Creating Production Schedules
After fine-tuning the production plan, you may need to use the Production Schedule pages to manually enter or maintain production that you want to track by day and shift.
Important! Both production IDs and production schedules can be created and maintained by using these pages.
Production schedules can be created and maintained for each production area and item combination. You can add a schedule for production quantities that are in the Entered status at the summary level. Because you define production quantities due on a specific production due date and shift, production schedules are always backward scheduled. You also can maintain multiple production schedules per shift, and you can set the due time as well as the due date.
Note: You cannot use production schedules to track rework, teardown production, or regular production using the kit issue method. Rework BOMs and routings and teardown routings are not available for production schedules.
When you change any information on an existing production schedule, you can have the system send the Production ID Change workflow notification to selected roles that you define. These roles might include a planner or buyer or a production control manager.
This section lists common element and discusses how to Create Production Schedules:
Page Name |
Definition Name |
Usage |
---|---|---|
SF_PA_SCH_SUMMARY |
Define and maintain production schedules. Add production IDs, or add, modify, and view all production for a specific production area. |
|
Total by Production Area, Shift Page |
SF_PA_SCH_SHIFT |
View the schedule quantity by shift due for each day of the week. |
SF_PA_SCH_DT_MAINT |
View details for a production schedule or production ID. Add production IDs, modify, or view details for all production in a specific production area. You must define at least one production schedule or production ID before you can access this page. |
|
Production by Area |
SF_PA_SCH_SUM_INQ |
View all production in a specific production area. Define at least one production schedule or production ID. |
SF_SCH_OUTPUT_LIST |
View or add production output information. |
|
Production Selection Page |
SF_PRDN_ITEM_SEL |
Access production, rework, and teardown information for a specific item. View production IDs, production schedules, or a combination of both. Define at least one production ID or production schedule for an item. |
Production List Page |
SF_PRDNID_ITEM_VW |
Access production information for a specific production schedule. Use this page to see the status of all production for a production area at the operation level. Define at least one production schedule for an item. |
Production for an Item - Production Detail Page |
SF_PRDNINQ_STATIC |
Display production, rework, or teardown details associated with any production ID displayed on the Production for an Area/Item inquiry page. |
Operation Detail Page |
SF_PRDN_DATA_DTL |
View operation list details. |
Production Item Output |
SF_PRDID_ITEM_OUT |
View output information for a specific item. Define at least one production ID or production schedule for an item. |
Production Text |
SF_PRDNINQ_PRTXT |
View text associated with any production schedule or production ID. |
Production Inquiry - Production Selection |
SF_PRDN_SELECTION |
Define production criteria for the production inquiry. |
Production Inquiry |
SF_PRDN_MAINT_INQ |
View production information for a particular production schedule or production ID. Enter production information on the Production Selection page before accessing this page. |
Production Detail Inquiry |
SF_PRDN_STAT_INQ |
View additional details for selected production. |
Production for an Item - Production Item List |
SF_PRDNID_ITEM_VW |
View a production summary for a selected item. |
Production Output |
SF_PRDN_OUTPUT_INQ |
View output information for production IDs or production schedules. Enter production information on the Production Selection page before accessing this page. |
Production Text Inquiry |
SF_PRDN_TEXT_INQ |
View text associated with the selected production. |
Production Output Mix Inquiry - Production Selection |
SF_COMP_OUT_SEL |
Enter the search criteria for the production schedule whose component and output data that you want to display. Define at least one production schedule or production ID with multiple outputs. |
Prdn Op Summary (production operation summary) |
SF_COMP_OUT_SUM |
View production operation sequence summary data at a summary level, including task and work center information. Enter search criteria in the Production Output Mix Selection page to see data that appears in this inquiry. |
Prdn Output/Component Details |
SF_COMP_OUT_DTL |
View specific production component and output ID data by operation sequence at a detail level. Enter production information on the Production Selection page before accessing this page. |
Production History |
SF_TRANSHIST |
View production transaction history. |
Production History Details |
SF_TXN_HIST_SP |
View transaction history details based on the selection criteria such as Completions Detail, Consumption Detail, or Operation Detail. |
Production Schedule by Area Report |
RUN_SFS2007 |
View total quantities, by item, produced each day for each repetitive production area. |
Field or Control |
Description |
---|---|
Frozen |
Select to freeze this production schedule in the PeopleSoft Supply Planning system. |
Frozen Sub (frozen substitutes) |
Select to freeze substitutes in the PeopleSoft Supply Planning system. When you send the production schedule to PeopleSoft Supply Planning, the Planning engine does not include substitute components. |
Revision |
Select if you want to use alternate revisions for the item if the item is revision-controlled. |
Use the Production by Area Summary page (SF_PA_SCH_SUMMARY) to define and maintain production schedules.
