Understanding Par Location Management
The par location functions in PeopleSoft Inventory enable you to establish stock locations that can be replenished without tracking item on-hand quantities and material movement transactions. With par inventory management, you stock par locations with defined optimal item quantities, consume items as necessary, conduct periodic inventory counts to determine replenishment needs, and then run the Create Par Replenishment Requests process (INPGCDMD) to generate orders for items that require replenishment. The par locations might be stockrooms in a warehouse or on a hospital floor, supply closets, exchange carts, moving carts that contain items, automated point-of-service dispensing machines, or trucks that are equipped with the supplies for handling service calls.
Field or Control |
Description |
---|---|
Distrib. Type (distribution type) |
Material stock requests generated for stock-replenished items use the distribution type that you define in the Define Par Location component. |
ChartField Overrides |
Click to access the ChartField Overrides page, where you can update ChartField and project information at the par location header level. You can override ChartField information for specific par location lines on the Define Par Location - Line page. |
Default Quantity Option |
Select the type of quantity that you want to enter for par location counts. Define a default value on the Define Par Location - Header page; you can override this value for individual counts on the Count Par Location Levels page. Values are: Count Qty(count quantity): The quantity that is entered during the count is the quantity on hand. The Create Par Replenishment Requests process uses this value to calculate order quantity. Request Qty (request quantity): The quantity that is entered during the count is the quantity that the Create Par Replenishment Requests process should order. |
(Par Location) Sort Option |
Determines how the system sorts data (by item, compartment, or count order). You can use this sorting option for the lines that appear on the Define Par Location - Line Details page or for the Par Location Count Listing report. |
The following diagram illustrates the methods you can use to count the current stock levels within par locations. The stock levels at the par locations can be updated using a manual counting, PeopleSoft Mobile Inventory Management, file-based counting, or EIP-based counting. The Create Par Replenishment Requests process creates a material stock request for stock items, a purchase order for stockless items, and a requisition for nonstock items.
The following diagram illustrates the methods you can use to count the current stock levels within par locations.
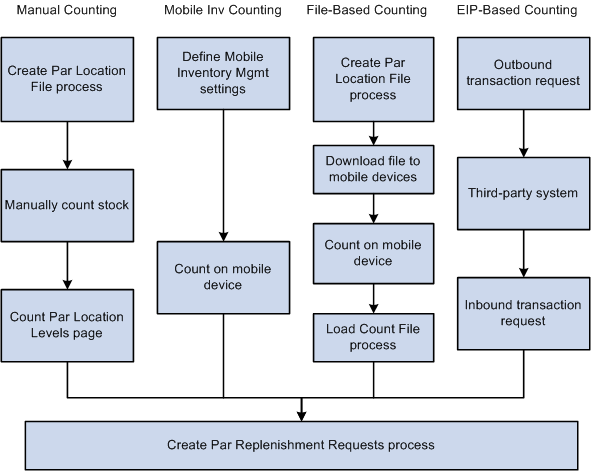
Using the Manual Counting Method
Using only PeopleSoft Inventory components and pages, you can complete a manual count of stock with your par locations. Once you have defined your par locations using the Define Par Location component, the steps include:
Print count sheets using the Create Par Location File process (INS9053).
Perform the count manually using the printed count sheets.
Enter the results into the system using the Count Par Location Levels page.
Run the Create Par Replenishment Requests process to generate orders for items that fall below optimal quantity levels. Based on your par location setup, this process replenishes the par locations using material stock requests, requisitions, or purchase orders.
Using the Mobile Inventory Counting Method
Using PeopleSoft Mobile Inventory Management in combination with PeopleSoft Inventory, you can use mobile devices to conduct periodic inventory counts to determine replenishment needs for each par location. The Mobile Inventory Management application provides tools to integrate mobile devices to the PeopleSoft Supply Chain Management system. Once you have defined your par locations using the Define Par Location component, the steps include:
In PeopleSoft, set up the Installation Options - Mobile Inventory page (Set Up Financials/Supply Chain, Install, Installation Options, Mobile Inventory) and the User Preferences - Mobile Inventory page (Set Up Financials/Supply Chain, Common Definitions, User Preferences, Define User Preferences, Mobile Inventory) to define your settings for par location counting in PeopleSoft Mobile Inventory Management.
Use your mobile devices to count the par locations. PeopleSoft Mobile Inventory Management provides two separate task flows to enter count quantities for par locations; Par Count or Par Count Ad Hoc.
In PeopleSoft Inventory, run the Create Par Replenishment Requests process to generate orders for items that fall below optimal quantity levels. Based on your par location setup, this process replenishes the par locations using material stock requests, requisitions, or purchase orders.
Using the File-Based Counting Method
Using PeopleSoft Inventory, you can create a file to download to mobile devices and then upload an updated file into PeopleSoft Inventory. Once you have defined your par locations using the Define Par Location component and have installed programs on the mobile devices to accept the file, the steps include:
In PeopleSoft Inventory, create a file of items to be counted using the Create Par Location File process (IN_CART_DNL).
Download the file to a mobile device.
Perform the count on the mobile devices.
In PeopleSoft Inventory, upload the count results into PeopleSoft using the Load Count File process (IN_CART_UPL).
In PeopleSoft Inventory, run the Create Par Replenishment Requests process to generate orders for items that fall below optimal quantity levels. Based on your par location setup, this process replenishes the par locations using material stock requests, requisitions, or purchase orders.
