Working With Substitute Items in Procurement
This topic provides an overview of Item Substitution in Procurement and discusses how to set up substitute items in Procurement.
Suppliers periodically backorder certain items and offer a substitute item that can replace the original item, thus avoiding shipping delays and partial orders. PeopleSoft Purchasing offers requestors in organizations or companies a way to track which items, according to the supplier, were back ordered and to procure automatically the supplier’s substitute item. After the buyer enables item substitutions, the system records current or future item substitutions at the time of requisition and updates the purchase order automatically. The system supports both manual and automatic selection of item substitutes based on the item SetID in order to dispatch an updated purchase order to the supplier, thus resolving matching issues between the purchase order and received items.
Item substitution is enabled in Procurement transactions when Item Substitution is enabled for the Purchasing Business Unit. You can specify whether items will be substituted manually or automatically in the requisition, in online Requisition Selection, in purchase order components, in a requisition, and during PO Batch Sourcing. You can also indicate whether a requester has the ability to accept or reject a substitute item in the requisition and whether a procured item will be visible to the end user.
Item substitution can be set up at the Item Supplier Location and Item levels. At each of these levels, you can control whether the item will be available for manual or automatic substitution or not available. The system will automatically search at the Item Supplier Location level for valid item substitutions using the item, supplier, and supplier location, and then it will select a substitute item whose Use for Procurement value is set for Automatic or Automatic and Manual substitution. If any substitutions are found, the system will select the substitute item with the highest priority and for which the transaction date is within the begin date and end date ranges. If no item substitution is found at the Item Supplier Location, then the system will search the Item Substitution level for valid items to substitute. If a substitute item is found, the user will be prompted to accept or reject the substitute item. If the user accepts it, then the substitute item will replace the item and the system will store the originally entered item in the Original Item Substituted field, convert the transaction unit of measure (UOM) to the substitute item’s UOM, and select the substitute item’s pricing into the transaction. Item substitution selection will be based on the original item substituted. Visual indicators will appear in procurement transactions to indicate whether an item was substituted. You can also use the Item Substitution Search icon to select item substitutions manually for your Procurement transactions.
Manual Item Substitution
Use the Manual Substitute Items search page to view all Substitute Items at both the Item Supplier Location level (if a Supplier ID/Location is available) and the Item SetID level if the Substitute Item is marked for Manual Substitution or for Manual and Automatic substitution.
You can access the Substitute Item search page from the Requisition line, the Requisition Selection line, or the Purchase Order line when you click the Item Substitution Search icon.
This example illustrates the fields and controls on the Substitute Items search page. You can find definitions for the fields and controls later following this example.
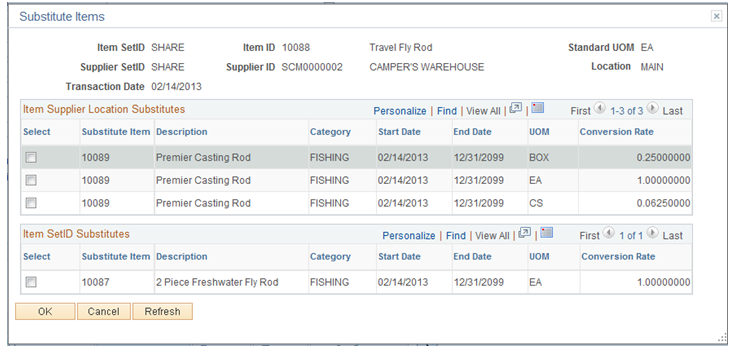
Field or Control |
Description |
---|---|
Description |
Displays the Substitute Item description for the selected Item ID. |
Category |
Displays the Substitute Item Standard UOM used for the item. |
Start Date and End Date |
Indicates the start and end dates. |
UOM |
Select the UOM (unit of measure) of the Substitute item that will be used in the transaction. If the Substitute Item does not have an Item Supplier relationship or if it does but Accept Any UOM is turned on, then the Substitute item UOM prompt field will display all Ordering UOMs for the Item ID. If the Substitute Item has an Item Supplier relationship and Accept Any UOM is turned off, then the Substitute Item UOM prompt field will display only Item Supplier Location UOMs. |
Conversion Rate |
Displays the quantity of the substitute item that is required to replace the original item. The default value is 1, however, you can modify the value as necessary. Conversion Rates are calculated by using the Substitute Item UOM listed and the Standard UOM of the Original Substituted Item. |
The search page displays all Substitute Items at both the Item Supplier Location level (if a Supplier ID/Location is available) and Item SetID level where the substitute item is configured as Manual Substitution or Manual and Automatic substitution. It also displays substitute items that are available on the Transaction Date that appears in the header of the Substitute Items search page.
