45 Inventory Counting
All merchandise items, whether entering the store through receiving and return functions or leaving the store through sales and shipping functions, are tracked using an inventory process. This inventory tracking occurs at the item level, resulting in an audit trail from the time the item enters the store and continuing until the item leaves the store.
The inventory process allows you to enter item inventory counts and make adjustments to the inventory quantity of items. The Xstore Physical Inventory function allows you to accurately and efficiently count on-hand merchandise. After a count takes place, the local inventory is updated, and accurate counts are posted to the home office. Physical Inventory can be conducted through Xstore POS.
-
Real-time inventory is adjusted automatically during normal POS activity. This normal activity includes-but is not limited to-sales, returns, shipping, and receiving of physical, saleable store merchandise. Real-time inventory does not require any additional interaction by the user during normal transaction processing.
-
The physical inventory method uses counting as the means by which store personnel manually count merchandise items in the retail store. A store associate using a mobile device to scan the count, and then adds the count values into the system where they are stored. The system applies the adjustments to each item's inventory.
Xstore provides three different types of inventory counts to meet your specific requirements:
-
Physical Count: Counting all in-stock items.
To perform a physical count, a layout must be set up for the store using the Store Layout Maintenance functionality in Xstore Desktop or Mobile Tablet. The layout cannot be created on the Handheld. Multiple count sheets are created to allow several associates to count different sections of the store. Count sheets are not printed as scanning is the preferred method.
Additional cycles of counting can be performed if there are variances from the expected values and from previous counts. See Physical Count Process for more information.
-
Cycle Count: Counting a subset of the entire stock.
Only one count sheet is used for a Cycle Count, although additional cycles of counting can be performed if there are variances from the expected values and from previous counts. See Cycle Count Process for more information.
-
Supply Count: Counting internally used supplies, rather than saleable items.
This count type is like a Cycle Count; however, it automatically populates the count sheet with all supply items defined for your store. See Supply Count Process for more information.
About this Chapter
The following processes described in this section are used to create and find the count documents, create count sheets, and count the on-hand merchandise.
Inventory Counting Steps - Overview
The following steps describe the generalized process that conforms to the system enforced steps for conducting inventory counts. Submitting and initiating counts can be done while the store is open (can be configured on or off). However, a warning message is displayed if you are performing an inventory count while the store is open. Xstore will automatically adjust for inventory changes during the count process. Sales and returns are calculated into the counts. It is recommended that all inventory movements are suspended while an inventory count is underway if the store is open.
The initial step is to find an existing Inventory Count document, or to create a new document if allowed by your store policy. Once the Inventory Count document is located, perform the following steps:
-
Generate Count Sheets for the Inventory Count document. This step applies to a Physical Count type only. Skip this step for Cycle Count and Supply Count sheets since they are generated automatically for the Inventory Count document.
-
Initiate the count for the selected Inventory Count document BASED ON SECURITY PRIVILEGE. This step is usually performed on the day of the count and takes a snapshot of the current inventory ledger. It is only performed when the store is online. The count must be initiated before the count quantities can be submitted (posted). This step allows your count to be compared to the system-expected quantity. Any variances between your count and the system expected quantity are reported, allowing you to resolve any discrepancies through additional counting cycles.
-
Perform the actual count of the items (scan items). Depending on your store policy, you may be able to perform this step before initiating the count. However, even though you may be able to enter your counts into the system, you cannot submit the count until the initiation step is performed.
-
Submit the count. Your count is compared to the system-expected quantity captured during the initialization process (step 3).
-
Perform a recount if there is a variance between the system-expected quantity and the count quantity:
-
If your system is set up for automatic variance processing, Xstore automatically creates a second count cycle for you, with only the items you must recount. If the second count results in any variances, the system creates another count cycle automatically, and continues to create as many cycles as needed to resolve any discrepancies, up to the maximum number of cycles allowed by your store policy.
-
If your system is set up for manual variance processing, the system will not create additional cycle counts automatically. However, you can mark individual sheets to be moved to the next cycle for recounting until the maximum number of cycles is reached, or the count is completed.
-
-
Complete and post the final counted quantities to update your inventory BASED ON SECURITY PRIVILEGE.
Inventory Count Documents
An Inventory Count document can be created at the home office and downloaded to a store, or a store can create its own Inventory Count documents, if allowed by store policy. An Inventory Count document contains the summary information for the count, specifies the date the count should be started, and identifies the items for the count.
-
If an Inventory Count document exists for the count you want to perform, see Finding an Existing Inventory Count Document below.
-
If an Inventory Count document does not exist for the count you want to perform, see Creating a New Inventory Count Document. This option will only be available if your store policy allows store-created Inventory Count documents.
Figure 45-1 Xstore POS Main Menu
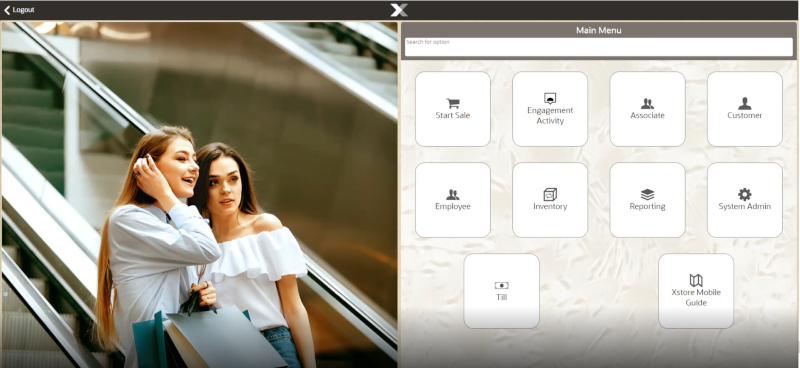
Finding an Existing Inventory Count Document
-
Select the Inventory option from the Main Menu.
Figure 45-2 Handheld Inventory Menu
Figure 45-3 Xstore POS Inventory Menu
-
Select Inventory Count Options from the Inventory menu.
Figure 45-4 Xstore POS Inventory Count Options Menu
-
Select Inventory Count.
-
At the Inventory Count search form, enter search criteria to find the Inventory Count document, then select Process to initiate the search.
Note:
This form is based on security privilege. If the logged in user does not have the search privilege, the search form will not display. Instead, Xstore displays a list of Initiated and Submitted counts.
Figure 45-5 Inventory Count Criteria
Note:
Leave all fields blank and select Process to list all Inventory Count documents.
The Inventory Count search form contains the following fields:
-
Count ID: This is the auto-generated count identifier associated with the Inventory Count document. Type or scan the count identifier in this field.
