Using Lot Trace and Lot Composition Inquiries and Reports
Page Name |
Definition Name |
Usage |
---|---|---|
Review Lot Trace/Composition - Lot Composition (inquiry) Page |
INV_LOT_COMP_INQ |
View receiving transaction history detail for a specific item-lot combination across the inventory and manufacturing business units. |
INV_LOT_COMP_POPUP |
Access associated inquiry pages where you can view additional information for the parent item-lot combination and its lot-controlled components. |
|
Lot Composition - Item Lot Information Page |
INV_LOT_COMP_SP |
View basic details about the item-lot combination on the Lot Trace/Composition - Lot Composition page. |
INV_LOT_C_CMP_SP |
View additional information about a component item-lot combination in a selected business unit. |
|
Lot Composition (report) Run Control Page |
RUN_INC5576 |
Set up run control parameters and run the Lot Composition report.
|
INV_LOT_TRACE_INQ |
View where a specific item-lot combination has been used, shipped, or issued across all of the inventory and manufacturing business units. |
|
INV_LOT_TRC_POPUP |
Access associated inquiry pages to view additional information for the component item-lot combination and for its lot-controlled parent items. |
|
Lot Trace - Item Lot Information Page |
INV_LOT_TRC_SP |
View basic details about the item-lot combination on the Lot Trace page. |
INV_LOT_T_PNT_OUT |
View the production details for all output item IDs for the parent product ID. The information that appears on this page is defined using the BOM Maintenance component in the Maintain BOMs and REVs menu. |
|
Lot Trace (report) Run Control Page |
RUN_INC5575 |
Set up run control parameters and run the Lot Trace report.
|
Lot Trace/Lot Composition Functionality
You can print reports showing the full transaction history detail.
Depending upon the installation, this feature accesses different data sources and displays data relevant to the transactions.
Note: You cannot track internal material transfers (such as bin-to-bin transfers) with the Review Lot Trace/Composition component. Use the Transaction History Inquiry page to view bin-to-bin transfers for an item-lot combination.
Lot Trace/Lot Composition in a Distribution Environment
In a standalone PeopleSoft Inventory installation, the Lot Trace/Lot Composition feature is used to track receipt, issue, and shipment activity for lot-controlled items—specifically, all supplier receipts, interunit transfer receipts, customer and internal returned material authorization (RMA) receipts, customer shipments, internal issues, interunit transfers, and return-to-vendor shipments.
Lot Trace/Lot Composition in a Manufacturing Environment
If the installation includes PeopleSoft Manufacturing, the Lot Trace/Lot Composition feature is used to track the same receipt, issue, and shipment activity as in a distribution enterprise, with additional visibility into manufacturing assembly transactions. Specific transactions include work-in-process (WIP) receipts and production ID, schedule, and kit issues, in addition to all supplier receipts, interunit transfer receipts, customer and internal RMA receipts, customer shipments, internal issues, interunit transfers, and return-to-vendor shipments.
Process manufacturing activity sometimes results in multiple outputs of by-products or co-products from a primary lot-controlled item ID. Using lot trace inquiries, you can view the production details for these multiple output IDs.
The inquiry process pulls data from the assembly's production ID and transaction history rather than from the bill of materials (BOM) to ensure the most accurate, up-to-date transaction information.
Lot Trace/Lot Composition Search
After you enter the required criteria on either of the inquiry pages and click the Search button, the system populates both the Lot Composition and Lot Trace page grids with relevant data, in effect performing a concurrent lot composition and lot trace inquiry. As with other searches performed in PeopleSoft Inventory, the system populates both inquiry pages with uniform data matching the search criteria. However, the search capabilities of this component enable you to populate the pages with different data.
The lot trace and lot composition inquiries search up or down one level at a time. To drill deeper into the item's composition or its movement, perform another search. You have two choices at this point:
Edit the search at any time by changing the values in the SetID, Item ID, Lot ID, and As of Date/Time fields in either page header and then click the Search button.
On the Review Lot Trace/Composition - Lot Composition page, you can perform a separate lot trace by moving to the Lot Trace page and editing the search criteria in the header section. This discards only the results from any previous Lot Trace searches and populates the Lot Trace inquiry page with new data. The same is true in the reverse (on the Lot Trace page, you can perform a separate lot composition trace).
Perform an independent lot trace inquiry when you click the value in the Parent Lot ID column on the Lot Trace - Production Parent page.
The results of the first lot trace inquiry are replaced with data reflecting where the item was used; the results from the first lot composition inquiry remain unchanged. Similarly, you can perform an independent lot composition inquiry when you click the value in the Comp Lot ID (component lot ID) column on the Lot Composition - Production page.
