Overview of Manufacturing Plants
A manufacturing plant is a type of inventory organization in which the manufacturing of a product is carried out. Manufacturing plants are categorized as:
-
In-house manufacturing
-
Contract manufacturing
Using the Setup and Maintenance work area, an SCM implementor sets an inventory organization either as an in-house manufacturing plant or a contract manufacturing plant in the Manage Inventory Organization Parameters page. Further, using the Manage Plant Parameters task, the parameters are set which influence the nature of the plant.
To know more about this, refer to the Implementing Manufacturing chapter in the Implementing Manufacturing and Supply Chain Materials Management guide.
Manufacturing plants are made up of work areas, which comprise work centers, resources, and resource instances. Here's an illustration:
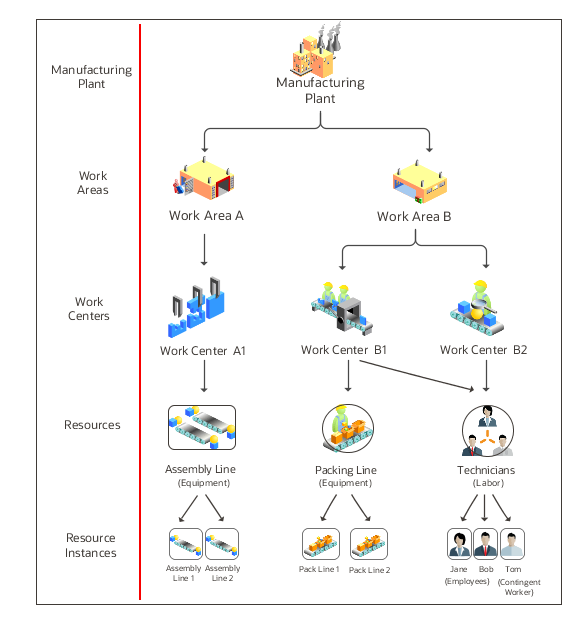
Figure 1 An illustration of a manufacturing plant.
Overview of the Steps to Set Up Your Manufacturing Plant
As a manufacturing engineer, you must set up the manufacturing plant that's used by a production supervisor or a production operator for their day-to-day manufacturing tasks. Here's how you set up your manufacturing plant:
-
Create work areas.
A work area is a specific region in the manufacturing plant where you execute production activities.
-
Create resources.
Resources are people, equipment, and tools allocated to a work center.
-
Create work centers and associate each of them with an appropriate work area.
Work centers are specific production units that consist of people or equipment.
-
Assign resources to work center and allocate resource units to shifts of your manufacturing plant. This helps you to maintain a work center resource calendar for each resource.
-
(Optional) Create specific instances of each resource that you created. Resource instances are specific equipment or individual people working in your shop floor.
-
(Optional) Create standard operations, where you define the attributes and assign specific resources to it. So, when you reference a standard operation to a work definition, all its attributes and resources are carried forward to the work definition. This helps you save effort and time by enabling reuse of the standard operation.
You can use the user interface to create the setup data. To create or update setup data in bulk, you can use the export and import of CSV file packages or Excel spreadsheets.