Setting Up the Cost Structure
The cost structure determines how inventory transactions are calculated, where accounting entries are posted, and how many sets of books are maintained.
To set up cost structure:
Establish the ledgers and ledger groups for the PeopleSoft General Ledger business unit or verify that the financials implementation team creates them.
Define the cost books at the SetID level.
Define the cost types at the SetID level.
Associate the cost books and cost types with the PeopleSoft Inventory business units and ledgers or ledger groups.
Define the cost profiles at the SetID level.
You determine the receipt cost method, cost flow, and deplete cost method for the items. For an item that is manufactured with PeopleSoft Manufacturing, a cost profile also determines the costing method that is used to value labor and machine costs.
Create cost profile groups at the SetID level.
This page combines the cost book and cost profile.
Associate the inventory items with a cost book and a cost profile.
This can be done in the Define Item component or the Define Business Unit Item component.
Define the cost elements to categorize the different cost components for an item, including material, conversion, landed, additional transfer costs, and outbound costs.
Attach the cost element to the various PeopleSoft pages that generate costs.
For the material costs of the item, add the cost element that is defined for material to the item by using the Define Business Unit Item-General: Common page.
Note: Once you have read the information in this section, it is recommended that you review the examples in, "Scenarios for PeopleSoft Cost Management". Please review the sections on calculating transaction costing based on the cost profile and determining your cost structure strategy.
Page Name |
Definition Name |
Usage |
---|---|---|
CM_BOOK_DEFN |
Create cost accounting books to identify the type of accounting records that are to be maintained. The books are added to the inventory business unit and the cost profile group. |
|
CE_TYPE |
Create separate costing groupings with different methods of costing, such as current, revised or forecasting. |
|
Ledger Group - Definition Page |
LEDGER_GROUP |
Define a ledger group and link it to a ledger template. Also used to assign ledger details to the group and to identify the unique attributes of each ledger within the group. |
CM_BU_BOOK |
Link the cost books and cost type with a PeopleSoft Inventory business unit, ledger, and ledger group. Define the books to populate with accounting entries for each business unit. |
|
CM_PROFILE_DEFN |
Establish the cost profile to determine how items are costed in the business unit's cost book. |
|
Cost Profiles - Manufacturing Page |
CM_PROFILE_DEF_MFG |
For items that are used in PeopleSoft Manufacturing, enter additional cost profile information to define the costing methods for labor and machine costs. |
Cost Profile Groups - Definition Page |
CM_GROUP_DEFN |
Define a cost profile group by entering a description and any comments. |
CM_GROUP_DETAIL |
Link the cost book and cost profile together under the cost profile group. |
|
Item Definition - General: Common Page |
INV_ITEMS_DEFIN1 |
Enter a cost profile group for an item. Although this is not required, associating the items to a Cost Profile Group simplifies setup when defining items at the inventory business unit level. |
Define Business Unit Item - General: Costing Page |
CM_ITEM_METHOD |
Define the cost profile of an item by business unit and cost book. |
CM_ELEMENT |
Cost elements categorize the components of an item's cost. The system maintains an item's cost-by-cost element. Cost elements also help define the debit and credit ChartFields in transaction processing. |
|
GEN_ATTRIB_INV |
Define the cost element for an item's material costs. |
Before beginning the process of defining PeopleSoft Inventory business units, you need to establish PeopleSoft General Ledger business units, ledgers and ledger groups. Ledgers and ledger groups represent a set of books and store the posted financial entries (journal entries) by accounting period and fiscal year. Different ledgers can be defined for recording financial records, tax records, management reports, and so on.
To define the types of accounting records to maintain, use the Cost Book (CM_BOOK_DEFN) component.
Use the Books page (CM_BOOK_DEFN) to create cost accounting books to identify the type of accounting records that are to be maintained.
The books are added to the inventory business unit and the cost profile group.
Navigation:
This example illustrates the fields and controls on the Cost Books page. You can find definitions for the fields and controls later on this page.
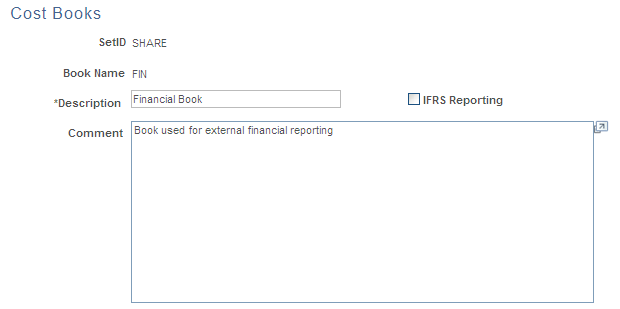
Define a separate cost book for each type of accounting records that you want to maintain. For example, define a cost book for financial records; another cost book for tax records, and so on.
You can create any number of books and assign the books to a PeopleSoft Inventory business unit. Each book enables you to use different cost methods; for example, a financials book can use standard costing for items, and the tax book can use LIFO costing for items. You can define any number of simultaneous books to be used. Each inventory transaction that has a financial impact creates a separate set of accounting entries in each book that is assigned to it. The accounting entries are then posted to the specified ledger or ledger group within PeopleSoft General Ledger.
Select the IFRS Reporting check box to enable this cost book to support International Financial Reporting Standards (IFRS). This check box cannot be selected if the existing cost book uses the LIFO cost flow method. For additional information about setting up IFRS reporting, please see the Valuing Inventory for IFRS section within the Costing Transactions and Creating Accounting Entries topics.