Blank fields in the grid indicate that the column attributes are not relevant to the transaction. If a search cannot return any data to either page in the component to fulfill the request, the system displays this message: Sorry, No Records Found.
Field or Control |
Description |
---|---|
Expiration Date |
Expiration date for the item-lot combination. |
From Date and To Date |
Range of dates for the transactions that you want to view. The system returns all transactions between these dates. |
Lot ID |
The ID assigned to the item on the Lot Control Information page. The lot's description appears beneath its ID. |
Purchase Lot |
The ID that the original manufacturer or supplier assigned to an item. This field only pertains to purchased item-lot combinations. |
Qty Available (quantity available) |
The quantity available to be picked in the business unit. |
Retest Date |
The lot retesting date defined on the Lot Control Information page. |
Source Code |
The source of the item (Make, Buy, or Floor Stock), which you established on the Define Business Unit Item - Manufacturing: General page in the Maintaining Items menu. |
Status |
The item-lot status assigned on the Lot Control Information page. |
Transaction Group |
The data source for the lot trace or lot composition inquiry. |
Transfer |
Click the button next to the Item ID field to access the Item Search Criteria page, where you can perform a more detailed item search. Click the button in a specific row in the grid to access other pages where you can view additional information for the item-lot combination. |
Use the Review Lot Trace/Composition - Lot Composition (inquiry) page (INV_LOT_COMP_INQ) to view receiving transaction history detail for a specific item-lot combination across the inventory and manufacturing business units.
Navigation:
This example illustrates the fields and controls on the Review Lot Trace/Composition - Lot Composition inquiry page. You can find definitions for the fields and controls later on this page.
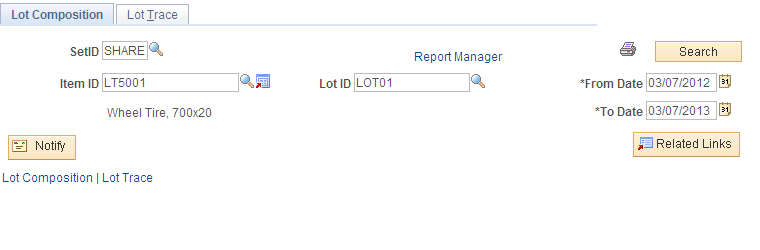
If the installation includes PeopleSoft Manufacturing, the components that make up a specific lot-controlled assembly item appear.
The grids display data from all of the receipts across your enterprise, including stocking transactions generated by purchasing receipts, interunit transfer receipts, RMA receipts, manufacturing production ID and completions, and WIP receipts.
If a search from this page returns data that includes lot-controlled components, you can click the component's lot ID link to access the Lot Trace page (without losing the original lot composition search results) and perform a concurrent lot trace search that displays one level of parent item information. The Lot Trace page is populated with parent item data for the lot-controlled component. To return to the original composition search results, select the Lot Composition tab or click the Lot Composition link. Alternatively, you can perform a lot composition search for another item-lot combination row, and the previous search results are discarded.
The transaction group name appears for each tab on this page.
Transaction |
Transaction Group |
---|---|
Receipt to Inspection |
010 |
Putaway |
020 |
Receipts from Production |
021 |
IBU Transfer Receipts |
022 |
Customer Returns |
024 |
InterCompany Receipts |
025 |
Field or Control |
Description |
---|---|
Production ID |
Identifies a specific production or work order for production tracking purposes or for managing discrete orders or batches. This identifier appears if the component was manufactured or assembled using PeopleSoft Manufacturing. Note: When an item is manufactured or assembled using a production schedule (rather than a production ID), the Production ID field is blank. Adjustments made to a component list for a given production ID after the completion process has run are not included in the lot composition inquiry's search results. |
Production Area, Prdn DueDt (production due date), and Prdn Due Shift (production due shift) |
Use to identify production completed on a schedule rather than on a production ID. |
From Production ID |
Indicates that system routed the production ID from another production ID rather than taking it from inventory. |
Component ID |
Indicates that the item is a component and might be used to build other parent items; perform a lot trace inquiry on the component to determine any additional where used locations. A blank field indicates that the parent item was received (not produced as a result of a production ID or schedule). |
Description |
Appears by default from the Define Item - General: Common page. A blank field indicates an end item; its description appears in the header. |
Comp Lot ID (component lot ID) |
Appears for lot-controlled items that are also components of a parent item. Click the value in this column to perform a lot trace inquiry for the component lot ID. |
Comp Qty (component quantity) |
The number of components used in each parent item. |
UOM (unit of measure) |
The UOM for the component quantity. |
Source Bus Unit (source business unit) and InterUnit ID |
Appears if the receipt is the result of an interunit transfer. |
RMA No (return material authorization number) and RMA Line No |
Display receipt information if the item is a return item. |
Use the Lot Composition Transfer page (INV_LOT_COMP_POPUP) to access associated inquiry pages where you can view additional information for the parent item-lot combination and its lot-controlled components.
