Overview of Depot Repair
Use the Depot Repair functionality to repair and return broken and serviceable customer products and parts.
Manage Depot Repair page
The Manage Depot Repair page in Service Logistics enables you to manage the complete end-to-end work flow of a repair depot. It gives you access to and visibility of all the existing and ongoing RMAs in a depot repair organization. The page also displays depot repair RMAs for assets that have passed or will pass through the selected inventory organization in the process of getting repaired.
Depot Repair Workbench
The Depot Repair Workbench enables you to manage the repair and return of a single repair RMA or broken product. It provides the service history, logistics, asset, repair order and service request information for that product. It gives you access to the repair technician's debrief and lets you create and edit charges for that particular repair order. Support engineers can open the Depot Repair Workbench from the repair RMA return line in the Service Request Part Details tab. They can see the status of the repair, the logistics, asset details, estimates, and charges. This helps them to provide updates on the status of the repair to the customer.
See the diagram below to understand how the depot repair solution leverages existing Fusion Service, SCM Cloud and Service Logistics functionality to manage the entire repair and return process from service request and Return Material Authorization (RMA) creation through repair execution to shipping and billing.
How does the depot repair process work?
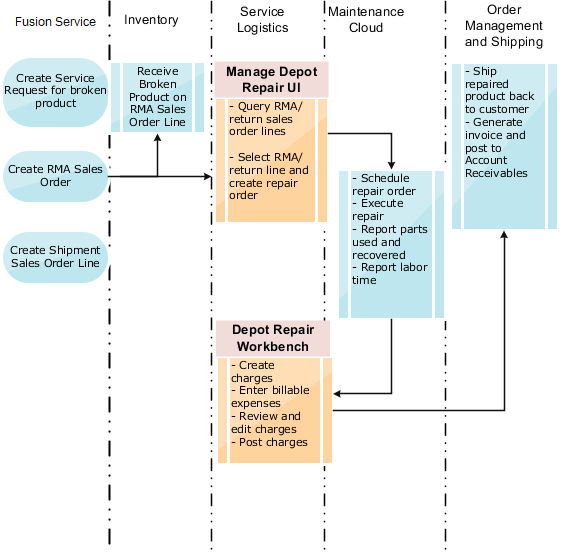
-
In Fusion Service, customers report a product issue through the customer service and support organization. A support engineer creates a service request for the broken part and verifies the customer's warrant or service contract. The support engineer then diagnoses the issue and if it requires depot repair, creates the RMA Sales Order and sends the RMA number to the customer. Simultaneously, the support engineer also creates the corresponding shipment order line.
A repair RMA can also come from Order Management or created in electronic interfaces. If the RMA is created in Order Management, the order line type on the RMA created must be associated with a Service Logistics service activity code of type Return and which is tied to the depot repair logistics business process.
-
The return and shipment lines are linked for processing so that Installed Base and the subscription contract are updated when the broken product or part is received and the repair or replacement is shipped. When the shipment order line is created for the repaired part, the source organization defaults from the RMA's destination organization. Note that the part is sourced from the repair center shipping dock and not from the parts supply chain. The shipment item defaults from the RMA item. The shipment service activity code defaults to the first shipment SAC that's set up in the Depot Repair Logistics business process.
-
Depot repair managers will the query all the RMAs in their depot repair inventory organization. Once the broken part is received in Inventory and the repair work is scheduled to begin, the Depot Repair Manager creates the repair work order using the appropriate work definition.
-
The depot repair manager then assigns the work order to the repair technician.
-
Depot repair technicians get their work from the dispatch list.
-
Depot repair technicians repair the part and record their debrief using the Maintenance Management pages. The technicians record the time spent on the work and the spare parts they used or recovered. Although Resource Activity isn't a required field, you must define a resource activity to create charges in the Depot Repair Workbench.
-
The Depot Repair Manager will click the Create Charges button in the Depot Repair Workbench for the selected RMA line and create the debrief and charges records for the maintenance work order. The labor, parts, and expenses debrief is now visible in the Depot Repair Workbench.
-
The Depot Repair Manager can edit and adjust these charges if required. After that, the Depot Repair Manager will post these charges to create bill-only sales order lines.
-
The shipment order details are then used in Order Management to ship the repaired part to the customer and generate the sales invoice.
Associating Projects to Depot Repair Work Orders
If you opt in to the Project-Driven Supply Chain feature in your Manufacturing and Supply Chain Materials Management offering, you can associate project details to your depot repair maintenance work orders. Charges for work orders with associated projects are posted as project expenditures.
Managing Complex Depot Repair and Return Logistics
In some instances, the broken part is transferred or moved across several locations before it's repaired and sent back to the customer. For example, the customer might return the broken part to the local warehouse from where it's transferred first to a distribution center and then to the actual repair depot. After the asset is repaired, it might be shipped back to the local warehouse or directly to the customer. In Service Logistics, you'll create transfer orders to move the broken asset across multiple locations. The transfers orders are created in the Depot Repair Workbench and linked to the Depot Repair RMA. Support engineers can directly access the Depot Repair Workbench from the Service Request Details page and track the movement of the broken asset through it's life cycle. In the Manage Depot Repair page, transfer orders linked to the depot repair RMA are also factored in when a query is run to retrieve all the RMAs for an inventory organization.
