Recording Completed Operations and Scrap for In-House Production IDs
At some point during the in-house production process, you must record completed operations and scrap. Using the Record Completions and Scrap component, you can:
Record completed operations for all or part of the production quantity.
Record completions and scrap for the production run with multiple outputs.
Scrap end items at an operation.
Backflush the entire production run or order.
Report completed setup or post production work independent of recording the completion of any end items.
Automatically consume components based on the quantity completed.
Automatically complete end items based on the batch completed quantity.
Manually substitute components where there is a shortage of an item or an item is out of stock.
Transfer completions data to PeopleSoft Quality, if your installation includes PeopleSoft Quality and you have defined quality configuration information and quality plans in PeopleSoft Quality for the manufactured item and its process.
You record quality control information for the manufacturing process for the end item and then access the Record Completions/Scrap page.
Assign serial numbers and lot numbers to completed end items before moving them out of the production area.
Route completed end items to another production ID or WIP location to be used on subsequent end item production.
Route completed end items (including primary items, co-products, and recycle by-products) to another production ID or WIP location to be used on subsequent end item production.
Indicate that production has been completed for the production ID.
Note: Primary items and co-products can be completed only at the last operation. By-products, such as recycle or waste, can be completed at any operation.
If you have enabled PeopleSoft Workflow, when you record end item scrap, the system sends notification to selected roles defined by you by using the Assembly PID Scrap Notification workflow. These roles might include a quality manager or a production control manager.
Page Name |
Definition Name |
Usage |
---|---|---|
SF_COMPL_SELECTION |
Select a production ID to record completions and scrap. You must define at least one production ID. |
|
SF_COMPL_ID |
Enter completions and scrap information for production IDs. In addition, use this page to move end items for production IDs with a single output or multiple outputs. |
|
SF_COMPL_SCRAP |
Enter scrap quantities, if applicable. |
|
Apply Defaults Page |
SF_COMPL_DEFAULTS |
Select the default putaway or alternate storage locations for completed end items. |
MG_SERIALRG_PG_SBP |
(Optional) Automatically generate serial numbers for production end items that are serial-controlled. You must define serial-controlled items in PeopleSoft Inventory. |
|
Work Center Details Page |
SF_WORK_CTR_SP |
View work center-related information such as WIP locations. |
Lot/Serial Number Selection Page |
SF_ED_CMP_SBP_GRD |
(Optional) Select the serial numbers of the serial-controlled components to be consumed during the completions process. You must enter a pending quantity greater than zero for a serial-controlled component before the Lot/Serial scroll area becomes available. |
Lot/Serial Number Selection scroll area Page |
SF_ED_CMP_SBP_GRD |
(Optional) Identify the lots from which you want to consume lot-controlled components. You must enter a pending quantity greater than zero for a lot-controlled component before the Lot/Serial scroll area is available. |
SF_COMPL_PRDN |
Indicate that production has been completed for a selected production ID. |
|
SF_TRANSHIST |
View production transaction history for production IDs. |
|
Transaction History Details (inquiry) Page |
SF_TXN_HIST_SP |
View production transaction history details based on:
|
With production IDs, you can:
Record completions and scrap by operation.
Record completions and scrap by count points.
Record partial production completions.
Complete an entire production ID.
Move the completed end items to stock, WIP location, or another production ID.
Note: There is no difference between the method that you use to record completed and scrapped end items for regular production and the method that you use for rework production. When recording completions for teardown orders, you report the number of end items torn down. The system calculates the quantity of the teardown end items based on the quantity of the end items being torn down. As is the case with all production types, you can override the teardown quantity for each end item.
Using the Record Completions and Scrap component, you can record in-house operation or end item completions and scrap for production IDs with a status of:
Entered or Firmed: The system automatically releases the production ID and the status changes to In Process.
The ability to release a production ID with a status of Entered or Firmed is dependent on the Manufacturing business unit production options for the autorelease of production IDs. When setting up the business unit, you can select Prompt for Auto Release, Auto Release, or No Auto Release.
Released: The system changes the status to In Process.
