Yield and Quality Cost Reporting
Yield reporting is a very common measure of quality and yield, the percent of defect-free units produced, can be calculated using Oracle Quality's user-defined formulas. As director of quality at a printed circuit board (PCB) manufacturing facility, you have decided to use yield reporting and quality cost reporting, another common tool in quality analysis, in your quality program.
An important quality characteristic of a printed circuit boards in your industry is that they be free from of 'open' and 'short' defects. An open is a defect that creates a break in the circuit; a short is a defect that changes the circuit pattern. Both of these defects can be detected by an electrical test performed by a board tester. Boards that are tested and free from defects are shipped to various computer manufacturers who populate them with components before assembling them into their products.
Boards that are found to be defective during test are normally routed to a Rework operation. Rework typically involves repairing circuits by either soldering for open defects and/or cutting out circuit lines for short defects. Rework repairs are expensive and, when they happen too often, can results in escalating manufacturing costs.
Sometimes boards with intermittent defects pass final electrical test and are shipped to customers. If defective boards are used in a customer's product, not only is your product quality compromised but the customer's is compromised as well. Defective products can erode customer confidence and result in losses for all parties involved. Obviously, board quality is therefore an important issue.
Currently your the plant is experiencing an increase in quality related problems. As director of quality it is your responsibility to discuss these problems with your customers and to outline to them a program for improving product quality.
Your first step is to assemble a product quality team. The quality team's initial mission is to improve the 'circuitize' process. A typical measure of quality for this process is first pass yield which is the yield measured during the first pass, before any rework is done.
The plant produces PCBs in batches of 200 units and all units are put through electrical test. It is during test that defective units are detected. Units that fail electrical test are moved to a rework operation where rework is performed for certain defects, namely 'open' and 'short' defects. Units that are inspected and found to have either Handling or Machine damage are disposed off as scrap.
The team is also interested in another measure of process quality: determining the cost of quality. They realize that they can more readily grab management's attention by presenting an analysis of quality costs than an analysis of first pass yield. The components of quality costs, also known as internal failure costs, include rework process costs and the costs of material that go into rework and the costs of scrap. Internal failure costs are dependent on the following factors.
- The item type, whether it is core, multi-layer board etc.
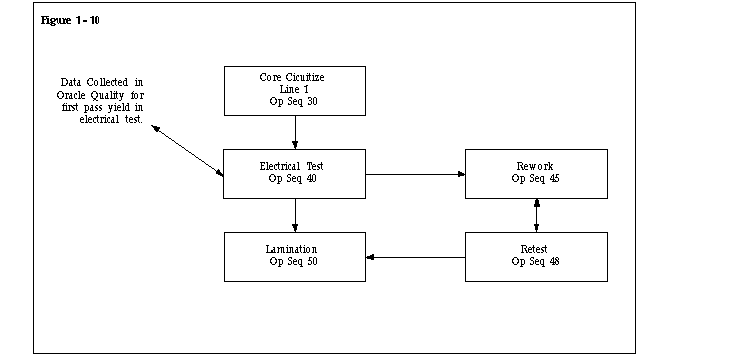
Figure 1 - 10 illustrates the process operations discussed above.
Setup
Based upon this business example, you have determined that you need to create two collection plans. The first, First Pass Yield, should include the following collection elements.
The second collection plan, Quality Cost, should include the following collection elements:
Cost Table
In this example, Total Quality Cost is calculated using information stored in a custom Oracle database table that is external to Oracle Quality and Oracle Manufacturing. This table should, at a minimum include Item, Defect Code, and Defect Unit Cost columns as it is assumed that for a given Item and Defect Code there is a specific Defect Unit Cost. Total Quality Cost is calculated by multiplying the defect cost per unit by the number of occurrences.
Attention: You could also create a collection plan to collect the data that is stored in Cost Table.
Normally, such a cost table would be maintained by the costing department with input from the quality department regarding the cost of defective units. Defect Unit Costs are either the cost of scrap, when items cannot be repaired, or the cost of rework, or both. Rework costs are normally calculated based on actual labor costs and average labor time required to repair an item. Scrap costs are normally based on the cost of scrapped material and the actual labor cost incurred in the disposal of the scrapped product.
In this example, the unit costs associated with 'open' and 'short' defects are considered rework costs since items with these defects are reworked. Defects that are caused by machine and handling damage cannot be repaired and result in scrap costs. It should be noted that an item with multiple 'open' and 'short' defects can be reworked many times but can only be scrapped once.
