Work Definitions for Contract Manufacturing
Contract manufacturing is a business process in which an organization, known as the original equipment manufacturer (OEM), outsources manufacturing to another organization, known as the contract manufacturer to manufacture a specific part or a full product. The contract manufacturer manufactures the product to exact specifications of the original equipment manufacturer's label. The original equipment manufacturer may supply some or all components to the contract manufacturer. Contract manufacturing allows the original equipment manufacturer to completely outsource their manufacturing process to the contract manufacturer. You can’t add operations that can be resequenced to a work definition in contract manufacturing organization.
The contract manufacturing business flow in Oracle Manufacturing involves two types of items:
-
Contract Manufacturing Finished Good: Refers to the item that's in demand. It is the ordered item on the customer sales order. The work definition and work order in manufacturing is created for this item.
-
Contract Manufacturing Service Component: Refers to the item with which the supply is fulfilled. It is the item on the purchase order. This item is issued to the manufacturing work order as a component.
In contract manufacturing scenarios, the work definition is the source document, business object that's used internally by the Oracle Fusion Supply Chain Orchestration to create the work order and communicate with the contract manufacturer. The following figure is a quick overview of the manufacturing related business processes that are involved:
The following figure explains how the various applications are involved in completion of the contract manufacturing business flow. This diagram partially depicts the flow, starting with creation of a sales order in Order Promising and ending in creation of a purchase order in Purchasing.
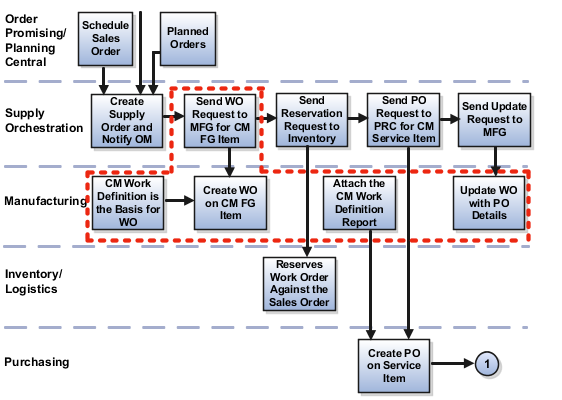
The following figure is a continuation of the previous diagram and explains the contract manufacturing business flow after a purchase order has been created in Purchasing. The flow ends with the work order completion notification sent to supply orchestration and then notifying supply availability for the service item.
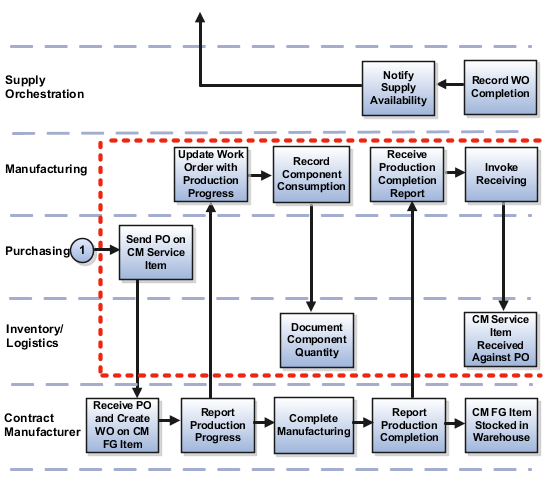
The following table summarizes key setup aspects in a contract manufacturing flow:
Setup |
Considerations |
---|---|
Define the Contract Manufacturer |
Do the following:
In the Plant Parameters page, ensure you have set the plant as a contract manufacturer with the supplier and supplier site as defined. |
Grant access to the manufacturing plant modeled as the contract manufacturer |
Same as that for an in-house manufacturing plant. |
Define the contract manufacturing service item |
Use the Contract Manufacturing Service Component item template provided in Oracle Fusion Product Information Management. If the contract manufacturing finished goods item is a dual units of measure item, which means the Tracking Unit of Measure is set to primary and secondary, then the contract manufacturing service item should be defined as a dual units of measure item as well. For more information about setting up items for outside processing, refer to the Implementing Contract Manufacturing chapter in the Oracle Supply Chain Management Cloud Implementing Manufacturing and Supply Chain Materials Management Guide. |
Define the contract manufacturing finished goods item and complete the item structure in Oracle Fusion Product Information Management |
Use the Contract Manufacturing Finished Goods item template provided in Oracle Fusion Product Information Management. The finished product for the contract manufacturing should be a standard product and not a configured product. |
Complete the definition of the contract manufactured item by defining the item structure |
Ensure that the service item is included as a component in the item structure or bill of materials. Also, ensure that the supply type of the component items is correct. For example, Supplier for the supplier provided components and Push for the OEM provided components. |
Attachment categories and the related item setup in Oracle Fusion Product Information Management |
Optional and is to ensure that the attachment of the work definition document is possible if used at the item definition level against the service item. In most of the scenarios, the work definition report is attached to the Blanket Purchase Agreement in Oracle Fusion Purchasing. |
In order for Supply Chain Orchestration to create a work order for a Contract Manufacturing Finished Good item, a primary work definition must be defined first. The contract manufacturing work definition has a few different business rules compared to a standard item work definition. The specifics are highlighted and discussed here in more detail.
In the context of a contract manufacturing work definition operation, the following simple business rules are reinforced:
-
The contract manufacturing service item must have a supply type of Assembly Pull. It is also recommended that there is only one service component on the work definition and consumed as such on the last count point operation of the work definition.
-
All other operation items on the work definition can use the following supply types only: Phantom, Assembly Pull, or Operation Pull for Original Equipment Manufacturer provided items and Supplier for Supplier provided items.
-
Contract manufacturing isn't applicable for supplier operations.
- Job profile and an equipment profile won't be enforced for contract manufacturing work orders.