View Calendar Details Example: Planned Buy Order
This example describes the calendar details of a planned buy order in an unconstrained plan.
You can tell it’s a buy order because the Supplier, Supplier Site, and Supplier Site Time Zone fields are displayed in the header section. This is an unconstrained plan. If this were a constrained plan, there would be two additional fields displayed in the header section: Earliest Start Date and Latest Start Date.
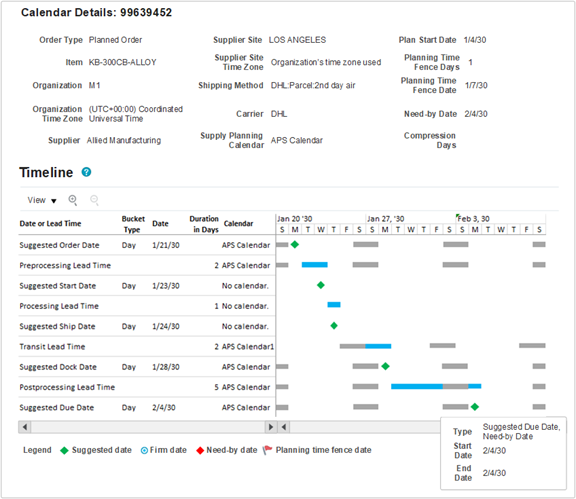
For planned buy orders, all lead times and suggested dates are applicable, so all available rows are shown in the Gantt chart.
Planning uses backward scheduling to calculate supply dates, so we’ll analyze the dates starting from the Suggested Due Date (the last row).
Date or Lead Time Row | Value | Explanation |
---|---|---|
Suggested Due Date | February 4 |
In this example, the Suggested Due Date is the same as the Need-by Date. Because unconstrained planning schedules supplies based on Need-by Date, it’s common that both dates are the same. When milestone dates overlap, the suggested date is always displayed on top in the Gantt chart. If you hover over the Suggested Due Date milestone, you can see that both the Need-by Date and Suggested Due Date are on February 4. The Need-by Date is also displayed in the header section for quick reference without having to hover. If needed, planning will move the Suggested Due Date out so that it’s on or after the Planning Time Fence Date. In this case, the Planning Time Fence Date is January 7, so there’s no need to move the Suggested Due Date out. The calendar used in calculating the Suggested Due Date is the Organization Manufacturing Calendar. In this example, the calendar used is APS Calendar, which has Saturdays and Sundays as nonworking days, represented by gray bars in the Gantt chart. Planning always ensures that the Suggested Due Date is on a working day, however, a planner may firm the order on a nonworking day. If the order is firmed, the Gantt chart will display the Suggested Due Date using the firm date icon (a blue circle), in place of the regular green diamond icon. The planning bucket type for this date and all other dates is day. This lets you know that the Suggested Due Date didn’t get moved to the last working day of the planning bucket, which is what happens when planning in aggregate planning buckets. |
Postprocessing Lead Time | 5 days |
The Postprocessing Lead Time’s duration in days value comes from the Items page and includes any simulation set overrides. In this example, there are 5 days of Postprocessing Lead Time. The same calendar used for Suggested Due Date (the Organization Manufacturing Calendar) is also used in calculating Postprocessing Lead Time duration. The end date of the Postprocessing Lead Time is set to the Suggested Due Date. The start date of the Postprocessing Lead Time is calculated by subtracting the Postprocessing Lead Time from the end date of the Postprocessing Lead Time, only counting the working days. In this example, the Postprocessing Lead Time starts at the beginning of the day on Tuesday, January 29, and goes through the end of the day on Monday, February 4 (skipping Saturday and Sunday, which are nonworking days on the APS Calendar). |
Suggested Dock Date | January 28 |
The Suggested Dock Date is based on the Organization Receiving Calendar. Depending on your setup, the Organization Receiving Calendar might be different from the Organization Manufacturing Calendar, which is used in calculating the Suggested Due Date and Postprocessing Lead Time. The Organization Receiving Calendar can be specific to the receiving organization, or to a carrier and receiving organization combination. In this example, the same calendar (APS Calendar) that’s used in calculating the Suggested Due Date and Postprocessing Lead Time is also used for calculating the Suggested Dock Date. In cases where the Organization Receiving Calendar is different from the Organization Manufacturing Calendar, the Suggested Dock Date might need to be moved earlier to ensure that it ends up on a working day on the Organization Receiving Calendar. In this example, APS Calendar is used as both the Organization Manufacturing Calendar and the Organization Receiving Calendar, so there’s no need to make any adjustment because of differences in working days between the two calendars. The Suggested Dock Date of January 28 matches what we expect to see, given the Postprocessing Lead Time. |
Transit Lead Time | 2 days |
The Transit Lead Time was derived based on the Shipping Method shown in the header section, which comes from the Interlocation Shipping Methods tab of the Supply Network Model UI. The calendar used in calculating Transit Lead Time is APS Calendar1, which has different working days from the calendar used for the Suggested Dock Date. Only Sundays through Thursdays are working days for APS Calendar1. The end date of the Transit Lead Time is set to the Suggested Dock Date. If the Suggested Dock Date is not a valid working day on the transit calendar, then the Transit Lead Time end date will be moved earlier, to a working day on the transit calendar. In this example, the Suggested Dock Date, January 28, is a valid working day on the transit calendar, so there’s no need to adjust the end date of the Transit Lead Time. The start date of the Transit Lead Time is calculated by subtracting the Transit Lead Time from the end date of the Transit Lead Time, only counting the working days on the transit calendar. In this example, Transit Lead Time starts at the beginning of the day on Sunday, January 27, and goes through the end of the day on Monday, January 28. |
