Example of Supply Chain Cost Rollup for Process Manufacturing
This example illustrates how the unit cost of an item in process manufacturing is calculated by the Roll up Costs process when using supply chain cost rollup.
Scenario
Organization ZQD is manufacturing the item SC_ABCDEF. Here's the overall output of the process manufacturing.
Item | Sourcing Rule | Output | Source Allocation Percentage | Quantity | Cost Allocation in Work Definition |
---|---|---|---|---|---|
SC_ABCDEF | Make | Primary product | 70% | 10 | 60% |
SC_ABCDEF | Buy | Primary product | 30% | 10 | N/A |
SC_CoProd | Make | Co-product | 100% | 10 | 30% |
SC_ByProd | Make | By-product | 100% | 10 | 10% |
To manufacture the item SC_ABCDEF, you need various other items. The items, their sourcing rules, and quantities are listed in this table:
Item | Organization | Sourcing Rule | Source Organization | Source Allocation Percentage | Quantity |
---|---|---|---|---|---|
SC_ABCDEF | ZQD | Make | N/A | 70% | 10 |
SC_ABCDEF | ZQD | Buy | N/A | 30% | 10 |
SC_Y | ZQD | Transfer | M1 | 100% | 1 |
SC_X | ZQD | Transfer | M1 | 100% | 1 |
SC_F | ZQD | Buy | N/A | 100% | 1 |
SC_PH3 | ZQD | N/A | N/A | 100% | 2 |
SC_E | ZQD | Buy | N/A | 100% | 2 |
SC_Ph2 | ZQD | N/A | N/A | 100% | 4 |
SC_CD | ZQD | Buy | N/A | 40% | 4 |
SC_CD | ZQD | Transfer | M1 | 60% | 4 |
SC_Ph1 | ZQD | N/A | N/A | 100% | 8 |
SC_A | ZQD | Buy | N/A | 100% | 16 |
SC_B | ZQD | Buy | N/A | 100% | 8 |
In the above table, you will note that no sourcing rules are mentioned for the phantom items SC_Ph1, SC_Ph2, and SC_PH3. The Roll up Costs process assumes that the phantom items will be 100% make items.
Apart from these materials, you also require the resource Labor-3 for 10 hours to manufacture the item SC_ABCDEF.
The subassembly SC_CD in the above table is made in the organization M1. The corresponding sourcing rules are listed in this table:
Item | Organization | Sourcing Rule | Source Organization | Allocation | Quantity |
---|---|---|---|---|---|
SC_CD | M1 | Make | N/A | 20% | 4 |
SC_CD | M1 | Buy | N/A | 80% | 4 |
SC_C | M1 | Buy | N/A | 100% | 8 |
SC_D | M1 | Buy | N/A | 100% | 4 |
Apart from these materials, you also require the resource Mach-01 for 5 hours to manufacture the subassembly SC_CD.
As you can gather from the tables, the organization ZQD requires the items listed here to manufacture the finished item SC_ABCDEF:
-
SC_Ph1 – ZQD makes this item and needs these items:
-
SC_A – ZQD buys this item and a standard or buy cost must be defined for this item.
-
SC_B – ZQD buys this item and a standard or buy cost must be defined for this item.
-
-
SC_Ph2 – ZQD makes this item and needs these items:
-
SC_Ph1 – ZQD makes this item and the cost is rolled up based on the item structure defined.
-
SC_CD – ZQD buys 40% of this item and a standard or buy cost must be defined for this item. The remaining 60% is transferred from M1 with a 10% markup.
-
-
SC_CD – M1 makes this item and needs these items and resources:
-
SC_C – M1 buys this item and a standard or buy cost must be defined for this item.
-
SC_D – M1 buys this item and a standard or buy cost must be defined for this item.
-
Mach-01 – M1 uses this resource for 5 hours to make one SC_CD.
-
-
SC_PH3 – ZQD makes this item and needs these items:
-
SC_Ph2 – ZQD makes this item and the cost is rolled up based on the item structure defined.
-
SC_E – ZQD buys this item and a standard or buy cost must be defined for this item.
-
-
SC_ABCDEF – ZQD makes this item and needs these items and resources:
-
SC_PH3 – ZQD makes this item and the cost is rolled up based on the item structure defined.
-
SC_F – ZQD buys this item and a standard or buy cost must be defined for this item.
-
SC_X – ZQD sources this item from M1.
-
SC_Y – ZQD sources this item from M1.
-
Labor-3 – ZQD uses this resource for 10 hours to make one SC_ABCDEF.