-
Begin Date: This is the date the count is to be performed.
-
Count Type: Select the type of count from the list: Physical Count, Cycle Count, or Supply Count. See the chapter summary Inventory Counting for more information about these three different types of inventory counts.
-
Status: Select the count document status from the list:
-
New: No action has been taken on this Inventory Count document.
-
Initiated: A snapshot of the database has been taken for this Inventory Count document.
-
Submitted: All count sheet status for this Inventory Count is submitted.
-
Complete: Items on this Inventory Count document have been counted, submitted, and completed.
Note:
If an Inventory Count document matching your search criteria is not found, or you want to create a new inventory count, select the Add New option. See Creating a New Inventory Count Document for a step-by-step procedure describing how to create a new Inventory Count document.
-
-
-
Xstore displays a list of Inventory Count documents based on your search criteria. Scroll up and down the list as required and select the document you want.
Figure 45-6 Inventory Count Document List
-
Count ID: The inventory count identifier.
-
Count Status: The current status of the count: New, Initiated, Submitted, or Complete.
-
Description: The brief description of the Inventory Count.
-
Count Type: The type of count: Physical Count, Cycle Count, or Supply Count.
-
Begin Date: The date the count is scheduled to begin.
Note:
Inventory Count documents created by the Home Office cannot be cancelled or edited.
-
-
Select Process.
-
Xstore displays the count screen for the selected Inventory Count document:
-
If you are performing a Cycle Count, continue with Cycle Count Process for step-by-step instructions.
-
If you are performing a Supply Count, continue with Supply Count Process for step-by-step instructions.
-
If you are performing a Physical Count, continue with Physical Count Process for step-by-step instructions.
-
Creating a New Inventory Count Document
The following steps describe how to create a new Inventory Count document. Any Inventory Count documents you create will be flagged as Store Created for tracking purposes.
Note:
Inventory Counts cannot be created or initiated in offline mode. Creating a new Inventory Count document is based on security privilege.
-
After selecting the Add New option at the Inventory Count Search form (refer to Figure 45-5 and Figure 45-6), Xstore displays the Inventory Count document form. Enter the information in the fields as required to create a new Inventory Count document for the type of count you want to perform and select Process.
Figure 45-7 New Inventory Count
-
Begin Date: Enter the date on which the counting should be started.
-
Count Type: Select the type of count for this Inventory Count document. The following count types are available in Xstore:
-
Cycle Count - Counts a subset of the entire stock. See Cycle Count Type Setup for setup instructions.
-
Supply Count - Counts internally used supplies, rather than saleable items. See Supply Count Type Setup for setup instructions.
-
Physical Count - Counts all in-stock items. See Physical Count Type Setup for setup instructions.
-
-
Description: Desktop, Thin Client, and Tablet only, type a brief description of the Inventory Count. The description does not need to be unique. The Handheld does not have a Description field.
-
Inventory Location: Select an inventory location or leave as Default. This inventory location is associated with the created inventory count just for the duration of the count.
-
Refer to the count types below for the specific information required for each type of count.
Cycle Count Type Setup
Note:
You can create multiple initiated Cycle Count documents. Xstore will not check for overlap of inventory so be sure to create counts for different areas of the store.
...continued from step 1
Figure 45-8 Cycle Count Setup Screen - Xstore POS
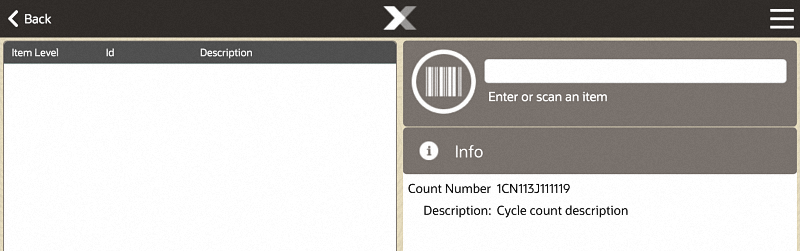
-
Choose one of the following options to add the items to the new Cycle Count document:
Scan or enter the item IDs to be counted on this Inventory Count document.
<OR>
Select the Add Merch Level option from the Context Menu to add all items in a merchandise level.
Figure 45-9 Add Merch Level Context Menu Option - Xstore POS
If you select the Add Merch Level option, you will be prompted to select a merchandise level to be added to the Inventory Count document:
Department, Subdepartment, Class, Subclass.
Figure 45-10 Select Merchandise Level
The actual items associated with each merchandise level are not shown in the list of items to be counted on the Inventory Count document. The merchandise level identifier (CLASS, DEPARTMENT, and so on) is displayed as a place holder and will be expanded to show the items within this merchandise level on the count sheets created in a later step. On Xstore POS, the count sheet is blank until items are scanned.
Figure 45-11 Cycle Count Items - Merch Level and Item Level
-
After adding the items to be counted on this Inventory Count document, select Save & Continue to create the new Cycle Count. Cycle Counts only use a single count sheet for all items.
Figure 45-12 Save & Continue Option - Xstore POS
-
At the confirmation prompt, select Yes to save the Cycle Count items you added.
Figure 45-13 Continue Count Process Prompt
-
The system displays the Cycle Count screen:
Figure 45-14 Cycle Count Screen - Xstore POS
-
Refer to Cycle Count Process to continue with the counting process.
<OR>
-
Select Back at the Cycle Count screen if you are not ready to begin counting currently. The Cycle Count document will be available in the list of existing Inventory Count documents when you are ready to continue with the count process.
-
Supply Count Type Setup
...continued from step 1
Figure 45-15 New Supply Count - Xstore POS
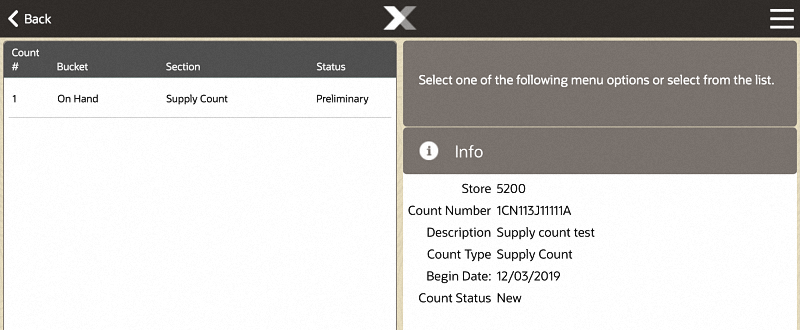
For a Supply Count, all items identified as supplies in your store are automatically added to the count sheet. Supply Counts use a single count sheet for all items. You cannot remove supply items or add any items to this sheet.