In Process.
Important! If you're using the production issue or production kit material issue method for regular production, you must still issue material to the WIP locations using the Pick Plan and Material Release components. If you're using the production replenishment method, ensure that sufficient inventory exists in the WIP location.
Use the Production Selection page (SF_COMPL_SELECTION) to select a production ID to record completions and scrap.
You must define at least one production ID.
Navigation:
Field or Control |
Description |
---|---|
Unit and Production ID |
Enter values for the production ID that you want to record completions and scrap. |
Search |
Click to retrieve the selected production ID. |
Use the Record Completions/Scrap page (SF_COMPL_ID) to enter completions and scrap information for production IDs.
In addition, use this page to move end items for production IDs with a single output or multiple outputs.
Navigation:
This example illustrates the fields and controls on the Record Completions/Scrap page. You can find definitions for the fields and controls later on this page.
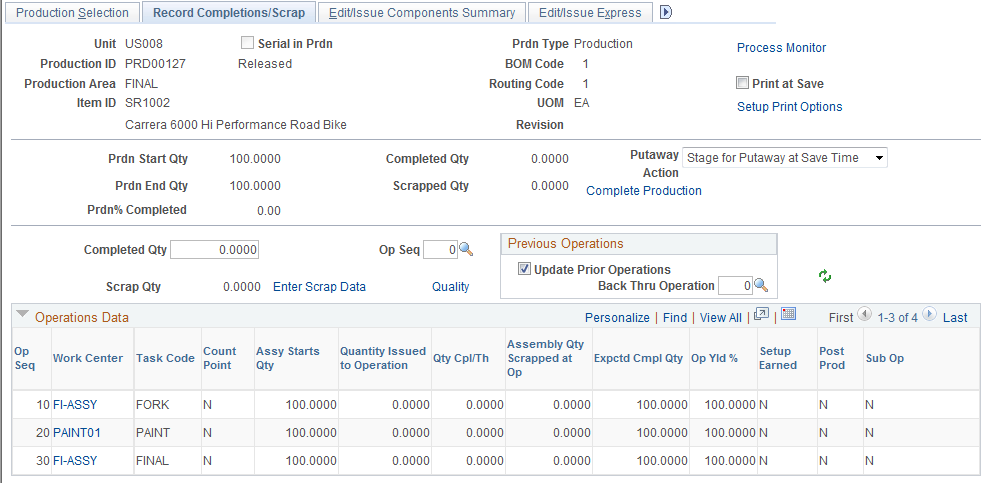
Previous Completions Information
Field or Control |
Description |
---|---|
Prdn Start Qty (production start quantity) and Prdn End Qty (production end quantity) |
Displays default quantity values from the Production ID Maintenance component. These values are updated whenever the quantity completed is changed. |
Prdn% Completed (production percentage completed) |
Displays the percentage of the batch production quantity that has been completed prior to this transaction. |
Completed Qty (completed quantity) and Scrapped Qty (scrapped quantity) |
Displays a quantity that represents the quantity that has been completed at the last operation. Scrapped quantity represents the quantity that has been scrapped at all operations. |
Putaway Action |
Select which putaway process to use. Options are:
Note: Upon saving the page, either stage the item for putaway or initiate the putaway process. Item completions are not allowed if the end item or a component of the end item is on hold. Similarly, item completions are prevented if a co-product or recycle by-product is on hold. However, completions are allowed for waste by-products with a hold status. |
Print at Save |
Select this check box if you want to print production documents for this particular production ID at save time. |
Setup Print Options |
Click this link to access the Process/Output Options page to select different print criteria for the production documents. |
Recording Operation Completions
Field or Control |
Description |
---|---|
Completed Qty (completed quantity) |
Enter the entire production ID quantity or any portion of that quantity for each operation sequence that you want to record completions. You can enter completions as many times as necessary to complete the production quantity for the production ID. For production IDs with a single output, this field represents the quantity completed at the operation sequence. |
Op Seq (operation sequence) |
Select the operation step where the end items were completed. You can record partial completions by specifying any valid operation sequence, even if prior operation completions haven't been recorded. If you're using count points and you enter an operation sequence that is not a count point, then you can record only scrap. When using count points, completion quantities can only be entered at operations flagged as count point operations. |
Update Prior Operations |
Select this option if you want to automatically record completions and scrap for prior in-house operations at the same time that you're recording completions for this operation. |
Back Thru Operation |
Indicate how far back you want to report completions by selecting the operation sequence. The quantity that you're currently completing is added to any previously completed quantities at all prior operations specified. If you're using count points, this field displays the operation after the previous count point. |
Previous Operations |
If you're recording prior operations at a later time, do not enter any information in this group box, and ensure that the Update Prior Operations check box is deselect. |
|
Click the Refresh button to update the information in the Operations Data grid. |
Viewing Operations Data
The Operations Data scroll area displays production details based on operation sequence. You can view operation-related information such as assembly starts quantity, scrap quantities, expected completed quantity, and operation yield.
