Editing Component Lists
At some point while recording operation completions and scrap, you may need to view or modify the component list or select the lot and or serial numbers for the consumed components. Using the Edit/Issue Components pages, you can:
Add components to or delete components from the component list.
Add substitute components to or delete substitute components from the component list.
Change the scheduled quantity, quantity per order or per assembly, operation sequence, or component yield percentage.
Change the pending issue or pending yield loss quantity.
View or edit components even if you haven't reported any end item completions or scrap.
Consume components that couldn't be consumed previously due to shortages in the WIP location.
Select the serial numbers or lot numbers of the components to be consumed. For lot-controlled components that are not serial-controlled, you can view or change the lot numbers assigned during backflush, if you have selected the backflush lot selection rule of Earliest Expiration Date or Earliest Available Date.
See Automatically Consuming Lot-Controlled Stock During a Backflush.
In addition to using this page to record the consumption of components in the process of recording completions or scrap, you can also use this page to:
Record miscellaneous consumption of components, independent of backflushing.
Consume pending component quantities that were created when you backflushed and a shortage existed in the WIP location.
If a shortage existed and you already recorded completions, you must first issue material to the WIP location and then use the Edit/Issue Components pages to consume those quantities.
Keep these in mind when editing component lists:
For regular production, the system displays the components in effect for the end item at the due date for production or for the item revision, if one is specified.
If a component for the item is designated as a phantom on the production BOM, the phantom item's components—not the phantom item—is listed here. The operation sequence for the phantom is used for the phantom components.
For production IDs using serial genealogy, and component's trace usage = serial or lot, the issue qty field is display-only.
Use the Component Association or the Maintain Serial Genealogy commands to associate and consume these components. To consume trace usage components that are not associated with a serial assembly enter quantity in the pending yield loss qty field.
For rework production, the end item is the only component listed unless you're using a rework BOM or have previously maintained the component list and added those components necessary to rework the end item.
For teardown production, the end item to be torn down is the only component listed, unless you have previously added additional components to the component list.
You can change any component to a different item ID, or you can add a new component or substitute.
You cannot change the component ID or operation sequence it is associated with once the component has been issued. In addition, for rework production, you cannot change the end item that is being reworked and for teardown production, you cannot change the end item to be torn down.
For all production types, when you add new components with an item status of Discontinue, you receive a warning message.
For regular production, you receive a warning message when you add a component with an item status of Hold. In both cases, receiving the warning message doesn't prevent you from performing the action. For rework and teardown, components with an item status of Hold are issued.
When using the online mode of this component (PID Completion Option on the MFG BU Prdn Options page), if the backflush process has completed and then a field is changed that causes the pending quantities field to be recalculated, this causes a recalculation of backflush lot selection rule. Fields that trigger the recalculation of the pending quantities include:
Completion Quantity
Scrap Quantity
Completion Op Sequence
Back thru Op Sequence
Component ID
Component's Op Sequence
Component's Qty Code
Component's Qty Per
Picking a substitute item
For regular production, you cannot add the end item as a component.
On the other hand, for rework production, you cannot delete the reworked end item from its component list. Duplicate components can exist as long as the operation sequence is unique. You cannot add a configured item as a component unless the end item is a configured item.
When deleting components, the system checks to see if:
The issue quantity for the component is greater than zero.
In this case, you cannot delete the component. To delete the component, reverse the backflush, unconsume the component, or use the Kit Issue/Return page to return the component, and then delete it.
The component's issue method is Kit, and a pick plan has been generated for this component.
Note: If you need to add a phantom component to the component list, you must enter all of the items that make up the phantom component. A substitute component cannot be a phantom or a component of a phantom. Where substitutes exist for a component, the component cannot be changed to a phantom.
Editing or Issuing Components for Production Schedules
You can also use the Edit/Issue process to consume existing pending quantities for a production schedule. After selecting the area or item and dates of the production schedule and clicking the Search button, a message appears if there are any existing pending quantities for production schedules that match the selection criteria. If Yes, then the components with existing pending quantities appear.