Add production IDs, or add, modify, and view all production for a specific production area.
Navigation:
This example illustrates the fields and controls on the Production by Area Summary page. You can find definitions for the fields and controls later on this page.
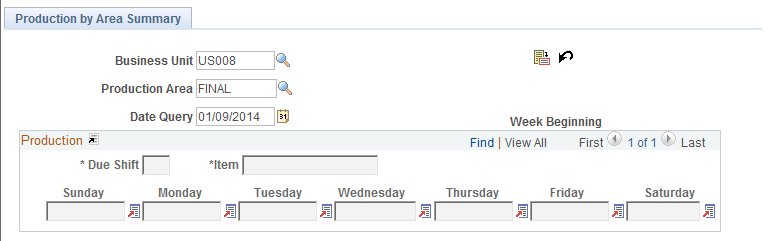
Field or Control |
Description |
---|---|
Date Query |
Enter the production due date to add or view production for the appropriate workweek. After you enter a date, the system displays the corresponding day of the week. |
|
Click the Fetch button to retrieve the production information, to add a new production schedule or production ID, or to make changes to existing production. |
Due Shift (production due shift) |
The system displays the shift when the production start quantity will be completed. The system also displays the schedule quantity due for each day of the week. |
|
Click the Production Detail button to select one of these links:
|
|
Click Insert to add a production quantity for an item in the selected area. Note: Click the Insert Row button to enter a row on this page. To delete a production start or production end quantity, use the Production by Area Details page. |
|
Click the Reset Selection button to clear the information that appears in the grid and select a new area or date. |
Due Shift |
Enter a production due shift for the item and scheduled quantity. |
Item |
Enter an item value. You can maintain production quantities for items that are manufactured using either production schedules or IDs. The only restriction is that the item must be defined for the production area selected. Once you save the information, you cannot change the item; you can only delete the schedule. |
Note: When adding an assembly with item status of Hold, you will receive a warning message. The warning message does not prevent you from performing the action. The system also gives you the option to cancel at save time.
Production Quantity
Enter the quantity on the day the week that you want the production to be completed. If you have specified a rate quantity per shift for the area and item, you can view and select that rate by clicking the down arrow in the appropriate day column. For example, the day that you choose for the quantity is the production due date. Whether you can enter a whole number or a decimal may depend on the item's unit of measure and quantity precision combination defined in PeopleSoft Inventory. For example, suppose that item ID A0007 has a unit of measure of EA and a natural round, whole number combination. Then you can only enter whole numbers. If you enter an incorrect number format, you receive an error message.
The system automatically calculates the production start date and shift as well as the actual start date and time and actual due date and time once you click the Process button. In addition, when you enter a quantity for a day:
The system adds the quantity on the date corresponding to the day of the week in which the quantity was entered.
The time is set to the last hour of operation for the last work center on the item's routing.
If you're using operation yield, the system calculates the production start quantity based on the production end quantity.
Because production schedules are always backward scheduled, you enter the production end quantity.
You can change the due time at the production detail level.