Click the Work Center link to view work center-related information.
Example: Recording Completions
Production start quantity: 10
Quantity completed: 10
Completing at operation sequence: 30
In this example, you want to complete a quantity of 10 at operation sequence 30. You selected the Update Prior Operations check box on the Record Completions/Scrap page, and indicated that you wanted to update previous operations back to operation sequence 20. The system calculates any production and scrap completed at operation sequences 20 and 30:
Operation Sequence |
Quantity Issued |
Quantity Completed Through |
Quantity Scrapped |
---|---|---|---|
10 |
10 |
10 |
0 |
20 |
10 |
0 |
0 |
30 |
0 |
0 |
0 |
40 |
0 |
0 |
0 |
Once you've completed 10 at operation 30 and updated back through 20, the operations appear as follows:
Operation Sequence |
Quantity Issued |
Quantity Completed Through |
Quantity Scrapped |
---|---|---|---|
10 |
10 |
10 |
0 |
20 |
10 |
10 |
0 |
30 |
10 |
10 |
0 |
40 |
10 |
0 |
0 |
Warning! You cannot update prior subcontracted operations using this option. If there is a prior subcontracted operation and the Update Prior Operations check box is selected, the system ignores the subcontracted operation when recording the prior operations as completed. Use the Subcontract Receipt component to record completed operations and scrap for the subcontracted operation.
Yield by Operation Example: Completing Less Production End Quantity than Expected
When using yield by operation, the beginning production quantities at subsequent operations are affected when either good or scrap production quantities are greater than expected. This example illustrates the effect of yield by operation when you scrap more end items than you originally expected.
Operation sequence: 30
Operation start quantity: 80
Operation yield: 98 percent
Scrapped quantity: 5
Operation Sequence |
Operation Start Quantity |
Quantity Issued to Operation |
Quantity Completed Through |
Quantity Scrapped |
Expected Completed Quantity |
Operation Yield Percentage |
---|---|---|---|---|---|---|
10 |
80 |
80 |
80 |
0 |
80 |
100 |
30 |
80 |
80 |
70 |
5 |
75 |
98 |
40 |
75 |
70 |
0 |
0 |
75 |
100 |
50 |
75 |
0 |
0 |
0 |
67 |
90 |
In this example, a quantity of 80 was issued and completed through operation 10. Because there is a 100 percent operation yield, a quantity of 80 is expected at the end of this operation. The original quantity complete at operation 50 was 70.
However, at operation 30, there is a 98 percent operation yield, and overscrapping of a quantity of 5 also occurs. This means that out of the operation start quantity of 80, only 75 are expected to be completed. As these 75 flow through operations 40 and 50, further loss is expected at operation 50, and the expected completion quantity for the order is now 67.
Yield by Operation Example: Completing More End Items than Expected
This example illustrates the effect of yield by operation on subsequent operations when you scrap fewer end items than you originally anticipated.