Workflow Notification
If you have enabled PeopleSoft Workflow, you can use the Replenishment Notification workflow to notify the stockroom when the quantity on hand for components with a component issue method of Production Replenishment falls below its minimum stocking quantity in that location. This notification indicates that the location must be replenished.
Note: When you're editing or issuing components, the system doesn't allow you to modify component information for components whose issue method is Kit. Use the Kit Issue/Return Component to edit or issue these components. Additionally, you can view but cannot modify components whose source code is Floor Stock.
Issuing Components and Effects on Quantities
Action |
Results to Quantities |
---|---|
Issuing components to production |
Decreases the business unit's on-hand quantity. |
Returning components to inventory |
Increases the business unit's on-hand quantity. |
Issuing material from a nettable, available WIP location |
Decreases the business unit's reserved quantity. |
Returning components to a nettable, available WIP location |
Increases the business unit's reserved quantity. |
For owned items, issuing components to production |
Decreases the business unit's owned quantity. |
Returning owned components to inventory |
Increases the business unit's owned quantity. |
Issuing components to production |
Decreases the storage location's quantity. |
Returning components to inventory |
Increases the storage location's quantity. |
Issuing lot-controlled components to production |
Decreases the lot quantity on-hand. |
Returning lot-controlled components to inventory |
Increases the lot quantity on-hand. |
Capacity Checking
You activate weight and volume capacity checking on the PeopleSoft Inventory Options page, and define the capacity for each storage location on the Volume/Weight Capacity page accessible from the Material Storage Locations page.
If the item is designated as an isolate item on the Inventory-Shipping/Handling page in the Define Business Unit Item component, it can only be put away or transferred to empty storage locations or to locations containing stock with the same item ID. The system prevents you from moving an isolate item to a WIP location with other items.
If you designate a WIP location as storing only one item on the Volume/Weight Capacity page that is accessible from the Material Storage Locations page, the system only issues material with that item ID to that location. If you do not specify an item ID for a single-item WIP location, the first issue transaction to the empty WIP location defines the only item ID that the location can contain until the item quantity has been fully depleted.
Page Name |
Definition Name |
Usage |
---|---|---|
SF_ED_COMPS_SELECT |
Select the production ID or production schedule for which you want to edit or issue components. Components must have an issue method of Issue or Replenish to use this page. |
|
SF_EDIT_COMPS_EDIT |
Edit or view components. In addition, use this page to edit or issue components during the Record Completions and Scrap process or after the Record Completions/Scrap process has been run. |
|
SF_EDIT_COMPS_EXPR |
(Optional) Select lot- or serial-controlled components that have pending issue or pending loss quantities. You can view or change lots assigned to lot-controlled components by the backflush lot selection rule. |
|
SF_ED_CMP_SBP_GRD |
(Optional) Select the lot or serial numbers or both of the lot- or serial-controlled components to be consumed during the completions process. You must enter a pending quantity greater than zero for a serial-controlled or lot-controlled component before the Lot/Serial scroll area is available. |
|
SF_EDIT_COMPS_DET |
View detailed information for each component for selected production. |
|
SF_TRANSHIST |
View production transaction history for components. |
|
Transaction History Details inquiry Page |
SF_TXN_HIST_SP |
View completions details based on the selection criteria. |
Use the Production Selection page (SF_ED_COMPS_SELECT) to select the production ID or production schedule for which you want to edit or issue components.
Components must have an issue method of Issue or Replenish to use this page.
