Recording Completed and Scrapped End Items for Production Schedules
For production schedules, you can record partial production completions, or you can complete the entire schedule.
Use the Record Completions/Scrap component to:
Record completed operations for all or part of the production quantity.
Record completions and scrap for production schedules with multiple outputs.
Scrap end items.
Completely backflush the entire production run or order.
Automatically consume components based on the quantity completed.
Automatically complete end items based on the batch completed quantity.
Manually substitute components where there is a shortage of an item or an item is out of stock.
Assign serial numbers and lot numbers to completed end items before moving them out of the production area.
Route completed end items, including primary items, co-products, and recycle by-products, to another production ID or WIP location to be used on subsequent end item production.
Indicate that production has been completed for the production schedule.
If you have enabled PeopleSoft Workflow, when you record end item scrap, the system sends a notification by using the Assembly Prdn Schedule Scrap Notification workflow to selected roles defined by you. These roles could include a quality manager or a production control manager.
Using this component, you can record in-house operation or end item completions and scrap for production schedules with a status of:
Entered or Firmed: The system automatically releases the production schedule, and creates the component list and operation list (if a routing exists).
The status is automatically changed to In Process.
Released: The system changes the status to In Process.
In Process.
If you're using production issue or production kit method for regular production, you still must issue material to the WIP locations using the Pick Plan and Material Release components. If you're using the production replenishment method, ensure that sufficient inventory exists in the WIP location.
Note: Quantities of an item that are stored in a nettable, available WIP location and reserved for production use are not available for other purposes.
You can record in-house operation or end item completions and scrap for production quantities that haven't been previously entered as scheduled quantities.
In this case, the system prompts you for the schedule quantity and the production schedule is automatically created with a status of In Process. You can then backflush a partial quantity or the entire production quantity and record any scrap.
If you're using the production issue method, you still must issue material to the WIP locations to ensure that there is sufficient quantity on hand to satisfy the production schedule quantities.
If you're using the production replenishment method, make sure that sufficient inventory exists in the WIP location.
This section lists common elements and discusses how to Record Completions and Scrap for Production Schedules
Page Name |
Definition Name |
Usage |
---|---|---|
SF_COMPL_SELECTION |
Select a production schedule to record completions and scrap. You must define at least one production schedule. The production status should be Released or In Process. |
|
SF_PA_SCH_PEG_SP |
Peg completions to a specific production schedule row. |
|
SF_COMPL_ID |
Enter completions and scrap information. In addition, use this page to move end items for production schedules with a single output or multiple outputs. |
|
Production Scrap Details Page |
SF_COMPL_SCRAP |
Enter any scrap quantities. |
Apply Defaults Page |
SF_COMPL_DEFAULTS |
Select the putaway locations for the completed end items. |
MG_SERIALRG_PG_SBP |
(Optional) Automatically generate serial numbers for production end items that are serial-controlled. You must define serial-controlled items in PeopleSoft Inventory. |
|
Work Center Details Page |
SF_WORK_CTR_SP |
View work center-related information such as WIP locations. |
Lot/Serial Number Selection Page |
SF_ED_CMP_SBP_GRD |
(Optional) Select the serial numbers of the serial-controlled components to be consumed during the completions process. You must enter a pending quantity greater than zero before the Lot/Serial scroll area becomes available. |
Lot/Serial Number Selection scroll area Page |
SF_ED_CMP_SBP_GRD |
(Optional) Identify the lots from which you want to consume lot-controlled components. Lots can be automatically assigned during backflush depending on your setting for the backflush lot selection rule. You must enter a pending quantity greater than zero before the Lot/Serial scroll area is available. |
SF_TRANSHIST |
View production transaction history for production schedules. |
|
Transaction History Details inquiry Page |
SF_TXN_HIST_SP |
View completions details based on the selection criteria. |
Field or Control |
Description |
---|---|
Prdn Start Date (production start date) |
The date on which the production is due to begin. |
Prdn Due Date (production due date) |
The date on which the production is due to be completed. |
Date Type |
The date used as a sort option for the production schedule—either by production start or production due date. |
Sch Method (scheduling method) |
For production schedules, Backward always appears. |
Use the Production Selection page (SF_COMPL_SELECTION) to select a production schedule to record completions and scrap.
