Understanding Additional Sales Order Options
PeopleSoft Order Management supplementary features increase efficiency, add information, and improve system flexibility. This section discusses:
Currency and credit currency information.
Delete line and delete schedule.
Product alternates.
Deliveries.
Total order and line reservations.
Reservation and backorder defaults.
Available to Promise (ATP).
Distribution codes.
Routes.
Direct shipping products.
Sales order messages.
Sales orders from contracts.
You can have only one currency per order. You can change the currency for the order before lines are added. The default value for the currency comes from the value established on the General Info page for the customer.
When you are viewing customer available credit, the system uses the Credit Check Currency field to bring all open receivables in multiple PeopleSoft Receivables business units to a common currency. If the customer has open receivables with different currencies in different PeopleSoft Receivables business units, the system converts the open amounts to a single credit-checking currency and then subtracts them from the customer's credit limit. The credit-checking currency can be different from the sales-order transaction currency.
You can quickly delete a new line or schedule if there is no quantity entered by selecting Delete Line from the Line Menu field on the Order Entry Form page or Delete Schedule from the Schedule Menu field on the Shipment Schedules page. Use these options if you accidentally enter a new line or schedule and must remove it. If you have not yet saved the line, you may change the quantity to zero and delete the line, or you may change the status to Canceled. If you have saved the line, you must change the status to Canceled to make it invalid for the order.
You can define product alternates and substitute those alternates for products under the conditions:
You have set up one or more alternates for a product on the Alternates page.
The sold to customer allows substitutions, as established on the Sold To Options page for the customer.
The alternate exists in the same PeopleSoft Inventory business unit as the original product.
The order date is within the start and end dates for the alternate product.
The alternate product does not have an associated message with the action of Reject.
The alternate product is an active product.
The View Product Alternates link in the Order Lines section of the Order Entry Form page is available only when alternate products exist for the product ID entered in the selected PeopleSoft Inventory business unit and if your customer allows substitutions.
When you select a product alternate, the system displays the alternate product ID on the order line. This enables you to maintain demand information for analysis and to print both product IDs on order acknowledgments and in other documents when there is a change.
The system also makes item substitutions during the picking process, if your customer allows substitutions and there are suitable substitutes for the product or item requested.
If the sales order delivery processing feature is turned on for the Order Management business unit, the system will automatically group sales order schedule demand into deliveries. The grouping is configured for each Inventory business unit to define which sales order demand attributes must match to be grouped in the same delivery. This way, at order entry time, you can view the number of shipments that you might have for the order. Based on the deliveries created, you can then calculate freight charges for each shipment individually and accumulate the freight charges for each shipment to obtain the order total freight charges. If you are integrating with a third party freight system, you can also use the freight shopping feature in order entry to choose different carrier IDs for the sales order shipment schedules and regroup the schedules into new deliveries for the most efficient freight options. Deliveries also enable you to use weight and volume pricing to offer discounts and surcharges if the shipment weighs out or cubes out. You can use deliveries for both sales orders and quotes.
See Setting Up Delivery Management.
See .Understanding Internal Freight Calculations
These fields must be the same to group schedules into the same delivery:
Inventory business unit.
Scheduled shipment date.
Document reference number.
In addition to the two required fields, you can further define deliveries by selecting other attributes on the Inventory Definition - Business Unit Options: Delivery Management Definition page.
For example, you might group order schedules that have the same ship via code, freight terms, and ship-to customer into one logical shipment. If the inventory is available for these items, they are shipped together.
You can have different delivery definitions for each PeopleSoft Inventory business unit.
Note: For weight and volume pricing, include the ship via code in the delivery definition. The ship via code determines minimum and maximum weight or volume limits. These limits are automatically managed at order entry time.
Note: If you override the ship-to address during order entry, the system creates a new delivery only if any of the fields are different: State, Country, and Primary Address - Ship To.