-
Here's an image illustrating the overall manufacturing flow for the finished item SC_FP01.
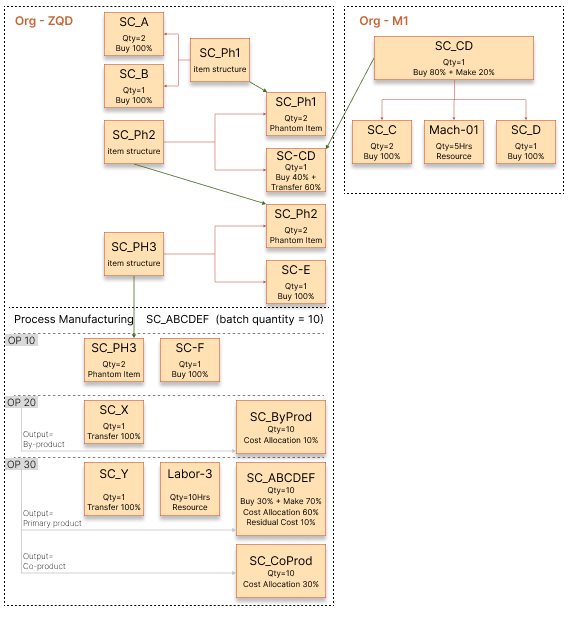
For this item, you create the work definitions.
Item | Work Definition Name | Version | Date |
---|---|---|---|
SC_ABCDEF | ZQD_Final | 1 | 11/1/2023 |
SC_CD | M1_Sub | 1 | 11/1/2023 |
Cost Scenario, Standard Costs, Resource Rates, and Overhead Rates
Now, to calculate the unit cost of SC_ABCDEF, you start by creating a cost scenario. You must make sure that the effective start date of the cost scenario is same as or later than the work definition start date. Also, ensure that the settings listed here are made in the cost scenario:
-
Enable Supply Chain Cost Rollup – Select this option.
-
Organization Context – Group
-
Cost Rollup Group – Select a cost rollup group that you've created with the cost organization and cost book combinations for the ZQD and M1 organizations respectively.
-
Effective Date – 11/1/2023
-
Assignment Set Name – Select the assignment set in which you have set the sourcing type for all the items. Also, ensure that you’ve defined the various sourcing rules. The sourcing rules must be planning enabled and linked to the assignment set. Also, check whether active supply sourcing rules with total allocation of 100% exist as of the scenario effective date.
Note: You must run the Extract Supply Sources process for the assignment set before running the Roll up Costs process. -
Transfer Charge Rule Set – Select the rule set with the transfer charge rule for transfer from M1 to ZQD. Define a 10% transfer charge rule.
-
Rollup Scope – Select Items. Add the items listed here:
-
SC_Ph1
-
SC_Ph21
-
SC_PH3
-
SC_CD
-
SC_ABCDEF
-
-
Use Latest Work Definitions – Select this option to use the latest version of active work definition in the manufacturing organization.
Next, you must define the standard costs for the materials used, the rates for the various resources used when manufacturing the item, and the overheads incurred.
Standard Costs
Item | Valuation Unit | Buy Cost | Cost Element | Cost Element Type | Expense Pool | Unit Cost ($) |
---|---|---|---|---|---|---|
SC_A | ZQD-Org1 | No | ||||
P2P-Material | Material | 135.00 | ||||
P2P-OH | Overhead | P2P_Exp_Pool | 15.00 | |||
150.00 | ||||||
SC_B | ZQD-Org1 | No | ||||
P2P-Material | Material | 180.00 | ||||
P2P-OH | Overhead | P2P_Exp_Pool | 20.00 | |||
200.00 | ||||||
SC_C | M1-Org1 | No | ||||
P2P-Material | Material | 720.00 | ||||
P2P-OH | Overhead | P2P_Exp_Pool | 80.00 | |||
800.00 | ||||||
SC_D | M1-Org1 | No | ||||
P2P-Material | Material | 810.00 | ||||
P2P-OH | Overhead | P2P_Exp_Pool | 90.00 | |||
900.00 | ||||||
SC_E | ZQD-Org1 | No | ||||
P2P-Material | Material | 1890.00 | ||||
P2P-OH | Overhead | P2P_Exp_Pool | 210.00 | |||
2100.00 | ||||||
SC_F | ZQD-Org1 | No | ||||
P2P-Material | Material | 4590.00 | ||||
P2P-OH | Overhead | P2P_Exp_Pool | 510.00 | |||
5100.00 | ||||||
SC_X | M1-Org1 | Yes | ||||
P2P-Material | Material | 1000.00 | ||||
P2P-OH | Overhead | P2P_Exp_Pool | 100.00 | |||
1100.00 | ||||||
SC_Y | M1-Org1 | No | ||||
P2P-Material | Material | 1300.00 | ||||
P2P-OH | Overhead | P2P_Exp_Pool | 200.00 | |||
1500.00 | ||||||
SC_CD | M1-Org1 | Yes | ||||
P2P-Material | Material | 3500.00 | ||||
3500.00 | ||||||
SC_CD | ZQD-Org1 | Yes | ||||
P2P-Material | Material | 3500.00 | ||||
3500.00 | ||||||
SC_ABCDEF | ZQD-Org1 | Yes | ||||
P2P-Material | Material | 3100.00 | ||||
3100.00 |
-
There are buy items for which Buy Cost hasn't been selected. You are defining a standard cost for these items that can be used to cost inventory transactions in Cost Accounting. When you select Buy Cost, the buy cost will be used by the Roll up Costs process to calculate the standard cost of the item only if the cost scenario is enabled for supply chain cost rollup and a buy sourcing rule exists for the item in the sourcing assignment. The buy cost is never used to cost inventory transactions in Cost Accounting.
