Defining Attributes in PeopleSoft Supply Chain Management
Before using PeopleSoft Supply Planning, you must define attributes in other PeopleSoft applications within the PeopleSoft Supply Chain Management application suite. This topic details the key setup pages and components and discusses how to:
Set up work center planning attributes.
Define and review manufacturing BOMs.
Define manufacturing routings.
Define item attributes at the business unit level.
Define planner codes.
Establish closure calendars.
Set up stocking periods.
Set up demand priority families.
Define transfer attributes.
Define purchasing attributes.
Define forecast sets.
Define forecast product information.
Create item forecasts.
Apply Security for Business Units and Planning Instances.
A work center can consist of one or more people and machines; it can represent a logical grouping of machines, a department, or a cost center. For a routing, you can assign to each operation or task a work center where the operation or task takes place. You can also assign one or more resources (crew, machine, or tool) to each work center.
You create and maintain work centers and their associated resources, conversion codes, text, locations, departments, and distribution types in the Define Work Centers component. When you add a new work center, or when you change any attribute in an existing work center, the system optionally sends a workflow notification to the roles that you have defined, such as an engineering manager or cost accountant.
Set up PeopleSoft Supply Planning work center options on the Define Work Centers - Planning Opts (define work centers - planning options) page.
PeopleSoft Supply Planning uses manufacturing BOMs for determining material requirements for production. On the Manufacturing BOMs component, you can create and maintain (on a summary level) all components that make up a manufacturing BOM or outsourced material for a group of assembly items or product families in a business unit.
You can create and maintain routings using the Manufacturing Routings component, where you can define the routing code, operations, scheduling options, routing times, conversion costs, routing text, attachments, and the associated tasks, count points, work centers, and resources. You can specify a routing by business unit for any manufactured or purchased item. When you add a new routing, or when you change any attribute in an existing routing, the system sends a workflow notification to the roles—such as engineering manager or cost accountant—that you define.
Use the Define Business Unit Item - Planning page to define business unit items
Navigation:
This example illustrates the fields and controls on the Define Business Unit Item - Planning page: General. You can find definitions for the fields and controls later on this page.
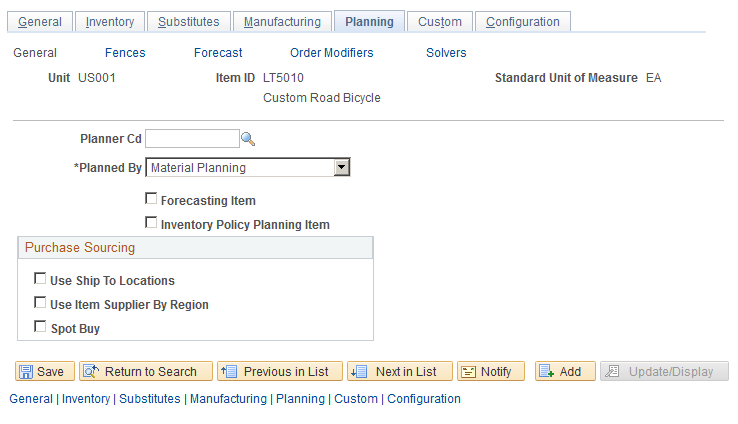
For each item, define information using the Define Items and Attributes - Define Business Unit Item - Planning pages:
On the Planning - General page, define planning information for an item, such as whether the item is planned by distribution planning, master planning, or material planning, or is not planned. You can also define the PeopleSoft Purchasing sourcing option. Options include Use Ship To Locations, Use Item Supplier by Region, or Spot Buy. You can only select one method.
On the Planning - Fences page, define planning time fences, planning message parameters, safety stock and excess stock parameters, lead times, new order fences, and other general information about how you will generate supply for inventory items.
Note: PeopleSoft Supply Planning generates recommendations for new orders, reschedules, or order cancellations and then routes these recommendations to PeopleSoft Inventory, Purchasing, Order Management, and Production Management. In many cases, the volume of changes number in the thousands. To help manage this activity more effectively, the system enables you to define a time fence and filters to control the message review and approval process.
On the Planning - Order Modifiers page, define transfer, purchasing, and manufacturing order quantities, order multiples, yields, and whether to use the purchase order modifier.
Note: For transfers, you can set up order modifiers on the Transfer Attributes page. The system uses the transfer order modifier values that you define on the Planning - Order Modifier page when you do not define values on the Transfer Attributes page. You can select the Include in Planning check box on the page to indicate that sourcing options will be created for this given item and business unit. You can also select to Include in Planning check box on the Transfer Attributes Defaults page.
Note: If you select the Use Purchase Order Modifier check box, the system uses the item's purchasing attributes defined on the Supplier's UOM and Pricing Information page.
For more information about the Planning page, see the documentation — PeopleSoft Managing Items.
Use planner codes to filter information for most pages and processes in PeopleSoft Supply Planning. Define planner codes on the Planner Code page.