Create Multiple Depot Repair Work Orders for a Single RMA
You can also create multiple depot repair orders for a single RMA. You might need to do so in the following scenarios:
-
When there are mistakes in an existing work order that need to be corrected, for example, overreported labor hours. In this scenario, you can create a new depot repair work order even after the RMA and shipment sales order lines are complete.
-
To manage work and costs at multiple locations in a complex depot repair supply chain.
You can see the multiple work orders when you query the RMA order line in the Depot Repair Workbench. The most recent work order is displayed in the Manage Depot Repair page.
Service Activities for Depot Repair
You must set up service activities for your depot repair return and order line in the Manage Service Activities page. Service Logistics provides two predefined business process that are used for depot repair activities:
-
Depot Repair Logistics: Use this business process to set up service activities for a depot repair return and order line. These SACs should be set up with a Zero Charge attribute as these lines are for the return and shipment of a customer owned product or part. Use an SAC tied to this business process when you're adding parts, that need to go for depot repair, to a service request. You can create the RMA and the corresponding shipment order line at the same time.
-
Depot Repair: Use this business process to set up service activities for depot repair debrief. The service activity code must also be mapped to the resource activity code used in the repair work order. You'll use this to add the labor and parts that were used during repair.
How are Taxes Calculated During the Pricing of Service Charges?
Service charges are created when the depot repair debrief lines are created in Service Logistics. Specifically, Service Logistics creates sales orders so that the estimated taxes aren't recalculated by Order Management. The official taxes are calculated in Receivables, which uses the tax determinants passed from Service Logistics to Order Management during pricing.
You'll define tax determinants for transactions, exemptions, products, and invoice details that Fusion Tax passes to Pricing.
Tax Determinant | Header/Line | Tax Determinant Inputs |
---|---|---|
Entity Code | Header | Order |
Entity Class Code | Header | SALES_TRANSACTION_TAX_QUOTE |
Entity Type Code | Header | ORDER_CREATED |
Internal Organization ID | Header |
The internal organization ID is the business unit on the debrief header. Depot Repair: Defaults from RMA sales order line and can't be changed. |
Transaction ID | Header | Debrief Header ID |
Transaction Date | Header | Sysdate (today’s date) |
Transaction Currency Code | Header | null |
Legal Entity | Header | Business unit’s legal entity |
Transaction Number | Header | Debrief Header ID |
Transaction Business Category | Line | null |
Transaction ID and Transaction Line ID | Line | Debrief Header ID |
Line Level Action | Line | CREATE |
Transaction Line Type | Line | ITEM |
Transaction Line Date | Line | Sysdate |
Transaction Line Currency Code | Line | null |
Line Amount | Line | zero |
Unit Price | Line | zero |
Transaction Line Quantity | Line | quantity on debrief line |
Exemption Control | Line | S (Standard) |
Exemption Certificate Number | Line | null |
Product ID |
Line | Item ID from debrief line (parts, labor, expense, fixed charge) |
Product Org ID |
Line | From debrief line:
|
UOM Code |
Line | Debrief line |
Ship-to Party ID |
Line | Customer from Debrief header |
Bill-to Party ID |
Line | Customer from Debrief line (or header) |
Ship-to Party Site ID |
Line | Depot Repair: Bill-to address |
Bill-to Party Site ID |
Line | null |
Ship-to Account Site Use ID |
Line | null (as ship-to account isn't captured) |
Bill-to Account Site Use ID |
Line | Derived from account and bill-to address (account site) entered on the debrief line (or header) and the usage bill-to. |
Tax Determinants | Example | Tax Determinant Type |
---|---|---|
Taxation Country | United States | Transaction |
Document Fiscal Classification (Document Subtype), such as accounting, taxable goods, standard taxable services | Document subtype: null (accounting, taxable goods, and standard taxable services) | Transaction |
First Party Tax Registration, based on registration type, legal reporting unit, tax regime code, tax | 4567890 (registration type, legal reporting unit, tax regime code, and tax) | Transaction |
Third Party Registration Number | null | Transaction |
Transaction Business Category, such as intercompany transaction, trade management | Sales Transaction (Intercompany, Transaction, Trade Management) | Transaction |
Tax Classification Code, such as AT VAT standard rate, AT VAT zero rate | VAT20 (VAT Standard Rate, AT VAT Zero Rate) - appears in Pricing Components UI | Transaction |
User Defined Fiscal Classification | null | Transaction |
Tax Exemption, such as standard or exempt | Standard (Standard or Exempt) | Exemption |
Tax Exemption Reason Code, such as hospital, manufacturer, resale, education | null (hospital, manufacturer, resale, education) | Exemption |
Tax Exemption Certificate Number | null | Exemption |
Product Category, such as cargo transport, professional services, services, software maintenance | null (cargo transport, professional services, services, software maintenance) | Product |
Product Type, such as goods (parts and fixed charges) or services (labor and expenses) | Goods (parts and fixed charges) or Services (labor and expenses) | Product |
Product Fiscal Classification | - | Product |
Intended Use | CPO-INTD1 | Product |
Tax Invoice Number and Date | null | Tax Invoice Details |