The delivery ID is assigned when the order schedule is created or modified. The Order Management business unit processing option selected on the Order Entry Features page determines whether you use deliveries and whether you want deliveries to be assigned when you change the field or save the page. If you elect to have deliveries assigned when you change the field, you can modify the delivery if you changed any of the required or optional fields that were used to group the delivery on the Delivery Management Definition page.
Note: Deliveries are available only for open schedules. Non-inventory order schedules or direct-shipped schedules are excluded.
During order entry, you can view shipping information for the delivery on the Deliveries page, and you can see the schedules that make up the delivery on the Schedules on Delivery page.
Ship Via Weight and Volume Test for Deliveries
If you include the ship via code field as part of the delivery definition, the system looks at the ship via to see if the delivery cubes or weighs out. The cube and weight dimensions are stored on the Ship Via page. The system checks both the volume and weight for the delivery against the minimum and maximum dimensions on the ship via to see if the shipment weight and cube fall within the specified parameters.
If the new order schedule causes the delivery to violate the cube or weight limits for the shipping method, the system automatically places the new schedule on a new delivery. If the new schedule as a whole violates the shipping method cube or weight limits, the system displays a warning message to the CSR when the order is saved. The CSR should then change the shipping method for the schedule or break the order line into multiple schedules so that the system can create separate deliveries.
To cube or weigh out, the delivery has to fall within the minimum and maximum values defined for the volume or weight.
If the delivery falls within:
The volume dimensions but not within the weight dimensions, then the system uses the volume to determine weight and volume pricing.
The weight dimensions but not the volume dimensions, then the system uses the weight to determine weight and volume pricing.
Both the volume and weight dimensions, then the system uses the first price rule in the weight and volume arbitration plan.
All weight and volume price adjustments for the deliveries will be summed together and added to the total order adjustments at the order header level.
The example demonstrates how the system uses weight for weight and volume pricing:
You have an order with five lines and one delivery.
The delivery contains schedules one through five.
A truck or container load is equal to 35,000 to 40,000 pounds or 3,500 to 4,000 cubic feet.
The schedule one weight is 10,000 pounds and 1,000 cubic feet.
The schedule two weight is 15,000 pounds and 500 cubic feet.
The schedule three weight is 7,000 pounds and 500 cubic feet.
The schedule four weight is 3,000 pounds and 100 cubic feet.
The schedule five weight is 5,000 pounds and 200 cubic feet.
The order should weigh out at 40,000 pounds and qualify for the weight and volume pricing discount.
When you save a sales order with a status of Open, the system writes to the demand table that PeopleSoft Inventory reads to reserve product quantities. The Material Reservation process runs against this table periodically, based on parameters that you define in the Process Scheduler.
To create soft reservations for orders or order lines without waiting for the Material Reservation process to run, save the order with a status of Open. To reserve the entire order, select Reserve Order from the Header Menu field on the Order Entry Form page. To reserve an individual line, select the individual line and select Reserve Line from the Line Menu field of the Order Entry Form page. All schedules associated with the line are reserved at the same time.
You can cancel a reserve by canceling the order line or schedule or by decreasing the quantity. Restrictions for decreasing quantity and canceling demand is controlled by the demand change configuration on the inventory business unit. You can also cancel an order line reserve using the Undo Fulfillment process in PeopleSoft Inventory.
You can select the auto-reserve option on the Order Entry Features page to automatically reserve the order lines when you save the order. This enables automatic reservations of everything on the order where possible.
Note: If an item is marked as a demand priority item, the system ignores it when you reserve the order or line.
See Establishing a PeopleSoft Inventory Business Unit Structure
Reservation/Backorder fulfillment rules are used during fulfillment to determine when to hold demand in the unfulfilled state until enough quantity has been reserved and to determine in what state to backorder demand if enough quantity is not available. Order Management uses the reservation/backorder rule defaulting engine to default the reservation/backorder rules to the order schedule:
Header level reservation rule
Line level reservation rule
Line level backorder rule
Line level backorder reservation rule
These order schedule reservation and backorder rules can be modified on the order schedule page and they are passed to inventory.