Note:
Supply Count items are listed automatically. You do not need to create the list.
Select Back if you are not ready to begin counting at this time. The Supply Count document will be available in the list of existing Inventory Count documents when you are ready to continue with the count process.
Refer to Supply Count Process to continue the counting process.
Physical Count Type Setup
...continued from step 1
-
Select the Generate Count Sheets menu option from the Context Menu to add the items in each section to this new Inventory Count Document.
Figure 45-16 New Physical Count
Note:
For a Physical Count, the Store Layout defined for your store is used to add items to be counted. See Store Layout Maintenance for detailed information about defining sections and items for your store.
The actual items associated with each section are not shown in the list of items to be counted on the Inventory Count document. The section identifier is displayed as a place holder and will be expanded to show the items within this section on the count sheets created in a later step.
Once the count is created, do one of the following:
-
To continue the counting process, refer to Physical Count Process.
-
If you are not ready to begin counting at this time, select Back. The Physical Count document will be available in the list of existing Inventory Count documents when you are ready to continue with the count process.
-
Count Process
The following steps describe the count process. Select a count type:
Cycle Count Process
The initial step in the Cycle Count process is to find an existing Inventory Count document, or to create a new document if allowed by your store policy. See Inventory Count Documents for detailed information about locating an Inventory Count document.
Once the Inventory Count document is located, perform the following steps.
-
Select the Cycle Count document you want to count.
Figure 45-17 Cycle Count - Xstore POS
The Cycle Count screen displays showing the Cycle Count status for both the Inventory Count document and for the count:
The area on the right side of the screen displays the information for the Inventory Count document: Store ID, Count Number, Count Type, Begin Date, and Count Status (New, Initiated, or Complete).
To the left, this area displays information for the count sheet:
-
Count Cycle (Count #): Indicates the number of times the bucket has been counted so far in order to reconcile any count variances and complete the count. The count cycle will always be set to 1 for the first count. If additional counts are needed to resolve a discrepancy, this number will increment for each recount.
-
Bucket: The inventory bucket identifier for this count sheet. Inventory buckets are pre-defined for your store. For cycle counts, only the On Hand bucket is counted.
-
Section: Identifies which cycle count we are on. Cycle Count without a number is the first cycle count done. Cycle Count coincides with the Count #.
-
Status: The status of the bucket within the current count and cycle:
-
Preliminary - The beginning status for a new count.
-
Printed - Indicates the count sheet has been printed.
-
Saved - Indicates the count sheet has been saved.
-
Complete - Indicates the count sheet has been completed.
-
-
-
To begin the counting process, you have the following options:
-
OPTIONAL If you want to see the items on the count sheet, select the count sheet. After the first cycle count the items to be counted are displayed. During the first cycle count, the count sheet is blank.
Press Back to return to the previous screen and print the count sheet.
-
Select the Print Count Sheet menu option to print the count sheet on the report printer. The count sheet status is updated to Printed and a count sheet is created in readiness to enter the number of items found although, it is not required to print count sheets when using Xstore POS.
Figure 45-18 Printed Count Sheet
On the Xstore POS, items to be counted are scanned and not manually added.
Figure 45-19 Context Menu Options
Note:
The Print Multiple Sheets option is usually used for Physical Counts of the entire store when more than one count sheet exists, not for Cycle Counts.
To print multiple count sheets, select the Print Multiple Sheets menu option. Select the count sheets to be printed. When prompted, select Yes to confirm. The count sheet status will be updated from Preliminary to Printed.
Note:
The store no longer needs to be closed to initiate a count and submit your counts. However, a warning message is displayed if you are performing an inventory count while the store is open.
Counts are usually initiated on the day the inventory count takes place.
If enforced by your store policy, you cannot enter your counts until the count has been initiated.
Note:
About the count menu options:
-
Initiate Count BASED ON SECURITY PRIVILEGE - This process allows your counts to be compared to the snapshot system- expected quantity. Depending on your store policy, you may be required to initiate the count before entering any counts into the system. Or, if your store policy allows, you may be able to enter your counts before initiating the count.
-
Cancel Count BASED ON SECURITY PRIVILEGE - This option allows you to cancel your count up until it is completed. Only store-created Inventory Counts can be cancelled. When prompted, select Yes to cancel the count.
Figure 45-20 Confirm Cancel Count
-
Complete Count BASED ON SECURITY PRIVILEGE - This option marks the count sheet as complete. The Complete Count menu option will only be enabled after the count cycles for the inventory count are complete.
-
Back - This option will exit the current Count document, and take you back to the Inventory Count search form (Figure 45-5).
-
-
-
Select Initiate Count to take a snapshot of current inventory. If the store is open, a warning message is displayed. Select Yes to continue or Noto exit the count.
This initiation process takes a snapshot of your current inventory ledger to be used to calculate variances between the expected (snapshot) quantity and the quantity you entered in to the system.
Counts must be initiated before they can be submitted.
-
Scan the items.
-
Open the Context menu and select Save Count Sheet.
-
Select Yes to confirm.
You are returned to the Cycle Count main page. The count sheet status changes to Saved.
-
Select the count sheet just saved to bring up two menu options:
-
Count: Returns to the count sheet to scan more items.
-
Submit: Submits the count sheet.
Figure 45-21 Cycle Count - Count or Submit Menu
-
-
Select Submit. The count sheet status changes to Submitted.
The system compares the count quantity you entered with the expected quantity based on the snapshot taken of the inventory ledger:
-
If the counted quantity and the expected quantity match, the inventory bucket for the item is marked as settled - no variance, and the count is complete. Skip to step 13.
-
If the counted quantity and the expected quantity do not match, the inventory bucket for the item is marked as having a variance.
-
If your system is set up for Automatic Variance Processing, any variances will automatically result in a new count cycle: count cycle 2. See Automatic Variance Processing for detailed information about this type of variance processing.
-
If your system is set up for Manual Variance Processing, you can choose whether to perform a recount. See Manual Variance Processing for detailed information about this type of variance processing.
-
-
-
If you must recount any items, perform the same steps you used for count cycle 1:
Note:
Since subsequent count cycles are always compared to the initial snapshot taken for the first count cycle, you cannot initiate the count again.
Select the count sheet on tablet (it's displayed as a row). Only the items with variances will be listed for a recount.
-
OPTIONAL You can select the View Variance Reports menu option to create a variance report showing the count discrepancies.
