Conventional Workflow
Information that is critical to a workflow process can be defined and stored in database tables, enabling a computer system to automate the flow of information and tasks. This automation minimizes the reliance on physical meetings to enter redundant data and to physically exchange paper. For example, using an automated workflow process, purchase orders and work orders can be processed to completion without a single printout. The defined workflow information might include order activity rules, workflow steps, and expenditure authorization requests, all of which can be routed automatically using email.
The following scenario demonstrates the savings in labor and time that can be achieved when workflow technology is applied to a typical business process like procurement.
This graphic shows the paper trail of a typical procurement process that is not automated. The step-by-step tasks of this conventional workflow and the total time required to complete the procurement process are explained in the following graphic.
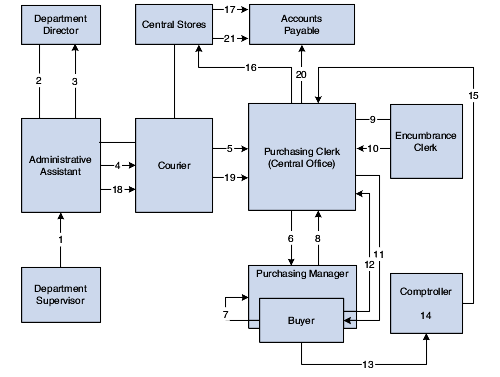
The department supervisor at a remote office fills out a requisition form to request goods.
The administrative assistant processes the requisition form, looks through two catalogs, and locates the items. The assistant then fills out the paper portion of the requisition and walks it to the department director.
The department director reviews the requisition, signs it, and puts it in an Out basket.
The administrative assistant retrieves the requisition and places it in a courier pack to the central office.
A courier drives to the remote office, picks up the courier pack, and delivers it to the purchasing clerk at the central office.
The purchasing clerk reviews the requisition, audits central stores, and sends the requisition to the purchasing manager if the item is in stock, or to the buyer if the item is not in stock.
The buyer reviews the document, selects the supplier, calls for a quote, and passes the requisition to the purchasing manager.
The purchasing manager reviews, signs, and places the requisition in an Out basket.
The purchasing clerk retrieves the requisition and passes it to the encumbrance clerk.
The encumbrance clerk reviews the items, assigns account codes, and checks the budget. If funds are available, the requisition is passed back to the purchasing clerk.
The purchasing clerk sends the requisition to the comptroller if the item is in central stores, or to the buyer if it is not in stock and must be bought and delivered to central stores.
The clerk retrieves the purchase order and delivers it to the comptroller or buyer.
The buyer consolidates the requisition into a single purchase order per vendor and places the order in the Out basket for delivery to the comptroller.
The comptroller reviews and signs the purchase order. At this step, the routing can take longer, based on the amount of the request and the level of authorization of the person approving the purchase.
The clerk retrieves the document and places it in interoffice mail. Another day passes.
Using interoffice mail, a multipart document arrives one day later in the purchasing department. The purchasing clerk tears out the white copy and sends the rest of the multipart form to central stores.
The purchasing clerk logs and files the white copy.
The central stores clerk retrieves the item from the shelf, tears out the pink copy, places it in the accounts payable stack, and ships the item and the remaining copies to the remote office.
The administrative assistant receives the item, tears out, logs, and files the blue copies, and places the green receiving and yellow accounts payable copy in a courier pack to go back to the central office.
A courier retrieves the pack and returns the green and yellow copies to the central office.
The purchasing clerk attaches the white original and green receiving copies to each other, puts them in the file, and sends the yellow copy to accounts payable.
The accounts payable clerk receives the invoice from central stores, retrieves the open yellow receiver copy from the file, and matches and enters the voucher.
Total time (in minutes) per item if the item is not in stock: 172.5
Total time (in minutes) per item if the item is in stock: 147.5