Note: Changes to these rules for existing sales orders are not changed or reevaluated but the changes are passed to Inventory. Rule changes on existing demand lines must be changed in Inventory. For example, if rule is entered on the sales order and the Inventory Business Unit Ship From is changed, the rules are not reevaluated.
You can calculate ATP quantities to promise orders against future supply in PeopleSoft Inventory. The system uses the APICS-standard ATP calculation. In PeopleSoft Order Management, you can perform ATP checks online to see more detailed information about sources of supply and demand.
See Understanding Inventory Reservations.
ATP Calculation Method During Online Sales Order Entry
ATP will be calculated after you enter the product and quantity on the line or schedule:
If the Skip Promising option on the Ship Options tab of the line or schedule is not selected when you save the order.
When you select ATP Decision from the Header or Line menu on the Order Entry Form page or from the Schedule Menu from the Shipment Schedules page.
If the entire quantity requested is available on the date requested, the system promises the item to the sales order schedule without displaying any additional information.
If you select the header or line level, the system will perform the ATP calculation for all of the associated schedules. If the system cannot promise all of the schedules, you will be directed to the Sales Order Message page to address the situation. If there is only one schedule and there is not enough quantity available on the date requested, the system will display the ATP Decision page where you can select from one of three options:
The quantity that can be promised for the given scheduled shipment date. The quantity on the order line and schedule is changed to the amount available to promise on the scheduled ship date.
A date when the total requested quantity can be promised. The system updates the scheduled shipment date on the order line or schedule.
To split the order line into multiple schedules, with each schedule having the maximum quantity that can be promised for the different scheduled shipment dates.
To view availability information detail, select Item/Product Availability from the Line Menu field on the Order Entry Form page, the Schedule Menu field from the Shipment Schedules page, or the Review Product Information menu.
The examples illustrate how the system handles ATP processing for situations where the entire quantity is not available on the date requested.
Example of Quantity Meeting the Customer's Requested Quantity But Not the Requested Shipment Date
Step |
Action |
Result |
---|---|---|
Create a new order. |
The system pulls in the PeopleSoft Order Management business unit options. The requested shipment date for the line uses today's date (for example, 02/01/2006) as the default. |
|
Enter Product A (10001) and the quantity of 50 on Line 1. |
The system checks the order promise option for the item. Then the system enters the highest priority PeopleSoft Inventory business unit as the default in the order line and calculates the scheduled shipment date. |
The appropriate PeopleSoft Inventory business unit and scheduled shipment date (02/01/2006) appear automatically on the line. |
Select the ATP option. |
The system calls the ATP function for the PeopleSoft Inventory business unit. The requested quantity, scheduled shipment date, item ID, and Inventory business unit are passed to this function. |
The system retrieves the appropriate ATP function. PeopleSoft Order Management displays the quantity available to promise on the scheduled shipment date (02/01/2005), as well as the promise date when all 50 will be available. |
The three available options (based on the ATP information) are:
|
Based on the option selected, the system:
|
The system creates the schedules based on the selected options. |
Example of Quantity Not Meeting the Customer's Requested Quantity and Shipment Date
Suppose that a customer orders 100 of product A, but only 70 units are available according to the ATP calculation. In this example, the product is a buy item, and PeopleSoft Purchasing is installed. The standard lead time to purchase item 10001 is 10 days. In this case, you have these options:
Accept the amount available today (70).
Accept a later date when all 100 can be shipped together.
The scheduled shipment date is the order date plus the standard lead time (2/1/2006 plus 10 days equals 2/11/2006).
Create multiple schedules:
2/1/2006 quantity of 10
2/2/2006 quantity of 10
2/3/2006 quantity of 20
2/7/2006 quantity of 10
2/9/2006 quantity of 20
2/11/2006 quantity of 30 (based on standard lead time)
Example of Quantity Not Meeting the Customer's Requested Quantity and No Future Supply Is Available
Suppose that a customer orders 60 of product A, but none are available according to the ATP calculation. The product is a make item; the fixed lead time to make item A is 7 days, and the variable lead time is 3 hours. In this case, ATP returns no promise quantities or dates on the sales order.