Field or Control |
Description |
---|---|
|
Click the Production Detail button next to the Quantity field on the day of the week that you want to change. Click the Detail link to complete the transfer. |
Important! You must click the Process button to save the schedule before you can access the Detail page.
You can change the due time for the scheduled production from the Detail page. You can define and maintain multiple production quantities, each with a different due time.
All changes to quantities for a day must be done at the production detail level.
You cannot delete production quantities in the Production by Area Summary page. Navigate to the Production by Area Details page to delete quantities.
If a routing is not defined for the item and you've entered a quantity for a shift and a day on this page, you must define the production start date and production start shift on the Production by Area Details page. The system automatically changes the due time to the last hour of operation based on the production calendar. The start date and shift automatically changes to the due date and shift. The time automatically changes to the first hour of operation based on the production calendar. You can change the actual start date and time within the production start shift as well as the actual due time within the production due shift.
The system displays production due shift options based on these scenarios:
The system uses the work center calendar for the routing's last operation, if one exists.
If a work center calendar does not exist for the routing's last operation's work center, the system uses the production calendar, if one exists.
If a production calendar does not exist, the shift for the five-day work week is available.
If you are adding production on the summary page, they are added in the Entered status. Access the Detail page to change the status or add production in the Firmed or Released statuses.
Click the Process button to save the production schedule or production ID. The system then calculates the production start date, time, and shift.
Note: If capacity and material availability are concerns, estimate the production start and production due dates and shifts when you create or maintain production using PeopleSoft Manufacturing, and then schedule the production schedule's or production ID's production start and production due dates and shifts using PeopleSoft Supply Planning.
The Process button uses Remote Call for three-tier processing. Remote Call is a PeopleCode API function that provides a means of calling a Tuxedo service from a PeopleSoft application. A typical use of Remote Call is to run data-intensive, performance-sensitive programs near or on the database server. If you experience a time-out or other error when adding or changing production information, use the Reschedule Production process (SFPCRSCH).
Production Status Change and Effects
If you are changing production information, the production status determines what changes you can make:
Production Status and Action |
System |
---|---|
If production is in the In Process status and you increase or decrease the order quantity on the Detail page. |
Adjusts the component scheduled quantities to reflect the new order quantity and marks the production as changed so that the Planning Engine reschedules the operations during the next planning run. |
If production is in the Released status and you change production information such as due time or production quantity on the detail page. |
Updates the component list and operation list with the new information. |
If production is in the Firmed status and a routing is specified. |
Recalculates the production start date and production start shift. The actual start date and time and due date and time are also recalculated. |
See the product documentation for PeopleTools: PeopleCode Language Reference
Use the Production by Area Details page (SF_PA_SCH_DT_MAINT) to view details for a production schedule or production ID.
Add production IDs, modify, or view details for all production in a specific production area.
Navigation:
Click the Production Detail button and select the Details link.
Click the Production Detail button and select the Details link.
This example illustrates the fields and controls on the Production by Area Details page. You can find definitions for the fields and controls later on this page.