Figure 45-22 View Variance Reports - Xstore POS
If prompted, select a Variance Report from the list.
-
The system creates and displays the report. See Variance Report for more information about these reports.
Figure 45-23 Inventory Count Variance Report
-
After the final count cycle sheet is submitted, the system displays a prompt indicating you have completed all count cycles:
Figure 45-24 Complete Count
Select one of the following options to continue the counting process:
-
Select Continue to return to the Inventory Count screen. From the Inventory Count screen, you can:
-
View/Print Variance Reports from all count cycles that had variances.
Note:
No Variance Report will be available for a count cycle that had no variances since all variance values would be 0.
-
Save the submitted count cycles and post inventory counts at another time.
-
Print count sheets (if available).
-
Cancel the count BASED ON SECURITY PRIVILEGE.
-
Complete the count to post inventory counts and adjust the inventory counts in the system BASED ON SECURITY PRIVILEGE.
<OR>
-
-
Select Complete Count to post inventory counts and adjust the inventory counts in the system BASED ON SECURITY PRIVILEGE.
-
-
After completing the count sheets, the system marks the Inventory Count document as Complete and inventory quantity will be adjusted accordingly.
Supply Count Process
A Supply Count is a count of items not sold in your store, but are required for normal store operations, such as rolls of receipt paper for cash registers or printer paper for report printers. The Supply Count process is like the Cycle Count process; however, the count sheets are automatically populated with only the items identified as supplies in your store. Usually Supply Counts are not downloaded from the home office, and you cannot add items to the count sheets. The initial step in the Supply Count process is to find an existing Inventory Count document, or to create a new document.
To locate a Supply Count document, refer to Finding an Existing Inventory Count Document.
To create a new supply count document see Creating a New Inventory Count Document.
-
Select the Supply Count document you want to count.
-
The Supply Count screen displays showing the count status for both the Inventory Count document and for the count sheet:
Figure 45-25 Supply Count Screen - Count Cycle 1
The Info box on the right-hand side of screen displays the information for the Inventory Count document: Store, Count Number, Description, Count Type, Begin Date, and Count Status.
The area to the left displays’ information for the count sheet:
-
Count Cycle (Count#): Indicates the number of times the bucket has been counted in order to reconcile any count variances and complete the count. The count cycle will always be set to 1 for the first count. If additional counts are needed to resolve a discrepancy, this number will increment for each recount.
-
Bucket: The inventory bucket identifier for this count sheet. Inventory buckets are pre-defined for your store. For supply counts, only the On Hand bucket is counted.
-
Section: Identifies which cycle count we are on. Supply Count without a number is the first cycle count done. Supply Count coincides with the Count #.
-
Status: The status of the bucket within the current count and cycle:
-
Preliminary: The beginning status for a new count.
-
Printed: Indicates the count sheet has been printed.
-
Saved: Indicates the count sheet has been saved.
-
Complete: Indicates the count sheet has been completed.
-
-
-
Select the top row to display the count sheet.
Note:
If enforced by your store policy, you may not be able to enter your counts until the count has been initiated. Counts are usually initiated on the day of the count.
If the store is open, a warning message is displayed. Select Yes to continue or No to exit the count.
Note:
About the count menu options:
-
Initiate Count BASED ON SECURITY PRIVILEGE - This process allows your counts to be compared to the snapshot system- expected quantity. Depending on your store policy, you may be required to initiate the count before entering any counts into the system. Or, if your store policy allows, you may be able to enter your counts before initiating the count.
-
Cancel Count BASED ON SECURITY PRIVILEGE - This option allows you to cancel your count up until it is completed. Only store- created Inventory Counts can be cancelled. When prompted, select Yes to cancel the count.
Figure 45-26 Confirm Cancel Count
-
Complete Count BASED ON SECURITY PRIVILEGE - This option marks the count sheet as complete. The Complete Count menu option will only be enabled after the count cycles for the inventory count are complete.
-
Back - This option will exit the current Count document and take you back to the Inventory Count search form (Figure 45-5).
-
-
Select Initiate Count to take a snapshot of current supply inventory. If the store is open, a warning message is displayed. Select Yes to continue and the Count Status changes to Initiated, or No to exit the count.
-
Scan the items. As you scan the supply items they display. You cannot enter a quantity; all items must be scanned to be counted.
Note:
The count sheet will be blank for the first cycle count. The next cycle counts display the items that need recounting, that is, the items with quantity discrepancies.
Figure 45-27 After Scanning Items
-
Select Save Count Sheet.
-
Select Yes to confirm. The count sheet status changes to Saved.
Figure 45-28 Supply Count Sheet - Saved Status
-
Select the Supply Count row. The following menu list displays:
Figure 45-29 Supply Count Menu Options
-
Count: Returns to the count sheet to scan more items.
-
Submit: Submits the count sheet.
-
-
Select Submit Count Sheet.
-
Continue with step 5 through step 9 to submit and complete your supply count following the same process used for cycle counts.
The system compares the count quantity you entered with the expected quantity based on the snapshot taken of the inventory ledger for supply items.
Figure 45-30 New Inventory Count Cycle Prompt
-
After Submitting the last cycle count (configurable number of counts), the following prompt is displayed:
Figure 45-31 Inventory Count Cycles Complete
-
Select Complete Count.
Figure 45-32 Inventory Count Complete
-
Select OK.
Figure 45-33 Supply Count Complete
The count screen shows the following status information:
Inventory Document Count Status: Complete
Count Status: Complete and the number of count cycles required to complete the count. Each count sheet status for all cycles is set to Submitted.
Physical Count Process
Before you can perform a Physical Count for all items in your store, you must set up a store layout plan to divide your store into manageable sections. Each section will have its own count sheet showing the items in that section. These count sheets can then be distributed to the associates responsible for counting each section. Refer to Store Layout Maintenance for more information about setting up your store layout.
The initial step in the Physical Count process is to find an existing Inventory Count document, or to create a new document if allowed by your store policy.
See Inventory Count Documents for detailed information about locating an Inventory Count document. See Creating a New Inventory Count Document for detailed information about creating an Inventory Count document.
Once the Inventory Count document is located, perform the following steps:
-
Select the Physical Count document you want to count and select Process. The system displays the Physical Count screen.
-
Select the Generate Count Sheets menu option on the Physical Count screen to create the count sheets based on your store layout. This screen shows the following information for the new Physical Count:
Figure 45-34 Physical Count Screen
The Info box on the right-hand side of the screen displays the information for the Inventory Count document: Count Type, Count ID, Inventory Location, Status, Begin Date, and Description.