The system calculates the scheduled shipment date as follows:
No other option is available.
PeopleSoft Order Management does not post entries directly to PeopleSoft General Ledger ChartFields except for incurred revenue from claimback claims. Instead, you select distribution codes that determine the accounts to debit and credit for invoice transactions, and the system passes the information to PeopleSoft General Ledger by way of PeopleSoft Billing. PeopleSoft Inventory manages the account distribution for the inventory transactions involved with a sale.
Set up distribution codes in PeopleSoft Billing or PeopleSoft Receivables. The codes reflect detailed account distribution information. Sales transactions are broken into discounts, revenue, and surcharges for distribution purposes. The entries in the discount distribution code, revenue distribution code, and surcharge distribution code fields establish the distribution code for each element of the transaction. Defaults for these fields may come from one of four places:
If you have associated discount and surcharge distribution IDs with your price rules, and the price rules are used for line or schedule pricing adjustments, then the system uses the discount and surcharge distribution IDs from the price rule.
If multiple price rules are used, and each price rule has a different discount and surcharge ID, each portion of the adjustment is allocated to the distribution IDs on the price rule. The system then selects the revenue account according to the hierarchy described in the next paragraphs. If no distribution IDs for discounts or surcharges are on the price rules, the default hierarchy also applies.
If you have established distribution rules and sets based on the elements of a sales order—customer, product, region, and so on—and the system finds a match with a distribution set, the default distribution codes come from that set.
The distribution rule code used to determine matches on the distribution sets is defined on the PeopleSoft Order Management business unit Accounting and Billing page.
If the distribution rule does not find a match, or if there is no distribution rule defined on the PeopleSoft Order Management business unit, the default for the distribution codes comes from the PeopleSoft Inventory business unit if the Inventory business unit has an associated PeopleSoft Billing business unit.
If the PeopleSoft Inventory business unit does not have an associated PeopleSoft Billing business unit, the default for the distribution codes comes from the PeopleSoft Order Management Accounting and Billing page.
Note: You can enter distribution percentages on the order schedule Distribution Percentages page to allocate a portion of the revenue, discount, and surcharge postings across multiple distribution IDs. This optional feature enables you to charge different departments or accounts for discounts taken on an order, or to allocate revenue across departments. The allocation percentages must add up to 100 percent.
You can change the entries during order entry on the Distribution Accounts page.
Note: If your price rules carry the distribution IDs for adjustments to the order line and schedule, you do not see the distribution IDs on the Distribution Accounts page. When distribution IDs are derived from a price rule, you cannot modify them. They are applied at billing time.
You can use routes to streamline deliveries. During order entry, you can assign the order to a route if the PeopleSoft Inventory business unit assigned to the schedule uses routes. In this case, the system searches the routes to find a match by PeopleSoft Inventory business unit, ship-to customer, address, carrier, and ship via code.
If the system doesn't find a match, it doesn't assign a route code. If the system finds a match, the system first calculates the scheduled ship date and time assigns the route code to the Ship Options tab on the Shipment Schedules page and then assigns the route stop number.
The system recalculates the scheduled arrival date and time by adding the transportation lead time to the scheduled ship date and time. The system performs the calculation when you save the order line; the system passes the calculation to the order schedule. If the new scheduled arrival date and time is later than the customer's requested arrival date and time, the system asks whether you want to override the scheduled arrival date and time. If you decline, the route is not assigned to the order schedule.
If the ship from PeopleSoft Inventory business unit, ship-to customer, address sequence number, scheduled ship date and time, carrier, and ship via values are changed after the route has been assigned, the system drops the route from the schedule.
You can still add a ship-to customer to a route on the Ship Options 2 tab on the Shipment Schedules page if the ship-to customer isn't part of the route definition. The scheduled ship date and time, carrier, and ship via code appear automatically.
Routes can also be assigned to electronic data interchange (EDI) orders using the same logic for orders entered during order entry.
