Understanding the Supplier Location Hierarchy and Multicurrency Pricing
PeopleSoft Purchasing uses the supplier location hierarchies to determine suppliers and various supplier locations for online requisitions. These hierarchies are also used by the PO Calculations Application Engine process (PO_POCALC) to determine the supplier necessary to create a purchase order and determines how pricing is ultimately derived based on this hierarchy.
This section also discusses how involvement of multicurrencies affects which pricing locations the system obtains. Depending on the setting of the multicurrency flags and which currencies have been set up for the purchasing business unit, requester, supplier location, and pricing locations, PeopleSoft Purchasing performs multicurrency conversions when required.
Here is the setup hierarchy for supplier location and pricing:
Field or Control |
Description |
---|---|
Level 1 |
When defined, the system uses Item Ship To Supplier Locations to determine the priority supplier and the supplier location specified for the item and ship to location. Based on the supplier and supplier location, the pricing location is derived from the Maintain supplier setup. If not defined, it uses level 2 defaulting. |
Level 2 |
When defined, the system uses the Item Region Supplier Locations to determine the priority supplier and the supplier order location specified for the item and region. Based on the supplier and supplier location selected for the region, pricing location is derived based on the supplier and supplier location selected for the region by accessing the location details from the Maintain supplier setup. If not defined, it uses level 3 defaulting. |
Level 3 |
The system selects the supplier based on the Item Supplier setup. When defined, the system uses the Ship To supplier Location to get the supplier order locations to derive the pricing location from the Maintain supplier setup. Ordering locations can be different from the default locations. If not defined, it uses level 4 defaulting. |
Level 4 |
The system selects the supplier based on the Item Supplier setup. When defined, the system uses the Region supplier Location to get the supplier order locations to derive the pricing location from the Maintain supplier setup. Ordering locations can be different from the default locations. If not defined, it uses level 5 defaulting. |
Level 5 |
When defined, the system uses the supplier priorities established in the Item supplier setup to derive the pricing location from the Maintain supplier setup. If the Item supplier setup is the only one defined, the pricing location is always derived from the supplier default location. If not defined, there is no control hierarchy defined. |
You can define various locations for a supplier on the supplier Information - Location page accessed from the Maintain suppliers menu. Each location that you define points to an ordering location and a pricing location.
The Item Ship To Supplier Location that you define on the Item Ship To Locations page is a setup based on the combination of the item and ship to location. This setup prioritizes the suppliers from which the item can be purchased for a ship to location and determines the specific supplier location from which to get a pricing location.
The Item Region Supplier Location that you define on the Item Region Locations page is a setup based on the combination of the item and region. This setup prioritizes the suppliers from which the item can be purchased for a region and determines the specific supplier location from which to get a pricing location. The region is derived from the ship to location on the requisition or staged purchase order's schedule.
The Ship To Supplier Location that you defined on the Ship To Locations page defines all of the suppliers that can ship an order to a particular ship to location and is not item-specific. Each supplier and the appropriate supplier order location appears. When determining the supplier ordering location, the system first references the Item supplier for the priority 1 supplier and then references the Ship To Location page to determine the order location.
The Region Supplier Location that you defined on the Region Locations page defines all of the suppliers that can ship an order to a particular region and is not item-specific. Each supplier and the appropriate supplier order location appears. When determining the supplier ordering location, the system first references the Item supplier for the priority 1 supplier and then references the Region Location page to determine the order location.
The Item supplier setup dictates only supplier priorities, and establishes supplier UOM pricing for their pricing locations. This setup does not dictate supplier order locations for the item. Supplier ordering locations default from one of the hierarchies discussed previously or, if no higher level defaults are found, from the default location defined on the Maintain supplier - Location page. The item supplier relationship that you defined on the Purchasing Attributes - Item Supplier page defines the pricing location for the supplier's default location.
Regardless of the setup that you implement, the pricing location the system uses is ultimately derived from the supplier ordering location. In addition, you can override anything that appears by default on the requisition. To ensure the override is carried to the purchase order, make sure that the Override Suggested supplier check box is clear on the Maintain Requisition - Requisition page and the Let POCalc Override supplier check box is clear on the Selected Item Details page accessed from the Sourcing Workbench.