Suggested Ship Date | January 24 |
The Supplier Shipping Calendar is used to calculate the Suggested Ship Date of a buy order. In this example, no Supplier Shipping Calendar was found, so all days are considered working days. Because all days are working days, there was no need during plan run to adjust the Suggested Ship Date so that it ended up on a working day. You might be asking why the suggested date is Thursday, January 24. Given that the start of the Transit Lead Time shown in the window was the beginning of the day on Sunday, January 27, shouldn't the ship date have been Saturday, January 26? The probable cause is that when Transit Lead Time was calculated during plan run, the end date of the Transit Lead Time wasn't at the very end of the day, but sometime earlier that day. This would cause the Transit Lead Time start date to be sometime during the day on Thursday, January 24 (given that Fridays and Saturdays are nonworking days on the transit calendar). So the Suggested Ship Date makes sense, even though there is a gap, because of the difference between the time stamps used during plan run and the time stamp used in the Calendar Details window to calculate lead times. |
Processing Lead Time | 1 day |
The Processing Lead Time’s duration in days value comes from the Approved Supplier List (ASL), which is displayed using the Suppliers UI. If no ASL exists for the Supplier/Supplier Site/Item combination, then the Processing Lead Time’s duration in days value comes from the Items page and includes any simulation set overrides. The Supplier Capacity Calendar is used in calculating Processing Lead Time. In this example, there is no Supplier Capacity Calendar, so all days are considered to be working days for the supplier. The Processing Lead Time end date is set to the Suggested Ship Date. If the Processing Lead Time end date is a nonworking day on the Supplier Capacity Calendar, it will be moved earlier to a working day. In this example, the Suggested Ship Date, January 24, is a valid working day, so there’s no need to adjust the Processing Lead Time end date. The start date of the Processing Lead Time is calculated by subtracting the Processing Lead Time from the end date of the Processing Lead Time, only counting the working days. In this example, the Processing Lead Time starts at the beginning of the day on January 24 and goes through to the end of that same day. |
Suggested Start Date | January 23 |
The Supplier Capacity Calendar is used to calculate the Suggested Start Date. In this example, no Supplier Capacity Calendar was found, so all days are considered working days. The Suggested Start Date of January 23 matches what we expect to see, given the Processing Lead Time. |
Preprocessing Lead Time | 2 days |
The Preprocessing Lead Time’s duration in days value comes from the Items page and includes any simulation set overrides. Preprocessing Lead Time and Suggested Order Date are used to account for the time it takes the organization to raise an order. So it's the Organization Manufacturing Calendar that is used in calculating Preprocessing Lead Time and the Suggested Order Date. In this case, the calendar used is APS Calendar. The Preprocessing Lead Time end date is set to the Suggested Start Date. If the Preprocessing Lead Time end date is not a valid working day on the Organization Manufacturing Calendar, it will be moved earlier to a working day. In this example, the Suggested Start Date, January 23, is a valid working day, so there’s no need to adjust the end date of the Preprocessing Lead Time. The start date of the Preprocessing Lead Time is calculated by subtracting the Preprocessing Lead Time from the end date of the Preprocessing Lead Time, only counting the working days. In this example, Preprocessing Lead Time starts at the beginning of the day on January 22 and goes through the end of the day on January 23. |
Suggested Order Date | January 21 |
The Organization Manufacturing Calendar is used to calculate the Suggested Order Date. In this example, the calendar used is APS Calendar. The January 21 Suggested Order Date matches what we expect to see, given the Preprocessing Lead Time. The supply dates of a purchase order or purchase requisition can be analyzed using the View Calendar Details action in the same way that supply dates are analyzed for planned buy orders. The only difference is that, by default, Preprocessing Lead Time is not applied to purchase orders and purchase requisitions. After the planned order is released and an order is created on the source system, the ordering process is complete and there’s no need for planning to account for the time it takes to raise an order. As a result, the Preprocessing Lead Time row isn't applied (and therefore it isn't displayed) for purchase orders and purchase requisitions. When Preprocessing Lead Time isn't applied, the Suggested Order Date is equal to the Suggested Start Date. |