Underneath displays information for the count sheet:
-
Bucket: The inventory bucket identifier for this count sheet. Inventory buckets are pre-defined for your store.
-
Count Cycle: Indicates the number of times the bucket has been counted in order to reconcile any count variances and complete the count. The count cycle will always be set to 1 for the first count. If additional counts are needed to resolve a discrepancy, this number will increment for each recount.
-
Status: The status of the bucket within the current count and cycle:
-
Preliminary - The beginning status for a new count.
-
Printed - Indicates the count sheet has been printed.
-
Saved - Indicates the count sheet has been saved.
-
Complete - Indicates the count sheet has been completed.
-
On the left, the screen lists each count sheet based on your store layout:
-
Count Sheet #: The sequential number associated with each count sheet for this Physical Count.
-
Bucket: The inventory bucket associated with the count sheet.
-
Section: The store area to be counted as defined in your store layout.
-
Status: The status for each count sheet.
-
-
Select a row to display that counts' count sheet. Scan or enter items. When items have been added, save the count sheet.
Figure 45-35 Count Context Menu Options
If required, use the Context Menu to print the count sheets:
-
To print one count sheet at a time, highlight the count sheet and select the Print Count Sheet menu option. The count sheet is printed, and the status will be updated from Preliminary to Printed.
Figure 45-36 Count Sheet - Status Printed
-
To print multiple count sheets, select the Print Multiple Sheets menu option. The system prompts you to select the count sheets to be printed. Select each sheet individually or choose the Select All menu option to print all sheets. When prompted, select Yes to confirm the count sheets to be printed. The count sheet status will be updated from Preliminary to Printed.
Figure 45-37 Printed Count Sheet Example
Use the printed count sheets to record the item counts. Blank lines are provided so that you can write in any items you find in the section that were not included on the printed list. When you have finished counting the items, return to the Inventory module to enter your counts into the system.
Note:
If allowed by your store policy, you can enter your counts before initiating the count.
If enforced by your store policy, you cannot enter your counts until the count has been initiated. See step 4 below.
-
-
Select Initiate Count to take a snapshot of current inventory.
If the store is open, a warning message is displayed. Select Yes to continue and the Count Status changes to Initiated, or No to exit the count.
Figure 45-38 Physical Count Initiated - Xstore POS
Note:
About the count menu options:
Initiate Count BASED ON SECURITY PRIVILEGE - This process allows your counts to be compared to the snapshot system-expected quantity. Depending on your store policy, you may be required to initiate the count before entering any counts into the system. Or, if your store policy allows, you may be able to enter your counts before initiating the count.
Cancel Count BASED ON SECURITY PRIVILEGE - This option allows you to cancel your count up until it is completed. Only store-created Inventory Counts can be cancelled. When prompted, select Yes to cancel the count.
Complete Count BASED ON SECURITY PRIVILEGE - This option marks the count sheet as complete. The Complete Count menu option will only be enable after the count cycles for the inventory count are complete.
Back - This option will exit the current Count document and take you back to the Inventory Count search form (Figure 45-5).
-
Now count the items listed on the count sheets...
When you have finished counting the inventory items, return to the Inventory module to enter your counts into the system. Refer to Physical Count Process if you need instructions for locating the Inventory Count document you are working on.
-
At the Physical Count screen, select a count sheet from the list and press Enter. Use the Count details that display to identify the area to begin your count. If required, print the count sheets.
Start scanning the items in the section of the store. No items display on the count sheet until the start of scanning and then the scanned items are displayed on the tablet.
Figure 45-39 After Scanning Item
Note:
Items cannot be added that do not belong to the area so there is no Add Count Item option.
-
After scanning all items on the count sheet, select Save Count Sheet from the Context Menu. The count sheet status will change from Preliminary to Saved. Repeat steps 5-7 for all count sheets.
Figure 45-40 Save Count Sheet Option - Xstore POS
Figure 45-41 All Count Sheets Saved Status
-
Submit the counts.
In this step, your count is compared to the system expected quantity captured during the initiation process. Any variances between your count and the system- expected quantity will be reported, allowing you to resolve any discrepancies through additional counting cycles.
-
To submit a single count sheet, select that count sheet and select Submit. The count sheet status changes to Submitted.
-
To submit multiple count sheets at one time, select the Submit Multiple Sheets menu option. The system prompts you to select the count sheets to be submitted. Select each sheet individually or choose the Select All menu option to submit all sheets. When prompted, select Yes to confirm the count sheets to be submitted.
Figure 45-42 Submit Option
-
-
The next step depends on the type of variance processing used: Automatic or Manual.
-
If the counted quantity and the expected Snapshot quantity match, the inventory bucket for the item is marked as settled – no variance, and the count is complete.
-
If the counted quantity and the expected Snapshot quantity do not match, the inventory bucket for the item is marked as having a variance.
-
If your system is set up for Automatic Variance Processing, any variances will result in a new count cycle: Count Cycle 2. See Automatic Variance Processing for detailed information about this type of variance processing.
-
If your system is set up for Manual Variance Processing, you can choose whether to perform a recount. See Manual Variance Processing for detailed information about this type of variance processing.
-
Note:
In Count Cycle 2 (and higher), all items with variances will be grouped by Bucket. The Sections used for counting in Cycle 1 are not used for Cycle 2 and greater.
For example, if you have sections within the Layaway bucket such as an Earrings Section, a Watch Section, and a Jewelry Section with variances reported in Cycle 1 (1), then in Count Cycle 2 (2), the three Layaway sections (Earrings Section, Watch Section, and Jewelry Section) will be consolidated into a single Layaway bucket and the Section identifier will be ignored. -
-
If you must recount any items, perform the same steps you used for count cycle 1:
Note:
Since subsequent count cycles are always compared to the initial snapshot taken for the first count cycle, you cannot initiate the count again.
-
Select the count sheet. Only the items with variances will be listed for a recount.
-
You cannot add additional items to Count Cycle 2.
-
When the recount is finished and saved, select the Submit Count Sheet menu option. Once again, the system will compare the entered counts with the expected counts.
-
-
You can select the View Variance Reports menu option to create a variance report showing the count discrepancies. When prompted, select a Variance Report from the list and press Enter. The system creates and displays the report.
-
After the final count cycle sheet is submitted, the system displays a prompt indicating you have completed all count cycles.
Figure 45-43 Complete Count - Handheld
Figure 45-44 Complete Count - Xstore POS
-
Select one of the following options to continue the counting process:
-
Select Continue to return to the Inventory Count screen. From the Inventory Count screen, you can:
-
View/Print Variance Reports from all count cycles that had variances.