-
Ensure that you select the appropriate cost organization and cost book combination for the items made or used by the ZQD and M1 organizations respectively.
Resource Rates
Resource | Plant | Cost Element | Cost Element Type | Expense Pool | Unit Cost ($) |
---|---|---|---|---|---|
Mach-01 | M1-Mfg | ||||
P2P-Resource | Resource | P2P_Res_Pool | 60.00 | ||
60.00 | |||||
Labor-3 | ZQD-Mfg | ||||
P2P-Resource | Resource | P2P_Res_Pool | 50.00 | ||
50.00 |
Overhead Rates
Plant | Overhead Rate Type | Cost Element | Expense Pool | Absorption Type | Rate |
---|---|---|---|---|---|
M1-Mfg | Plant overhead | Plant_OH | M1P-OH | Percentage | 20% |
M1-Mfg | Plant overhead | Plant_OH | M1P-OH | Fixed | 50.00 |
ZQD-Mfg | Plant overhead | Plant_OH | ZQDP-OH | Fixed | $1.00 |
ZQD-Mfg | Plant overhead | Plant_OH | ZQDP-OH | Percentage | 20% |
ZQD-Mfg | Plant overhead | Plant_OH | ZQDP-OH | Percentage of material cost at all levels | 4% |
ZQD-Mfg | Plant overhead | Plant_OH | ZQDP-OH | Percentage of total cost including overhead at all levels | 3% |
Analysis
After you define the cost scenario and the corresponding standard costs, resource rates, overhead rates, run the Roll up Costs process for the cost scenario.
Rolled Up Costs
Let's start identifying the costs for the items SC_CD, SC_Ph1, SC_Ph2, SC_PH3, and SC_ABCDEF.
The item cost calculation for SC_CD in the M1 organization is as shown here.
Operation Sequence | Component/Resource | Cost Element Type | Unit Cost | Quantity | Amount |
---|---|---|---|---|---|
SC_CD | 3300.00 | 1 | 3300.00 | ||
10 | SC_C | Material | 720.00 | 2 | 1440.00 |
Overhead | 80.00 | 2 | 160.00 | ||
10 | SC_D | Material | 810.00 | 1 | 810.00 |
Overhead | 90.00 | 1 | 90.00 | ||
10 | Mach-01 | Resource | 60.00 | 5 | 300.00 |
10 | Plant overhead | Overhead | 20% | 450.00 | |
Plant overhead | Overhead | 50.00 | 50.00 |
The sourcing rules for SC_CD in the M1 organization are 20% make and 80% buy. So, the cost of SC_CD in the M1 organization is:
Unit Cost of SC_CD = [0.20 * (Make cost of SC_CD) + 0.80 * (Buy cost of
SC_CD)]
We haven't defined a buy cost but a standard cost for SC_CD in M1, which we will use in this case. Therefore,
Unit Cost of SC_CD = [0.20 * (3300.00) + 0.80 * (3500.00)]
Unit Cost of SC_CD = [660.00 + 2800.00]
Unit Cost of SC_CD = 3460.00
The item cost calculation for SC_Ph1 in the ZQD organization is as shown here.