To define cost types, use the Cost Types component (CE_TYPE).
Use the Cost Types page (CE_TYPE) to create separate costing groupings with different methods of costing, such as current, revised or forecasting.
Navigation:
Define different cost types, such as current, revised, and forecasted costs, to create a working space with which you can perform what-if analysis. You calculate the cost of a manufactured item based on cost types. Purchased or make items using the standard cost method can use cost types to calculate a standard cost. Cost types are used as a key to conversion costs and overhead conversion costs to calculate both standard cost and actual cost make items. The cost type is added to the Cost Rollup process page when calculating the cost of an item. For a manufactured item using an actual or average costing method, the cost type should be defined on the Inventory Definition-Business Unit Books page that is to be used by the Transaction Costing process (within the Cost Accounting Creation process) when computing the item cost.
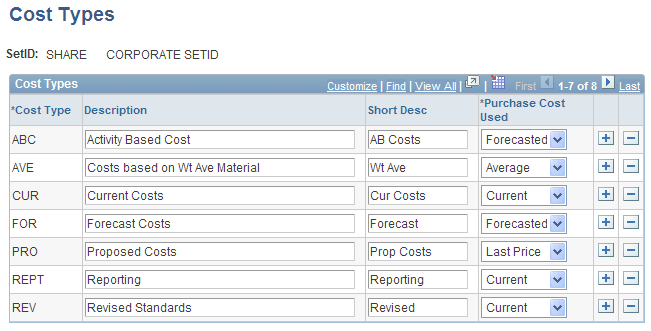
Select the method to calculate the cost of purchased components when computing the cost of an item. The method that you choose here applies to all cost versions using this cost type. Options for Purchase Cost Used include:
Field or Control |
Description |
---|---|
Average |
Average cost. This represents a rolling weighted average cost calculated as: [(current average cost) * (current QOH)] +{(putaway qty) * (PO price for material only)] / [(current QOH) + (putaway qty)]. QOH (quantity on hand). PO (purchase order). Qty (quantity). This cost is automatically updated in the Business Unit Item Definition record (the AVERAGE_COST_MAT field of the BU_ITEMS_INV record) when a purchase receipt is put away. The current value is displayed in the Avg Matl Cost field on the Define Business Unit Item-General: Common page. Use this cost when you want to reflect the supplier's price in the cost of the item. This average cost calculation only includes the material portion of the PO cost; it does not include landed costs, voucher updates, or cost adjustments. This average cost can be used by the Cost Rollup process to compute the material portion of the cost. |
Current |
The current purchase cost is a per unit cost which you manually enter in the Define Business Unit Item - General page (the CURRENT_COST field of the BU_ITEMS_INV record). Use current purchase cost if there is no need to vary material costs for cost simulations and what-if analysis. |
Forecasted |
Enter a forecasted purchase cost by a combination of item, business unit, cost type, and cost version using the Forecasted Purchase Costs page (CE_FCST_PUR record). Use forecasted costs when you want to manually maintain the material cost of purchased items. For example, you can base forecasted purchase costs on supplier quotes for items that are purchased during the standard cost period. If the purchase costs vary based on volume that is purchased from the supplier, you can set up two different versions and vary the forecasted cost for each version based on the volume assumptions. |
Last Price |
You can cost the item based on the price that is paid the last time that you purchased the item. This Last Price value (the LAST_PRICE_PAID field of the BU_ITEMS_INV record) is updated by the Complete Putaway process (PUTAWAY_REQ_INV) based on the PO price of the item's last receipt. Because it is constantly replaced, the value is an indication of an item's price at a specific point in time. In the cost calculation, you can use that price to represent the purchase cost of the component items. |
A critical step in designing the inventory business unit is to define the accounting links to the general ledger system. Use the Inventory Definition component to:
Identify the PeopleSoft General Ledger business unit that accepts financial transactions by using the Inventory Definition - Business Unit Definition Page.
Only one general ledger business unit can be defined per inventory business unit.
Define one or more combinations of cost book and ledger or ledger group for the inventory business unit by using the Inventory Definition - Business Unit Books Page.
When you attach a cost book, every financial transaction that is recorded in this inventory business unit creates accounting entries in that cost book. For example, let's assume that you identify two separate cost books, FIN and TAX, and an item is shipped from the inventory business unit. Two sets of accounting entries are recorded: one in the cost book FIN, and one in the cost book TAX. For each cost book that is defined for an inventory business unit, you must also define the ledger or ledger group that receives the accounting entries for the general ledger side. These ledgers and ledger groups must be part of the general ledger business unit that is defined for the inventory business unit.
Identify the cost type for makeable items by using actual or average cost methods.
If makeable items use actual or average costing methods, then enter a cost type for each cost book. The cost type is used by the Transaction Costing process (within the Cost Accounting Creation process) when calculating the cost of an item that is manufactured in PeopleSoft Manufacturing. Cost types enable the Transaction Costing process to pick up the correct conversion rates and overhead conversion rates, plus any additional costs.
Designating the Primary Book
The inventory business unit must have at least one book. When you associate a cost book with a PeopleSoft Inventory business unit, one book must be designated as the primary book. This is done by associating it with the primary ledger or default ledger group for the PeopleSoft General Ledger business unit. These ledgers and groups are defined on the Ledger Group - Definition page. This page also contains a Keep Ledgers in Sync option.
If the Keep Ledgers in Sync option on the Ledger field is unavailable on the Ledger Group - Definition page, transactions are posted to all ledgers in the ledger group that you select for the book. Exactly one book for the business unit must be pointing to the default ledger group.
