Defining the Standard Cost Foundation
Before you can calculate the standard cost of purchased or makeable items, you can define the basic codes and tables that PeopleSoft Cost Management uses to build and categorize an item's standard cost.
This section discusses how to:
Define cost types.
Define cost versions.
Create standard cost groups.
Define cost elements.
Define conversion codes.
Define conversion overhead codes.
Create costing conversion rates.
Create costing conversion overhead rates.
Copy cost structures.
Copy rates.
Update conversion rates.
Page Name |
Definition Name |
Usage |
---|---|---|
CE_TYPE |
Define cost types. |
|
CE_VERSION |
Define cost versions. |
|
CM_COSTGROUP |
(For standard costing only) Create cost groups. |
|
CM_ELEMENT |
Define cost elements. |
|
CE_CONCODE |
Define production conversion codes. |
|
CE_OHCODE |
Define conversion overhead codes. |
|
CE_CONRATE |
Create cost conversion rates. |
|
CE_CONOH_RATE |
Create cost conversion overhead rates. |
|
CE_COPY_COST_STRUC |
Copy cost structures. |
|
CE_COPY_COSTS |
Copy cost rates. |
|
CE_MANFRZ_CON |
Update conversion rates. |
Use the Cost Types page (CE_TYPE) to define cost types.
Navigation:
Create separate costing groupings with different methods of costing, such as current, revised or forecasting. The cost type also defines how purchased components are calculated.
To define cost versions, use the Cost Versions component (CE_VERSION).
Use the Cost Versions page (CE_VERSION) to define cost versions.
Navigation:
This example illustrates the fields and controls on the Cost Versions page. You can find definitions for the fields and controls later on this page.
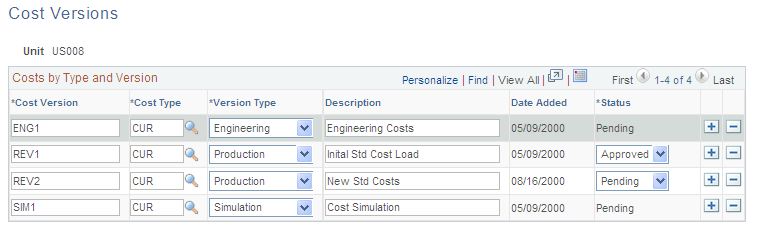
Use the Cost Versions page to define the different cost versions for a cost type. You can create unlimited cost versions for any cost type. By using different versions for a cost type, you can maintain a history of the different costs that are calculated for each cost type. You can base these cost versions on different sets of assumptions, such as different bills of material (BOMs; manufacturing versus engineering), effective dates, different labor rates, or different budgets that determine the overhead expenses.
Field or Control |
Description |
---|---|
Version Type |
Determines the BOM and routing that the Cost Rollup process (CEPCROLL) uses to calculate the cost of make items. Values are: Production: Rolls up manufacturing data only and uses the primary BOM and routing only, each with a code of 1. Use this option to roll up the costs for a manufactured or configured item. This is the only option that produces cost calculations that can update the live production tables. Engineering: Rolls up with either manufacturing or engineering data, with any combination of BOM and routing codes. Use this option exclusively for engineering roll-ups and comparisons. Simulation: Only rolls up with manufacturing data, but can use any combination of BOM and routing codes. Use this option to create what-if scenarios for makeable items. |
Each cost version can have a status of pending, denied, or approved. You can update frozen standard costs used for accounting purposes only if the cost version status is approved. Cost versions that are related to engineering or simulation always have a status of pending.
To create standard cost groups, use the Cost Groups (CM_COSTGROUP) component.
Use the Standard Cost Groups page (CM_COSTGROUP) to (For standard costing only) Create cost groups.
Navigation:
This example illustrates the fields and controls on the Standard Cost Groups page. You can find definitions for the fields and controls later on this page.
