Update Stock Request component or the Create Par Replenishment Requests process. If this UOM is not valid, then the system uses:
The UOM defined as the Default Stocking UOM on the item's Units of Measure page. This UOM must be defined as a shipping UOM for the Express Issue page and an ordering UOM for the Create/Update Stock Request component or the Create Par Replenishment Requests process. If this UOM is not valid, then the system uses:
The standard UOM defined on the Define Item - General: Common page (Items, Define Items and Attributes, Define Item, General).
Freight
Field or Control |
Description |
---|---|
Auto Pack on External System |
(External third-party freight only) Select this check box to indicate that the third-party freight provider should automatically consolidate individual demand lines in a delivery into packages. The third-party system will return freight for the packages. Some third-party freight providers have functionality to automatically combine loose stock into packages based on packaging algorithms. This field can be used to tell the third-party system to use these routines to estimate how many packages and the weight and volume of these packages for freighting purposes. If the Auto-Pack External System check box is not selected then the third-party freight system would assume that each individual quantity in the shipping unit of measure is a packaging unit. This check box is also located on the Setup Fulfillment-Delivery/Freight page. The selection on this page overrides the value at the business unit level. |
Use the Setup Item Fulfillment - Shipping Options page (OF_SETUP_IT2_INV) to override the business unit fulfillment shipping options for a specific item.
Navigation:
This example illustrates the fields and controls on the Setup Item Fulfillment - Shipping Options page. You can find definitions for the fields and controls later on this page.
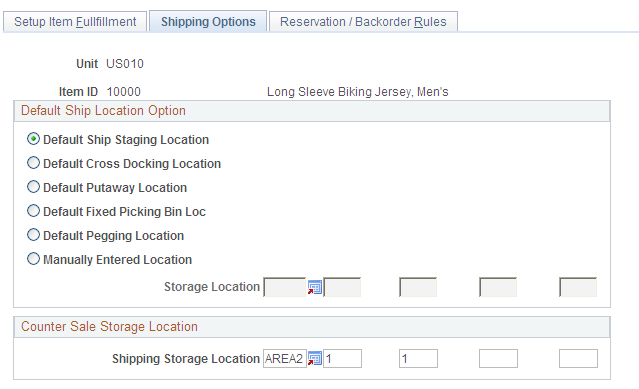
Select default values for the default ship location or the counter sale storage location for this item/business unit combination if it differs from the defaults set up at the business unit level using the Setup Fulfillment-Shipping page. For descriptions to these fields see the Defining Business Unit Fulfillment Options, Defining Shipping Options in this topic.
Use the Setup Item Fulfillment - Reservation / Backorder Rules page (OF_SETUP_IT3_INV) to override the business unit level defaults for the reservation and backorder rules with item-specific defaults.
Navigation:
This example illustrates the fields and controls on the Setup Item Fulfillment-Reservation / Backorder Rules page. You can find definitions for the fields and controls later on this page.
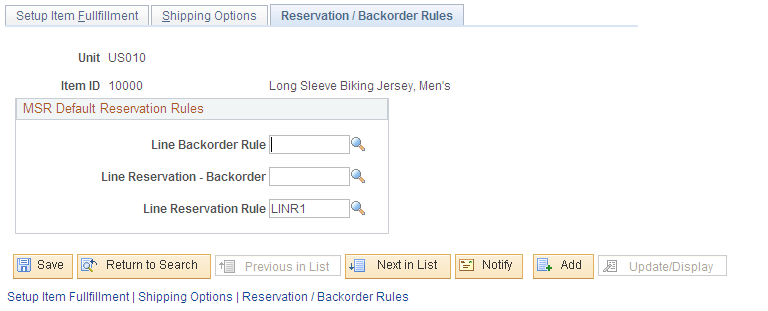
Reservation and backorder rules are used by the Reserve Materials process and online reservations to determine when the demand line of an order is ready to be moved downstream to the releasable state. Backorder rules are also used at shipping time to determine what to do with shortages that cannot be fulfilled. These rules can default to the demand line from this page (the item/business unit level). If the item/business unit level does not contain all the rules then the system looks at the Setup Fulfillment-Reservation page for defaults (the business unit level). Using this page you can enter or change the necessary default rules.
Note: If there are no reservation and backorder rules established for the demand line, then the system uses the Partial Qtys Can Ship, Cancel Backorder, and Partial Orders Can Ship check boxes to determine releases and backorders.
Field or Control |
Description |
---|---|
Line Backorder Rule (backorder rule) |
There are two parts to this rule:
|
Line Reservation-Backorder Rule |
Defines the specific criteria that must be satisfied by a backordered demand line before the demand line is moved to the releasable state. For example, a line reservation-backorder rule might be that the reserved quantity for an already backordered line must equal 100 percent of the requested quantity before it is set to the releasable state. If no line reservation-backorder rule exists, then the system used the line reservation rule for backordered demand lines. |
Line Reservation Rule (line-level reservation rule) |
Defines the specific criteria that must be satisfied by this individual demand line before the demand line is moved to the releasable state. For example, a line reservation rule might be that the reserved quantity must equal or exceed 90 percent of the requested quantity on the line before it is set to the releasable state. |
See Understanding the Reservation, Backorder, and Shortage Processes.