Operation sequence: 30
Operation start quantity: 69
Operation yield: 98 percent
Scrapped quantity: 0
Operation Sequence |
Operation Start Quantity |
Quantity Issued to Operation |
Quantity Completed Through |
Quantity Scrapped |
Expected Completed Quantity |
Operation Yield Percentage |
---|---|---|---|---|---|---|
10 |
69 |
69 |
69 |
0 |
69 |
100 |
30 |
69 |
69 |
69 |
0 |
69 |
98 |
40 |
69 |
69 |
69 |
0 |
69 |
100 |
50 |
69 |
0 |
0 |
0 |
62 |
90 |
In this example, a quantity of 69 was issued and completed through operation 10. Because there is a 100 percent yield, a quantity of 69 is expected at the end of this operation. The original quantity expected complete at operation 50 was 60.
However, at operation 30, there is a 98 percent operation yield and underscrapping occurred (scrapped less than expected). Out of the operation start quantity of 69, all were completed and continue to flow through production. As these 69 flow through operations 40 and 50, further loss is expected at operation 50, and the expected completion quantity for the order is now increased to 62.
Use the Production Scrap Details page (SF_COMPL_SCRAP) to enter scrap quantities, if applicable.
Navigation:
Click the Enter Scrap Data link.
Field or Control |
Description |
---|---|
Scrap Qty (scrap quantity) |
Enter an amount if scrap was generated during production. Scrap can be recorded at any operation sequence, even if you are using count points. For production IDs with a single output, the scrap quantity represents the number of scrapped end items at the operation sequence. For production IDs with multiple outputs, this field represents the number of scrapped end items for the batch (BOM) quantity, and not for each output. If the scrap at an operation exceeds the expected scrap quantity, you should create a new planned production order to meet the demand. For serial genealogy production, you may enter the specific serial ID that is being scrapped. If the serial ID has not previously been associated, you are given the option to create the association. If a routing has operation yield, a reported scrap quantity that is not equal to the expected scrap quantity changes start and end quantities at subsequent operations. It also changes the expected end quantity for the production order. Note: If the scrap quantity is greater than the production end quantity, the system updates the production start quantity so that the ending production quantity meets demand. |
Reason Code |
Select a value. This field indicates why the end item was scrapped. Scrap reason codes were previously defined using the Reason Code pages in the Set Up Financials/Supply Chain navigation. This field is required when a scrap quantity is entered. |
Scrap Pct (scrap production percentage) |
(Optional) This field indicates the percentage that the end item was completed at the operation where the scrap occurred. For example, if the scrapped end items were 75 percent complete before they were scrapped, enter that percentage here. In this example, when calculating the cost of scrapped end items, the system allocates all prior operation costs, plus 75 percent of the runtime costs of the operation where the scrap occurred to each scrapped end item. This percentage is used to calculate the amount of conversion costs earned and scrapped at this operation. If no value is entered, 0 appears in this field. |
Distrib. Type (distribution type) |
(Optional) This field indicates the transaction distribution type for the scrap transaction. The distribution type in combination with the scrap transaction determines the correct accounting entries to post the scrap loss to the general ledger. The system displays the default distribution type for the production scrap transaction group. Default distribution types are defined using the Default Distribution Types page. You can override the distribution type for each transaction. |
Note: If you're scrapping production that has an operation yield less than 100 percent, the scrap cost calculation is not performed.
The difference in expected and actual scrap is recorded as operation yield variance.
With production IDs, you have the option of scrapping end items at any operation or at the end of production when you can complete end items to stock or another production area. If you're recording scrap at an intermediate operation on a multiple output production ID, you're recording the scrap quantity for the batch and not the individual output items.
When recording scrap at an intermediate operation, the scrap quantity is associated only to the operation where the scrap was recorded. However, if you have selected to complete back through prior operations, the scrapped quantity will be presumed to have been completed at those prior operations.
Example: Scrapping at Operation 30 and Completing Back Through Operation 10
With no prior completed quantity, if you scrap 10 units at operation 30, the operation list would look as follows:
Operation Sequence |
Quantity Issued |
Quantity Completed Through |
Quantity Scrapped |
---|---|---|---|
10 |
10 |
10 |
0 |
20 |
10 |
10 |
0 |
30 |
10 |
0 |
10 |
40 |
0 |
0 |
0 |
Note: You cannot record scrap at the output level. Scrapped end items for production with multiple outputs are recorded at the batch (BOM) level.