If the Keep Ledgers in Sync option is off, you can select the ledger within the ledger group to which you want to post transactions for the book. In that case, the primary book must be pointing to the primary ledger within the default ledger. With the option off, you can also leave the Ledger field blank and transactions are posted to all ledgers in the ledger group that you select for the book. In that case, the book must be pointing to the default ledger group.
If you select a primary ledger, it must use the base currency of the PeopleSoft Inventory business unit and PeopleSoft General Ledger business unit. If you select a default ledger group, the primary ledger of that ledger group must use the base currency of the PeopleSoft Inventory business unit and PeopleSoft General Ledger business unit.
Inventory Definition - Business Unit Books Page
Use the Inventory Definition - Business Unit Books page (CM_BU_BOOK) to link the cost books and cost type with a PeopleSoft Inventory business unit, ledger, and ledger group.
Define the books to populate with accounting entries for each business unit.
Navigation:
This example illustrates the fields and controls on the Inventory Definition - Business Unit Books page. You can find definitions for the fields and controls later on this page.
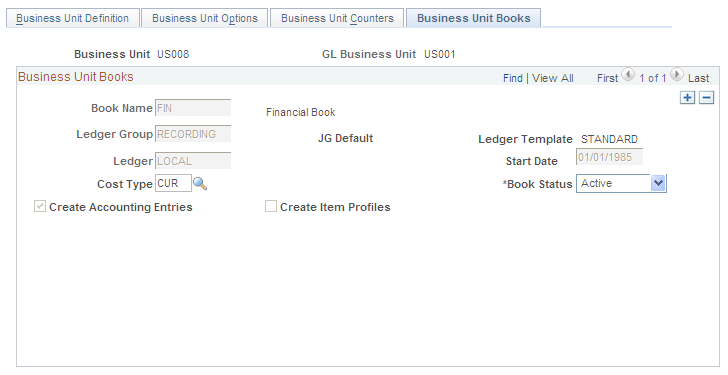
Field or Control |
Description |
---|---|
Cost Type |
Enter a cost type for the inventory business unit cost book. This enables you to use different actual cost conversion rates and overhead conversion rates in different cost books. Cost types are user-defined, and different cost types can point to different conversion and overhead rate structures. Users may wish to use a set of GAAP rates for their GAAP cost type, full absorption rates for their FULLABS cost type, and activity-based cost rates for their ABM cost type. Books point to ledgers in the general ledger, so with this structure users can use different cost rates for their various books which may each have different management and financial reporting purposes. Books that use the frozen standard cost profile always simply use the frozen standard, which is an attribute of items in business units across all books. In other words, the cost types that make up the frozen standards are not affected by the entry in this field. |
Create Accounting Entries |
Select to have transactions in this book create accounting entries in the associated ledger or ledger group when the status of the book is active. This check box should remain selected unless you are an advanced user and you wish to turn off accounting entry creation for an alternative cost book. |
Create Item Profiles |
If one or more items do not have profiles in the book, you can check Create Item Profiles and the system creates the missing profile for those items in that book, if those items are already associated with a cost profile group. If they are not, when you try to save the new book as an active status book, an error message appears, and you must manually assign the profiles for those items for that book by using the Define Business Unit Item - General: Costing page. This check box is unavailable if every business unit item has a profile associated with that book. This option is not necessary if all items already have a cost profile. |
In the Book Status field, enter the status of the book:
Field or Control |
Description |
---|---|
Pending |
When a book is added to a business unit, the default status is Pending. Use the pending status while preparing the book. When the book is ready, change the status to Active. If plans change, you can also change the status from Pending to Inactive or Cancelled. |
Active |
Active books can be used with the Transaction Costing process and the Accounting Line Creation process (both within the Cost Accounting Creation process). When you set a book to Active status, the system confirms that all items contain a cost profile for this book. This ensures that the active book can create complete accounting transactions. |
Inactive |
When an active book is no longer required, set the status to Inactive to prevent the book from creating further accounting entries. With an inactive status, the recorded accounting entries are not available for historical inquiries or reports. |
Stopped |
When an active book is no longer required, set the status to Stopped to prevent the book from creating further accounting entries. With a stopped status, the recorded accounting entries are still available for historical inquiries or reports. A warning message appears when changing an active book to Stopped. Warning! Once an active book has been set to the status of Stopped, it can never again be set to Active status. |
Cancel |
You can cancel a cost book if it is never used to record accounting entries. |
This table lists the conditions under which you can change the book status:
Change From This Status |
To Active |
To Inactive |
To Pending |
To Stopped |
To Cancel |
---|---|---|---|---|---|
Active |
--- |
Okay (warning appears). |
Not allowed |
Okay (warning appears). |
Not allowed. |
Inactive |
Not allowed. |
--- |
Not allowed. |
Okay. |
Not allowed. |
Pending |
Okay, if: All items in the business unit have a profile for the pending book. The book is seeded. The start date is greater than the present. |
Okay, if: The book is seeded. |
--- |
Not allowed. |
Okay, if: The book is not seeded. |
Stopped |
Not allowed. |
Okay. |
Not allowed. |
--- |
Not allowed. |
Cancel |
Not allowed. |
Not allowed. |
Okay. |
Not allowed. |
--- |
To define cost profiles for items, use the Cost Profiles (CM_PROFILE_DEFN) component.
Use the Cost Profiles page (CM_PROFILE_DEFN) to establish the cost profile to determine how items are costed in the business unit's cost book.