Operation Sequence | Component/Resource | Cost Element Type | Unit Cost | Quantity | Amount |
---|---|---|---|---|---|
SC_Ph1 | 622.50 | 1 | 622.50 | ||
10 | SC_A | Material | 135.00 | 2 | 270.00 |
Overhead | 15.00 | 2 | 30.00 | ||
10 | SC_B | Material | 180.00 | 1 | 180.00 |
Overhead | 20.00 | 1 | 20.00 | ||
10 | Plant overhead | Overhead | 20% | 90.00 | |
Plant overhead | Overhead | 4% | 18.00 | ||
Plant overhead | Overhead | 3% | 13.50 | ||
Plant overhead | Overhead | 1.00 | 1.00 |
The item cost calculation for SC_Ph2 in the ZQD organization is as shown here.
Operation Sequence | Component/Resource | Cost Element Type | Unit Cost | Quantity | Amount |
---|---|---|---|---|---|
SC_Ph2 | 4995.11 | 1 | 4995.11 | ||
10 | SC_Ph1 | Material | 450.00 | 2 | 900.00 |
Overhead | 50.00 | 2 | 100.00 | ||
10 | SC_CD | 3683.60 | 1 | 3683.60 | |
10 | Plant overhead | Overhead | 4% | 170.00 | |
Plant overhead | Overhead | 3% | 140.51 | ||
Plant overhead | Overhead | 1.00 | 1.00 |
ZQD buys 40% of SC_CD and 60% is transferred from M1 with a 10% markup. So, in the above table the cost of SC_CD is calculated as shown here:
Buy cost of SC_CD = 0.40 * 3500.00 = 1400.00
Transfer cost of SC_CD = 0.60 * [1.10 * (Cost of SC_CD in M1)]
Transfer cost of SC_CD = 0.60 * [1.10 * (3460)]
Transfer cost of SC_CD = 0.60 * [3806.00]
Transfer cost of SC_CD = 2283.60
Unit Cost of SC_CD = Buy Cost + Transfer Cost = 1400.00 + 2283.60 =
3683.60
Also, the plant overhead of 170.00 is calculated by considering only the total material cost of SC_CD and SC_Ph1. The plant overhead of 140.51 is calculated considering the total cost, that's material of SC_CD and material, resource, and overhead of SC_Ph1.
The item cost calculation for SC_PH3 in the ZQD organization is as shown here.
Operation Sequence | Component/Resource | Cost Element Type | Unit Cost | Quantity | Amount |
---|---|---|---|---|---|
SC_PH3 | 12599.52 | 1 | 12599.52 | ||
10 | SC_Ph2 | 4683.60 | 2 | 9367.20 | |
10 | SC_E | Material | 1890.00 | 1 | 1890.00 |
Overhead | 210.00 | 1 | 210.00 | ||
10 | Plant overhead | Overhead | 20% | 378.00 | |
Plant overhead | Overhead | 4% | 415.60 | ||
Plant overhead | Overhead | 3% | 337.72 | ||
Plant overhead | Overhead | 1.00 | 1.00 |
The cost of SC_Ph2 is taken as 4683.60 per unit. This is without the plant overhead that was applied when calculating the make cost for it in the earlier table. Which is:
(Standard Cost of SC_Ph2) - (Sum of the plant overheads in manufacturing
SC_Ph2)
(4995.11) - (170.00 + 140.51 + 1.00)
(4995.11) - (311.51) = 4683.60
The plant overhead of 378.00 is calculated using only the material cost at this level, which is the material cost of SC_E. Also, the plant overhead of 415.60 is calculated by considering only the total material cost of SC_E and SC_Ph2 from the lower level. The plant overhead of 337.72 is calculated considering the total cost, that's material of SC_E and material, resource, and overhead of SC_Ph2.
Now, let's identify the costs involved in manufacturing the final product SC_ABCDEF in the ZQD organization.
Operation Sequence | Component/Resource | Cost Element Type | Unit Cost | Quantity | Amount |
---|---|---|---|---|---|
10 | SC_PH3 | 11467.20 | 2 | 22934.40 | |
10 | SC_F | Material | 4590.00 | 1 | 4590.00 |
Overhead | 510.00 | 1 | 510.00 | ||
20 | SC_X | Material | 1000.00 | 1 | 1000.00 |
Overhead | 100.00 | 1 | 100.00 | ||
Overhead | 10% | 1 | 110.00 | ||
30 | SC_Y | Material | 1300.00 | 1 | 1300.00 |
Overhead | 200.00 | 1 | 200.00 | ||
Overhead | 10% | 1 | 150.00 | ||
Labor-3 | Resource | 50.00 | 10 | 500.00 | |
Plant overhead | Overhead | 20% | 918.00 | ||
Plant overhead | Overhead | 4% | 1054.80 | ||
Plant overhead | Overhead | 3% | 926.53 | ||
Plant overhead | Overhead | 1.00 | 10 | 10.00 |
In the above table the overhead of 10% for SC_X and SC_Y is the transfer markup for these items from M1.