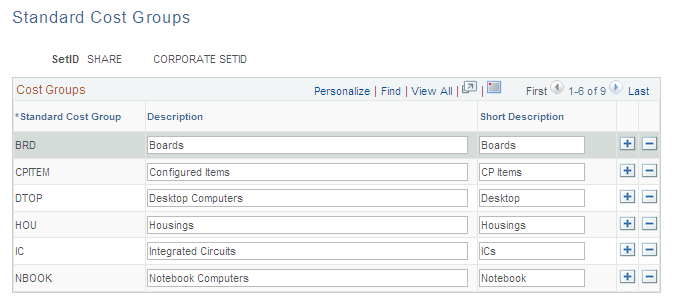
Standard cost groups, also known as cost groups, enable you to group together a set of items for standard cost roll up and standard cost update, comparing costs and reporting inventory value. Add items to the cost group by entering the standard cost group on the item's Define Business Unit Item - General: Common page. Then, enter a standard cost group on the Cost Rollup page or the Cost Update/Revalue page instead of defining a range of item IDs.
To create cost elements, use the Cost Element (CM_ELEMENT) component.
Use the Cost Elements page (CM_ELEMENT) to define cost elements.
Navigation:
Cost elements categorize the components of an item's cost that are tracked through the PeopleSoft Inventory system. The debit and credit ChartField combinations in transaction processing can also be defined by cost element.
To define conversion codes, use the Conversion Codes component (CE_CONCODE). Use the Production Conversion Code component interface to load data into the tables for this component.
Use the Production Conversion Codes page (CE_CONCODE) to define production conversion codes.
Navigation:
This example illustrates the fields and controls on the Production Conversion Codes page. You can find definitions for the fields and controls later on this page.
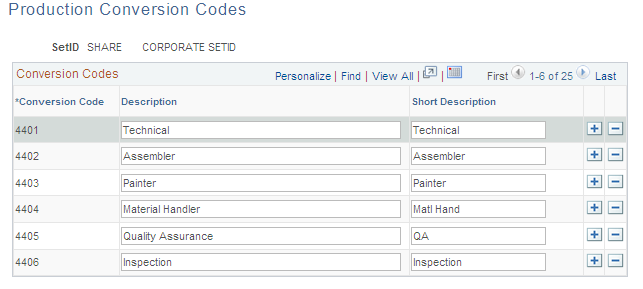
Production conversion codes can be used to categorize labor, machine, and other conversion tasks and activities within work centers in the manufacturing process. Use conversion codes to define conversion rates that are associated with work centers or tasks.
To define cost conversion production overhead codes, use the Conversion Overhead Codes component (CE_OHCODE_CODE). Use the Conversion Overhead Codes component interface to load data into the tables for this component.
Use the Production Overhead Codes page (CE_OHCODE) to define conversion overhead codes.
Navigation:
This example illustrates the fields and controls on the Production Overhead Codes page. You can find definitions for the fields and controls later on this page.
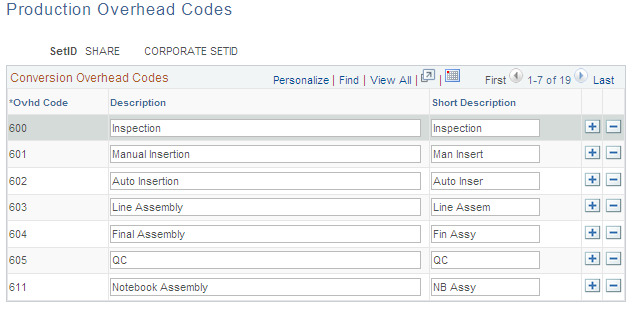
Production conversion overhead codes categorize the different types of overhead costs absorbed during the manufacturing process. Use conversion overhead codes to define conversion overhead rates that are associated with work centers or tasks. You can specify up to four conversion overhead codes for the work center or task.
To define cost conversion rates, use the Costing Conversion Rates component (CE_CONV_RATE). Use the Costing Conversion Rates component interface to load data into the tables for this component.
Use the Conversion Rates page (CE_CONRATE) to create cost conversion rates.
Navigation:
This example illustrates the fields and controls on the Conversion Rates page. You can find definitions for the fields and controls later on this page.