Navigation:
This example illustrates the fields and controls on the Cost Profiles page. You can find definitions for the fields and controls later on this page.
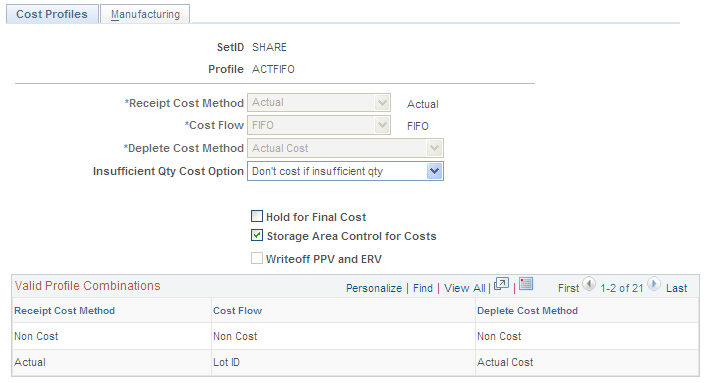
The next step in setting up the system is to determine the methods that you want to use to value inventory items. In PeopleSoft Cost Management, you assign cost profiles to items to determine the costing of inventory transactions for that item. PeopleSoft Cost Management offers a number of options for cost profiles that you can mix and match to suit your requirements. Different items or groups of items within a business unit may use different cost profiles, and the same item in different business units may also use different cost profiles.
A profile determines the costing method that is used to value receipts, depletions, and inventory stock.
The Receipt Cost Method, Cost Flow, and Deplete Cost Method fields cannot be changed once a transaction using this cost profile is entered into the costing records (that is, CM_RECEIPTS table).
Receipt Cost Method
The Receipt Cost Method is the method that PeopleSoft Cost Management uses to account for receipts to inventory. Receipts from PeopleSoft Purchasing and completions from PeopleSoft Manufacturing become putaways into PeopleSoft Inventory. PeopleSoft Cost Management tracks and accounts for each putaway. The Receipt Cost Method tells the system how the putaway is costed.
Field or Control |
Description |
---|---|
Actual |
The purchased item is valued at the PO price. You can also optionally adjust the cost based on the invoice price. The manufactured item is valued by the production ID that is closed for accounting. |
Non Cost |
The receipt of the inventory item carries no cost and is not processed by PeopleSoft Cost Management. This profile is used for inventory items for which you want to maintain quantity-on-hand information but do not want to account for value. PeopleSoft Cost Management does not support interunit pricing for non-cost items. Once transactions have been generated using this cost profile, do not change the non cost option without first removing all on hand quantity from the item/business unit. Run the Inventory Balance report (INS9090) and the Cost Management On hand Balance Validation report (CMS9010) to find all on hand balances. |
Std Cost |
The receipt is valued at the current frozen standard cost. The cost can be manually entered by you or calculated as a result of a cost roll-up. |
Cost Flow
The Cost Flow determines how you want depletions to occur. Although the choice is often a reflection of the physical flow of goods, the choice that you make here does not need to follow the true physical flow of items, especially when it is not practical or significant enough to track the specific flow of quantities. This is the accounting assumption for a particular book. As depletions from inventory are processed, PeopleSoft Cost Management uses this part of the cost profile to determine which putaway can be assumed to have satisfied the depletion and assign putaways to depletions.
Field or Control |
Description |
---|---|
FIFO (first in, first out) |
The oldest items and therefore the oldest costs are used to value inventory depletions (customer shipments, material stock requests, or issues from one stock location to another). The remaining inventory is valued at the most recent costs. When each putaway tends to be similar to all other putaways, this frees users from the need to track item attributes other than the item itself when processing inventory transactions. PeopleSoft Cost Management takes on the task of tracking which putaways are assumed to have available quantities and satisfies depletions in a first-in, first-out manner. The flow of costs are independent of the physical material movement. If you prefer, more physical flow granularity can be achieved with the storage area control option. |
LIFO (last in, first out) |
The newest items and therefore the newest costs are used to value depletions. The remaining inventory is valued at the oldest costs. Similar to FIFO, this method allows you to assign costs to depletions without detailed tracking of physical movement. |
Lot ID (specific identification by lot ID) |
If the item is lot controlled, the cost of the specific lot is used. This offers you a specific method of tracking quantities and costs by lot. |
Non Cost |
This value is entered by the system when you select Non Cost for the receipt cost method. The receipt of the inventory item carries no cost and is not processed by PeopleSoft Cost Management. This profile is used for inventory items for which you want to maintain quantity-on-hand information but do not want to account for value. |
Serial ID (specific identification by serial ID) |
If the item is serial-controlled, the cost of the specific serial ID is used. This offers you a specific method of tracking quantities and costs by serial ID. |
For lot ID, FIFO and LIFO items, it may take more than one putaway to satisfy depletions. A fully satisfied depletion is referred to as a depleted depletion. That is, using the cost flow that is specified, PeopleSoft Cost Management found enough on-hand quantities in putaways to satisfy the depletion.