Navigation:
Field or Control |
Description |
---|---|
Production ID |
Enter a value to edit or issue components for a production ID. |
Production Area and Item ID |
Enter values to edit or issue components for a production schedule. |
Revision |
Displays if the item entered is revision-controlled. You can change the revision code if you're building to a different revision. |
Eff Date (effective date) |
Displays the current date if the item is not revision-controlled. The revision or effective date determines the BOM configuration used to create the component list. |
BOM/Rtg Effdt |
Select a value if you have predefined specific BOM and routing combinations with the Production Options maintenance pages. |
|
Click the Select BOM/Routing button next to the BOM/Rtg Effdt field to access the Select BOM/Routing page to select a different BOM and routing combination. |
BOM Code and Routing Code |
Displays valid codes for the BOM and routing code combination. |
Search |
Click the Search button to retrieve the information associated with the production ID or production schedule. |
Use the Edit/Issue Components Summary page (SF_EDIT_COMPS_EDIT) to edit or view components.
In addition, use this page to edit or issue components during the Record Completions and Scrap process or after the Record Completions/Scrap process has been run.
Navigation:
This example illustrates the fields and controls on the Edit/Issue Components Summary page . You can find definitions for the fields and controls later on this page.
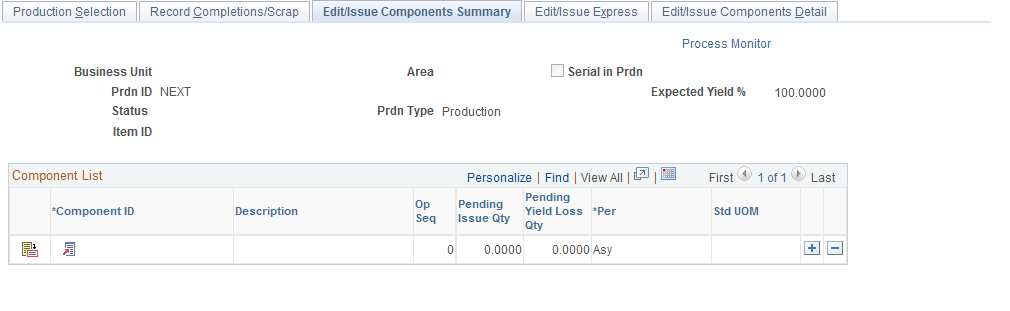
Field or Control |
Description |
---|---|
Print at Save |
Select this check box if you want to print production documents for a particular production ID at save time. |
Setup Print Options |
Click this link to access the Process/Output Options page to select different print criteria for the production documents. |
|
Click the Express Page button to access the Edit/Issue Express page to view or assign serial and lot numbers. |
|
Click the Detail button to access the Edit/Issue Component Detail page. |
|
Click the Item Search button to access the Item Search, Item Availability, or Item Substitution pages. |
Op Seq (operation sequence) |
Determines the WIP inventory location to which the components are issued and from which they are consumed. When you add a new component to the component list, the operation sequence defaults to zero. When recording end item completions and scrap, the system consumes a component with an operation sequence of zero at the first operation and decrements the component quantity on hand in the production area's default WIP location. You can change the operation sequence to any valid operation on the end item's operation list. When you select an operation sequence, the component must be issued to and is consumed from the WIP location associated with the operations work center. |
Per |
Indicates whether the quantity required is per assembly (Asy) or per order (Ord). Per assembly indicates the quantity required to complete one end item. Per order indicates the amount required, regardless of the end items that will be produced.
|
Pending Issue Qty (pending issue quantity) |
The system calculates this value for those components whose operations have had end item completions or scrap reported. Enter a new pending issue quantity if you consumed more or less than the quantity calculated. The pending issue quantity is based on the quantity completed plus the quantity scrapped multiplied by the quantity per assembly. If the quantity on the component list is expressed in terms of quantity per order, the full quantity appears. This quantity is consumed only at the time of the first backflush for production ID. For production schedules, the Calc Per Order for Production Schedules option on the Manufacturing Business Unit Option page determines how the quantity is displayed. If you have enabled PeopleSoft Workflow, the system sends a notice to the production supervisor that there is a nonzero quantity for this component. PeopleSoft Manufacturing uses the Identify Production with Pending Quantities workflow for this notification.