Note: Routes will not be calculated and assigned for schedules marked for customer pickup.
Note: Routes will not be recalculated if third-party freight shopping assigns a different carrier ID to the order schedule. The schedule and its demand will be removed from the route.
In addition to shipping products from your own warehouses, you can ship them to customers directly from another supplier (that is, use direct ship from supplier.) You must have PeopleSoft Purchasing installed to use the direct ship from supplier feature in PeopleSoft Order Management.
If a product is always shipped directly to your customer, select the Direct Ship from Supplier option when you define the product on the Product Definition - Options2 page. Some products might typically ship out of your own warehouses, but in special circumstances, you may want them shipped directly from the supplier. In those cases, you can select the Direct Ship option on the Ship Options tab on the Order Line region of the Order Entry Form page and the Shipment Schedules page.
When the order is saved, the system flags the demand to be directly shipped from the supplier to the customer. Purchasing picks up this demand in the Requisition Loader Process and creates a new requisition. If you want it to be shipped to your warehouse, you can use the Alternate Sources of Supply page to choose additional options or use the Pegging Workbench. Alternate Sourcing and Pegging require additional setup.
Note: You can also create a "direct ship from supplier" purchase order from the sales order using alternate sources of supply. The purchase order is created and saved when the sales order is saved.
See .Understanding Alternate Sources of Supply
Direct Ship Process Flow
The following diagram illustrates the shipping process flow that occurs for schedules that are shipped directly from the supplier to the customer:
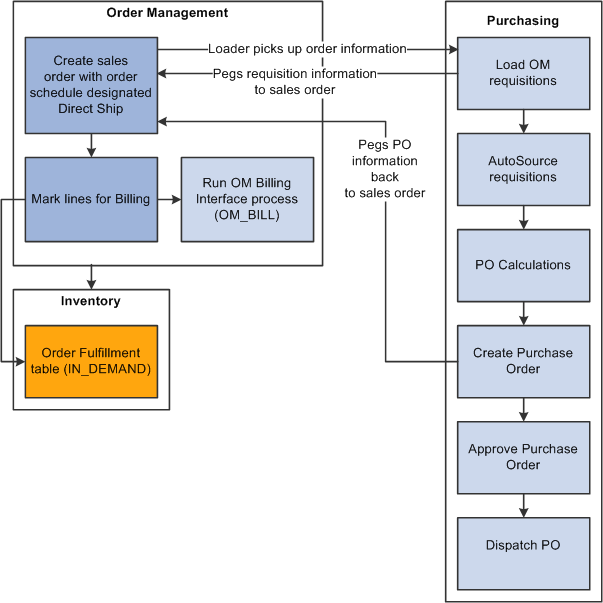
Direct shipping process
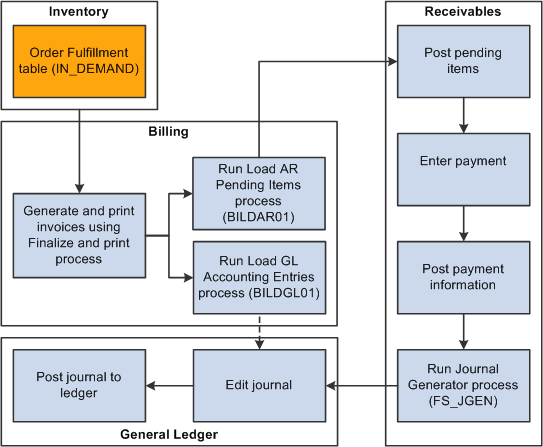
The steps describe the processing:
The Requisition Loader process in PeopleSoft Purchasing searches order schedules and ensures that the Direct Ship from Supplier option is set to Yes and that the order schedule (ORD_SCH_STATUS) is in Open status.