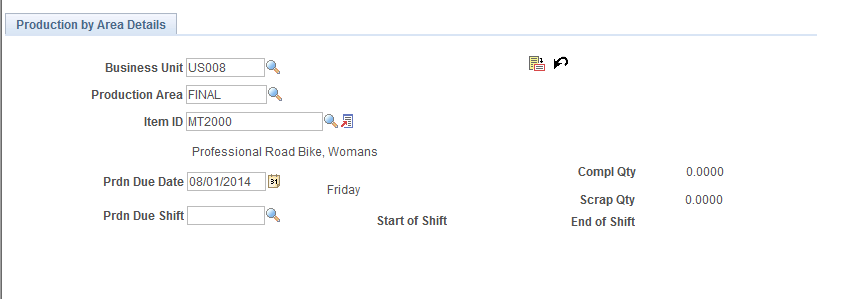
Field or Control |
Description |
---|---|
Prdn Due Date (production due date), Prdn Due Shift (production due shift), Item ID, Prdn Start Date, (production start date) and Prdn Start Shift (production start shift) |
Enter values for these fields to retrieve production information. |
Search |
Click to display the selected production information. |
Compl Qty (completed quantity) |
Indicates whether assemblies have been completed to stock or routed to another production area. |
Scrap Qty (scrapped quantity) |
Displays the number of assemblies that have been scrapped in process. |
|
Click the Insert button to add new production quantities. Each quantity that you add on the Production by Area Details page has the same business unit, production area, item ID, routing, routing item, and production due date. The system calculates the total production quantity for the production due date or on the Production by Area Summary page. You can only add production in the Entered, Firmed, and Released statuses, and you can delete Entered, Firmed, and Released schedules. |
Rtg Itm (routing item) |
Displays the referenced item's routing. The end item can either have its own unique routing or reference another item's routing. |
Due Time |
The actual due date and time when production should be completed for the given production due date and production due shift. |
Prdn Start Qty (production start quantity) |
Displays the beginning quantity at the first operation of the manufacturing process. The system will adjust this quantity to account for any operation yield. |
Prdn End Qty (production end quantity) |
Displays the quantity expected at the end of the manufacturing process. The is the production quantity that you entered in the days of the week fields on the Production Area by Summary page. |
|
Click to Output List button to access the Production Output List page. |
Production Status Change and Effects
Production Status and Action |
Effect |
---|---|
Firmed or Released |
The system recalculates the component scheduled quantities taking into account any operation yield. |
In Process and you increase or decrease the production start or production end quantity |
The system adjusts the component scheduled quantities (taking into account any operation yield) to reflect the new schedule quantity and marks the production as changed so that the Planning Engine reschedules the operations during the next planning run. |
You decreased the production quantity and have already issued components |
There might be a surplus of components at the WIP location. |
You changed the production start or production end quantity and the production is released |
The system automatically recalculates the actual start date and time taking into account any operation yield. |
Use the Production Output List page (SF_SCH_OUTPUT_LIST) to view or add production output information.
Navigation:
Click the Output List button.
Output List Tab
Field or Control |
Description |
---|---|
Output Type |
Select either Recycle or Waste by-products. Note: Teardown output items can only be used on teardown production IDs. |
Output Quantity |
Enter the production start quantity and indicate if whether this quantity is per assembly or per order. |
Note: You cannot change or add primary or co-products. However, you can change or add recycle and waste by-products.
Output Detail Tab
Field or Control |
Description |
---|---|
Output Schd Qty (output schedule quantity) |
Enter the values for the item being produced. Whether you enter a whole number or a decimal depends on the item's unit of measure and quantity precision combination defined in PeopleSoft Inventory. |
BOM and Routing codes |
Values appear and are automatically assigned from the BOM and routing code combination defined for the production area and item combination for regular production. Because BOM and routing combination effectivity dates are defined at the area and item level, the BOM and routing combination appears by default based on the combination in effect on the due date of the schedule. Therefore, you can have multiple BOM and routing combinations for the same area and item combination, and this affects completions. Note: Because production is always backward scheduled using these pages, the production due date is used to check the BOM and routing combination effectivity dates. |
Prdn Start Date (production start date), Prdn Start Shift (production start shift), and Start Time |
These fields indicate the actual date, shift, and time when production should begin, as follows:
The actual due time automatically changes to the last minute of the specified shift using the calendars associated with the last operation. The last minute for the specified shift is based on the work center's calendar for the work center associated with the last operation in the item's routing. If not, the system uses the production calendar. If a production calendar does not exist, the system uses the shift for the five-day work week. Change the due time to any valid time that falls within the production due shift specified. If the shift spans multiple dates, the system determines the actual due date based on the production due date, production due shift, and actual due time specified. |
|
Click the Process button to save changes to the production schedule. The system calculates the production start date, time, and shift. |