Deplete Cost Method
The deplete cost method is the method that is used to assign a cost to the depleted depletion. Options are:
Field or Control |
Description |
---|---|
Actual Cost |
Items use the actual cost of the putaway for the depleted depletion cost. Since PeopleSoft Cost Management tracks the actual cost for each putaway and knows which putaways are used to satisfy each depletion, the system knows the cost of the goods that are depleted. In the case of a specific identification cost flow such as lot ID or serial ID, the cost of goods that is depleted is more exact. In the case of FIFO or LIFO flowing items, PeopleSoft Cost Management lets you trade exactness for ease of administration, especially when it is not feasible or effective to track individual instances of items. For purchased items, the actual cost is the PO price, or an entered cost if you are doing express putaways, or the invoice price from PeopleSoft Payables, if it is available. At putaway, if the production ID (PID) is not closed, we use the current actual cost since we don't have the true cost. Once the PID is closed for accounting, we will adjust the items cost based on the PIDs finalized costs. Actual costs are stored in the records CE_ACTUAL_COST and CM_ACTUAL_COSTB. |
Non Cost |
This value is entered by the system when you select Non Cost for the receipt cost method. The receipt of the inventory item carries no cost and is not processed by PeopleSoft Cost Management. This profile is used for inventory items for which you want to maintain quantity-on-hand information but do not want to account for value. PeopleSoft Cost Management does not support interunit pricing for non-cost items. |
Periodic Weighted Average |
Depleted items use the periodic average cost calculated as of the run date that is used on the Transaction Costing process (CM_COSTING). The Transaction Costing process (within the Cost Accounting Creation process) may be run in two modes: Mid Period mode or Regular mode. If the process is run in Mid Period mode, the depleted depletion costing is postponed. The process waits to be run in Regular mode before attempting to calculate a periodic average cost for the depleted depletions. This allows you to run the Transaction Costing process as often as you like during a period to capture other information that you need to manage the business without prematurely computing periodic costs for these items. Once the Transaction Costing process is run in Regular mode, the periodic average cost is calculated and this one average is applied to all depleted depletions for the item during this period. The period is defined as the time that elapsed since the last time that the Transaction Costing process was run in Regular mode. Periodic average costs are stored in the CM_PERDAVG_COST record. |
Perpetual Weighted Average |
The perpetual average cost is a rolling average that is based on the current quantity on hand valued at the current average cost, plus the receipts at the receipt cost, divided by the quantity on hand and the quantity received. The perpetual average is recomputed for every putaway by the inventory putaway processes based on PO price or manufacturing cost. Perpetual average cost items use the average cost that is in effect at the moment that the depletion transaction occurs. For example, if a purchased item is put away at the PO price and the invoice (voucher) is not yet received and processed, then the weighted average calculation includes the PO price at the time of putaway. The invoice price is not part of the weighted average at this time. Once the invoice arrives, you have the option of applying the PO-Voucher difference to the item's weighted average. In the case of a manufactured item being placed into PeopleSoft Inventory, the production ID may not yet be completed and the actual cost may not be available at the time that the finished goods are put away. Therefore, the putaway processes use the current weighted average cost. As production is closed for accounting, the average costs are adjusted. The adjustment amount is always applied to the item perpetual average. You do not have the option to apply or not apply the adjustment. Perpetual average costs are stored in the CM_PERPAVG_COST record. |
Retroactive Perpetual Average |
The retroactive perpetual average cost computes a new average for each putaway, just like the perpetual average method; however, this perpetual average cost is calculated at the end of the period and applied retroactively to the depleted depletions. The period is defined as the time that elapsed since the last time the Transaction Costing process was run in Regular mode. This method enables you to value each individual depleted depletion transaction using the current perpetual average cost at depletion time and yet still delay the calculation of the average until the end of the period when more cost information is captured for a more accurate average cost. In other words, this method enables you to capture a more accurate average by delaying the calculation of the average until later in the period when the vouchers or production completions are available. This increases the accuracy of the average cost. The retroactive perpetual average is calculated when the Transaction Costing process is run in Regular mode. If the Transaction Costing process is run in Mid Period mode, no retroactive perpetual averages are calculated. Retroactive perpetual average costs are stored in the CM_PERRAVG_COST record. |
Value at Current Standard |
Items use their current frozen standard cost for the depleted depletion cost. Frozen standard costs are stored in the production cost (CM_PRODCOST) record. |
Insufficient Qty Cost Option
If you are using the negative inventory feature in PeopleSoft Inventory, this option enables you to control how depletion transactions are costed when the item quantity dips into negative quantity. The options are:
Field or Control |
Description |
---|---|
Always cost insufficient qty |
Enables the Transaction Costing process (within the Cost Accounting Creation process) to cost negative inventory depletion transactions before sufficient quantity is entered into the business unit. These costs can later be adjusted when sufficient quantity is placed in the Inventory business unit by putaway or adjustment transactions. |
Cost in Regular Mode Only |
Enables the Transaction Costing process, run in Regular mode only, to cost negative inventory depletion transactions before sufficient quantity is entered into the business unit. These costs can later be adjusted when sufficient quantity is placed in the Inventory business unit by putaway or adjustment transactions. If Transaction Costing is run in Mid Period mode, then the depletion transaction is costed up to the currently available quantity and the remainder is held. |
Cost to point of zero quantity |
Enables the Transaction Costing process to split a negative inventory depletion transaction and cost part of the depletion transaction up to the currently available stock quantity. The remaining depletion transaction is held until sufficient stock is received. |
Don't cost if insufficient qty |
Enables the Transaction Costing process to delay costing the entire negative inventory depletion transaction until sufficient stock is received to cover the depletion transaction. This is the default setting. |
Note: The negative inventory feature is activated by selecting the Allow Negative Inventory check box on the Inventory Definition-Business Unit Options page.
Note: If Periodic Weighted Average is entered as the Deplete Cost Method, then negative inventory depletion transactions cannot be costed before sufficient quantity has been received into the business unit. The Cost Profile can only use Don't cost if insufficient qty or Cost to point of zero quantity as the Insufficient Qty Cost Option.