The PeopleSoft Inventory closure calendar enables you to specify when the business units are closed for various inventory and purchasing activities. You use the Closure Calendar page to schedule regular (standing) closure days or specific closure periods and associate these closures with shipping, interunit and RMA receiving, and internal warehouse activities. If the installation includes PeopleSoft Purchasing, you can also define calendar closures for purchasing receiving activities.
Set up time-phased safety stock and excess stock levels on the Stocking Periods page. The information that you enter on this page overrides any stocking-level information that you entered on the Define Business Unit Item - Planning: Fences/Lead Time page.
Group similar items to establish a common priority for all items within a single group on the Demand Priority Family page. This setup set enables the system to establish demand priorities in PeopleSoft Supply Planning.
Define item transfer attributes to plan transfer for items between business units. Using the Transfer Attributes page, you can define transfer attributes for individual items. PeopleSoft Supply Planning uses these attributes that you define on the Transfer Attributes page to help fulfill material needs. After you set up transfer attributes, you can use them to set up sourcing template transfer options for an item on the Define Sourcing Templates page.
If you are using PeopleSoft Purchasing, use the Define Items and Attributes - Purchasing Attributes component to enter data that PeopleSoft Supply Planning requires.
On the Purchasing Attributes page, define the lead time and the primary buyer for the purchased item.
On the Item Supplier page, define the suppliers from whom you can purchase the corresponding item.
PeopleSoft Supply Planning recommends this supplier to PeopleSoft Purchasing for each planned order. If you do not specify a supplier for a purchased item, PeopleSoft Supply Planning creates a planned order without a supplier. In this scenario, you can use the purchase order load process to assign a supplier to the item. PeopleSoft Supply Planning ranks multiple suppliers for the same item based on the values that you define in each supplier's corresponding Priority field.
Define a ship-to location that represents an Inventory business unit. When you set up a purchase option, you can define a ship to location as an attribute only if the item has purchasing attributes. If an item has purchase attributes defined but no ship to locations, the system assumes that the item can be ordered at any Inventory business unit.
Whether you forecast products at the Order Management business unit level, forecast items at the Inventory business unit level, or use planning BOMs to forecast at the Inventory business unit level, you must define one or more forecast sets. Use the Forecast Sets page to define different versions of the forecast for PeopleSoft Supply Planning to create what-if scenarios with different versions of the material and capacity plan based on the different forecasts.
You might, for example, have three versions of a forecast: a conservative forecast, a most likely forecast, and an optimistic forecast. For each case, you can define forecast quantities by item. You use forecast sets for product forecasts in order management and item forecasts in inventory.
If you use Demantra Demand Management forecast data, you do not have to define forecast sets, because you obtain the forecasts from PeopleSoft Publish Forecast tables that are available in the Advanced Planning component. Demantra Demand Management provides a flat file (forecast.txt) of forecasts through the Process Integration Pack. Using the PeopleSoft Import Forecast routine, you can import the file into the Publish Forecast tables in PeopleSoft. After the import, the file is available for use by other PeopleSoft modules such as PeopleSoft Supply Planning and Inventory. To access the routine, select
In PeopleSoft Order Management, you can define product forecast information. PeopleSoft Supply Planning uses forecast sets to define different versions of a forecast. You associate products with forecast sets on the Forecast Products page.
Use the Forecast Items page to associate items with forecast sets. You select a forecast set that you want to use in PeopleSoft Supply Planning. You set up forecast sets on the Forecast Sets page to create what-if scenarios with different versions of the material and capacity plan based on different forecasts.
See Forecast Sets Page.
This is an optional step, only if you turn on the Security Option; you have to continue to define security on BU or Planning Instance, or User ID or Permission List.
Financial and Supply Chain Setting for Security allows users to define security rules, which refers to the row level (User ID) or permission list security. User ID and permission list security is defined using the Security Options page.
When security is defined for Business Unit by User ID, only the business unit allowed for this User ID will be displayed in Business Unit prompt. The same is true for Planning Instance. When the security is on for Planning Instance by User ID, only the planning instance defined for this user can be seen in the Planning Instance prompt. Business Unit by Permission List or Planning Instance by Permission List works the same way.
When both Planning Instance and Business Unit are on the search page, only one security would rule the page, and this is the Planning Instance security. Hence, the suggested way for the Setup is to define both Business Unit and Planning Instance security in the Security Option. Business Unit security is used primarily at Define Planning Instance Attribute, for Business Unit Group creation, and for Commit Plan search. In other areas, such as Solve Plan and Refine Plan, Planning Instance’s security is used. It is with the assumption, that when a user defines the Business Unit group, he/she has access to all Business Unit within his/her security setup. When the security setup is changed that would impact the list of Business Unit allowed for this User ID, user should update the Business Unit group and reload of Planning Instance to reflect the change.