Setting Up Basic Bulk Item Information
Access the Item Master Revisions form.
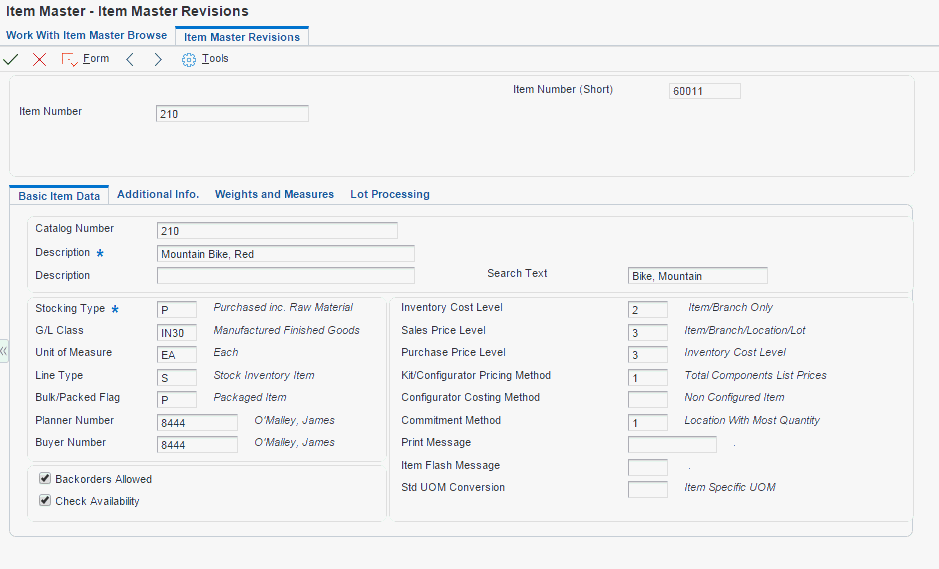
Complete these fields on the Item Master Revisions form:
Item Number
Description
Stocking Type
G/L Class
Line Type
Bulk/Packed Flag
Complete these optional fields:
Catalog Number
Search Text
Unit of Measure
Inventory Cost Level
Sales Price Level
Purchase Price Level
Item Number (Short)
Select these options:
Backorders Allowed
Check Availability
Click the Additional Info tab.
Select the appropriate option to rank the item as A, B, C, or D under each of these headings and click OK:
Sales
Margin
Investments
- Item Number (Short), Item Number, and Catalog Number
Enter an identifier for an item.
- Search Text
Specify how the system searches for an item. The entry should be specific and descriptive of the item. Type the words in the order a user is likely to enter them.
In single-byte environments, where computer storage space can hold only Latin-based language character sets, the system inserts the first 30 characters from the item's description if you do not enter search text.
In double-byte environments, where computer storage space can hold more complex language character sets (in languages such as Japanese, Chinese, and Korean), you must complete this field. It is a single-byte field that you complete with single-byte characters to phonetically represent the item description (which can be single-byte, double-byte, or both).
- Stocking Type
Enter a UDC (41/I) that indicates how you stock an item, for example, as finished goods or as raw materials. These stocking types are hard-coded and you should not change them:
0: Phantom item
B: Bulk floor stock
C: Configured item
E: Emergency/corrective maintenance
F: Feature
K: Kit parent item
N: Nonstock
The first character of Description 2 in the UDC table indicates if the item is purchased (P) or manufactured (M).
- G/L Class
Enter a UDC (41/9) that indicates which general ledger accounts receive the dollar amount of inventory transactions for this item.
- Unit of Measure
Enter a UDC (00/UM) that indicates the primary unit of measure for the item. The primary unit of measure must be the smallest unit of measure in which you handle the item.
This is the primary stock accounting unit (PSAU) of measure that the system uses to store all inventory. If you change the primary unit of measure, the conversion factors in the item-level conversion table are no longer valid.
The default value for this field is the unit of measure that you specify for the item on Item Master form.
- Line Type
Enter a code that controls how the system processes lines on a transaction. It controls the systems with which the transaction interacts, such as General Ledger, Job Cost, Accounts Payable, Accounts Receivable, and Inventory Management. It also specifies the conditions under which a line prints on reports, and it is included in calculations. Codes include:
S: Stock item
J: Job cost
N: Nonstock item
F: Freight
T: Text information
M: Miscellaneous charges and credits
W: Work order
- Bulk/Packed Flag
Enter a code that indicates if the item is a bulk liquid product. If it is a bulk product, you must perform temperature and density/gravity conversions. To record the movement of bulk products, you must use forms designed specifically for bulk products. If you try to record movement using standard inventory forms, the system prevents the movement. Values are:
P: Packaged
B: Bulk liquid
If you leave this field blank, the system uses P.
- Backorders Allowed
Specify whether to allow backorders for this item. You can allow backorders by item using the Item Master (P4101) or Item Branch/Plant (P41026) programs, by customer using the Customer Billing Instructions program (P03013), or by branch/plant using the Branch/Plant Constants program (P41001).
- Check Availability
Specify whether the system performs availability checking. You might want to select availability checking for certain items. For other items, if you assume that an adequate supply is available, leave availability checking disabled.
- Inventory Cost Level
Enter a code that indicates whether the system maintains one overall inventory cost for the item, a different cost for each branch/plant, or a different cost for each location and lot within a branch/plant. The system maintains inventory costs in the Inventory Cost table (F4105). Codes are:
1:: Item level
2: Item/Branch level
3: Item/Branch/Location level
- Sales Price Level
Enter a code that indicates whether the system maintains standard sales prices for an item, different sales prices for each branch/plant, or different sales prices for each location and lot within a branch/plant. The system maintains sales prices in the Base Price file (F4106). Valid codes are:
1: Item level
2: Item/Branch level
3: Item/Branch/Location level
- Purchase Price Level
Enter a code that indicates where to retrieve the purchase price for an item when you enter a purchase order. Codes are:
1: Use the supplier/item price from the Purchase Price table (F41061).
2: Use the supplier/item/branch price from the Purchase Price table (F41061).
3: Use the inventory cost from the Inventory Cost table (F4105). This cost is based on the inventory cost level and the purchasing cost method you specify for the item.
The first two codes are applicable only if you set up supplier costs in the JD Edwards EnterpriseOne Procurement system. If you do not set up supplier costs, the system uses the inventory cost as the default for the purchase order.