If the PO Item Supplier Security option for the transaction’s PO business unit is Edit Required Must Use Item ID or Edit Required When Use Item ID, then the search page displays only substitute items that have an Item Supplier relationship established for the current supplier, which appears in the search page.
This page will not display Items that have the Accept Any Supplier check box deselected and that do not have an existing Item Supplier relationship.
The search page displays the Substitute Items that are in a Catalog assigned to the requester.
The search page will display the substituted items if the Original Substituted Item field on the transaction line has a value. If the Original Substituted Item field does not have a value, then the Item ID on the transaction line will appear in the search page.
Automatic Item Substitution
When auto item substitution is enabled for the Purchasing business unit, the system will automatically find substitute items if they are available when a purchase order or requisition is created or changed. If item substitutes exist for an ordered item, the following message will prompt the user to accept the suggested item substitute:
“A Substitute Item has been found. Do you want the Substitute Item to replace the current Item ID at this time? (Yes or No)”
If you select No, the system will not replace the current Item ID with the substitute item, and item substitution will not occur. The Automatic Item Sub check box will be deselected automatically in the Requisition line.
If you select Yes, the system will replace the current Item ID with the substitute item, all Item Substitution fields will be updated correctly, and UOM Conversion will be performed.
When a change is made to an existing Requisition or PO line, the following actions should occur:
If the Item ID field is changed and the Original Substituted Item field is populated, then the Original Substituted Item and Original Substituted Item description fields will be cleared and the Substitute Item in Use indicator will be disabled or hidden.
If the Qty or UOM is changed and the Original Substituted Item field is populated, then the Automatic Item Substitution steps repeat to check for substitute items for the original substituted item (not Item ID) as the current substitute item may no longer be valid after the change or a more appropriate substitute item may be available for the original substituted item.
If the Supplier ID is changed in a Requisition line or Purchase Order header and the Requester or Buyer selects Yes in the Warning message to continue, then the Original Substituted Item field is cleared and moved back to the Item ID field. The Automatic Item Substitution steps repeat to check for substitute items for the Item ID and the new supplier.
If a requisition or purchase order is pegged to a source transaction and you substitute the item, then the pegged relationship will be broken.
If a requisition line is either partially or fully sourced, then item substitutes will not be considered.
If a purchase order line was previously dispatched or the Item ID is grayed out for any reason, then Item Substitution will not be considered.
When an Item ID is entered in a Requisition line by any of the following methods, the Automatic Item Substitution steps occur for each new line:
Purchasing Kit
Item Search
Catalog
Requester Items
ePro Favorites
Personal Templates
When a requisition is saved and the Requester Items and ePro Favorites are updated, if the Original Substituted Item field is populated, then a user can save this Item, rather than the substitute item, as a Favorite. This capability ensures that an item marked as a Substitute Item Only is not saved as a Requester Item or a Favorite and then selected in a subsequent requisition.
When an Item ID is entered in a Purchase Order line by any of the following methods, the Automatic Item Substitution steps occur for each new line:
Purchasing Kit
Item Search
Catalog
When using the Copy From feature to copy a requisition into a new requisition or a purchase order into a new purchase order, the Original Substituted Item field for each transaction line is cleared and the value is moved back to the Item ID field. The Automatic Item Substitution steps repeat to check for current substitute items.
