MICROS Retail OSCAR POS System "Fast Food"
From
Version 1.6 of the MICROS Retail OSCAR POS application on, a special POS system can be
configured for the section "Fast-Food".
The
following program description deals with:
The
Fast Food System supports the special functions necessary for this POS system.
These
special functions include the following POS and process units:
- 1st and 2nd
drive-in terminals
In a fast food system, generally
two POS terminal are configured as drive-in terminals. Drive-in terminal 1
is the POS terminal where the customers drive up with their car and where
their orders are received. The cashier books the desired items at drive-in
terminal 1 and the customer pays. The orders will be sent to the
corresponding Production
area, the Preparation Place, the Wrapping Counter and to drive-in terminal 2.
At drive-in terminal 2, the second terminal, the customers receive the
items paid for at terminal 1 after the order has been compiled and
confirmed at one of the assigned preparation places. At this POS terminal,
there is also the possibility of processing repeat orders.
For drive-in counters 1 and 2, a special POS terminal of the Type Fast Food and a special Process Unit must be created (with the Program POS Term.FF).
- Preparation Place
At the preparation place, the
orders which have been booked at the Drive-in Terminal 1 are compiled. A maximum of three preparation places can be assigned to one
drive-in terminal. Which of the assigned preparation places is to be
active can be decided by the operator and from the administration
terminal. For each preparation place, a Process
Unit must be created in the system (with the program PrepSrv).
An order that has been compiled at one of the preparation places and
confirmed by an operator will be characterized as processed at drive-in
terminal 2. There, the customer order will be checked against the ordered
items and handed out. Repeat orders can be dealt with at drive-in
terminal. The next transaction can only be handled on after the
transaction has been confirmed at the preparation place.
- Production Area
Production areas serve the kitchen
staff etc. as hints at the still open productions.
In the production area, the ordered items are sent from one of the Drive-in Terminals and displayed on the
screen. After working on the production item, the operator has to confirm
the item as produced so that it can be deleted from the screen.
For the production area, a Process Unit must
be created in the system (with the program PrepSrv).
- Wrapping Counter
The wrapping
counter displays all orders on the screen. This wrapping counter allows
all orders which have been worked on at one of the Drive-in Terminals to be chekced. The
quantity of the stored orders (receipts) is limited. <Scroll> keys allow the user to scroll
up and down. The receipts displayed on the screen can be characterized as
“done” by the operator.
For the wrapping counter, a Process Unit must
be created in the system (with the program PrepSrv).
The
following figure shows a possible configuration of an "MICROS Retail OSCAR POS Fast
Food" system.
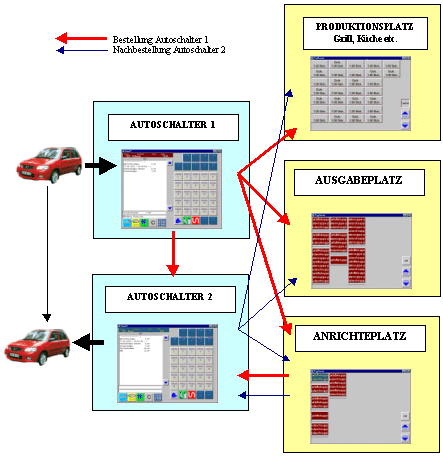
According
to the example displayed in the figure above, a fast food system is configured
as follows:
- Configure a Process Unit and
assign it to a System Unit.
- Enter the name POS
Term. FF in the field Program name.
- Activate the options Graphic and has
Database.
- Configure a POS Terminal
and assign it to the Process Unit for drive-in
counter (POS Term.FF).
- Select the type Fast
Food Layout in the field Touch
layout.
- In the update program Terminals,
call up the update mask via the button Add.Data in order to determine the
preparation places, production areas and wrapping counters to be assigned
to this terminal.
1st to 3rd
preparation place = Select the number of the process unit
that is to be assigned as a Preparation place to
this terminal.
1st to 3rd
prep. active = Activate the option Prep. active for the assigned
preparation places.
Wrapping Counter =
Select the number of the process unit that is to be assigned as a Wrapping Counter to this terminal.
Drive-in terminal 2 =
Select the number of the process unit that is to be assigned as drive-in
terminal 2 to this terminal.
Prep. Print Unit =
Select the number of the process unit to which a printer for the
preparation receipts is connected.
Prep. Print
deviceno. = Select
the number of the printer that is to print the preparation receipts.
Foreground Color = Select the number of the color to determine the
foreground color for the terminal screen of drive-in terminal and for the
buttons of the assigned preparation places and wrapping counters.
Background Color =
Select the number of the color to determine the background color for the
terminal screen of drive-in terminal and for the buttons of the assigned
preparation places and wrapping counters.
Production Table =
Select the number of the Production Table.
The production table contains the production areas and the production
types of a branch. In the update program Item -> Devices, the number of the
production type which refers to the production area in which the items are
to be displayed on the screen should be determined.
- Configure a Terminal Type
and assign it to the terminal for drive-in terminals 1 and 2.
- Select the type Standard
in the field Fast Food Type
if this terminal type is a fast food terminal.
- Select the mode Itemizing
receipt in the field Receipt
Mode. The terminal can only operate in receipt mode the fast
food business.
- In the update program Terminal Type, call up the
update mask via the button Add.Data and activate the option Itemising Terminal.
- Assign the desired payment, finance, transaction,
and price change parameters to this terminal type.
- Configure a Process Unit
and assign it to a System Unit.
- Enter the name PrepSrv
in the field Program name.
- Activate the option Graphic for this process unit.
- Configure a Process Unit
and assign it to a System Unit.
- Enter the name PrepSrv
in the field Program name.
- Activate the option Graphic for this process unit.
- Configure a Process Unit
and assign it to a System Unit.
- Enter the name PrepSrv
in the field Program name.
- Activate the option Graphic for this process unit.
- Go to Terminal ->
Add.Data-> Production table to create a new production table.
- The values in the fields Company and
Branch are already predefined. Enter a free number in the field Production Table and a name for
the table in the field Descriptor.
- Change to the update program Production Area via the appropriate button.
You can also call up this program from the update program Branch.
- The values in the fields Company, Branch and
Installation are already predefined. Enter the number of the production
area and a name. Assign the process unit you configured for the Production Area (ProdSrv) to this production area.
- Assign further production areas to this
production table if you would like to set up more than one production
area.
- Activate the option Active for all production areas to receive output in the
production area.
- The production type number must be entered in the
update program Item -> Devices in the field Production type to make sure
that the items can be displayed in the assigned production area.
- The production type number must be entered in the
update program Item -> Devices in the field Production type to make sure
that the items can be put out on the screen of the assigned production
area.
- Activate the option Preparation area in the update
program Item -> Devices to make sure that
the items can be displayed in the assigned preparation places.
MICROS Retail Deutschland GmbH
Salzufer 8
D-10587 Berlin
Germany