Note:
No Variance Report will be available for a count cycle that had no variances since all variance values would be 0.
-
Save the submitted count cycles and post inventory counts at another time.
-
Print count sheets.
-
Cancel the count.
-
Complete the count to post inventory counts and adjust the inventory counts in the system.
<OR>
-
-
Select Complete Count to post inventory counts and adjust the inventory counts in the system.
-
-
After completing the count sheets, the system marks the Inventory Count document as Complete and inventory quantity will be adjusted accordingly.
Automatic Variance Processing
In Automatic Variance Processing only items with count variances are moved to the next cycle of counting. This process will continue moving items with count variances to the next count cycle automatically until the count for the item matches the value expected by the system (from the snapshot), or the quantity counted for two count cycles matches.
Figure 45-45 Cycle Count - Automatic Count Cycle 2
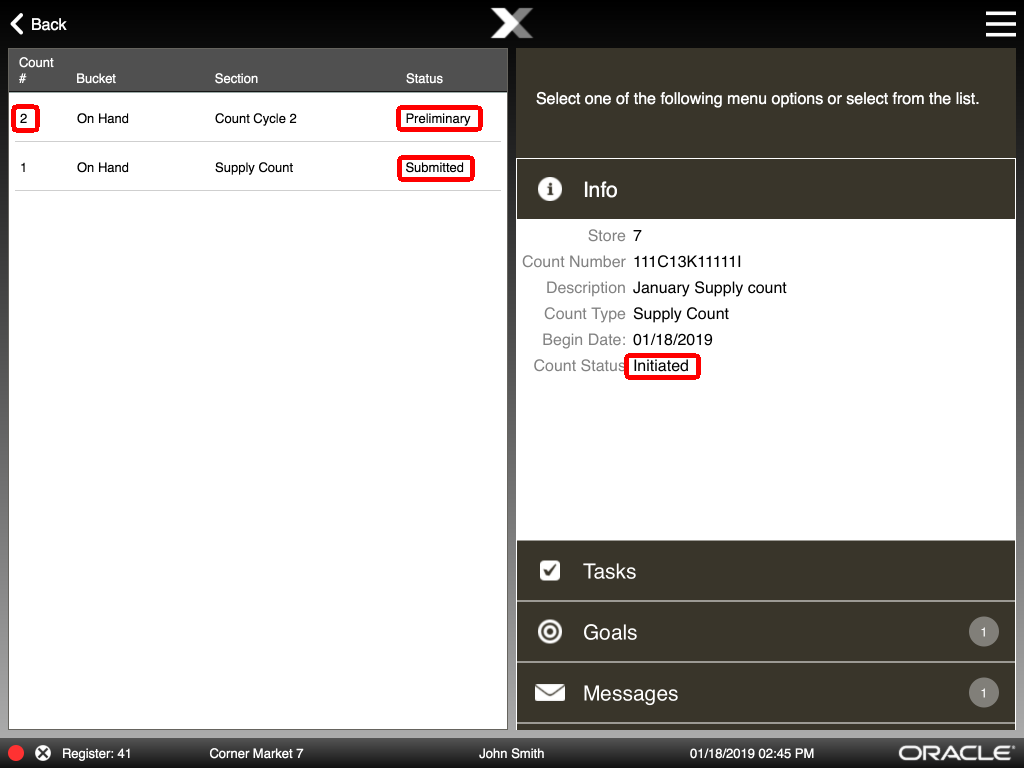
About Count Cycle 2:
The Inventory Count document status is Initiated. Any subsequent count cycles are always compared to the initial snapshot taken for the first count cycle. You cannot initiate the count again for this Count document.
If using Automatic Variance Processing, count cycle 2 is created automatically any time there is a count discrepancy between the counted and expected quantities in count cycle 1.
Any items with variances in count cycle 1 are moved to count cycle 2 for a recount. Items that matched the entered quantity and expected quantity will not be included in the recount.
Physical Inventory count processing for count cycle 2: Consolidating Sections
In Count Cycle 2 (and higher), all items with variances will be grouped by Bucket. The Sections used for counting in Cycle 1 are not used for Cycle 2 and greater.
For example, if you have sections within the Layaway bucket such as an Earrings Section, a Watch Section, and a Jewelry Section with variances reported in Cycle 1, then in Count Cycle 2, the three Layaway sections (Earrings Section, Watch Section, and Jewelry Section) will be consolidated into a single Layaway bucket and the Section identifier will be ignored.
Figure 45-46 Count Cycle 2 - Consolidated Sections

The count sheet status for count cycle 2 is set to Preliminary, indicating this is a new count.
The count sheet status for count cycle 1 is set to Submitted status and cannot be changed.
How the Variance is Calculated in Automatic Variance Processing
This section shows a simple example of the process the system uses to calculate variances between expected quantity and counted quantity. In this example, the store is set up to use a maximum of 4 count cycles per Inventory Count document.
Count Cycle 1
The system compares the submitted item count for the inventory bucket against the snapshot:
-
If the numbers match, the inventory bucket for the item is considered settled - no variance, and the count for the item is Complete.
-
If the numbers do not match, the item is moved to the next count cycle (count cycle 2) and must be recounted.
Count Cycle 2
The system compares the submitted item recount for the inventory bucket against the snapshot:
-
If the recount and snapshot numbers match, the inventory bucket for the item is considered settled - no variance, and the count for the item is complete.
-
If the recount and snapshot numbers do not match, the count is compared against the inventory bucket's prior count for count cycle 1.
-
If the count matches the count for count cycle 1, the recount of the inventory bucket is considered as matched, the count for the item is complete, and the matched count will be used to compute the variance.
-
If the count does not match the count for count cycle 1, or the original snapshot, the item is moved to the next count cycle (count cycle 3) and must be recounted.
Note:
Count Cycle Grouping: In a Physical Count, only a single count sheet will be created for Count Cycle 2 (and higher). The items to be recounted on the count sheet will be grouped by Bucket, and the Sections defined for Count Cycle 1 are no longer referenced.
-
Count Cycle 3 and Higher
The process is generally the same as described in Count Cycle 2. However, if the numbers do not match for the inventory bucket, the count will be compared against the inventory buckets for all prior count cycle counts, in addition to the original snapshot. If the item is not settled or matched once the maximum number of count cycles is reached, the system considers the last count as final and uses it to calculate the variance.