When a requisition is copied to a purchase order, if the Original Substituted Item value is populated in the Requisition line, then a user can perform the Automatic Item Substitution steps to check for substitute items of the Original Substituted Item (not Item ID), as the current substitute item may no longer be valid or a more appropriate substitute item may be available for the Original Substituted Item. If the Original Substituted Item field is not populated, users can perform the Automatic Item Substitution steps to check for substitute items for the Item ID.
When a contract is copied into a purchase order, no Automatic Item Substitution occurs. This is because the Contract line cannot be tied to a purchase order line when the Item IDs do not match. The contract can be updated before it is copied to a purchase order.
Automatic Item Substitution during PO Sourcing will occur based on the following:
If Automatic Item Substitution is selected at the Business Unit level, the Auto Item Substitution field is selected, and the Original Substitute Item field on the staging record is populated, then the Sourcing process will use this Item ID when searching for substitute items. However, if the Original Substituted Item field on the staging record is not populated, then it will use the Item ID value when searching for substitute items.
The Sourcing process uses the Item Substitute Usage Rules to search for substitute items, and it determines the most appropriate substitute item to use for the Original Substituted Item value.
If a Substitute Item was specified in the Requisition and PO Sourcing found a different item substitute (perhaps one with a different date), then PO Sourcing uses the most valid Substitute Item for the purchase order. PO Sourcing will update the Original Substituted Item and Description values if it finds a valid substitute. The system does not check for substitutes of substitutes.
PO Sourcing bypasses Item Substitution if a Procurement Group is associated with the line and the item is the Primary Unit for the Procurement Group or the Allocate Purchasing Group option is enabled in the Business Unit Options table.
PO Sourcing follows the same UOM Conversion and Pricing logic that is used for online requisitions.
Example: Item 10012 is selected in a requisition. An applicable item substitute item does exist for this item. Because the Business Unit level option indicates that a requester’s item can be substituted, the item in the requisition is changed to 10012A. PO Sourcing will determine whether a valid substitute exists for item 10012, the original item in the requisition. If item 10012B is now the most valid item substitute, then this item will be used in the requisition.
Item Substitute Usage Rules
Substitute items are established in the Item Supplier Location Substitution Items page and Item Substitution page. The system evaluates whether to use a substitute item from the Item Supplier Location Substitution Items page first. If none is found, the system evaluates whether a valid substitute item exists at the Item Substitution level. If the Business Unit Security option is Edit Required Must Use Item ID or Edit Required When Use Item ID , then you must establish an item supplier relationship for the substitute item.
A valid substitute item will be selected from the Item Supplier Location Substitution Item level if the Use for Procurement value is Automatic or Automatic and Manual If the date of the transaction is within the Begin Date and End Date of the substitute item, then the rows with the highest priority will be considered first. If the Purchasing Attribute Option - Accept Any UOM is turned off, then an item substitution UOM must be set up as a valid Item Supplier UOM.
A valid substitute item will be selected from the Item Substitution level if none has been found from the Item Supplier Location Substitution Item level. If the Use for Procurement value is Automatic or Automatic and Manual and the date of the transaction is within the Begin Date and End Date of the substitute item, then the rows with the highest priority will be considered first. If the Purchasing Attribute Option - Accept Any UOM is turned off, then an item substitution UOM must be set up as a valid Item Supplier UOM.
Item Substitution UOM Conversion Logic
If the Original Item on the transaction is in the Standard UOM, then the Substitute Item Conversion Rate between the two Items defined on the Substitute Item setup pages is used to determine the unit of measure (UOM) conversion. If the Original Item on the transaction is not in the Standard UOM, then the conversion between the Original Item Standard UOM and the Transaction UOM is determined first, followed by the Substitute Item Conversion between the two Items defined in the Substitute Item setup pages. While performing the Item Substitute UOM Conversion, if the Quantity Precision associated with the resulting Item Supplier UOM record is available and if Quantity Precision is the value Whole Number, then the Quantity is rounded according to the Rounding Rule.
After the UOM Conversion has occurred on the transaction line, Pricing is determined using the available Item Supplier UOM or the Standard UOM Price multiplied by the Item UOM conversion rate.
A breakdown of the UOM Conversion and Pricing logic, along with examples, follows:
Step 1: Convert Transaction UOM of the Original Item to Standard UOM of the Original Item.