You must define at least one production schedule.
Navigation:
Field or Control |
Description |
---|---|
Unit, Production Area, and Item ID |
Enter values for the production schedule. |
|
Click the Item Search button to access the Item Search Criteria page to locate a different item. |
Complete to a Specific Schedule |
Click this link if you want to select a specific production schedule. |
BOM/Rtg Code Effective Dates |
Because only one active BOM/routing combination is valid for an area at any one time, select the valid BOM/routing combination for accurate component consumption. By selecting an effective date in the BOM/Rtg Effdt (BOM/routing effective date) field, you determine the particular BOM/routing combination for which you want to complete. The BOM/routing effective date, which is the current date by default, determines which combination the system selects and displays in the BOM Code and Routing Code fields. For non-revision-controlled items, this BOM/routing date is used to decide which BOM/routing combination will be used and a second effective date that will be used for the components and outputs. If the item is revision-controlled, then both an item revision code and BOM/routing effective date must be selected. Note: Because you can create multiple schedules per area with only one combination effective at any one time, production schedules for prior effective date ranges may not be consumed if the effective date range for the combination has passed. For example, if you have BOM code 1 and routing code 2 valid from January 1, 2001, but BOM code 2 and routing code 2 is valid from June 1, 2001 for the same production area, then you could create production schedules for the 1/2 combination prior to June 1, 2001 but completing them after this date. In this case, the system is unable to consume for them because the new BOM/routing combination has taken effect. In addition, you get an auto-add message when you attempt to complete because no schedules currently exist for the 2 /2 combination. However, if you change the BOM/routing effective date back to a date prior to June 1, 2001, the system accesses the correct combination. |
|
Click the Select BOM/Routing button to access the Select BOM/Routing page to select a different BOM/routing combination. This selection also displays the effective dates of the BOM/routing combinations. |
Revision |
You can change the revision code if you're building to a different revision. If the item is not revision-controlled, the current date is displayed in the effective date BOM configuration used to create the component list. |
Negative Completions |
Select this check box if you are reversing a previous completions or scrap transaction. See Creating Reversing Entries to Correct Data Entry Errors. |
Search |
Click to retrieve the selected production schedule. |
Use the Schedule Selection page (SF_PA_SCH_PEG_SP) to peg completions to a specific production schedule row.
Navigation:
Enter the production area and item, and then click the Complete to a Specific Schedule link.
This example illustrates the fields and controls on the Schedule Selection - Summary page. You can find definitions for the fields and controls later on this page.
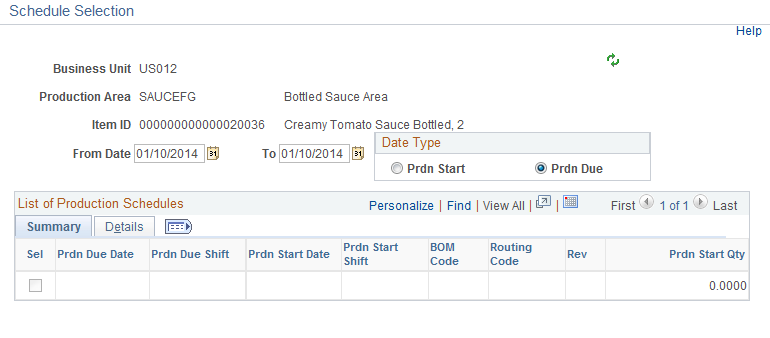
You may want to complete for a specific production schedule because a substitution was made or a data entry error needs to be corrected. In addition, by pegging to a production schedule, you update the specific production schedule when you run the Completions Update process.