Figure 45-47 Count Cycles: Automatic Processing
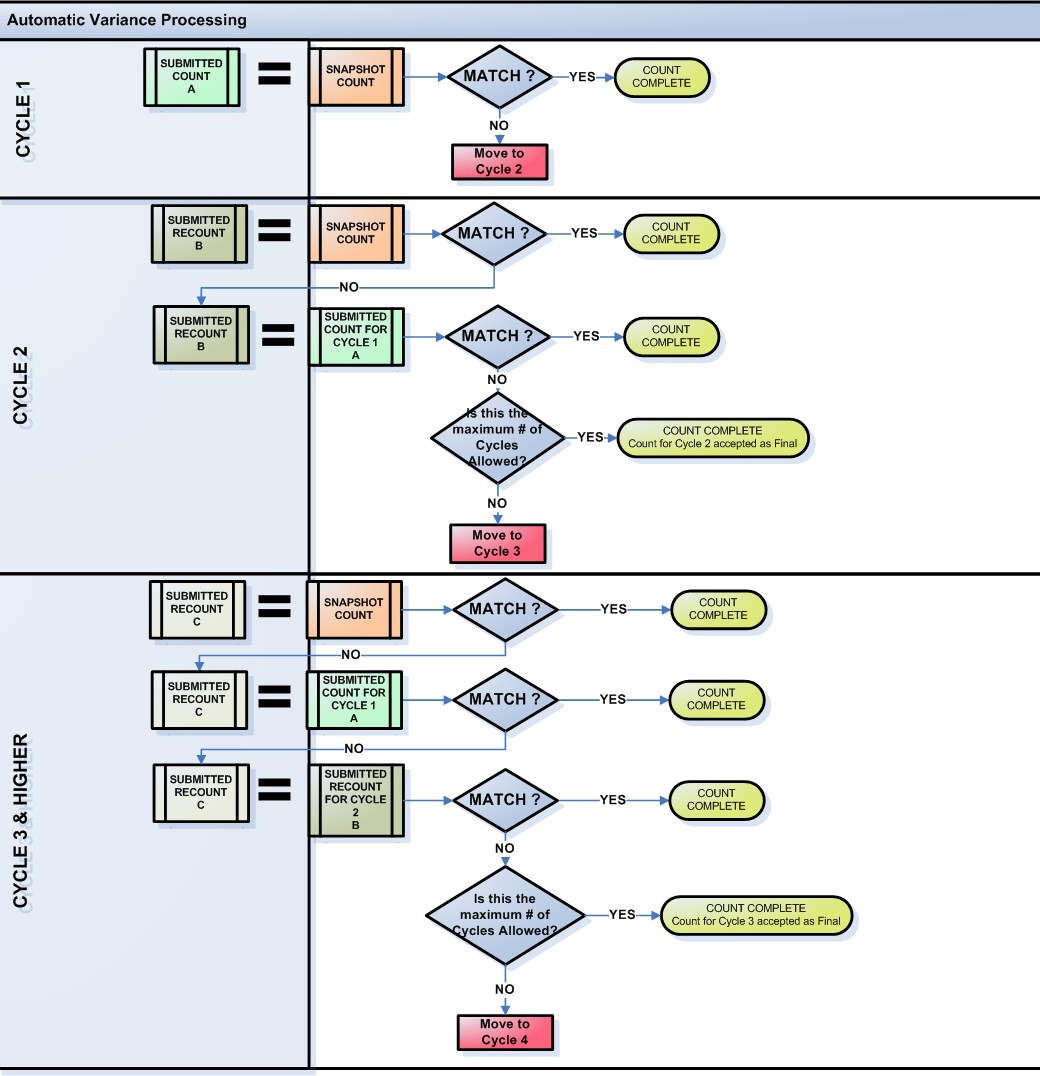
Automatic Variance Processing Examples:
Example 1 (Maximum: 4 count cycles)
Snapshot value = 4
Count for cycle 1 = 3
Count for cycle 2 = 4
Item is considered settled Cycle 2 = Snapshot, no variance 4-4=0
Example 2 (Maximum: 4 count cycles)
Snapshot value = 4
Count for cycle 1 = 3
Count for cycle 2 = 3
Item is considered matched Cycle 2 = Cycle 1, variance= -1 3-4=-1
Example 3 (Maximum: 4 count cycles)
Snapshot value = 4
Count for cycle 1 = 3
Count for cycle 2 = 2
Item automatically moved to count cycle 3 for recount No match between Snapshot or Cycles 1 and 2
Example 4 (Maximum: 4 count cycles)
Snapshot value = 4
Count for cycle 1 = 3
Count for cycle 2 = 2
Count for cycle 3 = 2
Item is considered matched Cycle 3 = Cycle 2, variance= -2 2-4=-2
Example 5 (Maximum: 4 count cycles)
Snapshot value = 4
Count for cycle 1 = 3
Count for cycle 2 = 2
Count for cycle 3 = 1
Count for cycle 4 = 6
The 4th count of 6 is final, variance= +2 6-4=2(System uses last count cycle value as the final count when there are no matches once the maximum cycles allowed is reached).
Manual Variance Processing
In Manual Variance Processing, the system does not perform any automatic movement of items from one count to the next. Instead, you can select individual count sheets to be recounted in the next cycle. The sheet can be moved to the next cycle until you determine that the count is complete, or until the maximum number of cycles is reached. The entire count sheet is provided for the recount, not only items that had a count variance from the expected quantity. However, on the last count cycle, or once the maximum cycles allowed is reached, only items with variances will appear on the Inventory Count Variance Report.
After submitting the last count sheet for an inventory bucket, the system displays a prompt to ask whether you want to recount this count sheet.
Figure 45-48 Manual Variance Processing - Recount Prompt
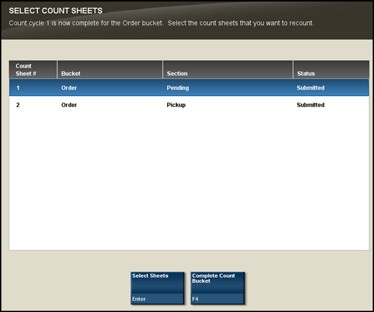
-
To recount the count sheet, select the sheet from the list. This moves the sheet to the next cycle of the count. Recount the items on the count sheet following the same process used for count cycle 1.
However, it is not necessary (or possible) to initiate the count again. Any subsequent count cycles are always compared to the initial snapshot taken for the first count cycle. You can recount the count sheet as many times as necessary, up to the maximum number of cycles permitted by your store policy.
