Understanding Recording Completions and Scrap
Within a manufacturing enterprise, you need to track end items as they make their way through the production area. With PeopleSoft Manufacturing, you can manage production by orders, repetitive schedules, backflushing, or creating a schedule to record completions and scrap after you have completed production. Subcontracted operations are fully supported. You can assign serial and lot numbers to completed end items and complete end items to containers while moving them to inventory or to another production area. While recording completed operations, the system accumulates manufacturing costs and variances. You can also record actual machine and labor hours for each production order or production schedule.
PeopleSoft Manufacturing tracks the serial genealogy of production. This enables you to trace the movement of a specific serialized assembly and its components throughout the manufacturing process.
Note: During completions, you can choose from serial IDs previously associated with a production ID, or you can enter a new serial ID for which the system automatically creates the serial association. Additionally, lot auto numbering only applies to configured orders.
PeopleSoft Manufacturing tracks the costs of material, labor, outside processing, and machines used to manufacture a product and manages the transactions necessary to report and track the status of a particular order or schedule by day and shift. The system supports these order types:
Production IDs for regular, rework, or teardown production.
Production schedules for tracking regular production by day and shift.
If you're recording completions and scrap for a production ID with subcontracted operations, you record the operation completions for the subcontracted operations slightly differently than for in-house production.
You can also record completions and scrap using electronic data collection.
See Understanding the Process of Recording Completions and Scrap Using Electronic Data Collection.
Recording Completions with Multiple Outputs
You can also record completions and scrap for production IDs and production schedules that have multiple outputs. Multiple outputs consist of:
Term |
Definition |
---|---|
primary items |
The main outputs from the manufacturing process. |
co-products |
Items, along with the primary item, that are planned for and produced as part of the manufacturing process. Co-products share the cost of the process; there may be independent demand in planning for the primary item. |
by-products |
Items that can be either waste by-products, which need to be disposed, or recycle by-products, which can be used as inputs to other processes. By-products are incidental to the process and have either a relief (negative) cost for recycle by-products or a disposal (positive) cost for waste by-products. There is typically not independent demand for by-products. |
Expected Output When Using Yield by Operation
The system recalculates the expected output quantities when over-completions or over-scrap are performed. Over-scrap is when the scrap quantity exceeds the expected scrap, based on the operation yield. For example, the system recalculates a new output quantity if the actual scrap quantity exceeds the expected scrap quantity at an operation.
Transferring Completions Data to PeopleSoft Quality
If your installation includes PeopleSoft Quality, and you have defined quality configuration information and quality plans in PeopleSoft Quality for a manufactured item and its process, then the Quality link is active on the Record Completions/Scrap page. You click this link to transfer to PeopleSoft Quality to initiate a data entry session to record quality control information for the manufacturing process.
Completions Actions and Effects to Quantities on Hand
This table lists the results of completions actions:
Completions Action |
Results |
---|---|
Recording positive completions |
Decreases the business unit's on-hand quantity of the components, and increases the business unit's on-hand quantity of the completed end item. Decreases the storage location's quantity for the components, and increases the storage location's quantity for the completed end item. Decreases the lot quantity on-hand for lot-controlled components and increases the lot quantity on-hand for the completed end item, if it is lot-controlled. |
Recording negative completions |
Increases the business unit's on-hand quantity of the components, and decreases the business unit's on-hand quantity of the end item. Increases the storage location's quantity for the components, and decreases the storage location's quantity for the end item. Increases the lot quantity on-hand for lot-controlled components and decreases the lot quantity on-hand for the end item, if it is lot-controlled. |
Recording completions to a non-WIP, nettable location |
Increases the business unit's quantity available for the completed end item. |
Recording negative completions to a non-WIP, nettable location |
Decreases the business unit's quantity available for the end item, if the end item comes from a nettable, available, non-WIP location. |
Recording positive completions to a nettable, available WIP location |
Increases a business unit's quantity reserved for the completed end item. |
Recording negative completions from a nettable, available WIP location |
Decreases a business unit's quantity reserved for the end item. Decreases the lot quantity available for the completed end item. |
You can manage discrete orders for regular, rework, or teardown production by creating production IDs for each production quantity that you want to track. Once you've created the production ID, you release production, and then either generate pick lists to issue material to production or maintain a maximum quantity on hand for components in a WIP location.
Once production begins on the shop floor, perform the following steps. These steps assume that all operations are performed in-house and none of the operations are subcontracted.