By selecting this check box on the requisition, you enable the purchase order to be created using the same hierarchy and ignore all of the overriding information that the user enters on the requisition. Once the purchase order is created, the buyer can still override this information prior to dispatching.
For example, suppose that the user changes the supplier or supplier location that appear by default on the requisition, and the override suggested supplier check boxes are selected, the purchase order is created following the hierarchy. This overrides the user suggested supplier or supplier location on the requisition.
The purpose of defining the areas described here is to enable more control and automation in the system, thereby reducing the level of repetitive effort by the user. If you want a more automated system, a greater effort is required for the initial setup. This setup is a one-time effort that can increase the utilization of time-saving batch processing capabilities by the system. These setups require occasional updating as supplier changes occur.
Note: These setup scenarios are based on normal day-to-day practices. Exceptions are handled through manual intervention at the requisition, sourcing, or the purchase order level.
Establishing Item supplier relationships associated with a ship to location or region provides the highest degree of control. These relationships are specific to the item and the ship to location or region, and enable definition of the supplier priority and supplier order location at a more granular level.
The ship to location is the most specific designation, which overrides both the Item Region Supplier Location and the Item supplier priorities and location. Grouping ship to locations into regions provides the ability to override the Item supplier prioritization and default supplier order location at the intermediate Item Region Supplier Location level. Both of these options, add flexibility to the default supplier selection hierarchy.
Defining item ship to vendor locations provides the highest degree of control. This location-pricing relationship is specific to the item and ship to location. You can specify a multitude of ship to locations for one item and define different supplier priorities for the same item based on ship to locations. Indeed, this can require a large effort depending on the quantity of items and ship to locations that you have. However, time spent on this one-time setup saves time and repetitive effort in the future.
When you create the online requisition or when you source an existing requisition, the system references the item and ship to location of the requisition and accesses the item ship to location to get the priority 1 supplier and its supplier location. The system derives the pricing location that you defined for the Supplier location. It then looks to the item-supplier relationship to access the pricing for the derived pricing location.
This diagram illustrates this default hierarchy:
This diagram illustrates this default hierarchy:
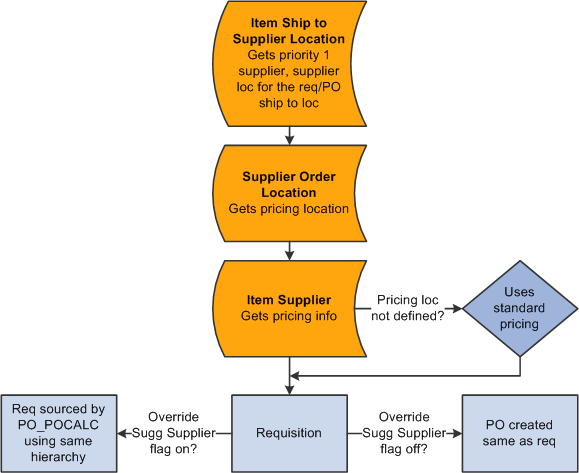
A Ship to location can be associated to a region, allowing for management of similar ship to locations at the region level. Item region supplier locations provide a location-pricing relationship that is specific to the item and region. You can associate many regions to an item and define different supplier priorities for the same item based on region. This level of flexibility in supplier prioritization ensures the right suppliers are assigned to the purchase orders, without driving all of the maintenance down to the item ship to location.
When you create the online requisition or when you source an existing requisition, the system references the ship to location to determine the appropriate region. If the ship to location is assigned to a region and a lower level override for the Item Ship To Location does not exist, the system will accesses the item region supplier location to get the priority 1 supplier and its supplier location. The system derives the pricing location that you defined for the supplier location. It then looks to the item-supplier relationship to access the pricing for the derived pricing location.
Establishing a supplier order location relationship with a ship to location or region provides an intermediate level of control (less control) in the supplier hierarchy. These relationships associate either a ship to location or a region to a supplier order location to override the supplier's default order location.
With these additional levels of the hierarchy, the priority supplier is determined from the Item supplier definition. Once the Supplier ID is identified, the determination of the supplier order location begins with the ship to supplier location, then looks to the region supplier location and finally the supplier default location, as defined on the Maintain suppliers component.
The next level of control is provided by defining the supplier order location for each ship to location. The ship to location is based on the requester and buyer setups that include ship to location defaults for the requisition and purchase order.
