Manufacturing Work In Process (WIP)
Manufacturers often use work orders to assemble the materials needed to produce an item. Manufacturing Work In Process lets manufactures track work orders through the production process, from gathering materials, through shop floor assembly, to stocking finished goods.
Assembly items built using Manufacturing Work In Process (WIP) are divided into the following processes:
-
Issue Work Order: Move raw materials to an assembly area (work center)
-
Complete Work Order: Assemble raw materials and stock finished goods
-
Close Work Order: Reconcile variances
This separation lets you enter work order transactions that define the completion of each step, from material consumption to assembly and completion.
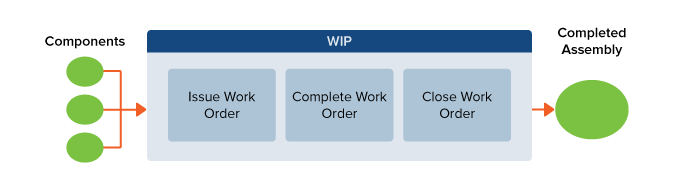
To know where materials are in the manufacturing process, use WIP to track your materials and record the number of:
-
Component materials in stock
-
Component materials consumed against a work order
-
Finished assemblies in stock
-
Assemblies you can build
Use WIP to track assembly component to identify the materials not used in the process.
Tracking goods and materials enables you to control your inventory and raw materials. Controlling stock can help you avoid the following:
-
Tying up funds in stock or on the production floor
-
Unanticipated raw material stock-outs
NetSuite supports production processes with a long lead time and can track item assemblies as a work in process.
To learn when materials are issued or removed from inventory, see Entering Work Order Issues.
To use WIP, enable the feature and set up item records, see Enabling the WIP Feature.
On transactions using WIP, you must identify a WIP location for line items. The WIP line location must match on all work order issue, work order completion, and work order close transactions.
Related Topics
- Setting Up Items as WIP Assemblies
- Setting Default WIP Accounts
- Setting Up Items as WIP Assemblies
- Using WIP on Work Orders
- Associating Components with Operations
- Entering a Completion for an Individual Work Order
- WIP and Inventory Costing
- Assembly Items
- Assembly Work Orders
- WIP and Inventory Costing
- Manufacturing Overview
- Advanced Bill of Materials
- Bill of Materials Member Control for Assembly Items
- Manufacturing Routing
- Outsourced Manufacturing
- Manufacturing Preferences Overview
- SuiteAnalytics Manufacturing Workbook
- Advanced Manufacturing
- Manufacturing Mobile
- Engineering Change Order
- Manufacturing