To record completions and scrap for in-house production IDs:
Indicate whether the business unit will record completions and scrap production IDs using the online or deferred method by selecting the PID Completion option on the MFG BU Prdn Options page. Select one of these:
Online: The background process calculates the associated production costs (such as earned labor and machine hours) and overhead conversion costs and consumes material utilizing the issue or replenishment issue methods.
Deferred: This option indicates that you're running the completions process at a later time.
All associated production costs are calculated when the completions update background process is run. You must run the Prdn Compl/Scrap process (production completions and scrap process) if you select this option.
Record completions and scrap quantities for in-house production using the Record Completions/Scrap page.
Record completions by operation, by count point, or for the entire production quantity, or perform a partial backflush of completed end items.
(Optional) If you're completing a production ID with multiple outputs, the Outputs Detail area appears.
You can complete planned or unplanned by-products at any operation. Scrapped end items are recorded at the batch level, but not for each output. You must record completions and scrap for primary items and co-products at the last operation.
(Optional) Change component information using the Edit/Issue Components page.
(Optional) Transfer completions data to PeopleSoft Quality by clicking the Quality link.
(Optional) If you're using serial in production or serial- or lot-controlled items, and the components are issued to production using the Replenish or Issue method, select the serialized components or lots from which to consume the components.
Automatically generate serial numbers by using the Rapid Serial Numbers page.
Access the Edit/Issue Express page, or click the button next to the serial- or lot-controlled component on the Edit/Issue Components Summary page. For lot-controlled components you can use the backflush lot selection rule to automatically select lot IDs during backflush. For more information on the backflush lot selection rule, see the "Automatically Consuming Lot-Controlled Stock During a Backflush" section of this topic.
Use the Route-To PID/Stor Locations (route to production ID and storage locations) scroll area on the Record Completions/Scrap page to assign a lot if the completed end item is lot-controlled.
Note: You can move end items to an existing lot or create a new lot.
Move completed end items out of production.
You may route them to a production ID, to another production area for further processing, or to a stores inventory location. You cannot route waste by-products.
(Optional) Click the Apply Defaults link to route the end items to a default putaway location.
Note: The completions process puts away items in their standard units of measure (UOM).
(Optional) Select an alternate putaway location.
Note: If you're routing the end item to another production ID, the putaway process is not required.
If you are using serial genealogy, you must perform completions at the last operation.
In addition, select the serial number for the appropriate assembly.
(Optional) Run the Completions Update process.
You run this process to update completions transactions that are staged by other processes, such as Edit Components updates, production completions, or subcontracted completions recorded through electronic data collection.
(Optional) Make reversing entries to correct data entry errors.
You can return components to their original storage location or to an alternate location. If you're returning lot- or serial-controlled components, you must select the serial IDs or lot IDs from which the components were originally consumed.
(Optional) Move excess components out of WIP locations using the Maintain Inventory navigation.
You can move these components to another production area or back to a stores inventory location. You can also move excess components from the production ID using the Kit issues transactions. Kit issue transactions are used for components whose issue method is Kit.
Record actual labor and machine hours.
Indicate that production is complete by using the Complete Production page.
PeopleSoft Manufacturing generates a schedule for processing by day and shift for regular production by:
Creating a production schedule as part of the supply planning process.
Creating a production schedule at the end of a production run.
Note: Production schedules support in-house production only. If you have subcontracted operations on a routing, you must use a production ID to track production.
Once you've created the production schedule, you release production, and then either generate pick lists to issue material to production or maintain a maximum quantity on hand for components in a WIP location.
If a production schedule has not been created, you can still record completions. At that time, the system prompts you to automatically add the production quantity to the schedule.
To record completions and scrap for production schedules:
Record completions and scrap quantities for production schedules using the Record Completions/Scrap page.
Record completions and scrap for the entire production quantity, or perform a partial backflush of completed end items. You can record completions for production schedules with multiple outputs. However, all multiple outputs and scrap must be completed at the last operation.
Note: If a schedule for the production date and shift has not been created when recording end item completions and scrap, the system creates a production schedule and releases production.
(Optional) If you're completing a production schedule with multiple outputs, the Outputs Detail area appears.
You can add unplanned by-products. Scrapped end items are recorded at the batch level, but not for each output.
(Optional) Change component information using the Edit/Issue Components page.
(Optional) Transfer completions data to PeopleSoft Quality by clicking the Quality link.
(Optional) If you're using serial- or lot-controlled items, and the components are issued to production using the Replenish or Issue method, you must select the serialized components or lots from which to consume the components.