This step is applicable only if the Transaction UOM is not the Standard UOM for the Original Item.
Example:
The Transaction UOM is BOX, and the Standard UOM is EA. One BOX contains 4 EA. The Transaction Qty is 10 BOX. The converted Qty and UOM is 40 EA.
Transaction Qty |
Transaction UOM |
Multiplied By |
Conversion Rate Between Standard UOM and Transaction UOM |
Equals |
Converted Qty |
Converted UOM |
---|---|---|---|---|---|---|
10 |
BOX |
* |
4 |
= |
40 |
EA |
Step 2: Convert Original Item Standard UOM to Substitute Item UOM.
Example:
Original Item Standard UOM is EA. Substitute Item UOM is CS. One CS contains 16 EA, so the UOM Conversion between EA and CS is 0.0625. The order Qty of the Substitute Item is 2.5 CS.
Converted Qty |
Converted UOM |
Multiplied By |
Conversion Rate Between Item Std UOM and Sub Item UOM |
Equals |
Order Qty |
Order UOM |
---|---|---|---|---|---|---|
40 |
EA |
* |
.0625 |
= |
2.5 |
CS |
Note: If Quantity Precision is defined as Whole Number on the Supplier’s UOM and Pricing page, then the Qty of 2.5 is rounded according to the Rounding Rule.
Step 3: Find the Price for the Substitute Item UOM.
The Price is obtained from the Supplier’s UOM and Pricing in the Purchasing Attributes if the UOM is defined on this page. If it is not, then the Price is derived from the Substitute Item Standard UOM Price.
Example:
The Substitute Item UOM of CS is not defined in the Supplier’s UOM and Pricing in the Purchasing Attributes. The Substitute Item Standard UOM of EA has a Price of 10 USD. The Conversion Rate between the Standard UOM of EA and the Ordering UOM of CS is 16. The Price for the Substitute Item UOM is calculated as 160 USD per CS.
UOM Defined in Supplier’s UOM & Pricing Page |
Substitute Item Standard UOM Price |
Multiplied By |
Conversion Rate Between Standard UOM and Order UOM |
Equals |
Order Price |
---|---|---|---|---|---|
N |
10 USD |
* |
16 |
= |
160 USD |
To allow Item Substitution in Procurement, you must enable Item Substitution at the business unit level in order to activate the item substitution functionality. You can then determine the item substitution options that work best for your organization or company. This section discusses how to:
Set up item substitution at the Purchasing business unit level.
Define item substitution priorities at the supplier level.
Define item substitution priorities at the item level.
Designate items for substitution only.
Override auto item substitution.
Setting Up Item Substitution at the Purchasing Business Unit Level
Use the Business Unit Options page to set up Item Substitution for a Purchasing Business Unit.
Navigation:
This example illustrates the fields and controls on the Purchasing — Business Unit Options page. The fields and controls that appear in this page are discussed following the examples.