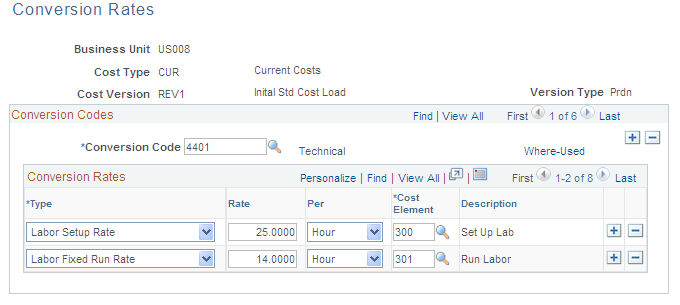
Establish these rates to capture labor and machine costs in the production process. You can enter fixed run, run, post-production, and set up rates for both labor and machine. The rates are based on several factors, including business unit, cost type, cost version, conversion code, and conversion rate type. Each conversion rate type then points to a cost element. Multiple conversion code definitions can point to the same or different cost elements. This structure gives you flexibility to set up and use several different rates. Link these rates with a work center or task where they are used to determine the labor, machine, and subcontracting costs of an item's routing operation.
For each conversion rate type that you want to associate with a specific conversion code, enter a rate.
Field or Control |
Description |
---|---|
Conversion Rate Type |
Enter fixed run, run, post-production, or set up rates for either labor or machine. These rate types correspond to the costing rate types that are defined for a task, and ultimately, to an operation on an item's routing or operation list. You do not need to enter a cost for each conversion rate type. However, if any costing time type on the task, routing, or operation list does not have a corresponding cost, then the system does not include that portion of the routing or operation list cost in the item cost. This enables you to call out task types which have different cost implications for the same conversion code in different cost types or versions. Likewise, if you specify a cost in the conversion rates but do not include the corresponding costing times in the routing or operation list, those costs are not included. |
Rate |
Enter conversion code rates. Use production conversion codes to associate conversion rates with multiple work centers or tasks. Use the Rate Maintenance/Defaulting group box on the Manufacturing Options - MFG Business Unit Options page to determine whether to enter conversion rates for work centers or tasks. |
Per |
Specify how the rate should be applied. You can enter conversion rates as an amount per Hour for labor and machine setup, fixed run, and post production. For labor and machine run, you can specify an amount per Hour or Unit. |
Cost Element |
Enter the cost element that is associated with this conversion cost. This cost element must have the category of conversion on the Cost Elements page. |
For subcontracted tasks or operations, the conversion cost should represent the charge from the supplier for the outside processing. If the supplier charges you a flat amount per unit, enter that charge as a per unit cost. If the supplier quotes you a rate per hour, enter that rate as a labor-setup, run, or fixed-run rate and enter the corresponding time that it takes the supplier to complete the task on the item's routing or operation list.
To define cost conversion overhead rates, use the Costing Conversion Overhead Rates component (CE_CONV_OH_RATE). Use the Overhead Rates component interface to load data into the tables for this component.
Use the Overhead Rates page (CE_CONOH_RATE) to create cost conversion overhead rates.
Navigation:
This example illustrates the fields and controls on the Overhead Rates page. You can find definitions for the fields and controls later on this page.
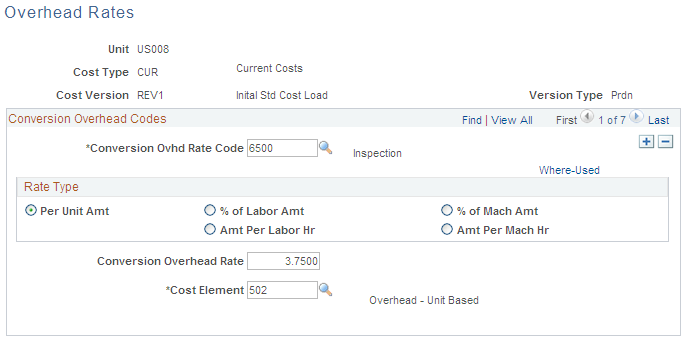
The conversion overhead rates represent the overhead expenses that are associated with the production of the assemblies. Enter the cost conversion overhead rates to use for overhead costs based on the units produced, labor and machine hours, or labor and machine costs. The rates are based on business unit, cost type, cost version, conversion overhead code and cost element. You can establish several different rates. In the case of subcontracted tasks or operations, it should represent the cost of preparing and sending the item to the subcontractor for outside processing.