|
Pending Yield Loss Qty |
If the quantity of components lost is more or less than planned, indicate the new pending yield loss quantity here. If the item's yield loss is set to calculate the pending yield loss quantity, then the system calculates the pending yield loss for those components whose operations have had end item completions or scrap reported. You define whether or not you want the system to calculate pending yield loss quantity at the business unit or item level. If you do not want the system to calculate pending yield loss quantity, then you manually record the yield loss at the appropriate times. The system uses this formula to calculate the pending yield loss quantity: (Quantity Completed + Quantity Scrapped) x Expected Yield Loss Percentage Expected Yield Loss Percentage = (1 - Component Yield / 100) |
Adding or Substituting Components
Field or Control |
Description |
---|---|
Component ID, Op Seq (operation sequence), Per Asy (assembly) or Ord (order), Pending Issue Qty (pending issue quantity), and Pending Yield Loss Qty (pending yield loss quantity) |
Enter values for these fields if you're adding or substituting components. Note: Pending issue and pending yield loss quantities are not calculated for expensed or floor stock items. In addition, you cannot enter values for components with an issue method of Kit. To change or enter the quantity per, yield, or scheduled quantity, use the Edit/Issue Component Detail page. If you're substituting a component, zero out the pending issue and pending yield loss quantity for the original component. |
Allowing Negative On Hand Inventory
If the PeopleSoft Inventory business unit parameter allows negative inventory balances and there is not enough material in the WIP location to cover the pending issue or pending yield loss quantity, the quantity on hand in the WIP location will become negative. Another business unit parameter determines when the system issues a warning message prior to driving quantity on hand negative. This message allows you to decide whether to continue with the completion transaction or to wait until the inventory is moved into the WIP location before continuing. If you do not allow the inventory to go negative, the quantity that couldn't be consumed remains in the pending issue or pending yield loss fields. These must be reconciled once the WIP location has sufficient quantity on hand.
Note: If the item that you're consuming is serial-controlled, you cannot drive the quantity on hand negative, regardless of the PeopleSoft Inventory business unit setting.
Use the Edit/Issue Express page (SF_EDIT_COMPS_EXPR) to (Optional) Select lot- or serial-controlled components that have pending issue or pending loss quantities.
You can view or change lots assigned to lot-controlled components by the backflush lot selection rule.
Navigation:
This example illustrates the fields and controls on the Edit/Issue Components - Edit/Issue Express page. You can find definitions for the fields and controls later on this page.
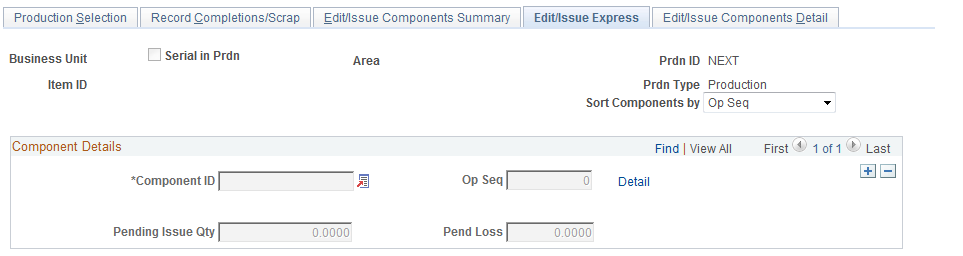
Field or Control |
Description |
---|---|
Component Details |
You can change any of this information on this page:
|
Use the Lot/Serial Number Selection page (SF_ED_CMP_SBP_GRD) to (Optional) Select the lot or serial numbers or both of the lot- or serial-controlled components to be consumed during the completions process.
You must enter a pending quantity greater than zero for a serial-controlled or lot-controlled component before the Lot/Serial scroll area is available.
Navigation:
Click the Select Lot/Serial link.