Navigation:
Click the Page Links button on the Review Lot Trace/Composition - Lot Composition page.
This example illustrates the fields and controls on the Lot Composition Transfer page. You can find definitions for the fields and controls later on this page.
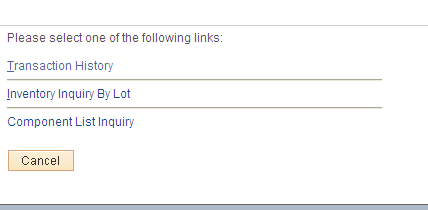
Primary Access Links
These links return information relating to the parent item for which you are searching on the header of the Review Lot Trace/Composition - Lot Composition page or relating to the component item in the grid, depending on which link you click.
Field or Control |
Description |
---|---|
Item Lot Information |
Click to access the Lot Composition - Item Lot Information page to view additional information about a lot-controlled parent item in a selected business unit. |
Component Lot Information |
Click to access the Component Lot Information page, where you can view detailed information about the component item-lot combination in a selected business unit. The Component Lot Information page is only available if the row being selected has a component listed with a lot ID. |
Navigational Links
Field or Control |
Description |
---|---|
Inventory Inquiry by Lot |
Click to access the Inventory Inquiry by Lot page to view current inventory information by component item and lot. |
Component List Inquiry |
Click to access the Production Selection page to view component list details for the production ID or schedule. |
Transaction History |
Click to access the Transaction History inquiry page to view all inventory transactions for the lot-controlled component item at the business unit level. |
Use the Component Lot Information (inquiry) page (INV_LOT_C_CMP_SP) to view additional information about a component item-lot combination in a selected business unit.
Navigation:
Click the Page Links button on the Review Lot Trace/Composition - Lot Composition page, and then click the Component Lot Information link on the Lot Composition Transfer page.
Note: This page displays information for lot-controlled component items. If the component item in the grid is not lot controlled, only the business unit, item ID, and description appear. If the row does not have a component ID (indicating the inquiry item was received and not produced), only the business unit appears.
Use the Review Lot Trace/Composition- Lot Trace (inquiry) page (INV_LOT_TRACE_INQ) to view where a specific item-lot combination has been used, shipped, or issued across all of the inventory and manufacturing business units.
Navigation:
This example illustrates the fields and controls on the Review Lot Trace/Composition - Lot Trace inquiry page. You can find definitions for the fields and controls later on this page.
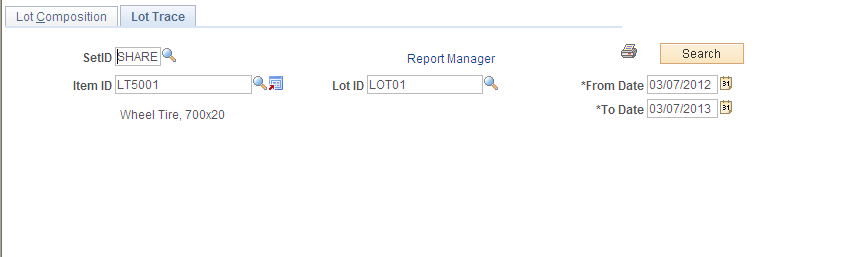
If the installation includes PeopleSoft Manufacturing, you can display the parent item information for a specific lot-controlled component item.
The grid displays data from all of the inventory shipment and issue transactions across your enterprise, including; customer, interunit, VMI, work order, and return-to-vendor shipments, plus material issued to the shop floor.
If a search from this page returns data that includes lot-controlled parent items, you can click the parent's lot ID link to access the Review Lot Trace/Composition - Lot Composition page (without losing the original lot trace search results) and perform a concurrent lot composition search that displays one level of component item information. The Lot Composition page is populated with component item data for the lot-controlled parent item. To return to the original lot trace search results, select the Lot Trace tab or click the Lot Trace link. Alternatively, you can perform a new lot trace search for another item-lot combination row and the system discards the previous search results.