Cost Element Option
This option is enabled when you select a deplete cost method of perpetual average or retroactive perpetual average.
Field or Control |
Description |
---|---|
Default Cost Element |
Maintain the item's perpetual average cost by the default cost element. This option combines all costs into the primary cost element and calculates one average cost per item. |
Maintain Avg by Cost Element |
Maintain the item's perpetual average cost broken out by each cost element that is defined for the item. |
Average cost at the cost element detail level only makes sense for items that consistently use the same cost elements for all putaways and if cost element level averages are required for reporting and accounting purposes.
Hold for Final Cost
The Hold for Final Cost check box delays the calculation of actual cost and standard cost variances for items until the final costs are received from PeopleSoft Payables or PeopleSoft Manufacturing. The benefit of this option is to minimize the number of extra accounting entries from PeopleSoft Cost Management. Without this option, the cost of the item is calculated when the item is put away into inventory at the currently available price (from the PO or production ID). This cost is later adjusted for any prices variances, such a, the invoice price or additional manufacturing costs. With this option and the Transaction Costing process run in Mid Period mode, the costing of all putaways and depleted depletions that are tied to unfinished costs (unvouchered and unmatched POs or production IDs with incomplete costs) are postponed. Costing of receipts and depletions is put on hold until the production is complete or PO, receipt, and vouchers are matched; this reduces the need for adjustments. If you run a period-end process, all transactions are costed by using the available cost, regardless of this check box setting.
For purchased items using actual cost, as supplier invoices (vouchers) are entered and matched to the PO and receipt ID by PeopleSoft Payables, PeopleSoft Cost Management is notified of the exact amounts that are vouchered for each receipt. PeopleSoft Cost Management is then able to adjust all receipts, depleted depletions, and variance calculations for costed transactions to the new revised cost and creates the necessary accounting entries for these adjustments. However, if you prefer to postpone the costing of quantity movements until the vouchers are been fully matched, you may select this option.
For makeable items, the Hold for Final Cost option delays the cost calculation of the manufactured item until the final costs from PeopleSoft Manufacturing for all components, conversion costs, or overhead costs are completed; reducing the number of variance adjustments that are needed. If you do not select the Hold for Final Cost option, then the Transaction Costing process calculates the cost of a manufactured item when the production ID is closed for accounting.
The Hold for Final Cost check box does not restrict the flow of item quantities through inventory. PeopleSoft Cost Management keeps track of uncosted and unaccounted-for quantity flows and catches the cost up with those flows as required by period-end requirements or when the final cost is determined, whichever comes first.
Writeoff PPV and ERV
For purchased items only, select this check box to record any differences between the purchase order price and the vouchered price in an expense account rather than catching up the adjustments with the inventory receipt and depletion transactions. This check box is only available if you have selected Actual for the Deplete Cost Method. The variance is inserted into CM_VARIANC_COST record using the transaction group 400 Std/Actual Cost PPV) and the transaction group 402 (Std/Actual Cost ERV). If this check box is not selected, then both the PPV and ERV are applied to the inventory receipt and depletion transactions; however, if the IFRS Reporting check box is selected on the cost book, cost profile group, or the item business unit definition, then the ERV portion is expensed. For additional information about setting up IFRS reporting, please see the Valuing Inventory for IFRS section within the Costing Transactions and Creating Accounting Entries topics.
Storage Area Control for Costs
Check Storage Area Control for Costs if you want to apply the FIFO or LIFO depletion method at the storage area level. This means that the system uses FIFO or LIFO costing based on the receipts to the specific storage area from which the item is depleted. You can use storage area control with or without location accounting. However, if you use location accounting, it is strongly recommended that you use storage area control. If the FIFO or LIFO costing of depletions should apply to all receipts at the business unit level, this option can be set to off (unchecked).
Valid Profile Combinations
The combination of receipt cost method, cost flow, and deplete cost method that you select must match one of the valid combinations that appear at the bottom of the page.
If you select a receipt cost method of Non Cost, the system sets the cost flow and deplete cost method fields to Non Cost.
If you select a receipt cost method of Actual or Std Cost, neither the cost flow nor the deplete cost method can be Non Cost. Otherwise, an error message appears.
Cost Profiles - Manufacturing Page
Use the Cost Profiles - Manufacturing page (CM_PROFILE_DEF_MFG) to for items that are used in PeopleSoft Manufacturing, enter additional cost profile information to define the costing methods for labor and machine costs.
Navigation:
This example illustrates the fields and controls on the Cost Profiles - Manufacturing page. You can find definitions for the fields and controls later on this page.
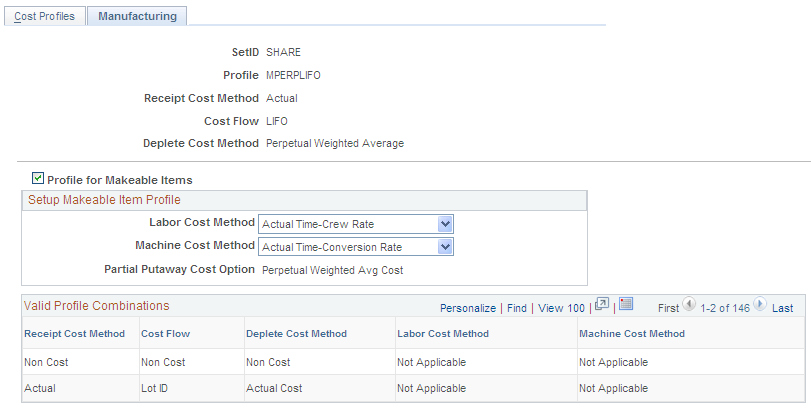
Field or Control |
Description |
---|---|
Profile for Makeable Items |
Select to define this cost profile for makeable items used in PeopleSoft Manufacturing. This check box activates the Labor Cost Method and Machine Cost Method fields for entry. For standard cost items, the relevant values are defaulted into the Labor Cost Method and Machine Cost Method fields and are not editable. |
Labor Cost Method
If you use PeopleSoft Manufacturing, use this field to specify how labor costs are calculated. This cost profile should be attached to the make item.