In this method, programs must be written on the mobile device to accept the downloaded file, operate the count procedure, and then to upload the file to a location where it is available to be processed by the Load Count File process. These programs can be developed in-house or purchased from a third-party.
Using the EIP-Based Counting Method
Using PeopleSoft Inventory and PeopleSoft Integration Broker, you can send and receive par location data with a third-party system using EIPs (Enterprise Integration Points). For example, a third-party systems can be a POU (point-of-use) supplier system. Once you have defined your par locations using the Define Par Location component and have set up the Integration Broker components, the steps include:
Use the PAR_LOCATION_SYNC service operation or the PAR_LOCATION_FULLSYNC service operation to send an outbound transaction request containing PeopleSoft Inventory's par location information. You can use the Full Data Publish process (Enterprise Components, Integration Definitions, Initiate Processes, Full Data Publish) to send the outbound transaction request.
The third-party system maintains information for each of its par location items set up in the PeopleSoft Inventory Par Location Definition component.
The third-party system uses the PAR_LOCATION_COUNT service operation to publish an inbound transaction request to PeopleSoft Inventory. This transaction request provides the PeopleSoft system with count quantities for each item in the par locations. To receive count results from your third-party system, load the PAR_LOCATION_COUNT transaction request into the PeopleSoft Integration Broker data tables and then run the Par Location Count process (RUN_INV_PAR_COUNT) within the Integration Broker (SCM Integrations, Process Transactions, Inventory, Par Location Count). Once the data is received, the PeopleSoft system updates the par location count tables.
In PeopleSoft Inventory, run the Create Par Replenishment Requests process to generate orders for items that fall below optimal quantity levels. Based on your par location setup, this process replenishes the par locations using material stock requests, requisitions, or purchase orders.
PeopleSoft Inventory offers four par location replenishment methods: stock, stockless, nonstock, and not replenished. The method that you use depends upon whether you replenish items from inventory, from PeopleSoft Purchasing, or from other par locations. The Create Par Replenishment Requests process replenishes each item according to the par replenishment option that you specified in the Define Par Location component.
The replenishment method determines how you handle general ledger accounting for par inventory. Stock replenishment transactions post to the general ledger business unit that is associated with the inventory business unit, while stockless and nonstock replenishment transactions post to the general ledger business unit that is associated with the purchasing business unit.
The following diagram illustrates the replenishment methods that you can use to restock par locations. Once a current count of the par locations have been completed, the Create Par Replenishment Requests process creates a material stock request for stock items, a purchase order for stockless items, and a requisition for nonstock items. The material stock request flows through PeopleSoft Inventory demand fulfillment. The purchase order and requisition flow through the PeopleSoft Purchasing system. The requisition created for nonstock items will require approval before a purchase order is created.
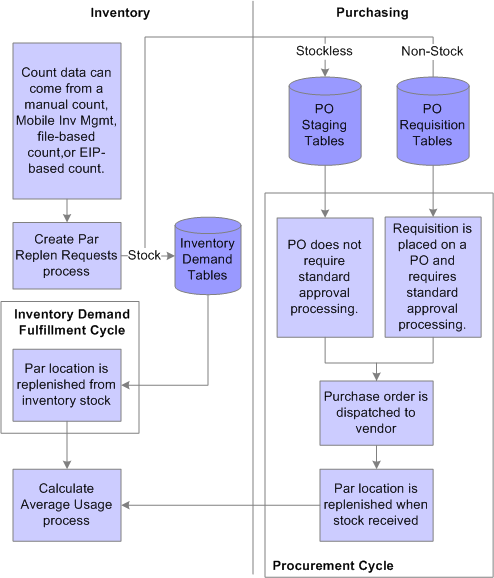
Stock Replenishment
Use stock replenishment for par location items that are part of your inventory stock and are replenished from a PeopleSoft Inventory business unit. When item quantity falls below the optimal level, the Create Par Replenishment Requests process creates a material stock request, subtracting any open on-order demand quantity from the material stock request quantity. The process does not evaluate whether sufficient stock exists to fulfill the replenishment request.
Stockless and Nonstock Replenishment
If the installation includes PeopleSoft Purchasing, you can use stockless or nonstock replenishment processing for par location items that are ordered directly through PeopleSoft Purchasing. Stockless and nonstock items might be part of the inventory stock.
The supplier supplies stockless items directly to the par location according to a previously established agreement. When item quantity falls below the optimal level, the Create Par Replenishment Requests process stages a purchase order that requires no approval processing. The process also cancels any backordered quantity that the supplier cannot supply with the first receipt; it does not, however, evaluate whether quantity exists on open purchase orders.
Nonstock items require standard purchase order approval processing. When item quantity falls below the optimal level, the Create Par Replenishment Requests process generates a requisition in PeopleSoft Purchasing. The system then subtracts from the requisition quantity any open on-order quantity that exists on a requisition or purchase order or in receiving.
Not Replenished
Use the Not Replenished option for items stored in par locations that are actual points of use for stock. Rather than running the Create Par Replenishment Requests process for such items, you restock the locations manually using items in replenished par locations. This option is useful when you want to conduct inventory counts in areas that are not true storage locations. For example, you might create a not-replenished par location for use in an operating room to ensure that all of the required instruments and surgical supplies are in place for a given surgical schedule. The system does not generate material stock requests from counts of not-replenished items.