Collection Elements
Of the collection elements listed above (for both collection plans), six (First Pass Yield, Product Type, Quantity Inspected, Quantity Rejected, Quantity Passed, and Total Quality Costs) must be defined by the user. Item and Job are context elements and data for these collection elements is automatically collected as move transactions are entered. Defect Code is a predefined collection element. See: Defining Collection Elements.
Collection Element and Collection Plan Element Values
You can define lists of values for the predefined collection element, Defect Code, and the user-defined collection elements. For example, the Defect Code list of values must include, at a minimum, the following values: 'open', 'short', 'handling damage', 'machine damage.' See: Defining Collection Element Values and Defining Collection Plan Element Values.
Collection Plan
Next, create the First Pass Yield collection plan and add the above listed collection elements to it. All collection plan elements, except First Pass Yield, should be defined as mandatory.
Also create the Cost of Quality collection plan and add the above listed collection elements to it. All collection plan elements should be defined as displayed and mandatory.
Transactions
Next, associate the First Pass Yield collection plan with the WIP move transaction. The move transaction should be made mandatory to ensure that quality data is collected before the move transaction is saved.
Based upon the fact that data collection for First Pass Yield should be invoked each time a move into or out of the Test Operation is made, define the following collection triggers and conditions:
- From Operation Sequence Number <= 40 (Test Operation)
- To Operation Sequence Number > 40 (Test Operation)
Also associate the Cost of Quality collection plan with the WIP move transaction and define the following collection triggers and conditions.
- From Operation Sequence number = 45 (Rework Operation)
- To Operation Sequence number = 48 (Retest Operation)
Again, the move transaction should be made mandatory to ensure that quality data is collected before the move transaction is saved.
Attention: The "=" condition is used when defining collection triggers for the From Operation and To operation sequences because data should be collected when boards are moved from Rework to Retest. The "<=" conditions was not used for the Rework operation because rework is not mandatory. All PCBs do not require rework and many boards that pass through the Retest Operation are found to be defect free.
Quality Actions: Calculating First Pass Yield
To calculate First Pass Yield, select the First Pass Yield collection plan and define a user-defined formula per the following steps:
1. From the Collection Plans window, select the 'Quantity Passed' collection plan element then choose the Actions button. The Quality Actions window appears.
2. In the Action Rules region, selecting the 'is entered' condition.
Note: The formula that calculates First Pass Yield should be triggered by an action rule defined for the Quantity Passed collection plan element. It is assumed that the user enters results values for Quantity Inspected, then Quantity Passed since these two values must be entered before the value of First Pass Yield can be calculated.
3. In the Actions this Rule Invokes region, select the Assign a value action.
4. In the Action Details region, choose the Action Details button. The Assign a Value window appears.
5. In the 'Assign to' field, select the First Pass Yield collection plan element.
6. Select the option to assign a value using a formula (this is the default selection).
7. Enter the following formula:
where QP and QI are tokens for collection elements Quantity Passed and Quantity Inspected respectively
8. Choose the Variables button. The Output Variables window appears.
9. Enter the token name 'QP' for the Quantity Passed collection plan element. Also enter the token name 'QI' for the Quantity Inspected collection plan element.
10. Choose OK to exit both the Output Variables and Quality Actions windows.
When results are entered, First Pass Yield is automatically calculated using the values entered for Quantity Passed and Quantity Inspected.
Since a First Pass Yield of less than 70% indicates a severe quality problem, you can optionally define an action, such as sending a message to the quality team leader, that is triggered when this critical yield is reached.
Quality Actions: Calculating Total Cost of Quality
To calculate Total Cost of Quality, select the Cost of Quality collection plan then define a user-defined formula per the following:
1. From the Collection Plans window, select the 'Defect Code' collection plan element then choose the Actions button. The Quality Actions window appears
2. In the Action Rules region, selecting the 'is entered' condition.
3. In the Actions this Rule Invokes region, select the Assign a value action.
4. In the Action Details region, choose the Action Details button. The Assign a Value window appears.
5. In the 'Assign to' field, select the Total Quality Cost collection plan element.
6. Select the option to define SQL text (formula is the default selection).
7. Enter the following formula:
Select &QD*unit_cost
From cost_table
where defect_code = &DEF and item_type = &ITEM
Note: QD, DEF and ITEM are tokens names (see Step 9) and unit_cost, defect_code and item_type are names of columns in the cost_table.
8. Choose the Variables button. The Output Variables window appears.
9. Enter the token name 'QD' for the Quantity Defective collection plan element, enter the token name 'DEF' for the Defect Code collection plan element, and enter the token name "ITEM" for the Item collection plan element.