Recording Scrap When Using Count Points
When using count points, scrap can be recorded at any operation, regardless of the count point designation. The system updates the scrap quantity for the operation where the scrap occurred. In addition, the system assumes the scrapped quantity was completed at all previous operations up to the previous count point.
Count point operations: 30, 60
Production start quantity: 15
Step 1
Production start quantity previously completed or issued: 10
Operation Sequence |
Quantity Issued |
Quantity Completed Thru |
Quantity Scrapped |
---|---|---|---|
10 |
10 |
10 |
0 |
20 |
10 |
10 |
0 |
30 (count point) |
10 |
10 |
0 |
40 |
10 |
0 |
0 |
50 |
0 |
0 |
0 |
60 (count point) |
0 |
0 |
0 |
Step 2
Scrap quantity: 5
Scrapping at operation sequence: 30
Operation Sequence |
Quantity Issued |
Quantity Completed Through |
Quantity Scrapped |
---|---|---|---|
10 |
15 |
15 |
0 |
20 |
15 |
15 |
0 |
30 (count point) |
15 |
10 |
5 |
40 |
10 |
0 |
0 |
50 |
0 |
0 |
0 |
60 (count point) |
0 |
0 |
0 |
Example 2
Production start quantity previously completed and issued: 10
Scrap quantity: 5
Scrapping at operation sequence: 50
Operation Sequence |
Quantity Issued |
Quantity Completed Through |
Quantity Scrapped |
---|---|---|---|
10 |
10 |
10 |
0 |
20 |
10 |
10 |
0 |
30 (count point) |
10 |
10 |
0 |
40 |
10 |
0 |
0 |
50 |
0 |
0 |
0 |
60 (count point) |
0 |
0 |
0 |
In this example, you have recorded scrap at a noncount point operation. In this case, the system records completions for any previous operations back to the operation after the previous count point (operation 40):
Operation Sequence |
Quantity Issued |
Quantity Completed Through |
Quantity Scrapped |
---|---|---|---|
10 |
10 |
10 |
0 |
20 |
10 |
10 |
0 |
30 (count point) |
10 |
10 |
0 |
40 |
10 |
5 |
0 |
50 |
5 |
0 |
5 |
60 (count point) |
0 |
0 |
0 |
Once an end item is scrapped, the scrap end item value is calculated and expensed. Item costs for expensed and floor stock items are not included in the end item scrap cost. The end item, including the components used to that point, and the labor, machine, and overhead costs earned to that point are no longer accounted for in WIP inventory.
Note: If you record scrap for an operation that precedes a subcontracted operation, and the purchase order has already been generated for the production quantity, the system sends a purchase order change request to PeopleSoft Purchasing, indicating a change in production quantity. This change must be processed before the end items are sent to the subcontractor.
Use the Rapid Serial Numbers page (MG_SERIALRG_PG_SBP) to (Optional) Automatically generate serial numbers for production end items that are serial-controlled.
Navigation:
Click the Generate Serial IDs link.
Field or Control |
Description |
---|---|
Serial Number Count |
Displays the number of completed end items that the system assigns serial numbers. A serial number is assigned to all the end items indicated as completed on the Record Completions/Scrap page. |
Serial ID Parameters |
Displays default information from the Automatic Serial Number page. |
Serial Number Prefix, Multiplier, Serial Number Length, and Zero Pad |
You can use the default values for the business unit or item or you can override these defaults here. The serial number prefix can contain up to three alphabetic and numeric characters. The Multiplier field indicates the increment in which to assign serial numbers. For example, a multiplier of 1 increments each serial number that the system assigns by one. If the last serial number assigned was MFG00001, then the next serial number is MFG00002. Select Zero Pad if you want to use zeroes as placeholders for the serial number length that you defined. Use the Start Num (start number) field to specify the first serial number that you want to assign to the completed end items. If you enter a specific starting number, the serial numbers begins with that starting number. The default for this field is blank, and you do not have to enter a starting number. If you leave the field blank and click OK, you receive a warning that the starting serial number is blank and zero appears by default. In this case, the starting serial number is MFG00000. If you enter 1 in this field, the starting serial number is MFG00001. |
OK |
When you click this button, each completed end item, along with the corresponding serial number, appears in the Route-To PID/Stor Locations scroll area on the Record Completions/Scrap page. |
You can use count points to record end item completions.