The output of operation 20 is SC_ByProd. Let's first calculate the cost of SC_ByProd.
Operation Sequence | Component/Resource | Cost Element Type | Unit Cost | Quantity | Amount |
---|---|---|---|---|---|
10 | SC_PH3 | 11467.20 | 2 | 22934.40 | |
10 | SC_F | Material | 4590.00 | 1 | 4590.00 |
Overhead | 510.00 | 1 | 510.00 | ||
20 | SC_X | Material | 1000.00 | 1 | 1000.00 |
Overhead | 100.00 | 1 | 100.00 | ||
Overhead | 10% | 1 | 110.00 | ||
Plant overhead | Overhead | 20% | 918.00 | ||
Plant overhead | Overhead | 4% | 1054.80 | ||
Plant overhead | Overhead | 3% | 862.03 | ||
Plant overhead | Overhead | 1.00 | 10 | 10.00 |
In the above table the plant overheads are calculated as shown here:
-
0.20 * (material cost of SC_F) = 0.20 * 4590.00 = 918.00
-
0.04 * (total material cost of SC_PH3, SC_F, and SC_X)
0.04 * (20780.00 + 4590.00 + 1000.00)
0.04 * (26370.00) = 1054.80
-
0.03 * (material cost of SC_F + total cost of SC_PH3 + total cost of SC_X)
0.03 * (4590.00 + 22934.40 + 1210.00)
0.03 * (28734.4) = 862.03
The output SC_ByProd has a cost allocation of 10% in the work definition and the batch size is 10. So the unit cost calculation for SC_ByProd is as shown here:
{{[(Total cost of material and corresponding overheads) + (Total cost of
plant overheads)] * 0.10} + Fixed plant overhead for SC_ByProd} /
10
{{[(22934.40 + 4590.00 + 510.00 + 1000.00 + 100.00 + 110.00) + (918.00 +
1054.80 + 862.03)] * 0.10} + 10.00} / 10
{{[(29244.40) + (2834.83)] * 0.10} + 10.00} / 10
{{[32079.23 * 0.10]} + 10.00} / 10
{{3207.92 + 10.00} / 10
{3217.92 / 10} = 321.79
One of the outputs of operation 30 is SC_CoProd. Let's calculate the cost of SC_CoProd.
The output SC_CoProd has a cost allocation of 30% in the work definition and the batch size is 10.
To calculate the cost of SC_CoProd, you start by calculating 90% of the material and corresponding overhead cost of items in operations 10 and 20. The reason is that 10% of the cost is allocated for SC_ByProd, the output after operation 20.
0.90 * (item costs in operations 10 and 20) = 0.90 * (29244.40) = 26319.
96
To this we next add the item costs and resource costs for operation 30.
26319.96 + 1300.00 + 200.00 + 150.00 + 500.00 = 28469.96
Now, let's add the variable plant overheads to this cost. Again, we will be considering only 90% of the material costs of items consumed in operations 10 and 20 when calculating the plant overheads.
28469.96 + [(0.20 * 4131.00) + (0.04 * 25033.00) + (0.03 *
28010.96)]
28469.96 + [(826.20) + (1001.32) + (840.33)]
28469.96 + 2667.85 = 31137.81
So, the unit cost of SC_CoProd is:
[(0.30 * 31137.81) + 10.00] / 10 = [9341.34 + 10.00] / 10 = 9351.34 / 10 =
935.13
Similarly, the unit cost to make SC_ABCDEF is:
{[(0.60 + 0.10) * (31137.81)] + 10.00} / 10
Here, 60% is the cost allocation in the work definition for SC_ABCDEF and 10% is the residual cost, as shown in the image earlier.
{[(0.70) * (31137.81)] + 10.00} / 10
{[21796.40] + 10.00} / 10
{21806.40} / 10 = 2180.64
As per the sourcing rules defined for SC_ABCDEF in the ZQD organization, the unit cost is:
[(0.70 * 2180.64) + (0.30 * 3100.00)] = [1526.45 + 930.00] =
2456.45