Field or Control |
Description |
---|---|
Date Range |
Enter the date range. |
Date Type |
Displays how you want to view the production schedules. Values are:
|
|
Click to refresh the data if you made any changes to the date range or date type. |
Sel (selection) |
Select the specific production schedule that you want to record completions and scrap. |
OK |
Click this button to return to the Production Selection process page. |
If the system indicates that no current outstanding production schedule quantities exist for this production area/item combination as of the BOM/routing effective date or effective date, you receive a warning message indicating that no outstanding production quantities exist for an area or item.
If you click Yes, the system creates a new production schedule. The system checks for any outstanding production schedules by comparing any unprocessed BCTP detailed transaction logs (BCT_DTLs) (Completed + Scrapped ) quantities and netting them against those matching open production schedules (production end quantity > completed + scrapped quantity) in the system.
The default rate quantity per shift from the production area or item definition appears as Production Rate Quantity. Click OK to accept this quantity or change the quantity to the quantity that you're currently producing.
Recording Completions and Scrap for Production Schedules That Haven't Been Released
You can also record completions and scrap for production schedules that have not been released.
To release Entered production schedules, use the Prod Schedule Status Change page or the Production Status Change process (SFPARELS). This process looks for production schedules that match the date, shift, BOM code, routing code, and primary end item of the selection criteria. The system releases all the production schedules with a status of Entered that match the selection criteria. You can then record completions and scrap for the production schedules.
Firmed production schedules are automatically released during the completions process.
Use the Record Completions/Scrap page (SF_COMPL_ID) to enter completions and scrap information.
In addition, use this page to move end items for production schedules with a single output or multiple outputs.
Navigation:
The process for recording completions and scrap for production schedules is similar to the process used for production IDs. However, there are a few differences:
Completions and scrap are recorded at the last operation sequence only.
You select one of these completions actions:
Field or Control
Description
Completions/Putaway on Save
Use this option to initiate the Completions Update process for the selected production schedule upon saving the page. The production end quantity completed and scrapped information is updated as well as the storage area quantity on hand. All completions processing is performed, including component updates.
Stage Compltns/Putaway on Save
Use this option to run the Completions Update process at a later time.
Use the Record Completions/Scrap page (SF_COMPL_ID) to enter completions and scrap information.
In addition, use this page to move end items for production schedules with a single output or multiple outputs.
Navigation:
To record completions and scrap for production schedules with multiple outputs:
Enter the completed quantity that represents the batch (BOM) production end quantity.
This quantity doesn't represent completed quantities for each output in the Output Details area. You can enter a quantity here or optionally enter the quantity of each output. If you enter specific output completions, the system determines the quantity of the batch completed.
The Op Seq field is unavailable and the last operation step appears.
Note: Because you're completing a production schedule, the Update Prior Operations check box is unavailable, and the first operation step appears by default in the Back Thru Operation field. These fields are display-only and cannot be changed.
Click the Enter Scrap Data link to make corrections to the scrapped component quantities.
Access the Output Details scroll area on the Record Completions/Scrap page.
Enter the completed quantity for each output.
The system calculates the multiple output quantities based on the batch completed quantity from the Record Completions/Scrap page. For example, if you entered a completed quantity of 5 on the Record Completions/Scrap page, the system would calculate each output quantity based on this quantity of 5. However, you can change the completed quantity for any of the outputs on the Output Details scroll area.
Note: If you want to change the production quantities for the batch, which changes the primary and co-product quantities, change the production end quantity for the production schedule on the Production by Area Summary or Production by Area Details pages.
(Optional) Click Add to add recycle or waste by-products.
Select the output type and output item.
Select the operation sequence where the additional by-product is being generated.
Enter the completed quantity, which is the output quantity that you're currently completing.
Enter the output quantity.
This quantity represents the output production end quantity based on per end item or per order.
Click Save to record the completions and scrap.
With production schedules, you can only complete end items at the last operation. When you enter the completed quantity on the Record Completions/Scrap page, the Route-To PID/Stor Locations scroll area becomes available. You use the Route-To-PID/Stor Locations scroll area to route completed end items for production schedules with a single output or multiple outputs.