Select the rate type that you want to associate with the rate code. Valid rate types include:
Field or Control |
Description |
---|---|
Per Unit Amount |
Select to apply cost to the item on a per unit basis. |
% of Labor Amount (percentage of labor amount) |
Select to base on the standard labor costs that the operation requires. To determine the amount of overhead cost, the system first calculates the total labor cost of the operation, then multiplies that cost by the factor that is specified in the Conversion Overhead % field. |
Amt per Labor Hr (amount per labor hour) |
Select to base on the standard labor hours that the operation requires. As with labor cost determination, it determines the number of hours that are necessary to complete the operation by adding labor setup, run, fixed-run, and post-production times (converted to hours), and then multiplies that time by the amount that is specified in the Conversion Overhead Rate field. |
% of Machine Amount (percentage of machine amount) |
This is similar to the percent of labor amount method except that the overhead cost is based on the machine costs that are associated with the operation. To determine the amount of the overhead cost to apply, the system first calculates the total machine cost of the operation, then multiplies that cost by the factor that is specified in the Conversion Overhead % field. |
Amt per Machine Hr (amount per machine hour) |
This is similar to the amount per labor hour method except that the overhead cost is based on the machine hours that are necessary to complete the operation. The system determines the number of hours that are necessary to complete the operation by adding machine setup, run, fixed-run, and post-production times, converted to hours, and multiplies that time by the amount that is specified in the Conversion Overhead Rate field. If you don't specify costing machine hours or run rates for the operation, the system does not apply overhead costs. |
Cost Element |
Enter the cost element that is associated with this conversion cost. This cost element must have the category of conversion overhead on the Cost Elements page. |
Use the Copy Cost Structures page (CE_COPY_COST_STRUC) to copy cost structures.
Navigation:
Copy the cost foundation structures: cost types, cost elements, production conversion codes, and production overhead codes from one SetID to another. This process copies only the codes that are associated with each record and not the rates or costs that are associated with those codes.
Use the Copy Cost Types/Versions page (CE_COPY_COSTS) to copy cost rates.
Navigation:
Copy costs and rates from one business unit to another. If another business unit has the rates and item costs that you want to use, or if you want to use one set of cost type and version information as the basis for other cost types or versions, you can use this page to copy those costs and rates.
Use the Update Conversion Rates page (CE_MANFRZ_CON) to update conversion rates.
Navigation:
This example illustrates the fields and controls on the Update Conversion Rates page. You can find definitions for the fields and controls later on this page.
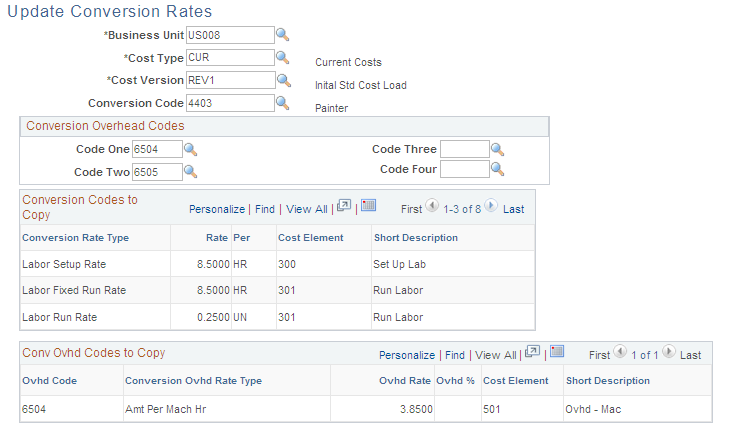
Use this page to update the set of production conversion rates and conversion overhead rates. For standard cost items, run the Cost Update/Revalue process (RUN_CES5001) to copy these conversion rates and conversion overhead rates into production. It then uses these rates to calculate earned labor and machine costs, as well as applied overhead for the assembly completions and scrapped assemblies. If you are introducing a new conversion rate or conversion overhead rate for a single item whose cost you are updating, you must also update the set of production conversion rates and conversion overhead rates that are used to calculate the item's cost. The lower portion of the page displays the conversion rates and conversion overhead rates to copy to the frozen rates records. Save the page to update the rates.