Example of Outsourced Manufacturing Flows
For both contract manufacturing and outside processing, the flow is similar.
Scenario
For example, for an outside processing flow, there will be two fiscal documents FD1 and FD2.
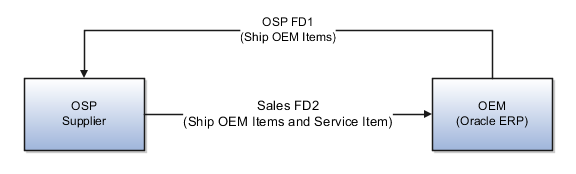
First, the manufacturer (OEM) sends the partially finished assembly or goods to outside processing (OSP) supplier along with an outbound fiscal document (FD1) called the Outside Processing fiscal document. This document contains information about the goods sent to the OSP supplier.
Once the supplier finishes the work, they send back the goods to the manufacturer, along with a fiscal document (FD2). This FD2 document contains information of the OEM material originally sent and the service item for which the OSP supplier needs to be paid for.
The OEM materials on FD2 will be only for bookkeeping and no receipt or invoice is created for those lines in the manufacturer's accounts.
On receiving FD2, manufacturer does the following:
-
Validates the fiscal document
-
Updates the work order
-
Calculates the taxes
-
References FD2 with FD1 to claim tax exemptions
-
Creates a receipt in Receipt Accounting for the Outside Processing flow
-
Creates an invoice for the PO with destination type as Manufacturing with Work Order
-
Matches the PO with the sales document (FD2) details to pay the OSP supplier
During outside processing, if there are any additional charges incurred on moving the items, they're included in the item cost.