Automatically generate serial numbers by using the Rapid Serial Numbers page.
Access the Edit/Issue Express page, or click the button next to the serial- or lot-controlled component on the Edit/Issue Components Summary page. For lot-controlled components you can use the backflush lot selection rule to automatically select lot IDs during backflush. For more information on the backflush lot selection rule, see the "Automatically Consuming Lot-Controlled Stock During a Backflush" section of this topic.
Use the Route-To PID/Stor Locations scroll area on the Record Completions/Scrap page to assign a lot if the completed end item is lot-controlled.
Note: You can move end items to an existing lot or create a new lot.
Move completed end items out of production.
You may route them to a production ID, to another production area for further processing, or to a stores inventory location. You cannot route waste by-products.
(Optional) Click the Apply Defaults link to route the end items to a default putaway location.
Note: The completions process puts away items in their standard UOMs.
(Optional) Select an alternate putaway location.
Note: If you're routing the end item to another production ID, the putaway process is not required.
(Optional) Run the Completions Update process.
You run this process to update completions transactions that are staged by other processes, such as Edit Components updates, production completions, or subcontracted completions recorded through electronic data collection.
(Optional) Make reversing entries to correct data entry errors.
You can return components to their original storage location or to an alternate location. If you're returning lot- or serial-controlled components, you must select the serial IDs or lot IDs from which the components were originally consumed.
(Optional) Move excess components out of WIP locations using the Maintain Inventory navigation.
You can move these components to another production area or back to a stores inventory location.
Record actual labor and machine hours.
Run the Close Production SQR process to indicate that the production schedules are complete.
Backflush is a method of consuming components for a production ID or production schedule. The system backflushes components with an issue method of Issue or Replenish. Typically, backflushing occurs when completion or scrap quantity is entered for an assembly. Backflushing consumes material from the WIP locations.
When consuming lot-controlled components, the backflushing process must decide which lot IDs to choose within the WIP location. The backflush lot selection rule enables you to determine which lot IDs are automatically selected for consumption when a backflush is performed. The backflush lot selection rule can be defined at:
The business unit-level using the MFG BU Prnd Options page. The options for the backflush lot selection rule are located in the Backflush Lot Option group box and include:
Manual:(default) Select this option to require the user to enter the specific lot IDs consumed during backflushing. The system does not automatically select any lot IDs.
Earliest Expiration Date: Select this option to have the system select the lot IDs for consumption based on the lot expiration date. The system first selects the lots with the earliest expiration dates.
Earliest Available Date: Select this option to have the system select the lot IDs for consumption based on the available date. The system first selects the lots with the earliest available dates.
The business unit and item-level using the Define Business Unit Item - Manufacturing: General page. The options for the backflush lot selection rule are located in the Backflush Lot Option group box and include:
Default from BU: (default) Select to use the backflush lot selection rule defined at the manufacturing business unit level on the MFG BU Prnd Options page.
Manual
Earliest Expiration Date
Earliest Available Date
The backflush lot selection rule defined at the business unit and item combination (the Define Business Unit Item - Manufacturing: General page) overrides the option selected at the business unit level (the MFG BU Prnd Options page).
See Define Business Unit Item - Manufacturing: General Page.
How the Backflush Process Uses the Backflush Lot Selection Rule
The backflush lot selection rule is used during the backflush process to determine the lots to consume from each WIP location for lot-controlled components. The Record Completions and Scrap-Edit/Issue Express page is one location where you can see some of the impacted fields:
This example illustrates the fields and controls on the The Record Completions and Scrap-Edit/Issue Express page. You can find definitions for the fields and controls later on this page.
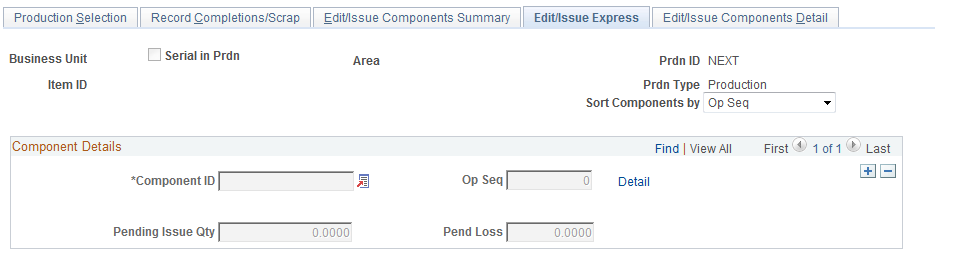
If the backflush lot selection rule is Manual, then the backflush process does not default lot IDs. You must manually enter the specific lot IDs and the quantity from each lot for consumed lot-controlled components.