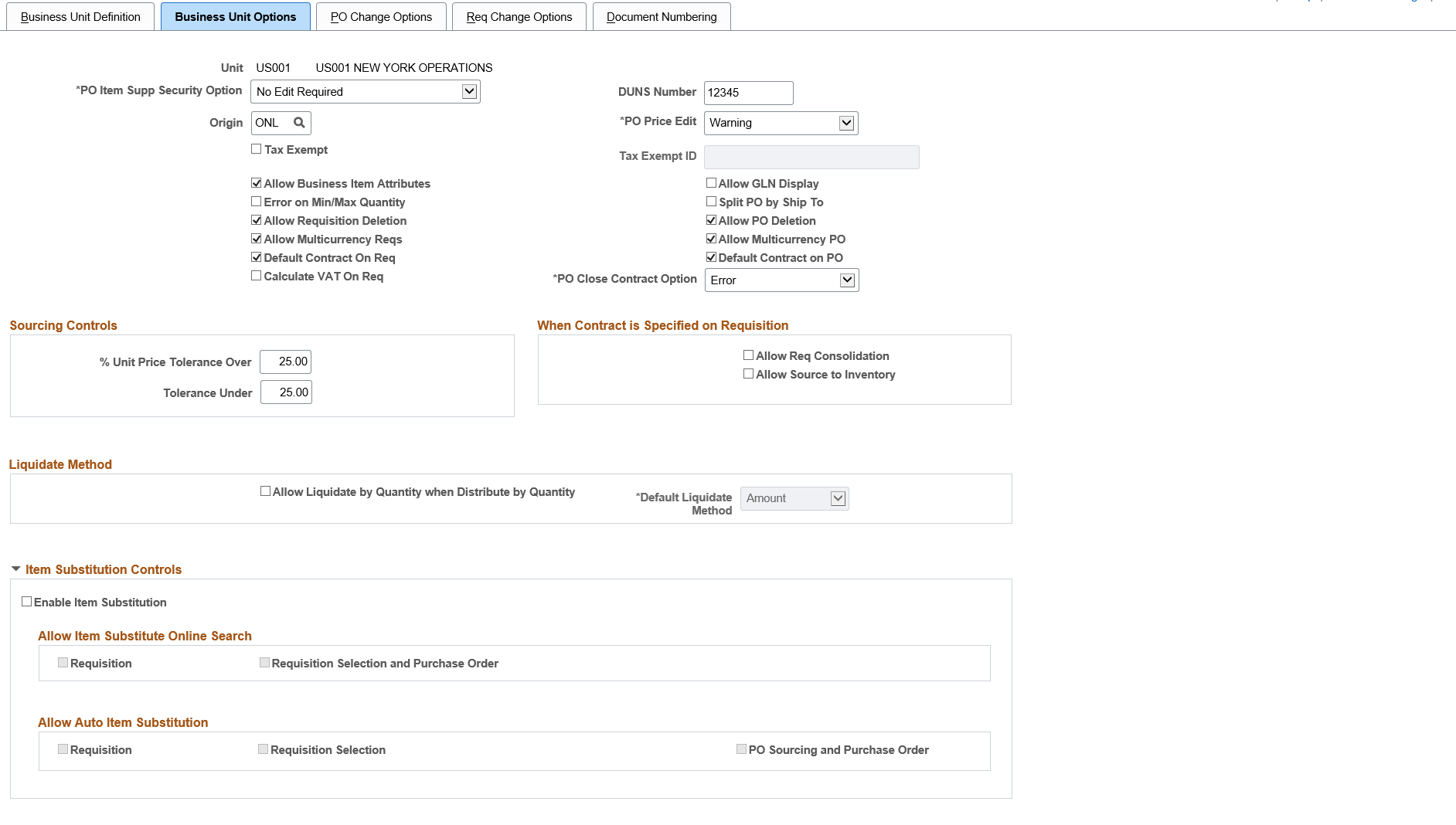
This example illustrates the fields and controls on the Purchasing — Business Unit Options page (2 of 2). The fields and controls that appear on this page are discussed following the examples.