Field or Control |
Description |
---|---|
Sel (select) |
Select the serial-numbered components that you want to consume by selecting one or more check boxes. |
Access the Lot/Serial scroll area on the Edit/Issue Express page
Field or Control |
Description |
---|---|
Lot ID |
Select a lot if you're editing or issuing lot-controlled components. You can view or change lots assigned by the backflush lot selection rule. |
Qty Req (required quantity) |
Specify the amount of components that you want to consume from each lot. This field can be automatically populated during backflush using the backflush lot selection rule. |
Use the Edit/Issue Components Detail page (SF_EDIT_COMPS_DET) to view detailed information for each component for selected production.
Navigation:
Detail button next to the component you want to edit or view.
Click the
This example illustrates the fields and controls on the Edit/Issue Components Detail page. You can find definitions for the fields and controls later on this page.
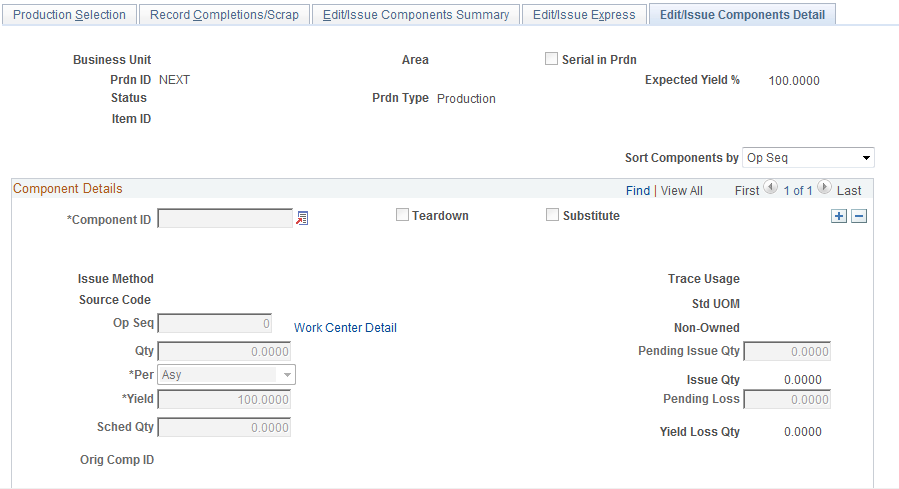
Component Details
Field or Control |
Description |
---|---|
Component ID, Op Seq (operation sequence), Qty (quantity), quantity Per, Yield, and Sched Qty (scheduled quantity) |
Enter or modify values for these fields. |
Work Center Detail |
Click this link to access work center-related information. |
Qty (quantity) |
The calculated quantity per is next to this field. The system calculates the quantity per by dividing the quantity per assembly by the bill of material's BOM quantity. You designate the level of precision for the calculated quantity per on the Manufacturing installation options page. |
Pending Issue Qty (pending issue quantity) and Pending Yield Loss Qty (pending yield loss quantity) |
Although these values appear by default from the Edit/Issue Components Summary page, you can change them here. Note: If you are not completing end items, a pending issue or pending yield loss quantity greater than zero indicates that the components couldn't be consumed from the appropriate WIP location from a previous completions or edit components transaction. This is due to a shortage of the component in the WIP location associated with the component's operation sequence. |
Issue Qty (issue quantity) |
This field represents the quantity consumed that was issued from the WIP location for the component and was charged to WIP. For items using the Kit issue method, this is the quantity that was issued during Material Release of a production Pick Plan or issued using the Issue/Return Kit Components page. You cannot modify kitted components here. This field is used for production IDs only. |
Yield Loss Qty (yield loss quantity) |
This field represents the component quantity that was scrapped during end item completion and issued from the WIP location. This field is used for production IDs only. |
Issue Method |
This field indicates the component replenishment issue method. |
Note: Quantities of an item that are stored in a nettable, available WIP location and reserved for production use are not available for other purposes.
An Application Engine process queries the production component table for any outstanding pending component quantities for production with a status of In Process or Pending Complete. If the system finds outstanding quantities, the system issues a worklist notification for each of the qualified production orders to relieve the component. When you work the worklist entry, you're transferred to the Edit/Issue Components Summary page. Once you consume material to relieve the shortages, the worklist entry is marked as completed.