One supplier ordering location for each supplier is defined for each ship to location. You can have more than one supplier for each ship to location but only one order location per supplier. This default system is not item-specific, but rather ship to location specific. This setup can require a large effort depending on the quantity of suppliers and ship to locations that you have.
As you create an online requisition or when you source an existing requisition, the system references the item-supplier relationship to get the priority 1 supplier. The system then accesses the ship to location to determine the order location for the priority 1 supplier and uses the order location to derive the pricing location. The system then retrieves the pricing for the derived pricing location from the Item Supplier setup.
This diagram illustrates the default hierarchy for defining the ship to supplier order location for each ship to location:
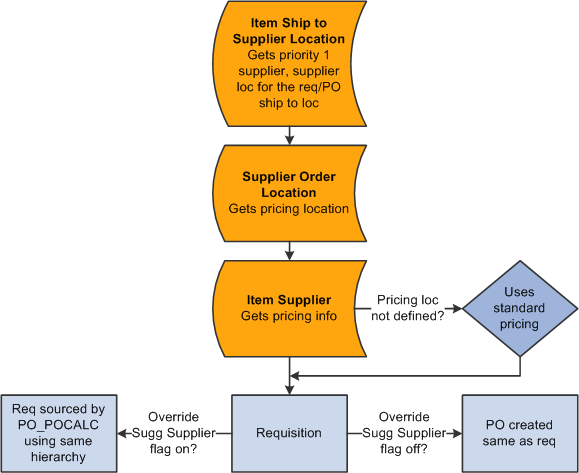
Using the procurement region enables you to group ship to locations for additional defaulting purposes. By defining the Supplier order location for each region, you can override the default supplier order location for additional control, without maintaining these overrides for every ship to location in the buying organization.
One supplier ordering location for each supplier can be defined for each region. You can have more than one supplier for each region but only one order location per supplier. This default system is not item-specific, but rather region specific.
As you create an online requisition or when you source an existing requisition, the system references the item-supplier relationship to get the priority 1 supplier. Once the system determines the ship to location's region, it accesses the region supplier location definition to determine the order location for the priority 1 supplier and uses the order location to derive the pricing location. The system then retrieves the pricing for the derived pricing location from the Item supplier setup.
The least amount of control and setup effort occurs in the item-Supplier setup scenario. In this case, you only define supplier priorities and Supplier UOM pricing for the pricing locations of each established supplier. If neither item ship to location nor ship to location is defined, the system uses the priority 1 supplier default location to derive its pricing location. Any other supplier locations and pricing locations, if defined, are not considered. It then goes back to the item-supplier relationship to reference the pricing for the derived pricing location. This hierarchy applies to purchase orders created online.
This diagram illustrates the default hierarchy for defining item-Supplier relationships:
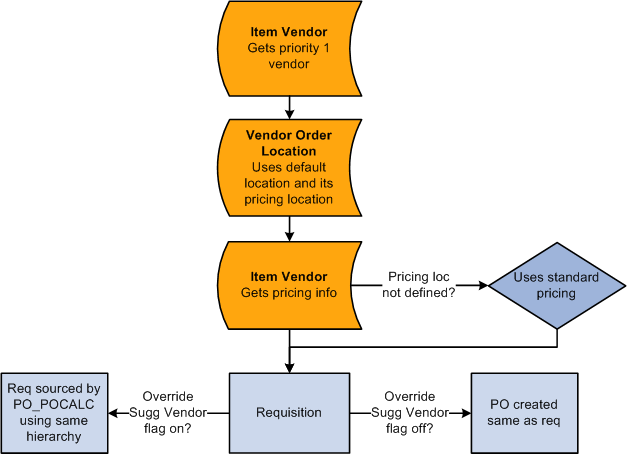
A zero-level of control results from not defining any of these setups, including no item-supplier relationships. In this scenario, no supplier automatically appears on the requisition, so the standard price is used. You can enter a suggested supplier, but the standard price remains. During the requisition selection process, you can select a supplier if the field is blank or change the supplier that the requester suggested. Because none of the setups were defined, the purchase order is built with the same pricing as the requisition or any buyer pricing updates are performed through requisition selection. Failure to establish item-supplier relationships prevents the creation of contracts. In the same scenario, purchase orders created online use the standard price as well.