Understanding Scheduled Preventive Maintenance
This section lists common elements and discusses:
Benefits of scheduled preventive maintenance.
Preventive maintenance process flow.
Field or Control |
Definition |
---|---|
Start Date and Service Order Date |
The required start date of the preventive maintenance service order. The system calculates this value by adding the specified service frequency to the date on which the previous preventive maintenance service order was closed. The system also takes the service level into account. For example, if the customer offers service Monday through Friday only, the start date would not be on a Saturday or Sunday. |
Creation Date |
The service order creation date (when the preventive maintenance service order will be generated by the Application Engine process). |
Scheduled preventive maintenance is a collection of services that are performed regularly on products to prevent unexpected product failure. These preplanned services, such as running performance checks and tune-ups or checking and replacing worn parts, help sustain the performance and extend the longevity of products. The result is a reduction in ownership costs to both service providers and customers.
The preventive maintenance feature in PeopleSoft Integrated FieldService enables you to:
Set up the system at the business unit level to automatically generate service orders for preventive maintenance services on installed products that are covered by an agreement.
These preventive maintenance service orders are processed the same way as other service orders (from assigning a technician to processing service activities and completing the service order).
Preview scheduled preventive maintenance services and make changes as necessary.
Review the preventive maintenance history for installed products.
For any installed product that is eligible for a preventive maintenance service, the system creates a preventive maintenance entry. This entry tracks the preventive maintenance process life cycle of each installed product. The preventive maintenance entry updates each time that the status of the corresponding service order changes during the process. When the entry is marked as completed at the end of the cycle, the system reevaluates the associated installed product for another preventive maintenance cycle. If the installed product passes the evaluation, the system automatically generates another entry for it, which starts a new preventive maintenance cycle.
Automatically generate service orders for preventive maintenance, calculate the service order start date and time based on agreement entitlements, and assign service orders to appropriate technicians.
The system automatically assigns technicians only if you have auto assignment configured. Dispatchers and field service specialists can use the dispatch board to view these service orders and manage technician assignment schedules.
These terms are used frequently in discussions of scheduled preventative maintenance:
Term |
Definition |
---|---|
Valid agreement |
An agreement is considered valid if the line status is set to Active, and the current system date is between the agreement line's start and end dates. |
Preventive maintenance entry |
A preventive maintenance entry is a row in the Preventive Maintenance History table (RF_INST_PROD_PM) for an installed product that passes the validation test and that is qualified for the preventive maintenance process. Preventive maintenance entries are used to track the statuses of preventive maintenance service orders. The system creates one preventive maintenance entry per installed product per service per agreement. An installed product can have more than one entry simultaneously if it is associated with multiple preventive maintenance services, or if it is associated with a service that is made available to more than one agreement line or agreement. |
Next preventive maintenance due date |
This is the date when the next preventive maintenance service for an installed product is scheduled to start. When the system initially inserts a preventive maintenance entry for an installed product, the system uses this equation to calculate the date: (Next Preventive Maintenance Due Date) = (Installed Product Installation Date) + (Frequency) The system then verifies whether the calculated date falls between the start and end dates of the agreement line. If the calculated date is earlier than the agreement line start date, the system schedules the preventive maintenance so that the creation date is the system date. The service order date is the creation date plus the lead time. The system also takes into account the service level when making this calculation. For subsequent preventive maintenance entries that are created for this installed product, the system uses this equation to calculate the next preventive maintenance due date: (Next Preventive Maintenance Due Date) = (Service Order Completion Date) + (Frequency) |
Preventive maintenance consits of several steps.
Image: Preventive maintenance process flow
This flowchart describes the preventive maintenance process. Each step of the process is discussed in the sections following the chart.
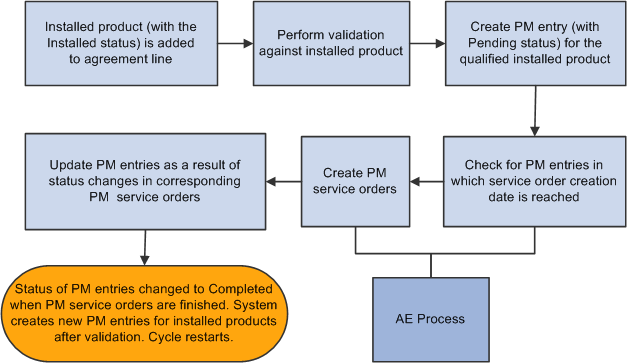
Validation of Installed Products for Preventive Maintenance
The preventive maintenance process begins when an installed product is added to an agreement line that is defined for a preventive maintenance service type and is saved.
The installed product is then evaluated for preventive maintenance eligibility by using the these validation rules:
The status of the installed product is set to Installed.
An asset tag or serial number exists in the installed product.
The installed product is covered by a valid agreement that is associated with a preventive maintenance service, and its next preventive maintenance due date (which is calculated by the system) falls between the start and end dates of the agreement line.
The installed product does not already have a preventive maintenance entry with a status set to Pending for the same preventive maintenance service for which the system considers adding a new preventive maintenance entry.
For every installed product that passes the evaluation, the system inserts a preventive maintenance entry with a status of Pending in the Preventive Maintenance History table.
Creation of Preventive Maintenance Entries for Qualified Installed Products
The system creates preventive maintenance entries for installed products that are eligible for preventive maintenance. It uses preventive maintenance entries to manage the life cycle of corresponding service orders throughout the process (from creation to completion). Based on the information in pending entries, service orders are generated through an Application Engine process. From this point on, the system tracks all preventive maintenance service orders by updating their associated preventive maintenance entries when statuses change in respective preventive maintenance service orders.