Note:
If you select a Count Sheet for a recount and the maximum number of cycles has been reached, you will be prompted to complete the count and no additional count cycles are permitted.
-
To complete the count sheet, accepting any variances if applicable, select Complete Count Bucket. This option does not move any counts into the next count cycle but completes the count for this inventory bucket. The counts from the last cycle completed will be used to calculate the final variances for the bucket against the snapshot.
Variance Report
A variance report is created for each bucket in each cycle of the inventory count. After the final count cycle sheet has been submitted, or once all inventory bucket statuses are complete, the system posts inventory and creates the final variance report for all buckets.
-
To view a variance report, select the View Variance Reports menu option. See Figure 45-49.
-
Select a variance report from the list:
Figure 45-49 Variance Reports List
-
Select Print report to execute the report and send the results to a printer.
-
Select Save report to save this report with the current data or save only the report parameters to run this specific report with these parameters again. If you save the report, assign a name to it so it can be viewed whenever needed. Xstore suggests a name, but you may type in the Save Report As field and change it.
Variance Reports include the following header information:
-
Count #: The auto-generated count identifier associated with the Inventory Count document.
-
Count Type: The type of count: Physical Count, Cycle Count, Supply Count
-
Count Cycle: Indicates the number of times the bucket was counted to obtain these results.
-
Inventory Bucket Section: Used for Physical Inventory counts; defines the store layout area for the count.
For each Item ID with a variance in the inventory bucket, the following information is shown:
-
Item ID: The item identifier.
-
Description: The item description.
-
Snapshot quantity: The quantity recorded when the count was initialized.
-
Counted quantity: The count value submitted by the associate after counting the items.
-
Unit variance: The difference between the snapshot value and the submitted count value.
-
% variance: The difference between the snapshot value and the submitted count value, as a percentage.
Variance Percentage Calculation Formula: If snapshot quantity = 0 then infinity,
else,
If snapshot quantity < 0 then (-1 * (unit variance / snapshot quantity)) * 100, else,
(unit variance / snapshot quantity) * 100
Please note that rather large variance percentages (well over 100%) are correct if you have a small snapshot quantity and a large unit variance.
Figure 45-50 Count Cycle Variance Report Example
-
Store Layout Maintenance
Store Layout Maintenance is available on the Desktop, Thin Client, and Tablet.
The most efficient way to count physical inventory is to divide the store into specific count sections, based on the physical store layout, and possibly the number of associates that will be counting the items. These count sections are set up for inventory buckets you have defined for your store. Each count section will generate a list of items on a count sheet. For example, if you set up four sections, then four separate count sheets will be created for the count process. This allows you to assign the associates to specific areas of the store, equipped with a count sheet specifying the items to be counted in that section.
-
At the Main Menu, select Inventory.
-
At the Inventory menu, select the Inventory Count Options option.
Figure 45-51 Xstore POS Inventory Count Options Menu
-
At the Inventory Count Options menu, select Store Layout Maintenance.
Figure 45-52 Store Layout Maintenance - Inventory Location List
The system displays a list of the inventory locations defined for the store.
-
Select an inventory location.
Figure 45-53 Store Layout Maintenance - Inventory Bucket List
-
The system displays a list of the inventory buckets defined for the store. Select an inventory bucket for this count section.
Figure 45-54 Inventory Bucket - Add Count Section
-
The system opens the Inventory Bucket. Select the Add Count Section menu option to create a count section for the bucket.
Figure 45-55 Add Count Section Name Prompt
-
Type a name or ID for the new count section within this inventory bucket and select OK to add the count section to the bucket.
Figure 45-56 New Count Section Added
-
Repeat adding count sections to the inventory bucket as needed.
-
Select a Count Section row to define the items that are part of the count section. A pop-up menu is displayed.
Items can be added individually (Add Item option) or by merchandise level (Add Merch Level option).
Figure 45-57 Count Section Options
Other options are available if you need to modify the count sections and items.
-
Select the Remove Count Section option to remove a count section and the associated items from the store layout.
-
Select the Remove Section Detail option to remove an item or merchandise level from a count section.
-
Select the Move Section Up or Move Section Down options to move the count section position higher or lower in the list of count sections.
-
-
Select either the Add Item option or the Add Merch Level option.
-
If you chose to add an item, scan or enter the item ID at the prompt and press OK.
Figure 45-58 Add Item Prompt
-
If you chose to add a merchandise level, select the merchandise level from the list and select Process.
Figure 45-59 Merchandise Levels List
The items and/or merchandise levels are added to each count section for the inventory bucket and shown on the view port.
Figure 45-60 Count Sections with Items and Merchandise Levels Added
At the Context Menu, select the View Store Layout option to print a report showing the Store Layout for the inventory buckets.
-
-
Select the Save & Exit menu option to save the store layout and return to the Inventory Count Options menu.
Once count sections are set up for an inventory bucket, you can maintain these sections by adding or removing items and merchandise levels as needed. However, any updates you make to the store layout will only apply to new Inventory Counts going forward. Any existing Inventory Counts that have been generated will use the layout defined at the time the Inventory Count was set up.
Inventory Count Technical Limitations
Inventory counts have several technical limitations to which they must adhere based on the amount of system resources available to a computer running Xstore. All size limitations are necessitated by either a memory concern, or an imposed technical limitation of supporting software, such as Microsoft® SQL Server®.
Limitations/Information
The following numbers are based on a system running Xstore with a maximum of 512MB of memory allocated to it.
-
The maximum number of items that can be on an inventory count is 300,000. When the count sheets are generated, an algorithm is employed to determine what the final count size will be. If it will be greater than 300,000, generation of count sheets will not be allowed to continue. This limit is necessary to prevent systems from running out of memory while processing an inventory count.
-
The maximum number of items that can be on a cycle count or supply count is 2,000. This limitation exists due to the required functionality of these types of counts in conjunction with the limitations of Microsoft SQL Server.
-
The maximum number of inventory adjustments that will be processed by Xstore at the conclusion of an inventory count is 15,000. If a count produces more than 15,000 final variances, the user will be prompted that inventory levels cannot be adjusted. Xstore automatically notifies the corporate office via the inventoryCount.xml file to indicate that variances were not adjusted. The corporate office can then take appropriate action to account for the variances. This limit is necessary to prevent systems from running out of memory while processing an inventory count.
-
Inventory count data must be deleted routinely at the corporate level to ensure the optimal performance of the queries involved in inventory counts. Also, the inventoryCount.xml file must be deleted after it reaches a certain size (a maximum size is about 250MB). After this size, performance in writing to this file will be significantly decreased