10. Choose OK to exit both the Output Variables and Quality Actions windows.
When results are entered for the Cost of Quality collection plan, the collection element values for Item and Defect Code are read from the external cost table and the Total Cost of Quality is automatically calculated per the above user-defined SQL script.
Results Analysis: First Pass Yield
After a few jobs are processed in the Circuitize operation and enough sample data has been collected, the quality team can choose to analyze data either after a given number of jobs have been processed or days have elapsed or after a member of the quality team is notified that the first pass yield has dropped below the threshold level of 70%.
The team can then view and chart quality results in a variety of ways. For example:
Data can be viewed in View Quality Results then exported to a statistics program/package and checked for differences between data sample subgroups. Statistical tests can be performed to determine differences in product types. Histograms can be created for to check for First Pass Yields differences between jobs.
The patterns of defects within subgroups can be further analyzed using Pareto charts. In this example, two important subgroups in such an analysis would be the subgroups resulting from open and short defects. Differences in subgroups should always be investigated since they reveal process anomalies that, once corrected, contribute to the continuous improvement process.
Continuous Improvement
A preliminary data analysis soon reveals that the primary cause of low first pass yields is 'open' defects. The operators performing the rework validated this conclusion when they met with quality team members. Furthermore, these operators stated that 'open' defects occurred more frequently in core items.
Based on results of the quality teams data analysis and real-time observations, you have decided to focus your efforts on investigating the causes of 'open' defects. As part of this investigative process, you have called a meeting with the quality team and performed a cause-and-effect analysis using an Ishikawa diagram. From this brainstorming session a list of the factors that contribute to defects has been drawn. These factors include:
2. Concentration of Etch chemicals
Your next step is to narrow this list of factors down to just one key factor using statistical tools. First a factorial experiment, an industrial experiment that statistically analyzes the effects of various factors on product quality, is designed and executed. Then the data from this experiment is analyzed using a statistical analysis software package. Analysis reveals that conveyor speed is the major factor influencing first pass yields. Therefore the quality team recommends that conveyor speed be increased by about 20%.
After increasing the conveyor speed there is a noticeable increase in the first pass yield. Thus the team has achieved their first small step towards process improvement. To close the loop in the continuous improvement cycle, an analysis of post-process improvement data is made and plans to further reduce defects are made. This cycle of improvements is consistent with the Deming cycle for continuous improvement.
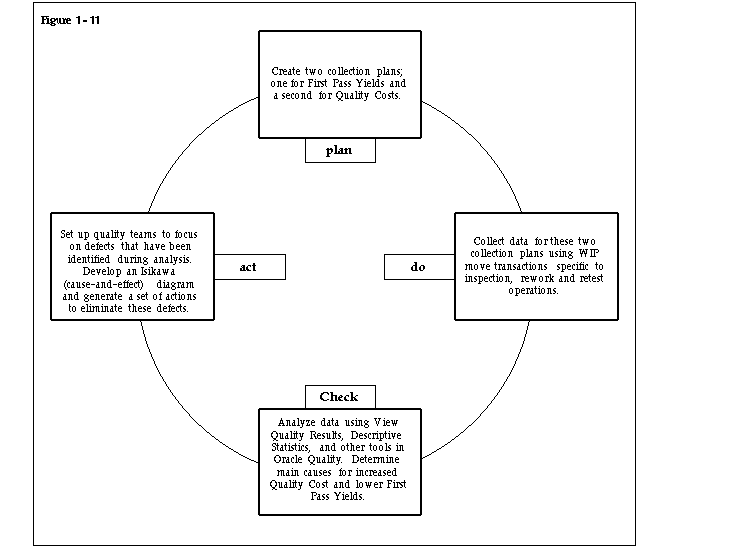
Figure 1 - 11 illustrates Deming's Circle For Continuous Improvement
Results Analysis: Cost of Quality
Using the Descriptive Statistics window, select the Cost of Quality collection plan and generate descriptive statistics using the Total Quality Cost collection plan element as the statistical element. You can generate descriptive statistics based on all or selected subgroups of data. For example, using the search capabilities of the Show Results Where region, you can select and analyze results that are specific to a an Item, a Job, or a specific Defect Code. The statistical sums of the various subgroups represent the cost of quality.
See Also
Creating Collection Plans
Defining Collection Plan Elements
Associating Transactions with Collection Plans
Defining Actions that Assign a Value: User-Defined Formulas
Associating Specification Types with Collection Plans
Viewing Quality Results
Viewing Descriptive Statistics
Creating and Viewing Pareto Charts
Creating and Viewing Histograms
Performing Move Transactions