A preventive maintenance entry, which appears on the Preventive Maintenance Detail page, is initially created with the these properties:
A status set to Pending.
A value in the Start Date field that is equivalent to the next preventive maintenance due date.
If this preventive maintenance entry is the first one created for the installed product, the service order start date equals the installed product's installation date plus the frequency.
If the calculated service order start date precedes the start date of the selected agreement line, the system schedules the preventive maintenance so that the creation date is the system date. The service order date is the creation date plus the lead time.
For example, suppose that a product was installed on January 1, and this installed product was added to an agreement on February 21. With the frequency set to once per month, the service order start date of this preventive maintenance entry becomes February 21. In this case, the system increments the service order start date by the frequency to March 21 and verifies that this date is covered by the agreement. No preventive maintenance entries are created if this date goes beyond the agreement end date.
Note: If you have enabled the automatic calculation of service order dates and times in the system, all preventive maintenance-related date calculations are based on the service level, response, and restore times of the associated agreement. This means that only contractually defined working days are considered in the calculation. Any calculated service order start date that falls on a nonworking day is automatically rescheduled to the next available working day.
See Understanding Automatic Calculation of Dates and Times for Service Orders.
A service order number appears when the Application Engine process creates a service order.
Note: You can modify information (including the business unit, agreement details, service order start, and creation dates) in the preventive maintenance entry as long as that information has a status set to Pending.
Validation of Preventive Maintenance Entries for Service Order Creation
PeopleSoft Integrated FieldService uses an Application Engine process to identify installed products for which preventive maintenance service orders must be generated.
When the process runs, it looks up all installed products that:
Are set to a status of Installed.
Are controlled by an asset tag or serial number.
Are covered by a valid agreement.
Have a pending preventive maintenance entry.
The process compares the current system date with the service order creation date (that is, the next preventive maintenance due date minus the lead time defined in the Service component) in each of these entries. If the system date is later than or equal to the service order creation date, a preventive maintenance service order is generated.
If there are preventive maintenance entries in which the service order creation date is past due (which occurs if the process has not run as scheduled for some reason), the system pushes out the service order creation date for these preventive maintenance entries by one day (from the system date). This delay enables the entries to still be evaluated for service order creation.
Once the service order is created, the system populates the Required Start Date field of the first service order line with the start date of the preventive maintenance service order. If you have enabled the automatic calculation of service order dates and times feature, the system takes the agreement entitlements (namely the specified service level, response, and restore times) into account when it calculates the required start date for the preventive maintenance service order. In addition, the system populates the service order number in the corresponding preventive maintenance entry and changes the entry status to Created.
Change of Status in Preventive Maintenance Entries
The status of a preventive maintenance entry changes as a result of a status update in its corresponding service order. For example, when a preventive maintenance service order is automatically created and its status is set to Open, the status of the associated preventive maintenance entry is set to Created.
This table summarizes the conditions under which status changes in preventive maintenance entries occur:
Condition |
Service Order Status Changes To |
Preventive Maintenance Entry Status Changes To |
Other Updates in the Preventive Maintenance Entry |
---|---|---|---|
A preventive maintenance entry is created. |
Not applicable (NA) |
Pending |
NA |
A service order is generated. |
Open |
Created |
The service order number is populated on the preventive maintenance entry. |
A technician is at the customer site awaiting customer response or is on hold for parts. |
On Site, Hold - Customer, Hold - Part (service order line status) |
In Progress |
NA |
A service order is completed. |
Complete |
Completed |
The system updates the Date field in the Preventive Maintenance History group box on the Preventive Maintenance Detail page with the service order completion date. A new preventive maintenance entry (with a status set to Pending) is created if required validations are passed. |
A service order is canceled. |
Canceled |
Canceled |
NA |
Completion of the Preventive Maintenance Process Life Cycle
The preventive maintenance process is approaching the end when the header status of the preventive maintenance service order changes to Completed. This status change takes place automatically when all associated service order activities have a status set to Completed, Canceled, or Closed.
When that happens, the system verifies that the installed product that is selected for this service order has a status of Installed and is covered by a valid agreement that is associated with a preventive maintenance service (in which the Preventive Maintenance check box of the service type for this service is selected in the Service Type record). Next, the system locates the corresponding preventive maintenance entry, which has the number of this completed service order and has a status of Created or In Progress. The system updates the date with the service order completion date and changes the status to Completed.
The ending of one preventive maintenance process may or may not mean the beginning of another one. The system uses the next preventive maintenance due date to decide whether the preventive maintenance process should continue for any installed product. As the status of a preventive maintenance entry is set to Completed, the system calculates the next preventive maintenance due date and verifies whether the date is covered by a valid agreement in which the corresponding preventive maintenance service is defined. If it is covered by the agreement, the system generates a new pending preventive maintenance entry in the Preventive Maintenance History table, and the next preventive maintenance due date is calculated by using the service order completion date plus the frequency. Additionally, the system looks for renewed agreements.
The preventive maintenance process discontinues if the next preventive maintenance due date that is calculated goes beyond the agreement end date.
The preventive maintenance entry status changes to Canceled if the associated preventive maintenance service order is canceled. In this case, a new pending preventive maintenance entry is generated with no service order number, and the next preventive maintenance due date is calculated as the service order cancellation date plus the frequency. However, if you cancel the preventive maintenance entry for the installed product, the preventive maintenance process cycle for the installed product stops. To restart the process, you must use the Preventive Maintenance Detail page to manually enter a preventive maintenance entry for the installed product with a status of Pending.