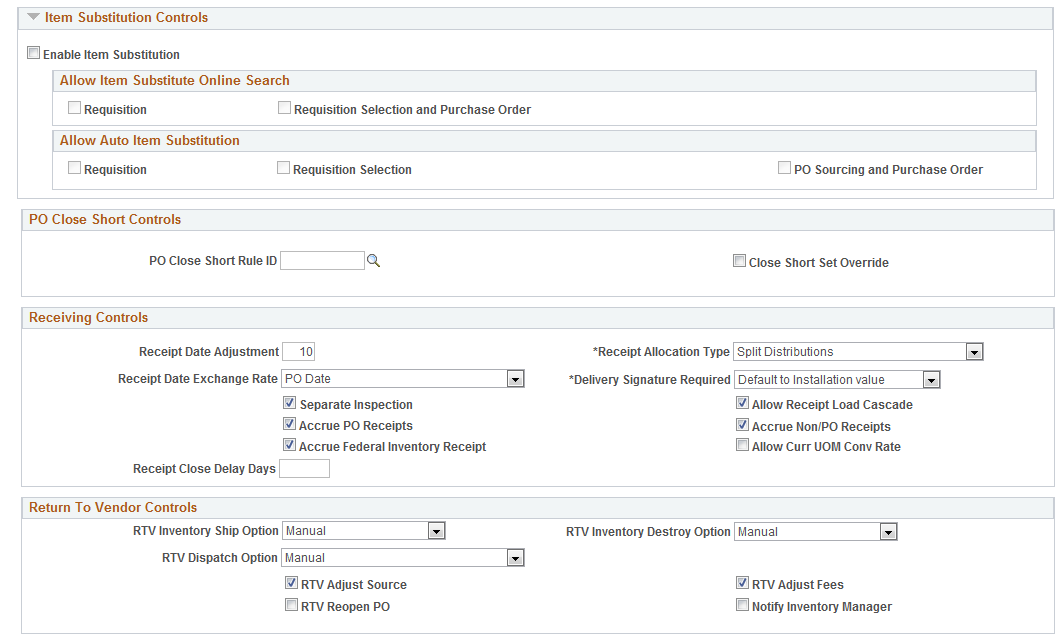
The Business Unit level option controls whether Item Substitution is turned on for the Purchasing business unit. When you select the Enable Item Substitution check box at the Business Unit Options level, the Allow Manual Item Substitution and Allow Auto Item Substitution sections will become available for selection.
If you select check box, all Item Substitute fields will be enabled on the Requisition, the Requisition Selection/Requisition Expediter, the Sourcing Workbench, the purchase order, the receipt, and other applicable components, as needed.
The Requisition check box under the Allow Item Substitution section allows you to enable manual item substitution on the Requisition (core and ePro). The Requisition Selection and check box allows you to enable manual item substitution during Requisition Selection and on the Purchase Order.
The Requisition check box under the Allow Auto Item Substitution section allows you to enable manual automatic item substitution on the Requisition (core and ePro). The Requisition Selection and PO Sourcing and Purchase Order check boxes allow you to enable manual item substitution during Requisition Selection, PO Sourcing, and on the Purchase Order.
Note: While setting up the item substitution controls, you must ensure that you have selected at least one check box in the Allow Item Substitute Online Search and Allow Auto Item Substitution sections.
Defining Item Substitution Priorities at the Supplier Level
Item substitutes defined at the Item Supplier Location level will apply only to a specific supplier. However, if the Purchase Order Item Supplier Security option for the transaction’s business unit is Edit Required Must Use Item ID or Edit Required When Use Item ID, then the substitute items without an item-supplier relationship will not be available for manual item substitution selection and they will not be provided by default.
SeeDefining Purchasing Item CategoriesSelecting Suppliers Based on Item Ship To and Item Supplier Locations
Defining Item Substitution Priorities at the Item level
Item substitutes defined at the Item level will apply to all suppliers.
Designating Items for Substitution Only
You can filter substitute items during item searches in Procurement transactions if you designate the item for substitutions only. In this case, the substitute item will not be available in any Item ID prompt fields throughout the Procurement system. Instead, the Item ID is considered a substitute item for exclusive use as part of the Manual and Automatic Item Substitution process within the Procurement process.
Overriding Auto Item Substitution
The Override Auto Item Substitute field on the Requester Setup page enables you to deselect the Auto Item Substitution check box on a Requisition Line when you want to retain the current Item ID and do not want it automatically substituted during PO sourcing. Additionally, you will be able to reject a Substitute Item found by Auto Item Substitution in the online Requisition.
If you select the Override Auto Item Substitute check box on the Requestor Setup page, the Auto Item Substitute check box in the requisition line will be ungrayed and it will be selected. You can also deselect this check box if you want to prevent Automatic Item Substitution from occurring for a Requisition line during the Sourcing process.
Selecting this check box also means that if Auto Item Substitution occurs for a Requisition line and a Substitute Item is found, then the Requester can answer No to prevent the Sub Item from overriding the requested item.
If you do not select the check box, then the Auto Item Substitution check box on the Requisition line will be grayed out and selected, and the Requester cannot deselect it. (The Buyer will still have the option to deselect this flag in Requisition Selection.)