If the backflush lot selection rule is Earliest Expiration Date or Earliest Available Date, then the backflush process consumes lot-controlled components by choosing the lot IDs and quantities from each lot ID within the WIP locations. The following rules are applied:
The backflush process does not override an existing lot entry but populates any blank fields or default-value fields.
The process can select one or more lots. For example, if 15 units are needed, the first 8 units are selected from lot L200, when this lot is exhausted then the last 7 units are selected from lot L500.
The process consumes lot-controlled stock until the consumed component is satisfied or the existing stock in the WIP location is exhausted. If there is not enough lot quantity in the WIP location, then the process leaves the remaining quantity in the pending issue quantity and pending loss quantity, as appropriate.
If the rule finds multiple lots in the WIP location that could be used, then the first tiebreaker is the opposite date (that is, the Earliest Expiration Date rule uses the earliest available date and the Earliest Available Date rule uses the earliest expiration date). If there still are multiple lots, then the next tiebreaker is the ascending lot ID value.
For consigned items, the process uses the stock in the owned WIP location. If more quantity is needed, then the non-owned WIP location is used.
The backflush lot selection rule cannot be applied to:
Items that are both lot-controlled and serial-controlled.
Items using serial genealogy.
Items that has the component issue method of Kit.
For these items, the backflush lot selection rule is set to the value of Manual.
Components Impacted by the Backflush Lot Selection Rule
The backflush lot selection rule is applied during backflush and impacts the following components:
Record Completions and Scrap (Production Control, Process Production, Complete Production, Record Completions and Scrap).
Edit/Issues Components (Production Control, Process Production, Issue Materials, Edit/Issue Components).
Receive Subcontract Assembly (Production Control, Process Production, Subcontract Production, Receive Subcontract Assembly).
The above components can be used in online or deferred mode. If you are using the online mode (PID Completion Option on the MFG BU Prdn Options page), the online pages display the results of the backflush lot selection rule; that is, the lot ID and quantity to be consumed from the WIP location. You can view and override the selected lot IDs and quantities. If you are using the deferred mode (PID Completion Option on the MFG BU Prdn Options page), the system does not consume the components until later; however, you can use the online pages to enter override lot IDs and quantities.
Using the online mode, if the backflush process has completed and then a field is changed that causes the pending quantities field to be recalculated, this causes a recalculation of backflush lot selection rule. Fields that trigger the recalculation of the pending quantities include:
Completion Quantity
Scrap Quantity
Completion Op Sequence
Back thru Op Sequence
Component ID
Component's Op Sequence
Component's Qty Code
Component's Qty Per
Picking a substitute item
In addition, entering a pending issue quantity or a pending yield loss quantity when there is no completion or scrap quantity triggers the calculation of the backflush lot selection rule. If the lot consumption fields have already been populated and then you manually change the pending issue quantity or a pending yield loss quantity, the system displays the following message:
Message Text: Recalculate the Lot IDs to consume (Y/N)?
Explanation: You have modified the pending issue or pending loss quantity for a component that contains values in its lot scroll. Select Yes to clear the lot scroll and repopulate based on the entered quantity - all other occurrences of this component on the component list which share the same WIP location will also have their Lot IDs recalculated. Select No to keep the pending quantity entered without changing the lot scroll - you will then need to modify the lot scroll so that its quantities correspond with the pending quantity entered. Select Cancel to cancel the action - the original pending quantity will be restored and the lot scroll will not be modified.
Using the Production Completions and Scrap Process with the Backflush Lot Selection Rule
Prdn Compl/Scrap (SFPDCDRV) process (Production Completions and Scrap process) can perform a backflush and looks to the backflush lot selection rule to determine the method for the lot consumption from the WIP locations. This Prdn Compl/Scrap process is located in both the SCM Integrations menu (SCM Integrations, Process Transactions, Manufacturing, Process WO Completions) and the Production Control menu (Production Control, Process Production, Complete Production, Process Completions and Scrap). The Production Completions and Scrap process uses data stored in the BCT tables to update the production tables and can record completions and scrap for:
Electronic data collection files and other EIP messages. The data transactions are stored in the BCT tables.
Online components using the deferred mode (PID Completion Option on the MFG BU Prdn Options page). The online data entry is stored in the BCT tables.