The process picks up the order schedules without holds that affect purchasing (PO_HOLD_FLAG=No), where the direct ship from supplier status (PO_DISTRIB_STATUS) is Active. The system creates requisitions, and, if the special handling flag (SPEC_HANDLE_CODE) on the order schedule is selected, it uses the shipping method code (SHIP_TYPE_ID) and carrier ID (CARRIER_ID) on the order schedule for the requisition schedule. This information is passed to the purchase order. If the product is configured, the Requisition Loader process also picks up the configuration code and template ID. When the Requisition Loader process picks up a direct shipped schedule, the system changes the direct ship from supplier status to Processed.
Requisition Loader creates pegging detail in the pegging tables to peg the requisition to the sales order schedule.
The AutoSelect process loads the information into the staging tables.
The PO Calculations process picks up the information from the staging tables, calculates the prices, and selects the suppliers.
The Create Purchase Orders process creates the purchase order and updates the Order Schedule record with the purchase order number. The Create Purchase Order process creates pegging detail to peg the purchase order to the sales order schedule.
The instructions to the suppliers on the purchase order are to direct ship the product to the customer indicated on the schedule.
The system inserts a pending line into the IN_DEMAND table for each direct ship from supplier order schedule when the schedule is saved. When the schedule is marked for billing the demand status is set to depleted.
Run the Mark Lines for Billing process (OMMARKLN) or manually record shipment lines for non-stock and direct ship from supplier schedules using the Mark Lines for Billing page.
To automatically record a depleted line for each non-stock order schedule when you save it with a status of Open, select the Mark for Billing at Order Save option on the PeopleSoft Order Management business unit Order Entry Features page.
When you run the Mark Lines for Billing process, you can mark order schedules for billing if a purchase order schedule is matched to a voucher in PeopleSoft Payables. The system inserts the line for direct ship from supplier schedules based on a purchase order schedule level match of the voucher in PeopleSoft Payables and PeopleSoft Purchasing. If the schedule has a value of M (fully matched), the system inserts a shipped line.
Note: If you run the Mark Lines for Billing process, you must select the Mark Direct Ship If Matched option on the Mark Lines for Billing Process page; otherwise, the process marks all direct ship schedules for billing, regardless of whether the voucher is matched.
You can run the Journal Generator process for these transactions from either PeopleSoft Billing or PeopleSoft Receivables.
Holds on Direct Shipped Schedules
You can set up hold processing for a number of sales order conditions on the PeopleSoft Order Management business Hold Processing page. With the Pass to Purchasing option, you determine whether the hold conditions prevent processing of direct ship from supplier orders and new purchase orders created from alternate sourcing in PeopleSoft Purchasing. You can also make this choice for holds that you apply manually or for messages that include holds.
If a direct ship from supplier order schedule is on hold and you have elected to prevent processing in PeopleSoft Purchasing for the hold condition, the Requisition Loader process does not pick it up. If you elected to create a new purchase order from alternate sources and the schedule is on hold, the PO is not created. If you selected the Pass to Purchasing option, the system sets the hold status for purchasing (PO_HOLD_FLAG) to No. In this case, orders are processed in PeopleSoft Purchasing even if the order line or schedule is on hold.
If there is a hold on a direct ship from supplier schedule that applies to processing in PeopleSoft Purchasing and the hold is removed, the system changes the purchasing hold status to No and the Requisition Loader process picks it up. If you chose to create a new purchase order from alternate sources, the PO is created when the hold is removed online and the order is saved.
If you put a direct shipped order schedule on hold after the Requisition Loader process has picked up the schedule, the system changes the direct ship status to Modified. Depending on the processing status within PeopleSoft Purchasing, this occurs:
When the requisition has been created, the requisition line is canceled.
When the purchase order has been created or dispatched, the requisition line is canceled and the quantity on the purchase order is decreased by the original requisition quantity.
If this decreases the purchase order quantity to zero, the purchase order line is canceled.
If the purchase order has been closed, no changes are made.
When the hold is removed, the Requisition Loader process picks up the direct ship from supplier schedule and creates a new requisition.
Changes to Direct Ship from Supplier Schedules
When the Requisition Loader process in PeopleSoft Purchasing picks up direct ship from supplier schedules, it changes the direct ship status of the schedule to Processed. With this status, additional Requisition Loader process runs ignore the schedule.
