How Drop Ship Works in Order Management
Use Order Management to manage your drop ship flow.
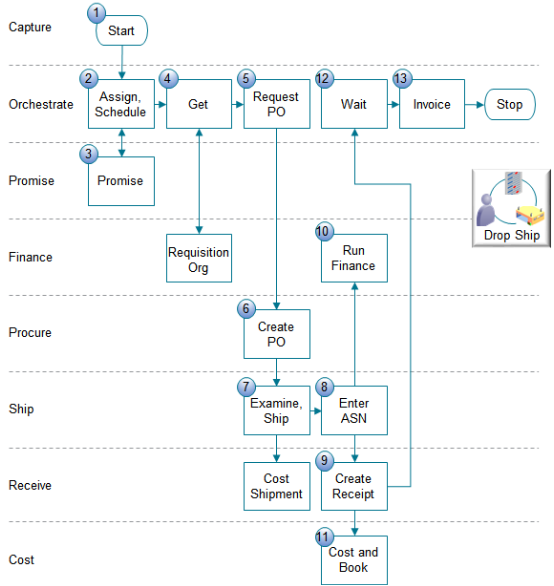
Note
-
An order capture system captures a source order.
-
Each horizontal row in the diagram represents a system or application.
-
The drop ship flow is a variation of the order-to-cash flow.
-
Order Management comes predefined to capture sales orders in the Order Management work area. You can also capture source orders in an order capture system that resides outside of Order Management.
-
-
Order Management assigns an orchestration process to the sales order, uses the Schedule Order task to start scheduling the sales order, then sends a scheduling request to Global Order Promising.
-
Global Order Promising considers sourcing rules, supplier calendar, capacity, and so on to identify the supplier and supplier site that can fulfill the order in the most efficient way. If the sales order specifies a supplier, then Global Order Promising uses this supplier.
-
The orchestration process gets the requisition organization from Supply Chain Financial Orchestration so it can create a purchase request.
-
Order Management sends a purchase request to Oracle Procurement.
Note
-
Procurement doesn't use the Product Category or Product Fiscal Classification to create a purchase order.
-
Order Management doesn't set a default value for the Product Category attribute on the order line. The Order Entry Specialist can specify this value when setting tax determinants, but Order Management doesn't send it to Procurement, so the purchase order doesn't contain a value for Product Category. For details, see Edit Tax on Order Lines.
-
Order Management sets a default value for the Product Fiscal Classification in the sales order. The purchase order in Procurement also has a Product Fiscal Classification attribute and Procurement sets it to the same value that's on the sales order, but it isn't required.
-
-
Procurement creates a purchase requisition, approves the requisition, creates a purchase order, then sends the purchase order to the supplier.
Note
This Attribute
References This Attribute
Customer Sales Order attribute in the Purchase Requisitions work area
Number attribute on the sales order in the Order Management work area
Requisition attribute in the Purchase Orders work area
Requisition Number attribute in Purchase Requisitions
Drop Shipment PO attribute on the Supply Details tab of the fulfillment line in the Order Management work area
Purchase order
Requisition attribute on the Supply Details tab of the fulfillment line in the Order Management work area
Purchase requisition
-
Order Management sets the order line status when Procurement creates the requisition and the purchase order.
What Procurement Does
Order Line Status
Creates the requisition.
Requisition Created
Creates the purchase order.
Awaiting Shipping
-
Receiving can send an advance shipment notice to Order Management after the status goes to Awaiting Shipping.
-
Receiving can create an advance shipment notice for the entire quantity or for only part of the quantity.
-
-
If a blanket purchase agreement exists, then Procurement might source the requisition from the agreement.
-
Procurement sends responses to Order Management while the purchase order moves through its lifecycle.
Response
What Procurement Did
PO_IMPLEMENTED
Created the purchase order.
PO_CO_IMPLEMENTED
Added a change to an existing purchase order.
PO_CO_RESCINDED
Rejected a change in the purchase order.
REQ_LINE_CANCEL
Canceled a line in the purchase requisition.
-
-
The supplier examines the purchase order and uses your shipping fulfillment system to ship the item to the customer. The enterprise supplier also communicates with the receiving part of Inventory Management to cost the shipment.
-
The supplier uses a supplier portal to enter an ASN. Order Management sends the notice to interested parties and Financial Orchestration. For details, see Supplier Portal Integration.
-
The receiving part of Inventory Management creates a logical receipt in the receiving organization. It doesn't create a physical receipt because the supplier ships the item directly to your customer.
-
Financial Orchestration runs a financial flow that comes predefined to handle drop ships, and that specifies how to handle the flow that runs from the supplier to the customer.
-
Cost Management does receipt accounting and cost accounting.
-
Order Management waits to receive the advance shipment notice from receiving. The notice indicates that the item shipped and that the customer acknowledged receipt.
-
Order Management communicates with Oracle Receivables to create an invoice and process payments.
You can modify some of these steps. For example, use Manage Sourcing Rules to modify how Global Order Promising considers sourcing rules, or use Manage Drop Ship Financial Flows to modify how Supply Chain Financial Orchestration sets up a relationship between the selling business unit and the requisition organization. For details, see Set Up Drop Ship in Order Management.