If you have selected the backflush lot selection rule of Earliest Expiration Date or Earliest Available Date, then the incoming files are not required to have a lot ID for consumed components. The lot ID is assigned during the Production Completions and Scrap process; therefore, the incoming files are not put in the error status for correction in the Transaction Maintenance component (SCM Integrations, Transaction Error Handling, Maintain Transactions, Transaction Maintenance). If the incoming file does contain some lot IDs for consumed components, then the Prdn Compl/Scrap process uses those entries rather than the backflush lot selection rule. In addition, the incoming files must contain the lot IDs for consumed components if you have selected the backflush lot selection rule of Manual.
See Running the Completions Update COBOL/SQR Process (SFPDCDRV).
Setting Up the Backflush Lot Selection Rule
Before changing the backflush lot selection rule in your PeopleSoft system, you should examine the physical movement in your WIP locations to:
Verify the physical usage of the lot components in the WIP locations match the chosen backflush lot selection rule. For example, if stock with the earlier expiration date is selected first from the WIP location during production, then you should select the Earliest Expiration Date option for the backflush lot selection rule.
Ensure your data movement transactions to and from the WIP locations are accurate and promptly recorded. If you are using data collection systems for material movement or completions and edit component transactions, the batch jobs that process these transactions must be processed in a timely manner.
Confirm that you have one primary method for entering completion transactions. If you vary the method used to record completions, (for example; sometimes using data collection completions and sometimes using on-line pages), then the backflush lot selection rule may cause inaccurate results due to timing issues.
Before changing the backflush lot selection rule, it is recommended that you process all pending transactions in the staging tables (BCT tables) that impact production completion. If pending transactions are in the BCT tables, use caution when changing the backflush lot selection rule on the MFG BU Prnd Options page or the Define Business Unit Item - Manufacturing: General page. Changing the rule can impact how the pending transactions are processed.
You can integrate PeopleSoft Manufacturing with an electronic data collection system or a Manufacturing Execution System (MES), or both.
Electronic Data Collection
You can use electronic data collection to collect completions and scrap transactions, then import them to PeopleSoft Manufacturing. You can also collect and import actual hours transactions using electronic data collection.
For actual hours, the data collection method employs the same breakout of hour types as the online method such as setup, run, fixed run, and post-production. Electronic data collection allows for individual or crew reporting as well as single or multiple machine reporting.
Use the Actual Hours EIP to import actual hours information from a third-party system.
See Understanding the Process of Recording Completions and Scrap Using Electronic Data Collection.
Manufacturing Execution System (MES)
If you're integrating PeopleSoft Manufacturing to an MES, you can record operations completed, quantity completed, and scrap quantity in the MES. You can then import completion transactions to enable the optimization of production activities from production order launch to completion of finished goods. All production IDs, production schedules, and operations must be recognized in the PeopleSoft system; otherwise the system marks the transactions as errors in transaction maintenance. You then need to make corrections so that the transaction can be processed.
For multiple output transactions, you can record actual outputs in the MES, including completed quantities for co-products and by-products. You must send the completed output quantity if the batch quantity complete is not reported. You can report only unplanned by-products, not unplanned co-products.
You can also report the serial, lot, or container numbers for items produced or consumed in production. If the produced item requires lot, serial, or container details in the PeopleSoft system, the system marks transactions sent without this information as an error in transaction maintenance. For serial-controlled components or components that are both lot and serial-controlled, the serial numbers and lot IDs must be provided to the system or the transaction is marked in error to be corrected in transaction maintenance. For lot-controlled components, the incoming data must contain the lot IDs for consumed components if you have selected the backflush lot selection rule of Manual. If you have selected the backflush lot selection rule of Earliest Expiration Date or Earliest Available Date, then the incoming files are not required to have a lot ID for consumed components.
You can also report component consumption and communicate it to PeopleSoft Manufacturing using the Production Order Issue EIP. This EIP is a batch subscribe (inbound), asynchronous message.
When you pass component usage from the MES, all component consumption for a production order is sent, regardless of whether the quantity consumed was the default quantity. If components consumed are under serial or lot control, the lot or serial numbers are passed from the MES to update PeopleSoft Inventory. For lot-controlled components, the lot IDs can be automatically added by the Prdn Compl/Scrap (SFPDCDRV) process if you have selected the backflush lot selection rule of Earliest Expiration Date or Earliest Available Date.
The system validates component consumption transactions coming into the PeopleSoft system to ensure that the production IDs and items are valid in the business unit. The items must be valid for the BOM or as substitutes. If the consumption transaction would drive inventory negative in a business unit where negative inventory is not permitted, the system doesn't process the transaction.