In addition to holds, PeopleSoft Order Management sets the direct ship status to Modified when you change any of the fields for direct shipped schedules:
Product ID.
Quantity.
Unit of measure.
Requested shipment date and time.
Requested arrival date and time.
Schedule status (Cancel).
In addition, if you selected the special handling option (SPEC_HANDLE_CODE), any changes in the carrier ID (CARRIER_ID) or shipping method (SHIP_TYPE_ID) change the direct ship status to Modified.
The Drop Shipments Update process on the Requisition menu in PeopleSoft Purchasing picks up modified schedules and updates the requisitions. If the requisition has been sourced to a purchase order or orders, each changed field generates a change request for each affected purchase order.
If you cancel the sales order schedule, the corresponding requisition schedule is canceled if the schedule has not already shipped. If purchase orders have been created, the purchase order schedule is also canceled. If you have selected the Mark Lines for Billing at Order Save option on the Order Entry Features page or manually run the Mark Lines for Billing process, you cannot cancel the schedule, because the system considers the order already shipped for billing purposes.
Note: If the purchase order has already been created for the requisition, changes made on the sales order will take effect immediately on the purchase order using the alternate sourcing order change functionality. Only the purchase order will be updated with the changes.
Messages are used through out the Order Entry Form component when the system runs into issues completing a request. The Sales Message page displays providing the CSR with information about the order. The CSR can accept the situation that the system encountered, provide additional information, or change the information so the situation is resolved.
The Sales Message page displays for situations in previous releases that were displayed using an error message on the screen after the order was saved.
In PeopleSoft Contracts, use the Sales Order page to determine which lines from a contract are sent to PeopleSoft Order Management. Once the lines are selected, the sales order is created in the Electronic Commerce staging tables. In addition to the Electronic Commerce process (OM_EC) the PeopleSoft Order Management batch processes (Order Completion, Hold Checking, Credit Checking, and Populate Demand) are run to generate the sales orders in the same manner as other incoming orders that are not entered through the online pages.
VAT, freight, tax calculations, and pricing are not handled in PeopleSoft Order Management for orders originating from PeopleSoft Contracts. Processing exclusions for VAT, freight, taxes, and price adjustments must be set up for 'CA' and 'RCA' source codes for both sales orders and quotes on the Exclusions by Source Code page. The Order Completion process uses the exclusions by source codes to avoid performing VAT, freight, tax calculations, and pricing. It also does not add distribution accounting and perform processing for buying agreements.
The system also uses order source codes to handle sales order processing for orders generated from PeopleSoft Contacts. You must set up 'CA' and 'RCA' order source codes on the Order Source Code page in addition to setting up exclusions by source codes.
Contract orders and replacement contract sales orders cannot be manually created in PeopleSoft Order Management. Changes to increase or decrease the quantity can be made, updates will be restricted, and you will not be able to add additional lines to the order. Changes made to a sales order originating from a contract must be manually updated in the contract in PeopleSoft Contracts. Similarly, any changes made to the contract order in PeopleSoft Contracts after the order has been inserted into the EDI staging tables must be manually made to the order in PeopleSoft Order Management.
You cannot copy from purchase history or copy orders in PeopleSoft Order Management for orders originating from PeopleSoft Contracts (denoted by 'CA' and 'RCA' source code).
PeopleSoft Contracts bills the orders generated from a contact. The Populate Billing (OM_BILL) process ignores orders with a source code of 'CA' and 'RCA'. All non-stocked and direct-shipped order lines with order source code of 'CA' and 'RCA' are processed using the PeopleSoft Order Management Mark Lines for Billing page (or auto-mark lines for Billing) to create the shipment and costing data in PeopleSoft Supply Chain Management. The Populate Billing process flags the CA and RCA shipments with BILLING_STATUS = "C" (billed from PeopleSoft Contracts) so that PeopleSoft Billing will not bill the orders.
Products used in PeopleSoft Contracts are set up on the Contracts Options page of the Product Definition.