Field or Control |
Description |
---|---|
Actual Time - Conversion Rate |
Labor costs are computed by using the production ID's actual time on the Record Actual Hours page and the conversion rates on the Conversion Rates page (by cost type/cost version). |
Actual Time - Crew Rate |
Labor costs are computed by using the production ID's actual time on the Record Actual Hours page and the rates on the Crew Actual Cost page. |
Not Applicable |
Labor costs are not calculated for this item. |
Standard Time - Conversion Rate |
Labor costs are computed by using the standard times that are established on the Define Routings - Operations: Times page and the conversion rates that are on the Conversion Rates page (by cost type or cost version). This is the default setting for standard cost items. |
Machine Cost Method
If you use PeopleSoft Manufacturing, use this field to specify how machine costs are calculated. This cost profile should be attached to the make item.
Field or Control |
Description |
---|---|
Actual Time - Conversion Rate |
Machine costs are computed by using the production ID's actual time that is on the Record Actual Hours page and the conversion rates that are on the Conversion Rates page (by cost type or cost version). |
Not Applicable |
Machine costs are not calculated for this make item. |
Standard Time- Conversion Rate |
Machine costs are computed by using the standard times that are established on the Define Routings - Operations: Times page and the conversion rates that are on the Conversion Rates page (by cost type or cost version). This is the default setting for standard cost items. |
Valid Profile Combinations
The combination of receipt cost method, cost flow, deplete cost method, labor cost method, and machine cost method that you select must match one of the valid combinations that are displayed at the bottom of the page.
To define cost profile groups, use the Cost Profile Group (CM_GROUP_DEFN) component.
Use the Cost Profile Groups - Books page (CM_GROUP_DETAIL) to link the cost book and cost profile together under the cost profile group.
Navigation:
This example illustrates the fields and controls on the Cost Profile Group Books page. You can find definitions for the fields and controls later on this page.
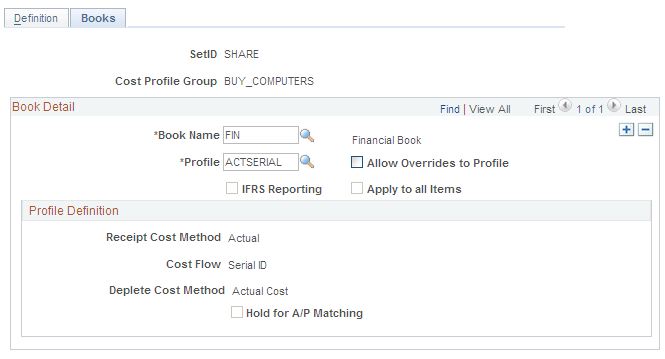
Cost Profile Groups are designed to minimize the maintenance of item cost profiles by defaulting the proper cost profile into the business unit, item, and cost book combination. Cost Profile Groups are used to associate items with like costing profiles. First you give the cost profile group a description, then you associate it with a cost book and cost profile. By assigning the profile to the book and associating the book and profile to a cost profile group, all items that are assigned to that group use the specified cost profile as the default.
You can have any number of profiles to cost the items. Each profile can be associated to a unique book so that entries can be made to various ledgers based on different cost assumptions.
Field or Control |
Description |
---|---|
Allow Override to Profile |
If you select this option, the cost profile can be changed on the Define Business Unit Item - General: Costing page. The value for the cost profile can appear by default from the cost profile group that is entered on the Item Definition - General page. If this option is not selected, then the cost profile cannot be changed on the Define Business Unit Item - General: Costing page. |
IFRS Reporting |
Select this check box to enable this cost profile group to set up support for the International Financial Reporting Standards (IFRS). This check box cannot be selected if the cost profile group uses the LIFO cost flow method. For additional information about setting up IFRS reporting, please see the Valuing Inventory for IFRS section within the Costing Transactions and Creating Accounting Entries topics. See |
Apply to all Items |
If you change the profile for a book, you can optionally check Apply to all Items. This function provides a utility to apply cost profile changes throughout all business units in this SetID that use this book and have items that are in this cost group. This feature is especially useful during initial implementation if you develop item definitions in a repetitive manner. You may make changes at the SetID level and have those changes propagated down through the business units automatically with this function. When you first enter the page, this option is always deselected. If the option is selected, the changes that you make are propagated through the business units upon saving the PeopleSoft Inventory business unit. The system is careful to not permit changes to cost profiles in those business units where you have already started processing transactions. Once transactions have started with active cost profiles, changes are no longer allowed to protect the accounting validity of the book. |
As items are added to inventory business units, it is required that a cost profile be defined for each cost book that is used by the business unit. This ensures a complete set of accounting entries for each book. Methods for adding the cost book and cost profile to the item within an inventory business unit include:
Automatic Default Approach: Enter the cost profile group on the Item Definition - General: Common page as you define the item at the SetID level.