To record completions and scrap for production IDs using count points:
Access the Record Completions/Scrap page.
Enter the Completed Quantity for the operation sequence.
If you enter the completed quantity first, only the count point operation steps are available.
Select the Op Seq (operation sequence) that is a count point.
If you click the operation sequence look up without entering a completed quantity, all operation sequences appear.
Note: When you record completions at the last operation (which must be a count point), the system assumes that you have or will complete at all prior count points. Therefore, the completed quantity is updated only back to the prior count point.
Because the system automatically completes back to the operation after the previous count point, the Update Prior Operations and the Back Thru Operation fields are unavailable and the operation after the prior count point (operation sequence) appears by default. This indicates that the quantity completed will also be recorded for operations up to, but not including, the prior count point. If you're recording completions at the first count point, the system automatically completes back through and including the first operation.
All other processes, such as entering scrap data and routing completed end items, remain the same as those used with completing production IDs at intermediate operations.
Example: Recording Completions Using Count Points
Count point operations: 30, 50
Production start quantity: 10
Step 1
Quantity completed: 10
Count point at operation sequence: 30
In this example, you want to complete a quantity of 10 at operation sequence 30, which is a count point. The system calculates any production and scrap completed at operation sequences 10, 20, and 30:
Operation Sequence |
Quantity Issued |
Quantity Completed Through |
Quantity Scrapped |
---|---|---|---|
10 |
10 |
10 |
0 |
20 |
10 |
10 |
0 |
30 (count point) |
10 |
10 |
0 |
40 |
10 |
0 |
0 |
50 (count point) |
0 |
0 |
0 |
Step 2
Quantity completed: 5
Count point at operation sequence: 50
In this example, you want to complete production for a quantity of 5 at operation sequence 50, which is a production ID count point. The system doesn't include operation sequence 30 because it is the prior count point:
Operation Sequence |
Quantity Issued |
Quantity Completed Through |
Quantity Scrapped |
---|---|---|---|
10 |
10 |
10 |
0 |
20 |
10 |
10 |
0 |
30 (count point) |
10 |
10 |
0 |
40 |
10 |
5 |
0 |
50 (count point) |
5 |
5 |
0 |
To record completions at the last operation:
Access the Record Completions/Scrap page.
Enter the last operation on the operation list in the Op Seq (operation sequence) field if you want to complete all operations for the production ID and all of the operations are performed in-house.
Select Update Prior Operations, then select the first operation from the Back Thru Operation options.
Enter the number of completed end items in the Completed Qty (completed quantity) field.
You can record completions for the entire production quantity for the production ID or any portion of the quantity.
All other processes, such as entering scrap data and routing completed end items, remain the same as those used with completing production IDs at intermediate operations.
Note: Co-products can only be completed at the last operation.
Use the Record Completions/Scrap page (SF_COMPL_ID) to enter completions and scrap information for production IDs.
In addition, use this page to move end items for production IDs with a single output or multiple outputs.
Navigation:
When completing end items at the last operation, the Route-To PID/Stor Locations scroll area on the Record Completions/Scrap page becomes available. You can route the completed end items to a storage area, another production ID, or to a WIP location. Additionally, if the end item is lot- or serial-controlled, or if you're utilizing containers, you can assign serial numbers, lot IDs, or container IDs to the completed end items.
If a default putaway location is defined for the end item, you can route the completed end items to that location using the routing portion of the page.
Click Apply Defaults to indicate that you want to put away the end items to the default putaway location.
Note: The completions process puts away items in their standard UOMs.