The transaction group name appears for each tab on this page. The following table lists which transaction groups are included as data sources for lot trace inquiries:
Transaction |
Transaction Group |
---|---|
Return to Vendor |
012 |
Return to Vendor From Inspection |
013 |
Usages & Shipments |
030 |
InterBU Transfer Shipments |
031 |
Ship on Behalf of Other BU |
034 |
InterCompany Transfers |
035 |
VMI Interunit shipment |
037 |
Component Kit |
220 |
Component Consumption |
230 |
Work Order Usage |
231 |
Field or Control |
Description |
---|---|
Production ID |
Identifies a specific production or work order for production tracking purposes or for managing discrete orders or batches. This ID appears if the component is manufactured or assembled using PeopleSoft Manufacturing. |
To Production ID |
Indicates that the production ID was routed to another production ID rather than being put away into inventory. |
Multi O/P Flg (multiple output flag) |
Indicates that the component item that you are tracing has either a co-product or a by-product associated with it. You can view further details when you click the Transfer button on the same line to access the Lot Trace Transfer page, where you can access the Multiple Output Information page. |
Note: When an item is manufactured or assembled using a production schedule (rather than a production ID), the Production ID field is blank. Adjustments made to a component list for a given production ID after the completion process has run are not included in the lot trace inquiry's search results.
Note: When a component is part of a multiple output for a parent production ID, the quantity for the parent production ID reflects the total quantity output related to the component. To view the actual breakdown of item output quantities, use the Multiple Output Item Lot Detail page.
Field or Control |
Description |
---|---|
Parent Item ID |
Populated when the item-lot combination for which you searched is a component, indicating another level for inquiry. |
Parent Lot ID |
Lot-controlled items that are also parent item assemblies display a parent lot ID. Click the value in this column to perform a lot composition inquiry for the parent lot ID. |
Parent/Routed Quantity |
The number of parent items completed. |
UOM |
The UOM for the parent item completions. |
Use the Lot Trace Transfer page (INV_LOT_TRC_POPUP) to access associated inquiry pages to view additional information for the component item-lot combination and for its lot-controlled parent items.
Navigation:
Click the Page Links button on the Review Lot Trace/Composition - Lot Trace page.
This example illustrates the fields and controls on the Lot Trace Transfer page. You can find definitions for the fields and controls later on this page.
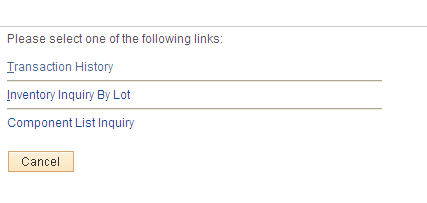
Primary Access Links
Field or Control |
Description |
---|---|
Item Lot Information |
Click this link to access the Lot Trace - Item Lot Information page, where you can view basic information for the lot-controlled parent or end item in a selected business unit. Lot trace functionality searches up one level at a time, when you are tracing where a component is used or shipped, you are viewing its end-use or parent-item details—no further component information is visible at this level. |
Parent Lot Information |
Click to access the Parent Lot Information page to view more information about a lot-controlled parent item in a selected business unit. |
Multiple Output Information |
Click to access the Multiple Output Information page to view production details for all output for the production ID. |
Navigation Links
Field or Control |
Description |
---|---|
Inventory Inquiry by Lot |
Click to access the Inventory Inquiry by Lot page to view current inventory information by parent item and lot. |
Component List Inquiry |
Click to access the Production Selection page to view component list details for the parent item-lot combination. |
Output List Inquiry |
Click to access the Displaying Production Output Mix Information page to view output list details for the production ID. |
Transaction History |
Click to access the Transaction History inquiry page to view all inventory transactions for the lot-controlled parent item at the business unit level. |
Access the Parent Lot Information page (Click the Parent Lot Information link on the Lot Trace Transfer page).
Note: This page displays information for lot-controlled parent items. If the parent item in the grid is not lot controlled, only the business unit, item ID, and description appear. If the row does not have a parent ID (indicating the inquiry item is an end item), only the business unit appears.
Use the Multiple Output Information page (INV_LOT_T_PNT_OUT) to view the production details for all output item IDs for the parent product ID.
The information that appears on this page is defined using the BOM Maintenance component in the Maintain BOMs and REVs menu.
Navigation:
Click the Page Links button on the Review Lot Trace/Composition - Lot Trace page and then click the Multiple Output Information link on the Lot Trace Transfer page.
Field or Control |
Description |
---|---|
Output Type |
A multiple output item type can be either a co-product or a recycle or waste by-product. |
Output Item |
The output item ID. |
Op Seq (operations sequence) |
The operations sequence number for the by-product item. This field is blank for co-product items, which can only be completed at the last operation. |
Output Quantity |
The quantity of the multiple output item produced for the primary output (parent item-lot combination). |
Per |
The quantity produced per assembly or order. This is for by-products only. |
Output Schd Qty (output scheduled quantity) |
The output scheduled quantity for the multiple output item. |
Qty Compl to Date (quantity completed to date) |
The total batch quantity completed against the co-products. |
Res % (resource allocation percentage) |
Determines how much of the batch quantity each co-product represents. |