Then, when you create the item ID and inventory business unit combinations by using the Define Business Unit Item component, the cost book and cost profile that is defined for the cost profile group appear by default on the Define Business Unit Item - General: Costing page. Use this method if you plan to use the same cost book and cost profile for every inventory business unit where this item is used.
Non-Automatic Default Approach: Enter the cost profile for each item ID and inventory business unit combination by using the Define Business Unit Item - General: Costing page.
The cost book appears by default from the inventory business unit definition. Use this method if the cost profile that is used for the item varies by inventory business unit.
Use a combination of both methods by moving the book and profile by default from the SetID level and then changing the cost profile on any Define Business Unit Item - General: Costing page that does not follow the default method.
Be sure to select Allow Overrides to Profile on the cost profile group if users at that item-in-business unit level should be able to modify cost profiles.
Note: An item cannot use a cost profile with the cost flow methods of lot ID or serial ID unless the item is defined as lot or serial controlled.
Note: On the Define Business Unit Item - General: Costing page, the Used in Mfg check box indicates that the item is used in manufacturing.
To define cost elements, use the Cost Elements component.
Use the Cost Elements page (CM_ELEMENT) to cost elements categorize the components of an item's cost.
The system maintains an item's cost-by-cost element. Cost elements also help define the debit and credit ChartFields in transaction processing.
Navigation:
This example illustrates the fields and controls on the Cost Elements Page. You can find definitions for the fields and controls later on this page.
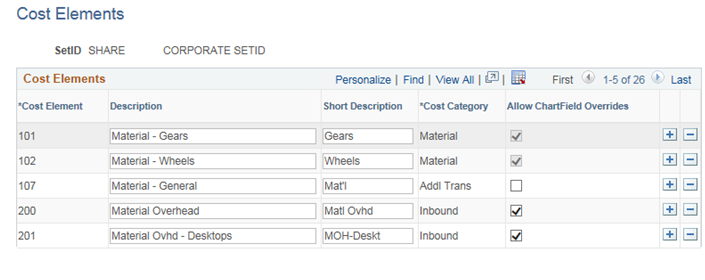
Use the Cost Elements page to define or maintain cost elements, which are used to categorize different components of an item's cost. An item's cost is calculated and maintained by cost elements. You can use cost element categories to define the costs at a summarized or very detailed level by using one or many cost elements. Cost elements also help define the ChartField combinations that are used to create accounting entries during the Accounting Line Creation process.
When defining cost elements, you must associate the element with a predefined cost category. Options are:
Field or Control |
Description |
---|---|
Addl Trans (additional transfer costs) |
Additional transfer costs are the expenses that are associated with transferring stock from one inventory business unit to another. They include expenses such as freight and handling. |
Con Ovhd (conversion overhead) |
Conversion overhead costs are the overhead expenses that are associated with the assembly process. They include expenses such as utilities, operating supplies, rent, manufacturing supervisor expenses, or assembly department benefit expenses. This category is used only in a manufacturing environment. Note: The flag is hidden, the reason is based on the test, conversion or conversion overhead cost is not displayed when performing the primary transactions. |
Conversion |
Conversion costs are the direct, nonmaterial costs (including labor and machine costs) that are involved in the manufacture of items. This category is used only in a manufacturing environment. Note: The flag is hidden, the reason is based on the test, conversion or conversion overhead cost is not displayed when performing the primary transactions. |
Inbound |
Inbound costs are the overhead expenses that are associated with procuring material such as inbound freight, duty, purchasing, receiving and inspection, or warehousing. Use the inbound cost category when you do not need to track the variances that are associated with these types of costs. |
Landed |
Landed costs are the miscellaneous charges that are needed to bring an item in-house. They can include charges such as freight, handling, sales and use tax, and value-added tax. Landed costs can be charged by the merchandise supplier or by a third-party such as a shipping organization. Use the landed cost category to track the variances that are associated with these types of costs. |
Material |
Material costs are associated with the direct cost of an item, typically the cost to procure the item exclusive of any overhead (if purchased), or the sum of the lower level component's purchase costs (if manufactured). The flag should be checked and grayed. |
Other |
Other costs are used for any additional costs that are not covered in the other categories. |
Outbound |
Outbound costs are the overhead expenses such as material handling, staging, or warehousing that is associated with shipping material. |
Allow ChartFields Override |
The Material Cost Category will always be checked. For all other Cost Categories the ChartFields Override entered for the Material Cost will also be applied to the selected Cost Categories. |
PeopleSoft Cost Management uses the cost categories throughout for reporting purposes. Additionally, the system uses only certain categories of costs for certain transactions. PeopleSoft Cost Management uses the costs that are associated with conversion, conversion overhead, material, inbound, landed, and other cost categories to value inventory and all the transactions. For shipments, outbound costs are also included.
Once you define the cost elements, attach the appropriate cost elements to the different costs that are generated by PeopleSoft Cost Management, including:
Attach a default cost element to items by using the Define Business Unit Item page. This cost element is used when valuing receipts.
Use landed cost elements to categorize landed costs by using the Misc Charge/Landed Cost Definition page.
Use additional transfer cost elements to categorize interunit transfer costs by using the Transfer Pricing Definition component.
For a purchased item using standard cost:
If you are not using the Cost Rollup process, then define cost elements for the items by using the Item Production Costs page. This is not a recommended method.
If you are using the Cost Rollup process to calculate costs, then define cost elements on the Additional Item Costs page.
For makeable items, use the cost elements to define costing conversion rates, costing conversion overhead rates, additional item costs, and forecasted purchase costs.